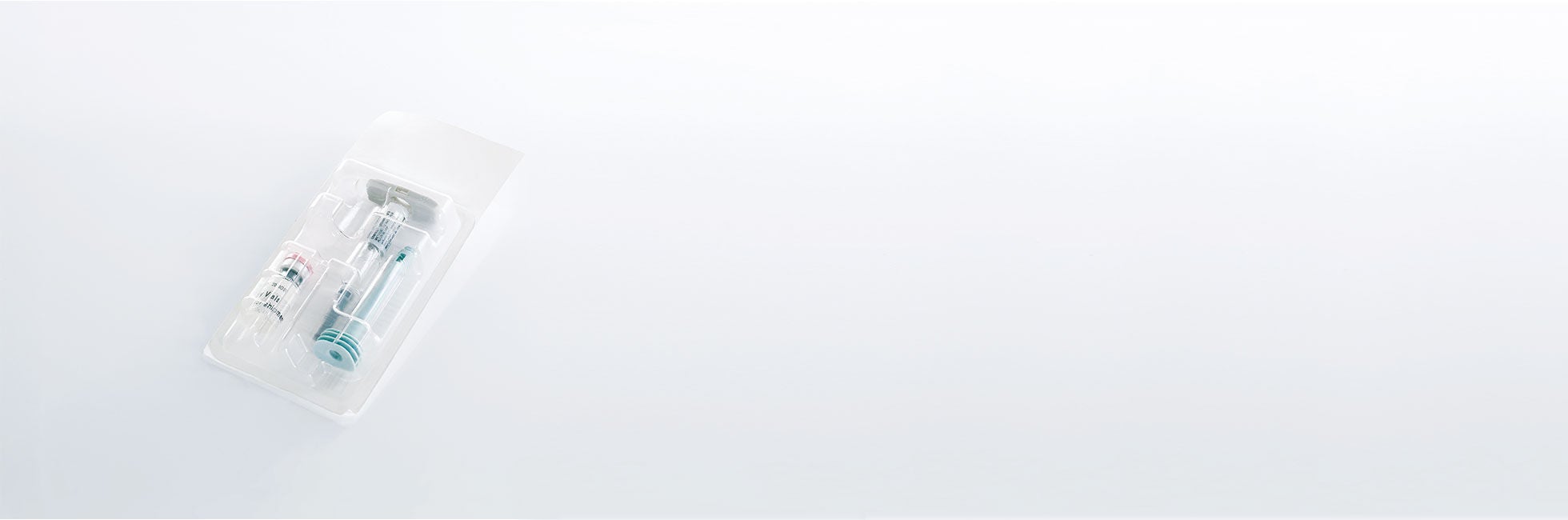
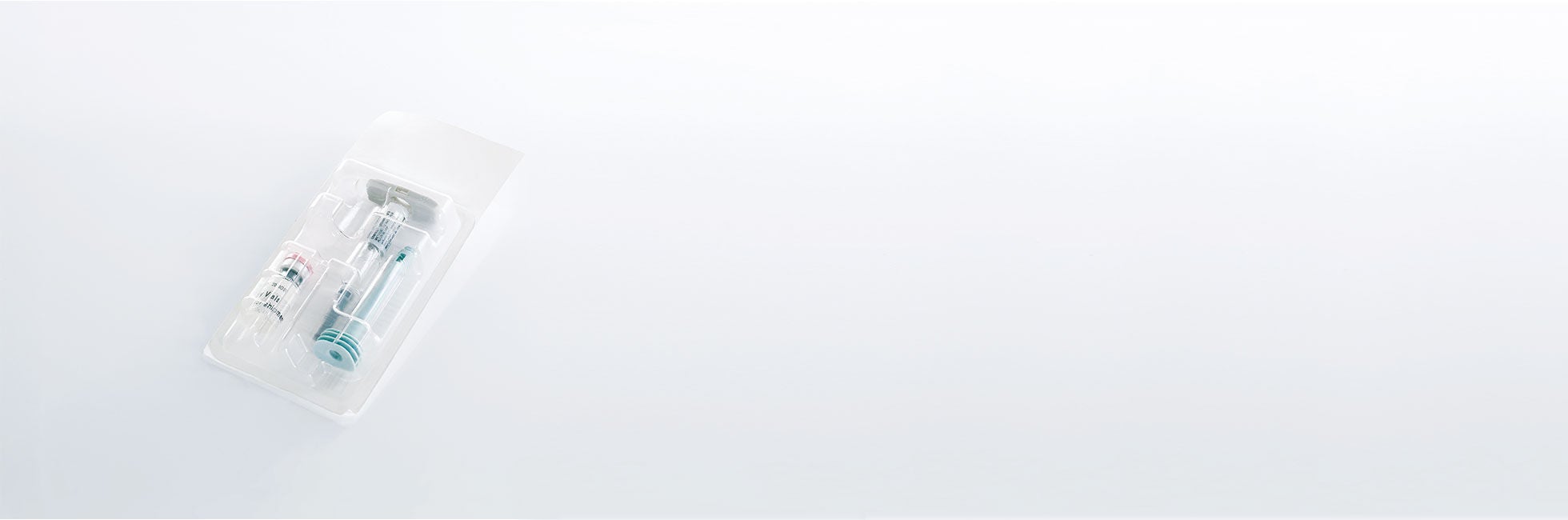
This concept involves a circulating carrier system for loading usually several different products into pre-made blisters or trays with several pack cavities. The flexibility of the design is such, that the tray carrier can be used for either individual production in very small batch sizes (even from batch size 1) or for producing much larger numbers of a particular product. In the case of small batch numbers, the loading is usually manual, while it can also be automated for higher throughputs.
