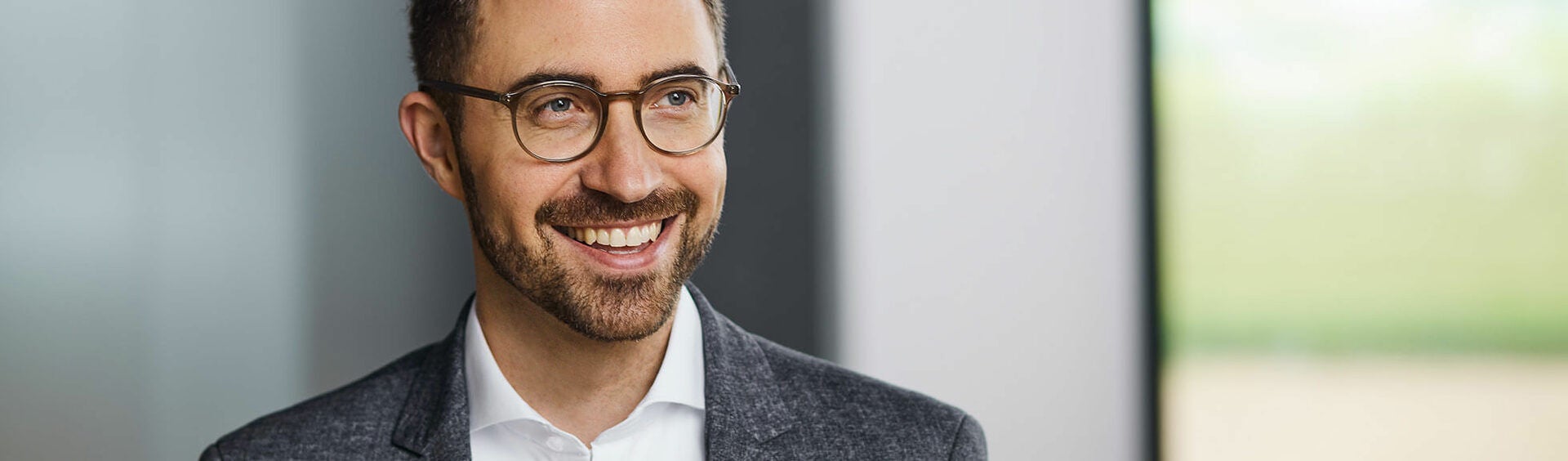
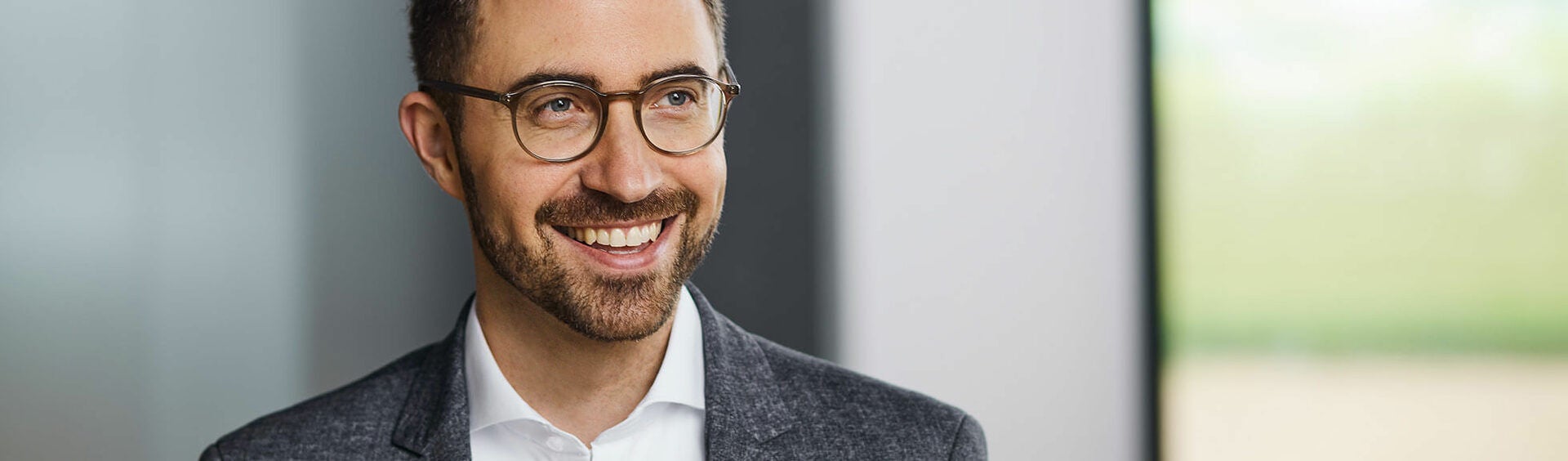
Corona has accelerated the already growing and natural development of digital technology: for example, services such as Remote Assistance or Smart Services have overnight become more relevant than ever, since restrictions on travel and access to companies have grown during the pandemic. We have also seen a similar trend in the area of collaboration, where video conferencing has become the new standard for communication.
