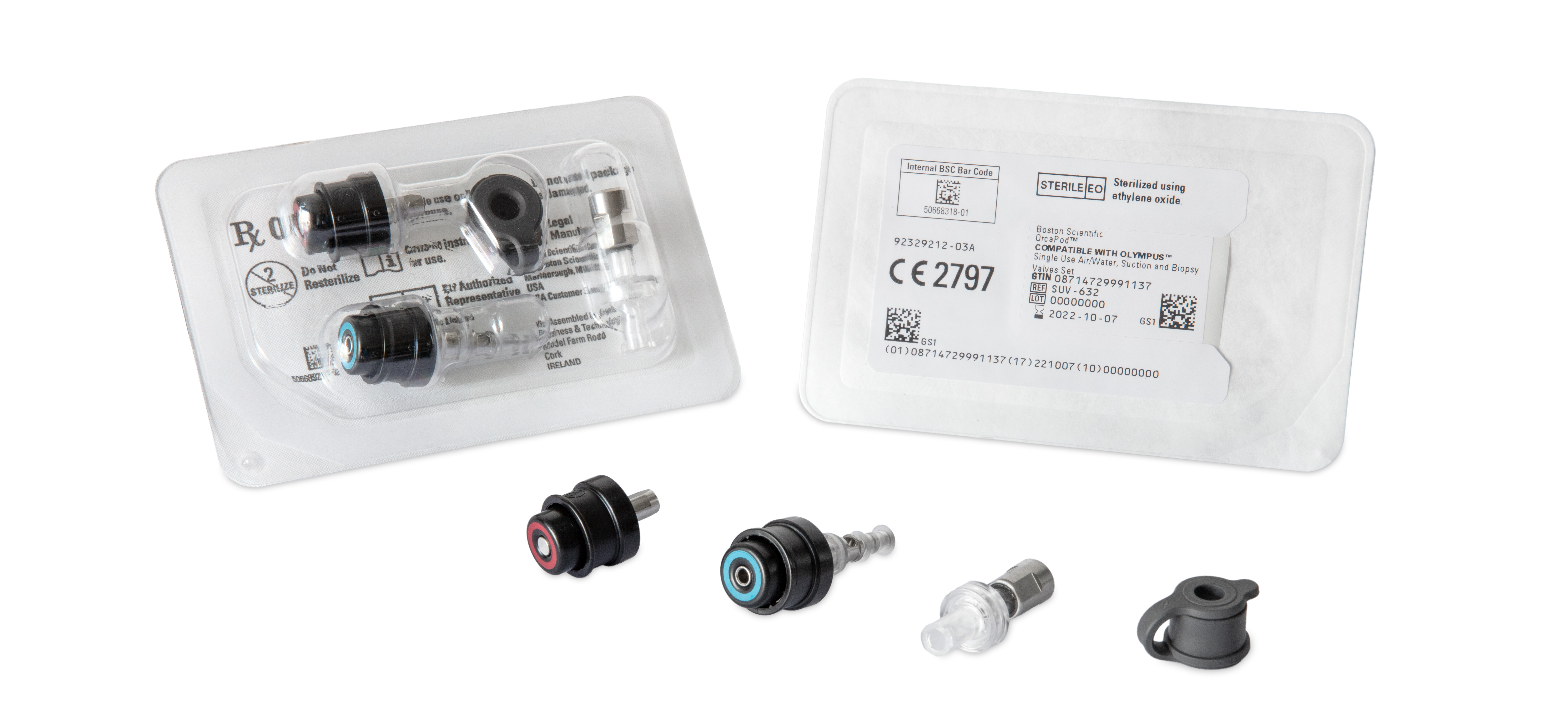
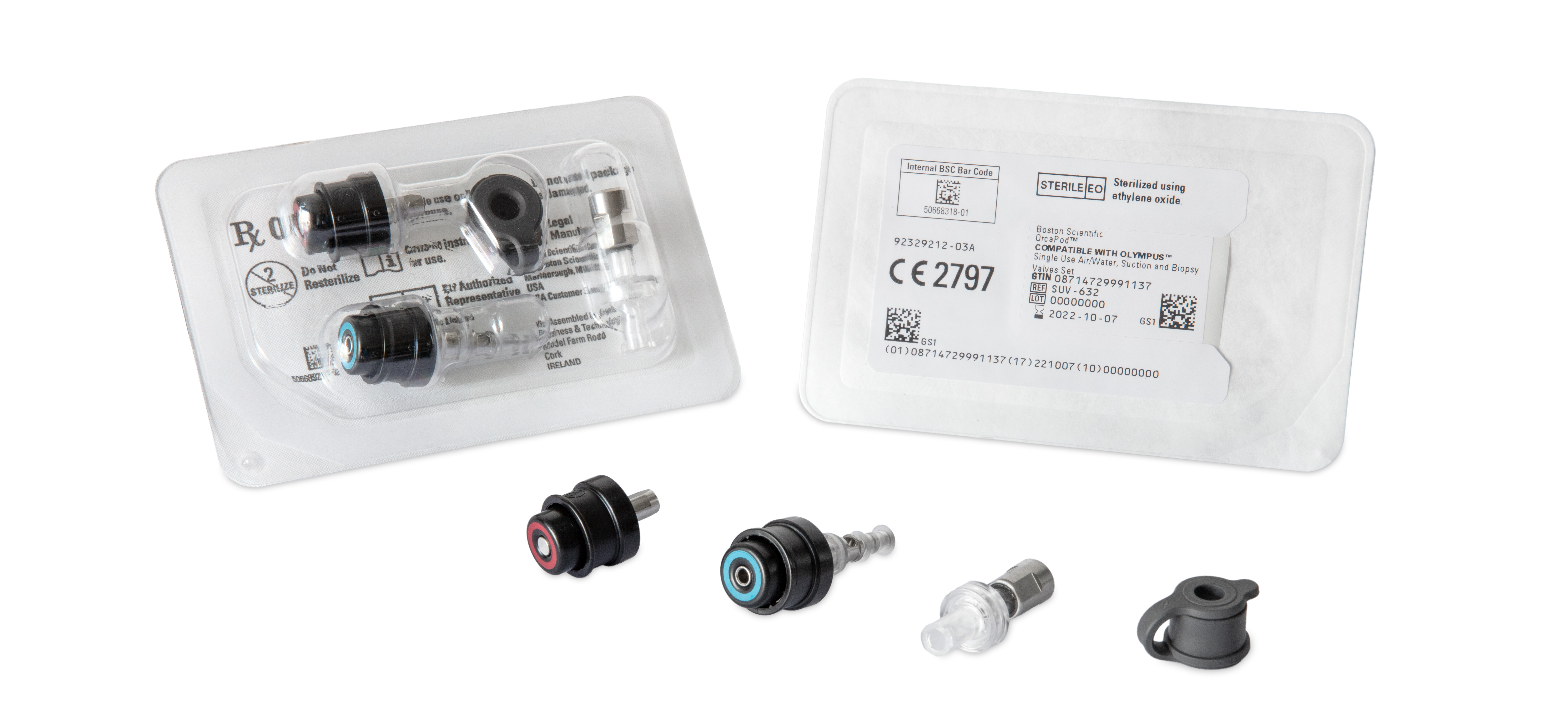
Science and technological progress, combined with inspiration and determination - this is the basis of Boston Scientific's success. In line with this basic principle, the US manufacturer of medical devices decided on a state-of-the-art packaging solution from MULTIVAC for its Irish production site in Cork - a packaging solution that meets all their requirements in terms of process reliability and operating security. The new packaging line is automated from the loading stage right up to the end-of-line area, and it not only reduces any contamination risk to an absolute minimum, but also ensures that operation is simple and reliable thanks to its single machine control.
Boston Scientific, which is based in Marlborough, Massachusetts, was founded in 1979 by John Abele and Peter Nicholas as a holding company for the previous Medi-Tech. Its declared aim was to position itself successfully in the sector of interventional medicine in order to gain sustainable, global growth. Thanks to a number of strategic acquisitions, the company was able to rapidly embark on a targeted expansion of the product range, which now consists of a widely differentiated spectrum of medical devices for many applications. This ranges from catheters to stents, heart pacemakers and even defibrillators (ICD) and much more. With a total of 13 production sites in the USA, Costa Rica, Puerto Rico, Malaysia and Ireland, as well as a turnover of around nine billion US dollars and a workforce of 29,000 employees, Boston Scientific is today one of the leading manufacturers worldwide of medical devices. A crucial factor in its continuing success has always been the consistently high level of innovation within the company, which was listed among the Top 100 Global Innovators for three years running thanks to its pioneering product developments from 2016 to 2018. In addition to many other awards, Boston Scientific also received the Prix Galien Award in 2018 for its minimally invasive WATCHMAN™ LAAC procedure (left atrial appendage closure).
