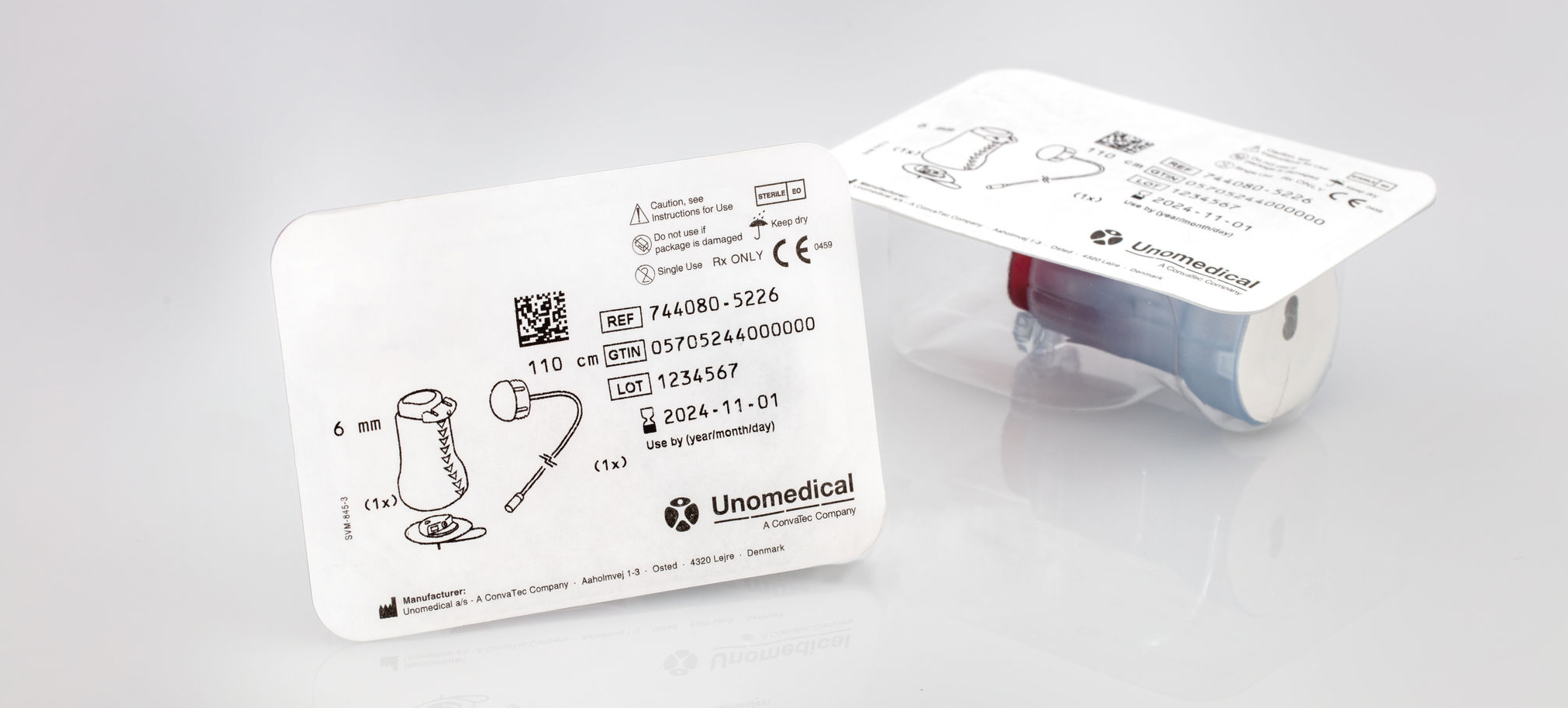
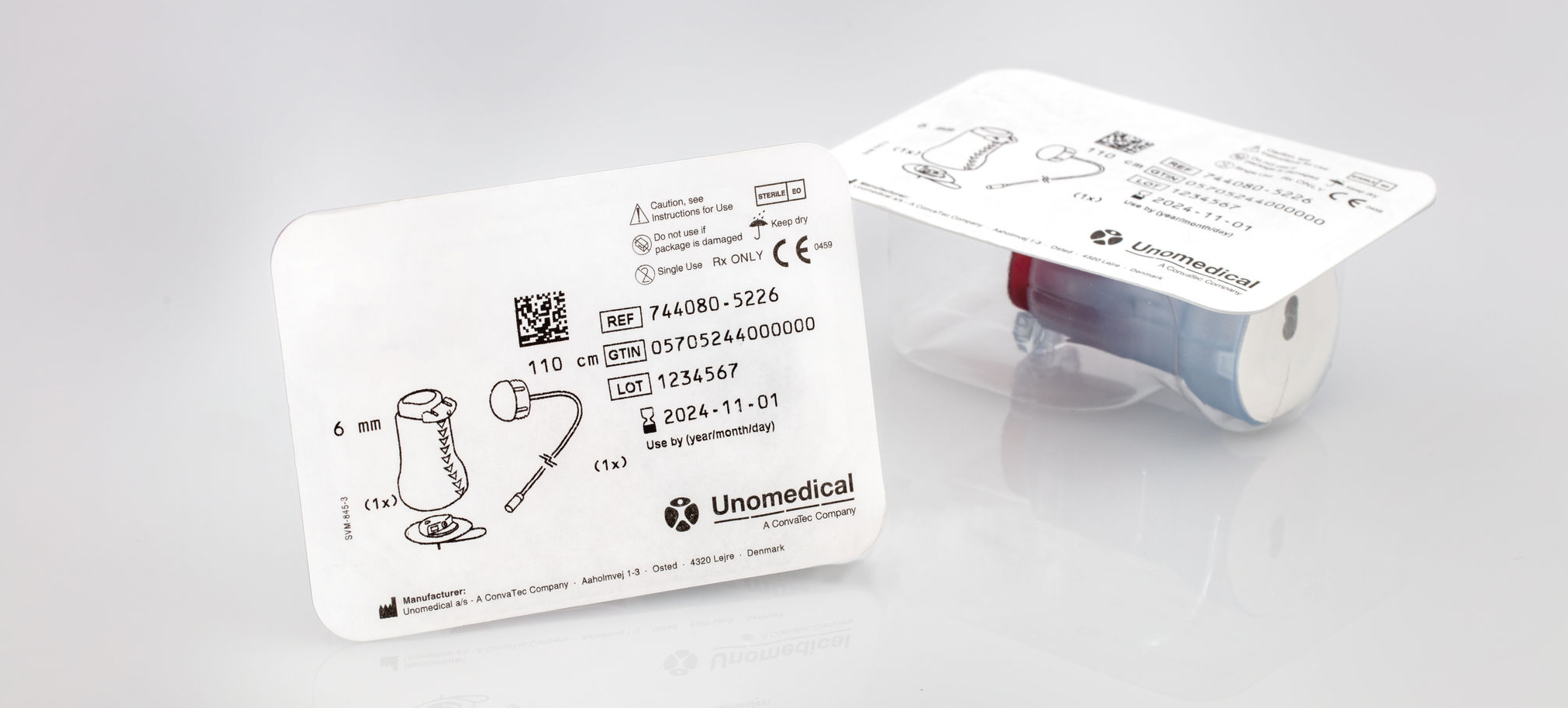
ConvaTec and MULTIVAC can look back over 20 years of successful cooperation. MULTIVAC was once again able to demonstrate its comprehensive expertise and professional project management in complete packaging lines, when it undertook the latest joint project in the Danish town of Osted with the globally operating manufacturer of medical products.
I t is essential in the production and packaging process of sensitive medical products, that all the parts of the process and all the components of a line are perfectly tailored to each other, so that the products are transported gently, and the maximum process reliability and overall equipment effectiveness are achieved. But the greatest focus is on the sterility of every individual pack. “The interfaces between the individual modules of the packaging line are particularly critical,” explains John Crosse, Vice President for Investor Relations at ConvaTec.
“In addition to the quality and various features of the particular modules and line components, the crucial aspect for us when designing a new packaging solution is therefore their level of integration into the overall line. In our view, it is precisely in this area that one of MULTIVAC's greatest strengths lies.” For around 20 years the manufacturer of medical products, which has its company headquarters in the British town of Reading, has been placing its trust in MULTIVAC solutions. Ten systems from MULTIVAC are now installed at the different ConvaTec sites, and they are all in active daily use.
