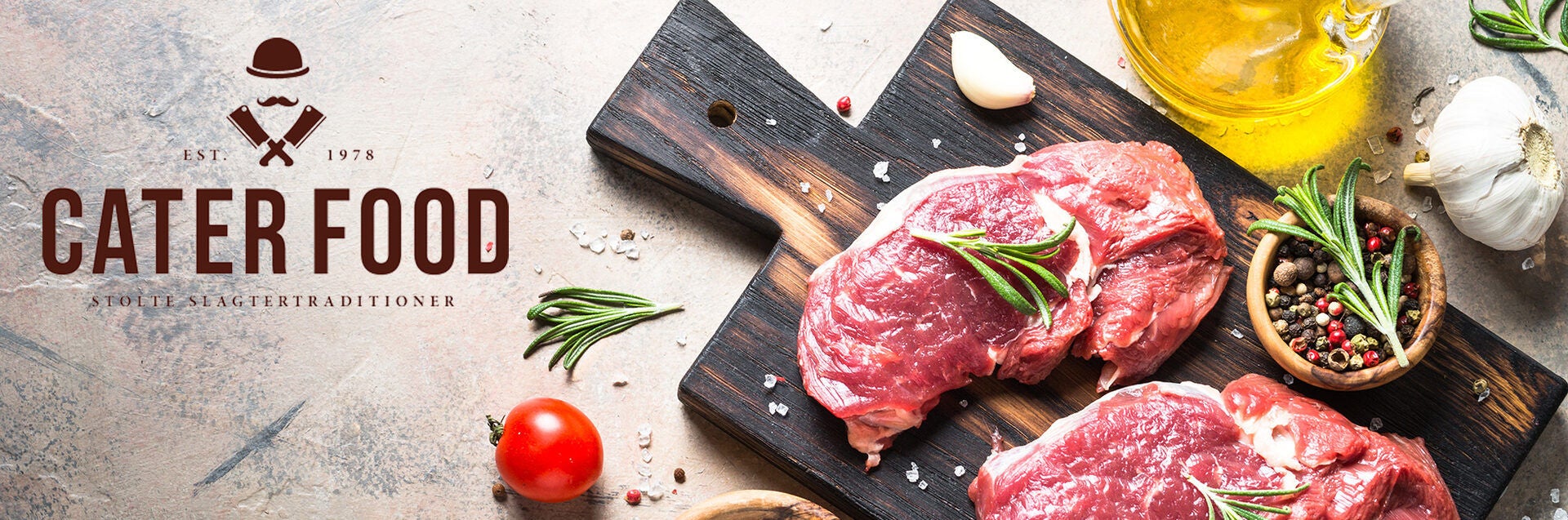
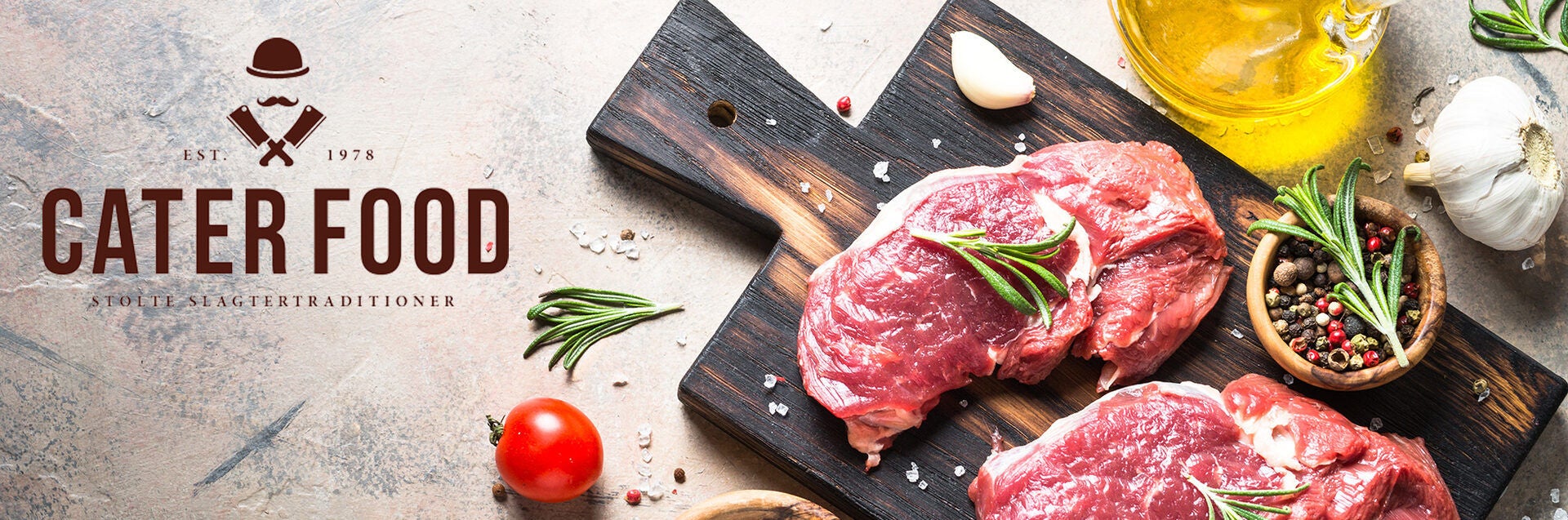
“Due to its many years of project experience and unique packaging expertise, MULTIVAC was always the first choice for us as a business partner,” explains Finn Jensen, CEO of Cater Food. The company had been using up to then a total of three thermoforming packaging machines at two sites in the North of the country. While the Mors site produces primarily minced meat and deli specialities, the Herrup site produces sliced products, ready meals and sous-vide products. The sous-vide products in particular are enjoying increasing popularity – Cater Food recognized this trend at an early stage and is now one of the largest Danish manufacturers in this sector.
