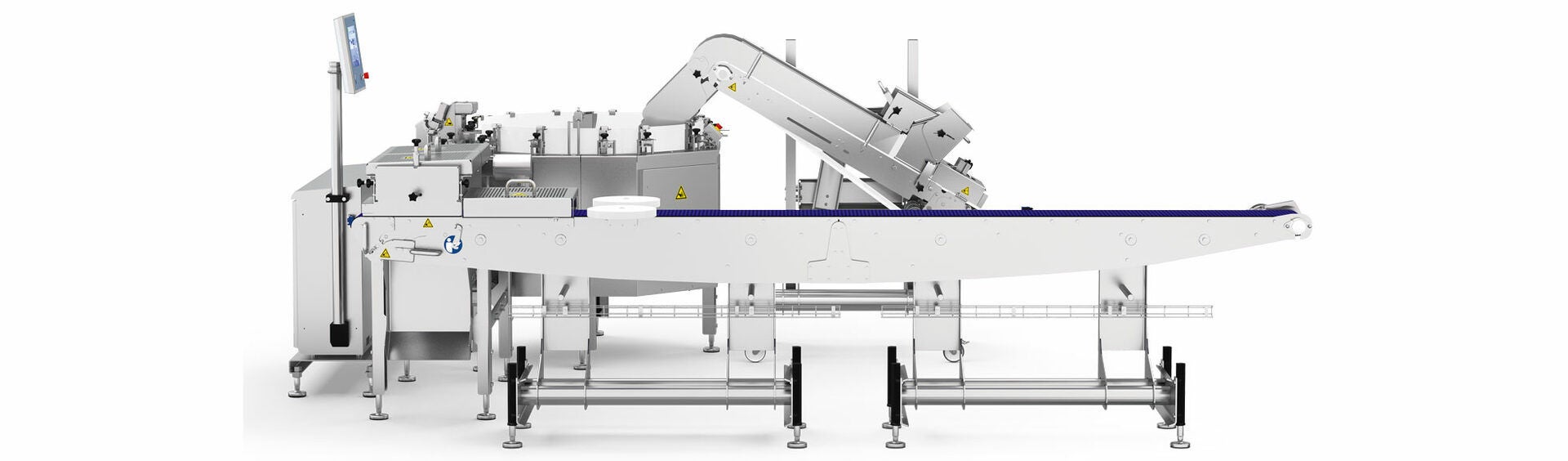
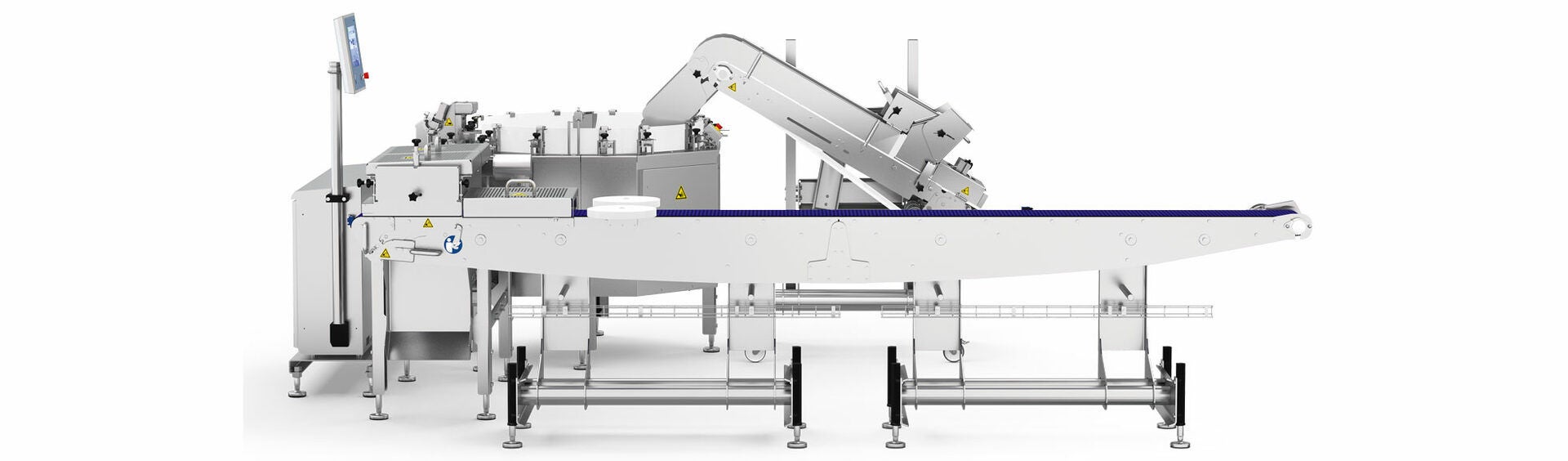
Most industrial robots worldwide are sold in the automobile and electronics industries, and the number of robots and handling modules employed in the food industry is currently still very small by comparison. The reason for this is essentially, that in the food industry it is largely a case of products with a very low level of standardisation, since the shape and consistency of individual products vary even within a single production batch. In addition to this, the individuality of food products such as meat, sausage, cheese, or snack and bakery products of all types is not only accepted by consumers but expressly desired, since this is associated primarily with hand-crafted processing and not industrial-scale manufacturing.
In order to achieve the optimum product and pack result, the packaging process in all its different parts has to be tailored individually to the particular product, its shape and its specific characteristics. However, this is difficult to standardise in the areas of product infeed and loading.
In contrast to industrial products, there are exacting requirements in terms of hygiene, which have to be met in the food industry. Food products are susceptible to bacteria and spoilage and, where there is direct contact with grippers, cross contamination must be prevented, which means there are special requirements as regards their design. The classic automation solutions are not designed for these demands and can not therefore be used in the food industry.
For this reason there is currently a rapid surge in automation in the food industry - the sector is now seen as an important growth market. And rightly so, since automation solutions contribute to increasing productivity while reducing the use and costs of personnel, and they also minimise accidents at work while at the same time improving hygiene. The use of robots is an important key to higher quality and efficiency, particularly in terms of their flexibility, speed, precision, reproducibility, and hygiene. Sophisticated and tailored automation solutions can even meet the requirements of small and medium-sized businesses in the food industry, which frequently have a wide range of tasks as well as many batch and product changes.