Special valve sets, named Orca™, for endoscopes are manufactured at the Cork production site, and these single-use valves reduce the risk of infection transmission to a minimum. The packaging process for the valve sets, which are packed in two-, threeand four-part variants, must of course meet the highest hygiene standards. “Sterility up to the point of use is of course imperative, and it is therefore essential to produce a secure primary pack with a sterile barrier. In addition to this, the entire production and packaging process must be designed for cleanroom compatibility,” explains Richard Guilfoyle, Engineering Manager at Boston Scientific Cork. Up to then the valve sets had been loaded manually into the pack cavities. With the planned new packaging solution, which was intended to be automated in the loading and unloading parts of the process in particular, it was hoped that there would be a significantly higher level of efficiency than previously. There was also potentially another major benefit in being able to label the packs and transport boxes within the overall process. “We considered the end-to-end automation of the entire packaging line to be an extremely important aspect in terms of higher productivity and efficiency. In parallel with this however, it was also vital in our view that all the line components should be completely integrated, so that there would be the greatest possible process reliability,” adds Cathal Reilly, Director of Manufacturing Engineering at Boston Scientific Cork. Those responsible for the project also envisaged further benefits as a consequence of automatic loading in terms of significantly improved cost efficiency. “MULTIVAC was for us the only possible candidate thanks to the high quality of its machines, the company's comprehensive expertise in packaging technology, automation and complete lines, as well as its unrivalled facilities for producing sample packs at the start of the project,” says Richard Guilfoyle, explaining the background to the decision.
