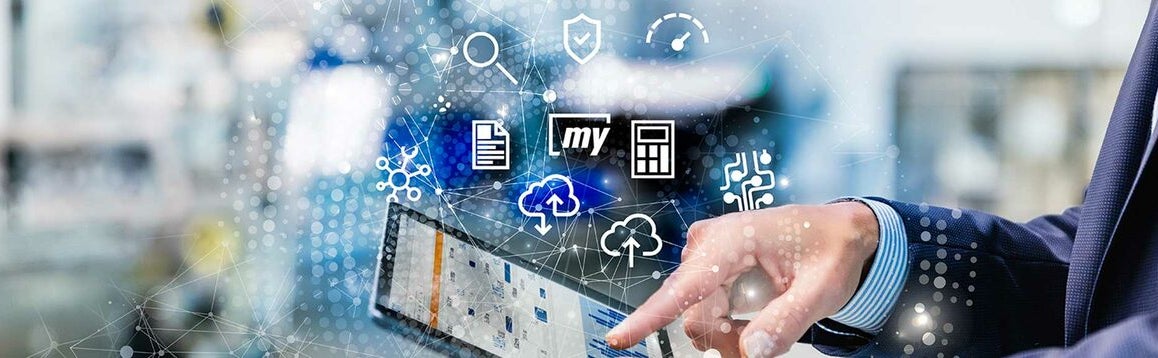
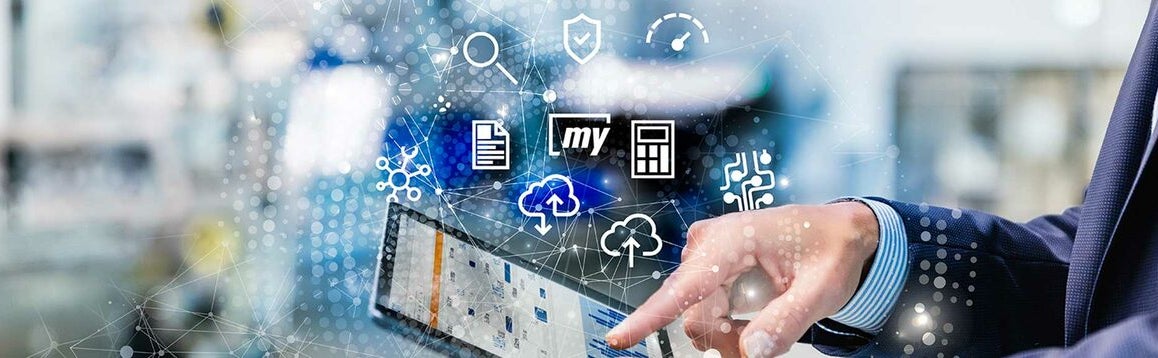
Zero productivity progress, no organisation, no standardisation: In the opinion of some experts and many in the media, the German economy has been asleep, when it comes to digitalisation and Industry 4.0. But as this interview shows, Dr Marius Grathwohl, Vice President of Digital Products and Transformation at MULTIVAC, the specialist packaging company, is convinced that this is far too pessimistic. And this is why there are grounds for hope.
What the German economy has achieved with digitalisation in recent years can not, in my opinion, be dismissed as "zero productivity progress". Many things have been done. For example, the BITKOM, VDMA and ZVEI industry associations founded and expanded the Industry 4.0 platform - one of the largest Industry 4.0 networks worldwide, which cooperates with many different alliances, as well as giving practical start-up help on digitalisation and Industry 4.0 to small and medium-sized companies. According to BITKOM, some 62 percent of companies in Germany have since introduced Industry 4.0 applications. And the platform has also provided stimulus within the international discourse. That is a very important point. A powerful vision like Industry 4.0 needs sufficient time. We should not expect, that all the players are at the same level, and that everything is ready at the same time. And we should not lose patience. Not after just ten years. Think of the Amazon founder, Jeff Bezos, who had the vision in the 1980s of shifting heavy industry into outer space and transforming the earth into a sort of national park. Only today, some four decades later, are private space flight companies being developed, which could transform the vision into reality. Big dreams can take time. And things are already happening on the journey. We at MULTIVAC started in 2017 to engage intensively with the subject of the Industrial Internet of Things. Since then we and our technology suppliers have made rapid progress. The infrastructure and the networking of machines are striking examples. Even Chinese experts recognise this and have recently come onto our exhibition stands asking about Industry 4.0. That is a good sign. Big things are due to happen for us.
I see digitalisation as a powerful instrument for promoting trade and industry. Particularly in the machine engineering industry, one of the foundations of the German economy, it is the digital transformation, which offers companies the opportunity to reposition themselves and develop new markets. One example of this is service. Here the business models will change in the next ten years - driven by Industry 4.0 technology. Away from the classic spare parts business towards proactive and customer-focused service. Thanks to digitalisation, networking and key technology such as Big Data and Artificial Intelligence, it is possible for operators to analyse the live operation of machines and lines, as well as optimising the throughput, eliminating faults more quickly, and therefore increasing the machine availability. Services, which mean hard cash for customers and are consequently very attractive. But it is not only about promoting economic efficiency. In my opinion, digitalisation is also an aid to sustainability. Thanks to networking for example, machines and lines can provide live consumption figures for power, compressed air and coolant, and these key performance indicators support companies in making their processes more transparent and recognizing potential for savings.
German machine manufacturers have been diligent in recent years in introducing digitalisation. Most of them have developed their own range of digital products and smart services. But this now presents the question: How do we build up a functioning eco system, and how do we create the interfaces, so that the various technologies operate across all manufacturers and provide the maximum added value for users? I am cheerfully optimistic about the prospects. There are some very promising solutions, which are now "ready for market". If you just think of the Asset Administration Shell. This standard across all sectors makes it possible for networked machines and components to communicate with each other in the Internet of Things. This ensures that worldwide interoperation can be achieved. However it is not only the openness of manufacturers, but also that of users, which is important for progress in digitalisation. Data security plays a large role here. Fortunately increasingly few of our customers have concerns, if it is a question for example of sending data to the cloud. A sort of basic trust has developed in recent times, particularly when working with established cloud providers such as Microsoft or Amazon. Today there is far less discussion about dangers, and much more about functions and added value.
Industry 4.0 does not only have significance for the producing industries. The areas of application also include mobility, health, climate and energy. Politicians need to apply the necessary focus in these areas as well. And also on the constraints, with which companies are grappling. These include inadequate financial means and a lack of technical staff. It would be desirable for politicians to give companies greater financial support for Industry 4.0 applications, as is the case in other European countries. In my opinion, initiatives such as the Open Industry 4.0 Alliance also deserve greater attention and support. The community charged with implementing these digitalisation measures plays an important role, when it comes to creating an open eco system for Industry 4.0 with the maximum degree of interoperation.
٣١.٠١.٢٠٢٣