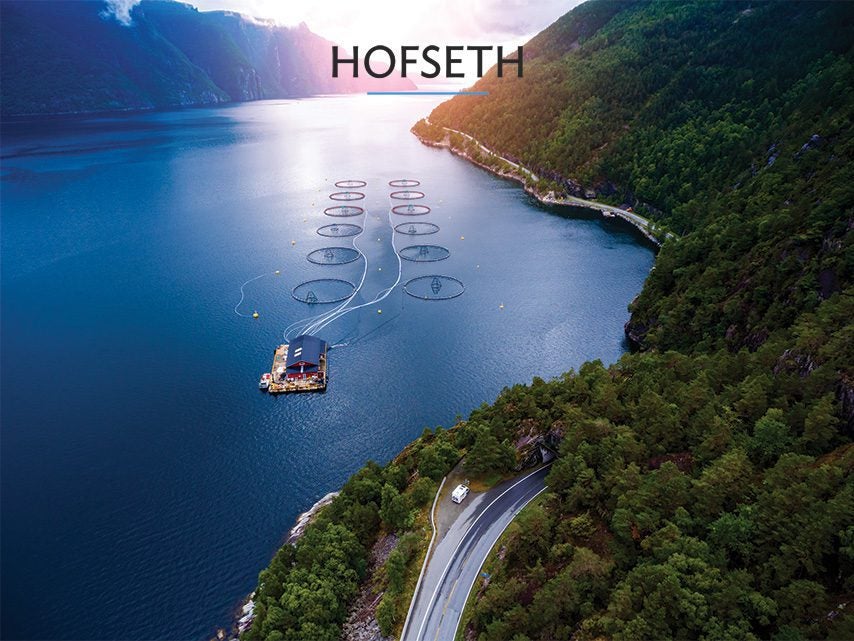
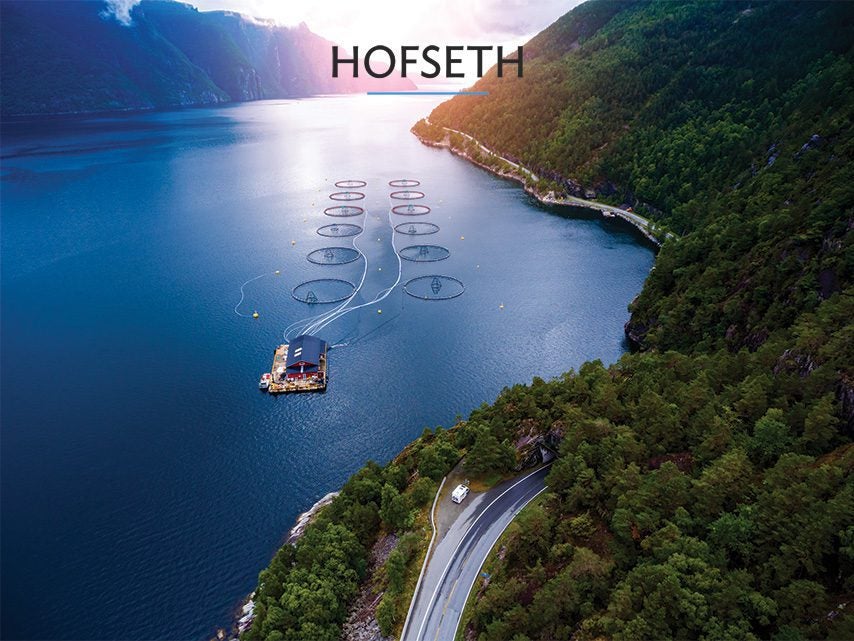
HOFSETH packs top-quality fish in many different variations and portion sizes: frozen and fresh salmon, hot- and cold-smoked salmon, salmon fillets, and marinated salmon in various flavours, as well as absolutely fresh sashimi salmon. The products are exported throughout the world, and 94 percent of production goes for export.
At HOFSETH the high-performance R 575 MF thermoforming packaging machine is used to produce the vacuum skin packs.
The R 575 MF was developed to produce MultiFresh™ vacuum skin packs in very large batches, and it has also been optimised to pack high products. The model offers the widest range of MultiFresh™ applications, and this allows the packs to be matched precisely to individual customer requirements.
