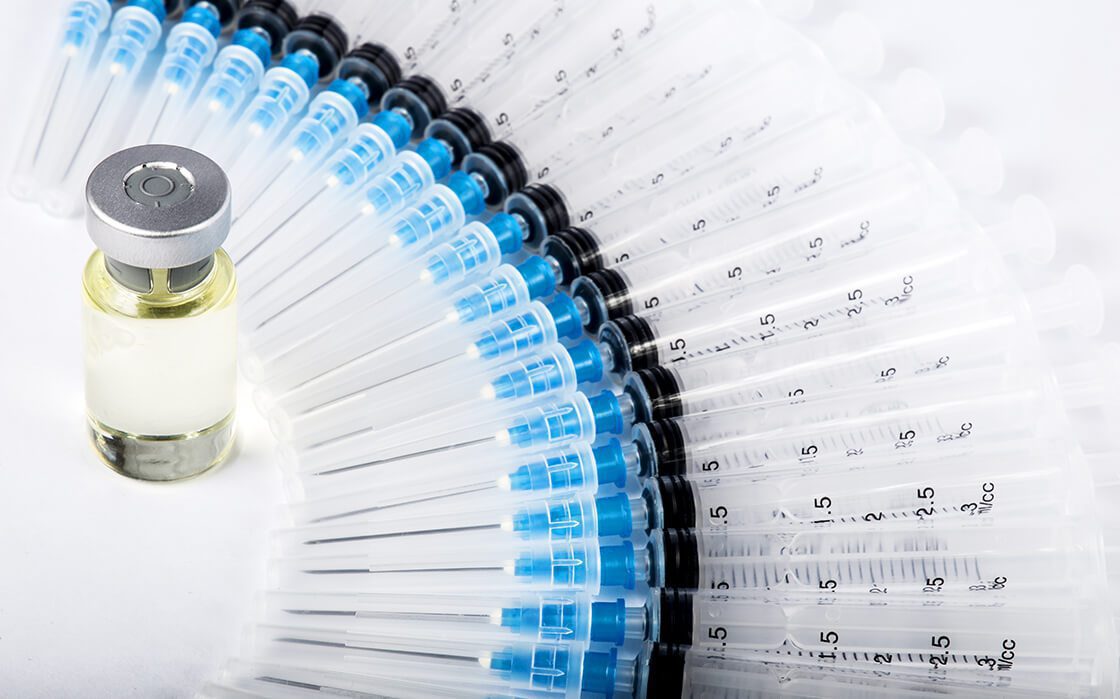
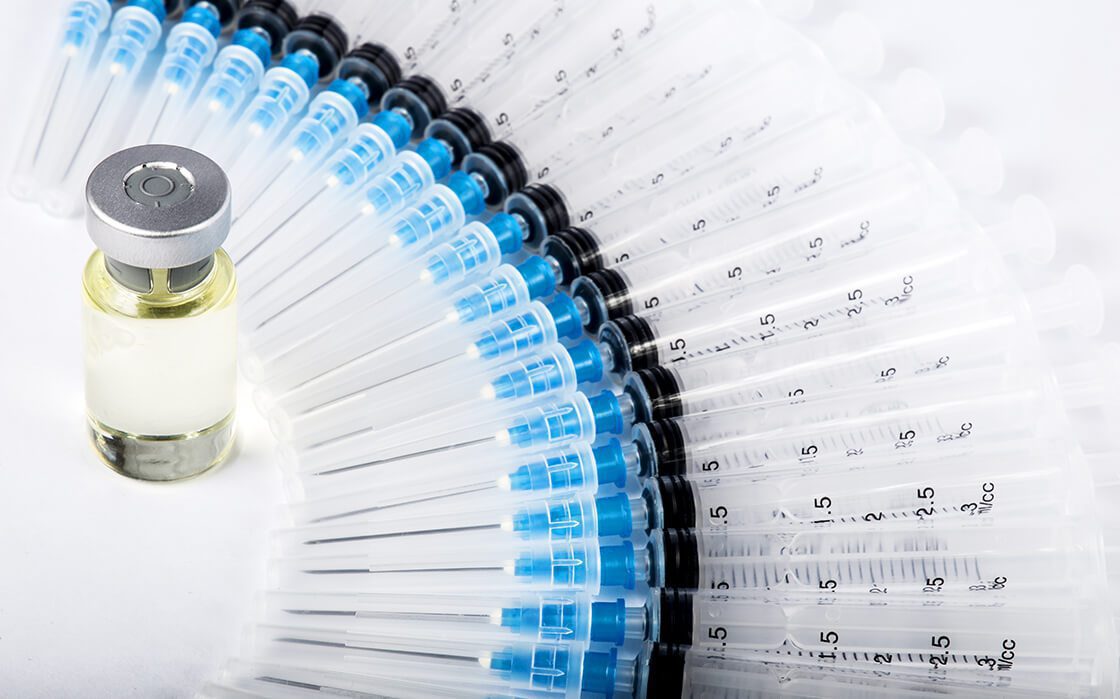
A largely automated packaging procedure increases process reliability, raises efficiency and guarantees optimum product protection. But when is it sensible to automate the packaging procedure? And what are the approaches to this?