To meet all these different requirements, MULTIVAC offers a wide range of solutions, which can be adapted individually to the specific need. However, as Peter Lenz, Head of the Strategic Product Management department at MULTIVAC, explains: “Today it is more about integrated solutions and line concepts rather than the implementation of isolated handling solutions.” MULTIVAC, as the leading packaging specialist worldwide, has systematically expanded its product range in recent years to include solutions both upstream and downstream of the packaging process, and it is now in a position to automate all parts of a packaging line.
There is particular focus on the efficient linking of these systems to the packaging machine. “Today we can offer solutions, which are groundbreaking in the market. We are able to generate significant benefits for our customers when implementing such concepts, because we look at the whole solution holistically, starting from the pack design and then going through aspects such as labelling and quality inspection right up to the configuration of the complete line,” adds Peter Lenz. The motto: Line efficiency can only be maximised by perfectly coordinated system components and higher-level line control.
It is a fact, that efficient and gentle loading of the product is one of the critical factors in overall equipment effectiveness - but at the same time also a real challenge. Automation is of particular value in this process, since it is generally an onerous and monotonous task, which is frequently not very ergonomic and has to be performed very hygienically. When it comes to the loading and packing of natural products such as meat, sausage, cheese, or bakery products, automation does however require a high level of expertise in systems and applications. When implementing integrated robot solutions, it is also important to ensure the footprint of the line can be reduced as much as possible, and that the robotic system is integrated into the overall line control, so the maximum reliability and efficiency of the process is achieved. The MULTIVAC product portfolio in this sector now includes an extensive range of solutions, which is constantly being expanded and adapted to the needs of the market.