At HOFSETH the R 575 MF is used to produce packs of fresh or frozen fish, where the pack cavity has a depth down to 10 mm and where the particular product can protrude up to 45 mm above the top of the pack cavity. The many benefits of the high-quality MultiFresh™ vacuum skin packs include the fact that the product is not distorted and retains its natural appearance. The vacuum in the pack contributes to an extended shelf life for the fish products. The delicate products are firmly located in the pack, allowing the retail packs to be presented either standing up or hanging, as well as lying flat.
“The R 575 MF is equipped with upper web heating, which preheats the upper web before it is transported into the sealing die. The film is then heated again in the dome of the sealing die, so that it can cling tightly around the delicate product without creasing,” explains Trond Lia, Sales Specialist at MULTIVAC Norway. The integrated upper web chain guidance on the MultiFresh™ thermoforming packaging machines ensures the upper web is firmly guided as far as the sealing process, since the film is held permanently under tension across the transport direction. This procedure ensures a high level of process reliability, and it also delivers very high pack quality irrespective of the machine speed.
With full-wrap labelling, which is often called D labelling or sleeve-style labelling, a label encloses four sides of a pack, similar to a banderole. Thanks to this, full-wrap labelling offers many possibilities in the design of the pack, and this in turn contributes significantly to increasing the attractiveness of these packs at the point of sale.
D labelling is then added to the finished packs, which are also equipped with an opening aid for easy opening. D labelling, which is also called full-wrap labelling, offers many possibilities in the design of the pack, and this in turn contributes significantly to increasing the attractiveness of these packs at the point of sale. Similar to a sleeve or banderole, the label is completely wrapped around all four sides of the pack. The L 310 conveyor belt labellers are currently still used as a stand-alone solution, and the product infeed is performed manually. However, all the line components are due to be integrated in future into the line and controlled by a central machine control, so the productivity and efficiency of the packaging solution can be increased still further. “In view of the ever increasing demand for D labelling, particularly from the UK market, we decided to purchase two conveyor belt labellers from MULTIVAC,” explains Finn Olav Stokkereit, CTO of the Norwegian Group. In the case of the skin packs produced at Ålesund, the label plays a particularly important role in increasing the attractiveness of the packs.
Reinforced by the very positive experience with the MULTIVAC Sales and Project team, the decision to purchase the labellers was also made in favour of the same specialist packaging company, since MULTIVAC’s solutions had always been considered ideal for the wide range of requirements: due to the extensive system of modular construction used by MULTIVAC, solutions for D labelling can be offered, which are designed very flexibly for a wide range of pack shapes and materials. This means the optimum labelling result can always be achieved, even when there are frequent changes of pack shape or design. “In addition to this, we have many years of expertise and can offer our customers solutions, which are tailored to their individual
requirements,” adds Trond Lia. “The critical factor is that the labelling systems are always matched to the labelling materials being used.”
The robust and low-maintenance L 310 labellers can run label widths up to 500 mm. At Seafood Farmers the labels are applied from above at approx. 15 mm away from the front edge of the pack, they are then adhered over the sides of the pack, before finally being fixed in place on the base of the pack by means of a pneumatically operated press-on unit.
The pack sizes vary between 120 x 200 mm and 200 x 220 mm. So batch changes can be carried out quickly and easily, adjustment units with position displays are used, which enable the label dispensers to be adjusted laterally and in height. The correct settings are displayed to the operator as a preview on the control terminal, and the corresponding values are saved in the particular recipe.
The weight of the individual packs is checked prior to labelling by the two new I 210 checkweighers, which were similarly purchased from MULTIVAC. They ensure only sufficiently filled packs make their way to the labellers. Each product is synchronised and monitored by means of line-motion control.
The feedback from the customer has been very positive. The high-quality and attractively labelled packs for the premium salmon products have been very well received and underline the product quality. Everyone at Seafood Farmers and HOFSETH is very satisfied with the results. “The investment has really paid off,” says Finn Olav Stokkereit, who was also very impressed with the
professionalism and expertise of the MULTIVAC team during the entire project management and implementation phases.
24.09.2018