Inspection systems can also check the completeness of packs, as well as the correct positioning of the loaded products. Reject or empty packs are reliably ejected, while good packs are fed to the traysealer. The correctly filled trays are sealed to an upper web in the packaging machine, and a wide range of materials such as multi-layer films, Tyvek® and paper or aluminium composite materials can be used. When the sealing process has been completed, the finished trays are inspected for completeness and quality. The good packs are then transferred to a downstream machine, for example for loading into boxes, where so-called “in process control” (IPC) can be used. Reject or empty packs are ejected from the process.
The packs generally contain several components, such as pre-filled syringes, needles, vials, pack leaflets and smaller parts such as caps or sleeves. If sensitive products are being packed, multi-compartment trays are often used, where the cavities are formed in such a way, that the products are firmly fixed in the tray, so that they can not slide around or be mechanically damaged. The trays can be made from a wide range of materials - a typical example is an APET blister, which is sealed to an upper web of paper or Tyvek®.
However, such complicated blister formings are often not self-standing. Since loading the packs requires by definition a high level of positioning accuracy, it is expedient to use special infeed equipment in the form of carrier systems and to transport the trays by means of these carriers to the individual process stages of the packaging procedure. One such solution is the MULTIVAC Tray Carrier, which is ideally suited to automatically infeeding and loading products, as well as discharging the finished combi packs. It offers a very high degree of flexibility for any batch size being processed.
The MULTIVAC Tray Carrier is generally combined with an automated MULTIVAC traysealer. A MULTIVAC tray denester is used for loading the empty trays into the carriers.
⇒ The T 700 traysealer can be equipped with a tray carrier system
Depending on the requirements with regard to size and number of trays, the tray carrier solution can be configured accordingly. If small batches are being produced, the circulating system can, for example, be equipped with just one tray carrier, while higher cycle rates might require several tray carriers to be equipped.
The loading system first uses an inspection system to check, whether all the cavities of the tray carriers have actually been loaded with empty trays. The carriers are then transported via a belt system to the next process stage. There, the trays are automatically filled with the individual products.
The often automated infeed of the different product components is handled by various systems, which are individually designed for the particular product. Pre-filled syringes, for example, are fed in by means of so-called object carriers for the pick & place procedure. Small components such as caps, sleeves, or needles are often supplied as bulk products to a vibrating unit where they are separated and aligned. Products, which arrive from an upstream process stage such as a marking or labelling solution, are fed in via a roller conveyor or belt system.
Each tray is filled with the corresponding products by means of pick & place. Depending on the product and required cycle rate, MULTIVAC’s modular handling modules are equipped with one or more robots. Using suitable grippers, they pick up the particular products and place them precisely and reliably in the corresponding tray cavity.
Camera inspection systems are used to monitor the completeness of the finished loaded trays. If the packs are OK, they are sealed to the upper web in the traysealer. The sealed packs are then transported onwards in the tray carriers to the removal station. There a further handling module removes the trays from the tray carriers. Depending on the requirements, the trays are either removed singly or as multiples. The good packs are then transported on a transport conveyor to the next packaging stage, such as loading into boxes.
The ejection of reject packs takes place during the removal process, and this is always performed on an individual pack basis. Empty packs or incomplete packs can be fed back again into the process. Reject packs are ejected completely from the packaging procedure. Random sampling removal as part of so-called “in process control” (IPC) can be performed at any time. As part of the “good philosophy” principle, the removal process is designed in such a way, that the robot first ejects the reject packs and then places the good packs on the transport conveyor. This contributes again to the process reliability of the system.
The reliable and efficient packaging solution is composed of simple individual modules, which are perfectly matched to each other. Thanks to its modular construction, the system can be ideally designed to the particular requirements, and the range extends from batch size 1 to large production numbers.
Tyvek® is a registered trademark of E. I. du Pont de Nemours and Company
07.06.2018