The products are sold on the Danish market. Countless purchase orders with varying volume have to be processed daily by staff at high speed. “If a purchase order from a domestic customer arrives with us before 3.00 pm, the customer can expect to receive his delivery on the following morning,” explains the company boss.
In the case of the Herrup site, two thermoforming packaging machines, which were around 30 years old, had been used up to then, and their capacity limit had already been reached due to the permanently high production quantities. “In addition to frequent faults and breakdowns, the die changes were very time-consuming and spare parts were proving difficult to obtain,” says Peter Dalum Hansen, Technical Manager at Cater Food, looking back at the situation at that time.
At the second site in Mors one thermoforming packaging machine had been used up to then to carry out the daily tasks. “Thanks to the expert advice from MULTIVAC, we considered however the purchase of a traysealer in the light of the high pack weight of the minced meat,” says Finn Jensen. This was due to the fact, that Cater Food packs the minced meat in portions of 1 kilogram and 2.5 kilograms. The company also wanted to achieve an extended shelf life for the sensitive product by packing it in modified atmosphere. “The demand for MAP packs is rising - one aspect, which was also crucial in our investment decision for the factory in Mors,” confirms Finn Jensen.
In addition to this and the improved control over a more stable workflow, the aspects of ease of operation, future-proof technology, pack quality, price-performance ratio, expert service and support as well as low levels of downtime were also top priorities for Technical Manager, Peter Dalum Hansen.
When it comes to technology, needs-based machine equipment, pack design and suitable materials, the company placed its trust in MULTIVAC’s expertise - both for the traysealer and the thermoforming packaging machine.
Since August 2017 the R 515 thermoforming packaging machine that is equipped with four format sets has replaced the two earlier models in Herrup. The R 515 is specially designed for the requirements of the fresh meat industry. Typical applications are for example large ham packs as well as wholesale and transportation packs. In addition to vacuum packs, it is also possible to produce packs with modified atmosphere (MAP) at high output.
As an option, the R 515 can be complemented by a jumbo film unwind for the lower web, so that changeover times for film changes can be reduced significantly. In addition to this, the model also offers an optional quick-change system for forming and sealing dies. This makes the conversion to other pack formats much easier - one aspect, which was a high priority for Cater Food, since meat products and ready meals have to be packed at Herrup in a wide range of variations and pack formats. The spectrum ranges from large pork roasts to smaller meat cuts of one to two kilograms.
A new packaging solution also went into service at Mors before the machine in Herrup. The complete line consists of the T 600 traysealer, a two-track tray dispenser from a third-party supplier, an infeed conveyor and a L 300 labeller. It replaced the previous thermoforming packaging machine and is used for packing minced meat in large PP trays with a weight of 1 kilogram and 2.5 kilograms.
The T 600 is the smallest MULTIVAC traysealer, which can be fully integrated in an automated line. The machine can be scaled and individually equipped as required. It is suitable for producing MAP and EMAP packs or vacuum skin packs in small and medium-sized batches.
The L 300 conveyor belt labeller, which can be used very flexibly, applies labels efficiently and reliably to the top and bottom of packs as well as over the edge of the pack, and it can therefore be used for all standard labelling tasks. It can be integrated into the controls of the packaging machine.
Everyone at Cater Food is very satisfied with the two new packaging solutions: both the thermoforming packaging machine and traysealer line achieve the higher output required to meet the strong demand - and all this without additional operators. The downtime has been reduced significantly, since operators have been able to handle die changes quickly. The pack quality from both the thermoformed packs and MAP traysealer packs for minced meat is excellent, as the company is able to “discern from the very positive feedback from our customers,” says Finn Jensen.
He looks to the future with optimism. “We have found the optimum solution with both new packaging machines, so that we can satisfy the requirements of our customers and position ourselves better in the market, particularly as regards our minced meat packs. And last but not least, we have learnt that with the right packaging solution one can pack much larger quantities of different products efficiently and economically.”
For Cater Food MULTIVAC is not only a machine supplier, but also a genuine partner thanks to the positive experience with the packaging specialist. The very constructive dialogue from the start with all the MULTIVAC staff in the Spare parts, Sales and Service departments, as well as with the Management at MULTIVAC, has ensured that all the challenges in Herrup and Mors have been satisfactorily met.
Which aspects of the two investment projects caused a few headaches? Technical Manager, Peter Dalum Hansen, replied with a smile: “Initially we had no concrete notion of how we would use the MAP technology to produce the packs for the larger minced meat portions. But MULTIVAC gave us so much good advice, that ultimately we achieved exactly the packs that we need to remain competitive.”
There were no unexpected problems with the installation of the two machines. The thermoforming packaging machine was positioned and assembled in Herrup in just a single day. The connections for power, inert gas and water were made on the following day, so that the first packs were able to be produced. On the third day the machine was put into normal operation. The installation of the traysealer in Mors also went without problems. “Today we are producing at 12 cycles per minute with 2.5 kilogram portions and 21-22 cycles with 1 kilogram portions. This means that we have achieved our primary objective,” adds Peter Dalum Hansen.
24.09.2018