In order to be able to load the products as efficiently as possible, MULTIVAC frequently relies on specific pre-grouping solutions that are tailored to the application. The objective here is to minimise the robotic loading processes required, by ensuring that several products are loaded at the same time. In addition to ensuring gentle product handling and high output, the main challenge of the pre-grouping process is to make sure that the tolerances of natural products can be managed, and that it is possible to eject products, which are outside the prescribed specification. In order to ensure that this can be achieved, MULTIVAC has over recent years developed a range of grouping solutions for specific applications and integrated these into the handling modules.
A good example of this is the MULTIVAC Centrifuge Feeder (MCF), which can be integrated seamlessly into automated packaging lines. This hygienic solution, which is also gentle on the product, was specially developed for pre-grouping straight and uniform sausages. The products are sorted very effectively, so that they can be loaded with maximum efficiency into the downstream packaging machine. Compared to manual loading, the use of this solution can enable handling costs to be reduced by up to 60 percent.
The system comprises five high-performance components: the sausages are transported via an inclined conveyor to the centrifuge plate that is constantly turning. There they are orientated at the outside edge of the plate by the centrifugal force and are taken up individually from the centrifuge ring. Then a V conveyor transports them to a downstream compartment conveyor that carries each product, individually and precisely aligned in a separate compartment, to the handling module. There the gripper picks up the desired number of sausages and loads them into the pack cavity.
But this is only one of many examples. When cheese blocks are being loaded for example, MULTIVAC often relies on a pre-grouping solution for the cheese blocks, which precisely matches the format of the packaging machine. This enables a 2-axis robot to load one complete format all at once. This significantly reduces not only the output required of the robot, but also the complexity of the loading process, since no vision system for example is required. The dimensions of the cheese blocks can also be checked at the grouping stage, and product can be ejected in the event of non-compliance with the specification.
Today the range of MULTIVAC grouping solutions covers many more applications, and it is constantly being expanded through new market demands and creative ideas.
Another example of MULTIVAC's expertise in product loading is its gripper technology. The design of a gripper system plays a major role, since its characteristics have to be matched to those of the particular food product. The correct design of the gripper is essential to ensure, that the product is handled reliably and gently, and that the ideal loading result is achieved.
When it comes to the selection of gripper technology and design of the grippers, MULTIVAC has a significantly larger degree of freedom thanks to the use of innovative vacuum gripper technology in the food sector. A vacuum rinsing system, which was specially developed by MULTIVAC, enables the complete vacuum system to be rinsed with water and cleanser and then subsequently dried. Thanks to the design of the vacuum system, which has no dead space and can be safely rinsed, the vacuum gripper technology can be used in the food sector.
Unlike mechanical grippers, vacuum grippers allow the product to be introduced right into the pack cavity, and this means that significantly better loading results can be achieved. The vacuum gripper technology also offers significantly more freedom when loading several products into one or more pack cavities. This makes it possible to achieve significant efficiency gains.
“In order to meet the individual requirements of our customers, we of course use our modular design system with its standard components,” explains Peter Lenz. “But where required, we also develop gripper systems, which are specific to a product and ideally tailored to the particular application. Thanks to the large number of projects we have completed, we now have a wealth of experience in this area.”
All the solutions of course meet the demanding requirements of the food sector in terms of hygiene without compromise. The degree of product safety and shelf life, which is required in the food industry, can only be achieved through completely hygienic handling and by observing the relevant requirements of cleaning and disinfection.
Another process, which it is sensible to automate, is that of monitoring and inspection, since as an integral part of an overall automation solution, it ensures the maximum process reliability and pack security are achieved. Reliable inspection at high output can today only be performed with fully automatic solutions. Inline quality inspection normally also includes the automatic ejection of reject packs. In order to be able to guarantee the functionality of this process, it is also however necessary to have fully integrated line control.
MULTIVAC's product portfolio is rounded off with a wide range of integrated belt systems for product infeed and transport. The design of these systems is largely dependent on the product requirements and on the method of transportation to the packaging process.
03.12.2019