Medical products are usually launched onto the market as single packs or combination packs. It is frequently the case that a leaflet, label or desiccant sachet has to be inserted with the product into the pack. Medical devices with active product components may also be packed, as well as sensitive products, which have to be reliably protected against external influences such as oxygen, vibration or radiation. Due to the increasing individualisation of products, batch sizes are becoming ever smaller, which means the need to convert pack formats on packaging machines is also becoming more frequent. The sector is therefore characterised by a wide spectrum of products, as well as high demands on pack quality and the packaging procedure itself.
Automation enables pack quality, process reliability and efficiency to be increased. Taking pack quality as an example, a robot guarantees the product is loaded precisely and completely into the pack cavity. This means the reject quota is reduced considerably. No less positive is the effect of an automated process on hygiene, since the fewer people involved in the packaging procedure, the higher the hygiene level is. A higher level of process reliability is also assured by track and trace, the detection and ejection of reject packs, reliable line clearance and the consequent prevention of cross contamination. Efficiency can also be increased by higher cycle outputs and the reduction or even prevention of stoppages and lost time. The changeover to an automated packaging procedure pays off, as long as the focus is on these factors.
A greater degree of automation does however demand a very high level of flexibility as regards the packaging machine and automation components. As a general rule, practically all process stages can be automated, including the upstream and downstream processes. This includes the orientation, separation and automatic transfer of the products to the packaging machine, as well as loading the pack cavities and right through to separating the packs and transferring them to downstream equipment such as a boxing unit. When selecting the individual automation components, the nature of the particular product to be packed has a great influence.
A quick look at the products to be packed shows that these require different infeed systems depending on the nature of the product. Needles, plungers and smaller products are for example presented as bulk items. These can be separated by means of vibratory units or centrifuges, before being fed in one or several rows to the packaging machine. Syringes and bags are often fed in via a converging unit and subsequent transport conveyor to the packaging machine, and the orientation of the products is monitored by a vision system. Carrier systems are often used for the infeed of high-value or sensitive products, such as filled syringes, complex devices or inhalers. Ampoules or vials can be transferred to the packaging machine by means of a converging unit that is specifically adapted to the particular product.
The examples mentioned above show how the individual products are aligned during the infeed in such a way, they can be precisely positioned for picking up by a robot and loading into the pack cavities. However, the gripper must be matched exactly to the particular product, which is frequently very light or sensitive. Special devices for checking the presence of the product in the pack also increase the process reliability. When loading the product, the gripper must load it precisely into the particular cavity and never allow it to fall. Mechanical damage, such as scratches, must also be prevented. In order to ensure there is flexibility of the packaging line as regards different products, it is recommended that gripper systems are used, which can be changed easily and quickly. There are also similar requirements when unloading the finished packs from the machine, before they are transferred to downstream equipment for loading into outer packaging or boxes.
As a matter of principle, all the requirements imposed by the medical products industry on the packaging machine are also transferred to the particular automation component. In addition to the flexibility stated above, it is also important to mention the positional accuracy of the handling modules. Other requirements include easy access to the modules and ease of cleaning, which help to ensure the system complies with Good Manufacturing Practice. When designing its automation components, such as with the enclosures for its gripper systems, MULTIVAC ensures they are easily accessible, and also uses wherever possible smooth surfaces, as well as systematically reducing protruding parts and hidden corners. The cleanroom compatibility of the components is also a factor in the design. This can ensure particle formation is prevented as far as possible thanks to minimal vibration and air flow during operation of the modules.
MULTIVAC offers a wide range of automation components for the packaging of medical products. The product portfolio comprises a wide selection of conveyors, carrier systems and special infeed systems for a large range of products. These modules are individually designed depending on the products to be packed and the upstream production equipment. Thanks to their design and particular features, all the system components are characterised by their high level of GMP compliance, and they can be fully integrated into the machine control of the packaging machine.
When it comes to loading the pack cavities, MULTIVAC offers a wide range of handling modules, which can be individually equipped with a variety of kinematics and gripper systems. The gripper systems on the handling modules can be converted very easily, so a high degree of flexibility for the packaging line can be achieved. These handling modules can also be used for unloading the finished packs from the machine and transferring them to downstream equipment. They also ensure reject packs are safely ejected, thereby contributing to a maximum level of process reliability.
03.05.2017