In November 2018 the new packaging line was put into operation after a project phase lasting ten months. Since then the R 245 thermoforming packaging machine has been producing packs made of a transparent APET lower web and a Tyvek® upper web. The loading process is as follows: The Orca™ valve sets are fed directly from the assembly stage to the packaging process by means of automatic product carriers, and there the valve sets are removed before being loaded into the packs, after which the product carriers are transported back again via a carousel system. The products are loaded into the packaging machine by a H 242 handling module. The delta robot grips all the valves for one pack in a single operation and places them with great precision in the pre-formed pack cavity. Before the pack is sealed with the upper web, the individual products are inspected by means of a MULTIVAC Vision System of the MR842 type. The system checks the presence, completeness and correct position of the valves. The print on the inside of the Tyvek upper web is also checked for correctness. After the packs have been sealed, a MR625 cross web labeller, which is equipped with a high-performance thermal transfer printer, applies the printed labels to the upper web of the packs. There is subsequently a label presence check. In the end-of-line area the sealed packs are then separated by means of a complete cutter into five individual packs. The gripper of a further H 242 handling module removes the packs each cycle directly from the cutting tool, and it then places them into the outer box, which has been fed into position. During the packaging process these boxes are prepared in advance by a box erector, and they are then taken by transport conveyors to the loading point. Should there be any reject packs in a cycle, these are ejected via a conveyor. The remaining packs in the cycle are stored temporarily in a movable buffer system, until a complete cycle of five packs can be created again. This complete cycle is then picked up by the gripper and placed into the outer box. A booklet dispenser then provides the DFU (Directions For Use) for each of the outer boxes, which are filled with 50 packs. At the end of the line there is a L 310 conveyor belt labeller, which applies labels to the finished secondary packaging.
In order to ensure that all the line components were perfectly matched to each other, the whole line was subjected to an exhaustive factory acceptance test at MULTIVAC in Wolfertschwenden. It was only after this test had been completed successfully, that the line was approved for installation at the site in Cork. The line meets all the requirements for pack quality, process reliability, cleanroom compatibility and of course the required sterile barrier without any reservations whatsoever. MULTIVAC's service quality is particularly appreciated by Boston Scientific. “Communication worked very well from the start,” says Cathal Reilly, praising the cooperation. “The experts at MULTIVAC analysed our specific requirements very profession - ally and always applied their profound know-how during the entire process. The result is a solution, which is ideally tailored to our individual application,” says Richard Guilfoyle, adding that “The outstanding support did not end after the line had been installed. Even after this point we were always able to turn to MULTIVAC, if we needed to optimise the line settings still further.”
Thanks to the very transparent operating system, the operation of the highly complex packaging line is child's play for the user. “We were also particularly impressed with the seamless inte - gration by MULTIVAC of components from third-party suppliers,” says Richard Guilfoyle with satisfaction. Operators only have to be trained in one single, intuitive operating system with a uniform operating logic in order to be able to control the line, and this means that they are very familiar with the line after just a short period of instruction. “The quota of operator errors is therefore practically zero.” There is a positive response not only from the operators but also from the users of the Orca™ valves. “During a hectic work - ing day the tear strip on the outer box is particularly appreciated by users,” says Cathal Reilly. The feedback on the primary pack has also been thoroughly positive − this is “not only more com - pact and cleaner in its design, but also significantly easier to open and generally more practical in its handling.” “Overall the new line reflects our company's claim to lead - ership in innovation for the wellbeing of the patient - and now also at the level of packaging technology,” says Richard Guilfoyle in summary. As the next step, the company also wants to consider inspection of seal seam quality, as soon as a suitable system is available.
Gary Stafford, Business Manager for MCP and Automation at MULTIVAC Ireland, said at the presentation of the award: “We are very pleased, that Boston Scientific values MULTIVAC as a reliable partner in the con - tinuing success of its business. Thanks to the close cooperation between our team at MULTIVAC Ireland, the Medical & Pharma Solutions Business Unit at the German parent company, and of course the team at Boston Scientific, we were able to install the first automated and high-output packaging line within a tight time period.” Derek Nugent, Managing Director of MULTIVAC Ireland, added: “We are very proud of our customer service, which cov - ers the entire life cycle of all our packaging solutions. This award is recognition of the success of the project, which was made possible by the close cooperation with Bos - ton Scientific - from the original conception right through to installation, training and local customer service. Our established partnership is a good basis for further project success.”
31.12.2019