ConvaTec Inc. had its origin in the research work of the scientist Dr James Chen, who in the 1960s for the first time invented hydrocolloid for use in dental surgery. This subsequently served as the basis for the development of Stomahesive® skin protection, which contributes to drastically improving the quality of life for patients with an ostomy. As a consequence of this, ConvaTec was founded in 1978 from E. R. Squibb & Sons (today Bristol-Myers Squibb) as a subsidiary for manufacturing ostomy care products. The company has since established itself with a large range of innovative products as the leading company in ostomy care and the treatment of chronic wounds. In addition to products for ostomy treatment and hydroactive wound care, the company's focus is now also on improving the quality of life for chronically ill patients, as well as on continence and intensive care, and even in the area of infusion devices. Employing 9,400 staff at its ten locations in seven countries, ConvaTec today serves 110 markets and has a turnover of approx. 1.8 billion US dollars.
At its site in the Danish town of Osted, the company packs infusions sets with a soft cannula and an integrated one-touch inserter (so-called neria™ guard infusion sets), using a thermoforming packaging machine installed in a cleanroom, which is certified to the ISO 8 standard. After the packaging process is completed, the products are sterilised with ethylene oxide, and the absolutely reliable sterility of the packs up to the point of use at the patient is one of the most important quality requirements. As the demand for these products continued to rise, ConvaTec decided in March 2018 to invest in a new and fully automated packaging line, of which the footprint could not be larger than that of the old equipment due to the space limitations. The decision was made in favour of the R 245 thermoforming packaging machine. An APET/PE multi-layer film is used for the lower web of the packs. The upper web is a Flexpeel KDS 70 medical paper. H 242 handling modules provide efficient and high-output loading and unloading. The infusion sets are transported in special trays from the assembly process directly to the packaging machine, where they are fed to the loading process. Here 40 products per tray are then orientated, separated and prepared for the pick & place process. The individual infusion sets are subsequently placed in the pack cavities of the packaging machine by means of delta robots. Inspection systems constantly monitor, whether all the products have been placed correctly and completely. The empty trays are discharged via another transport conveyor. These trays are then provided once again to the assembly process, so that the loading loop is closed.
A MULTIVAC MR 295 direct web printer ensures that the packs are printed reliably and correctly. It is equipped with two TTO 20 thermal transfer printers. Variable data such as batch number and use-by date is printed onto the pre-printed upper web by means of this printing system. A MULTIVAC I 420 vision system is used to check the packs after sealing for correct text, legibility and positioning of the text. The packs are separated from the web by means of a complete cutting tool. The individual packs are removed from the 68 | PACKS FROM AROUND THE WORLD | CONVATEC cutting tool by another H 242 handling module, which places the packs onto a transport conveyor. The packs are orientated before being fed through a checkweigher and then on to final box packing. The process includes the automatic ejection of faulty and incomplete packs.
As part of the twelve-month project phase, a testing phase was also used to calibrate the line and validate the reproducibility of all the processes. Particular importance was attached to the sterility of the packs. The optimum synchronising of all the interfaces between the individual modules was a crucial aspect in observing the quality-related parameters throughout the entire packaging line. The new line has been in operation since March 2019, and it completely meets all expectations as regards productivity, efficiency and process reliability. “The overall equipment effectiveness was of central importance for us. Thanks to the new solution, we can now produce so cost-effectively that the return on investment will be achieved in less than two years,” says John Crosse.
Significant improvement to the pack was also achieved by MULTIVAC, while the pack was being developed. During the course of the project, it was possible to make a change to the pack design. The optimised pack can now be packed into the boxes much more easily. This brings not insignificant benefits for the downstream logistical processes. When it comes to working with MULTIVAC, John Crosse particularly appreciates the professionalism of the contact people locally. “The Danish MULTIVAC team, together with their colleagues in Wolfertschwenden, once again demonstrated very impressively over the entire project their depth of know-how and expertise in project management,” says John Crosse in summary. “With this manufacturer we particularly appreciate the fact, that installing and putting such a highly complex line into operation went according to plan, and that MULTIVAC rigidly adhered to all delivery dates and installation schedules.” The Vice President is very confident, that ConvaTec will be working with MULTIVAC in the future to ensure that the line capacity continues to be optimised, and that the highest quality standards for both products and packs are sustained.
31.12.2019