But it has also become clear, particularly during recent times of relaxation, that personal contact can not be underestimated for certain tasks. For the foreseeable future we will still need service technicians to carry out complex repairs or diagnostic work on our machines. And important negotiations or personal discussions will still preferably take place in future on a face-to-face basis.
The positive aspect of the pandemic in this regard, is that we are all now familiar with both worlds, and even "digital latecomers" have come into contact with digital tools. I think that in future a healthy mix will be productive - and we will go forward reinvigorated and imbued with the knowledge from the corona crisis, as to when and to what degree a physical presence is sensible and advisable.
The growing expansion of digital services in the B2C sector is certainly a significant driver for B2B business. Consumers are becoming ever more used to accessing electronic services via smartphone app or wifi, and for example controlling or monitoring their equipment remotely. This trend is also awakening similar expectations in production environments. It is of course a precondition, that the status of a machine can be called up, so that the manufacturer can support the user in optimising the machine.
There is also of course a discernable pressure across all sectors to increase efficiency. Companies are looking for possible ways of increasing the transparency and ultimately the efficiency of their production environments, so that costs can be saved or output increased. Such optimisation projects require however the monitoring of essential key performance indicators, so that progress can be measured and reference values established at the outset.
We are seeing the largest number of enquiries from our customers in the food industry. We have already successfully concluded several digitalisation projects in this sector. Our customers in the medical and pharmaceutical industries are still however hesitant, when it comes to digitalisation. This is largely because these companies are very sensitive about connecting their machines to the cloud and data processing services. We are however optimistic, that in the near future we will be able to connect one of our customer's machines in the medical sector.
As regards the various regions of the world, we can proudly point in 2021 to the USA. MULTIVAC USA successfully connected the first customer's machine at the start of 2021, and by the middle of the year there were already around 20 connected packaging machines - clearly a rising trend. We are also working successfully with other subsidiaries around the world on connecting our packaging machines: for example in the Czech Republic, New Zealand, Chile, Great Britain and the Philippines.
One thing I would however like to emphasize: fundamentally we do not focus our digital solutions on certain target groups or company sizes. This is because digitalisation holds great potential for optimisation at smaller and medium-sized companies as well as large businesses. The range of possibilities extends from predictive maintenance and Remote Assistance right up to our X-line series of thermoforming packaging machines and traysealers. These machines are able to set their own parameters to the optimum operating point, thanks to innovative features and a comprehensive sensor system, and they can produce packs of the highest quality and with the greatest operating convenience without any loss at the start of production
Thanks to our myMULTIVAC customer portal, we can also offer all our customers a central, digital point of access. There they can not only order spare parts and consumable materials online, they can also manage their complete installed base of machines, as well as enter directly into Smart Services. MULTIVAC's Smart Services are structured on a modular basis, and they can be activated gradually depending on the requirements of the particular company and the availability of investment.
We connected the first machines to our cloud solutions in April 2018. But it was in the first half of 2021 in particular, that the subject of digitalisation gained enormous momentum: within 6 months from the beginning of January to the end of June 2021, we managed to more than double the number of connected packaging machines. Our objective now is to increase this number by another 50 percent by the end of the year.
By producing the MULTIVAC Smart Link, we have developed a secure retrofit solution, which enables digital services to be used without a large initial investment, even on existing machines that are suitably equipped. The two-piece hardware, consisting of an industrial computer and Internet router, is installed in the machine on-site at the customer. This hardware is also the prerequisite for Remote Assistance via VPN.
In addition to this, we decided in the third quarter of 2020, that we would preselect these infrastructure components. This meant that the hardware was preselected for larger thermoforming packaging machines and traysealers, so that the number of connected packaging machines could be increased still further. Currently every fifth machine, which we supply with the MULTIVAC Smart Link, is subsequently used for Smart Services and connected to the MULTIVAC Cloud.
In our view, it is particularly smaller and medium-sized companies, which can benefit immediately from connecting their machines to the MULTIVAC Cloud and using the available Smart Services. Their production can be automatically monitored and optimised, and all this without further costs or investment in additional software.
But there are also of course many benefits for larger companies as well, and this is starting to become visible in the marketplace: we have already noticed, that a high level of IT expertise is now a basic requirement by many such companies for any manufacturer of machines. Services, which we now regularly provide for our larger customers, include the customised installation of Remote Assistance, the integration of machines into the customer's own network, and the individual transfer of data on a Cloud-2-Cloud or Edge-2-Cloud basis.
That is correct. I would first like to mention here our MULTIVAC Pack Pilot, which is cloud-based software that supports operators in setting up the packaging machine to the optimum degree, without a high level of expert knowledge being required. This is available for the RX 4.0 thermoforming packaging machine as well as the TX traysealers - and it ensures the highest possible output is achieved, as well as consistently high pack quality and maximum process reliability.
Today there is also strong demand for a transparent overview of the production environment, and this is precisely what is offered by our Smart Production Dashboard. Of equally great interest to customers is our Smart Log Analyzer service, which is an intelligent tool for identifying potential areas of optimisation. It reads the machine's information and fault memory, which we can subsequently analyse. The data capture ranges from higher-level information, such as the machine's productive time, right up to individual events that cause downtime.
In addition to these, there are other services available to customers. These include Smart OEE Analyzer, which is similarly a strategic instrument for increasing efficiency. And Smart Machine Report enables rapid and meaningful comparisons to be drawn, while Smart Data Backup is essentially a tool for backing up valuable data.
Transparent processes and process data in real time make an important contribution to the efficiency and cost-effectiveness of systems and lines. Thanks to our digital products and services, we can offer our customers innovative solutions for monitoring, controlling and optimising production - even networked across all locations to facilitate comparison. Simple, convenient and "live". This means our customers benefit equally in all operational and strategic areas, from machine operator to factory manager.
As well as constantly working on our existing services, we are also developing new solutions for our product range. Another Smart Service that we are already able to announce is MULTIVAC Watchdog, which will enable the status of machine components to be monitored. Data from the machine is monitored in real time, and it notifies the user via an alarm system, if maintenance work is due, or if there are any abnormal developments in the machine's performance. As well as optimising process times still further, the objective is to prevent any downtime at all, or at least to reduce it through short reaction times.
We are also continuously expanding the number of machine types, which are compatible with our Smart Services: whereas at the start it was only one machine type, today we can support more than ten different machine types, which are capable of being connected to MULTIVAC Smart Services. Our objective is to offer our customers not only analysis of individual machines, but also added value through analysis across the entire line.
Since we began our digitalisation initiative in 2017, we have worked very closely with our customers, so that we could integrate customer feedback into our developments at the earliest possible stage. We regularly hold so-called Customer Reviews, and these give our customers the opportunity to share their views about new services or functions with us.
In addition to this, we learn about each company's requirements at every visit, by observing the processes in the production environment and the needs of each particular customer. We have inspired many of our customers in this way - and they are an important source for the further development of our products. Many aspects of our Smart Production Dashboard for example were based essentially on the requirements from several of our customers.
But naturally we at MULTIVAC have the incentive to remain ahead of the pack with our own solutions, and to always provide valuable new ideas to our customers. For example, our Production Flow feature in the Smart Log Analyzer was one such innovation that was driven by us, and which today is very popular among customers seeking to optimise their machine performance.
Digitalisation is of great importance at the current time. This is because digital tools facilitate virtual and hybrid collaboration not only in the office but also in manufacturing environments. Thanks to our Smart Services, we can offer service technicians and customers alike the opportunity of increasing productivity through data analysis and collaboration with MULTIVAC, without having to hold face-to-face meetings. Our customers benefit twice from connecting their machines to our MULTIVAC Cloud. Firstly, they themselves can gain access quickly and easily to the data and information from their machines. And secondly, they can share this information with MULTIVAC Service, which is then able to troubleshoot in a rapid and targeted way, or even make a proactive contribution to preventing the problem arising again.
10.10.2021