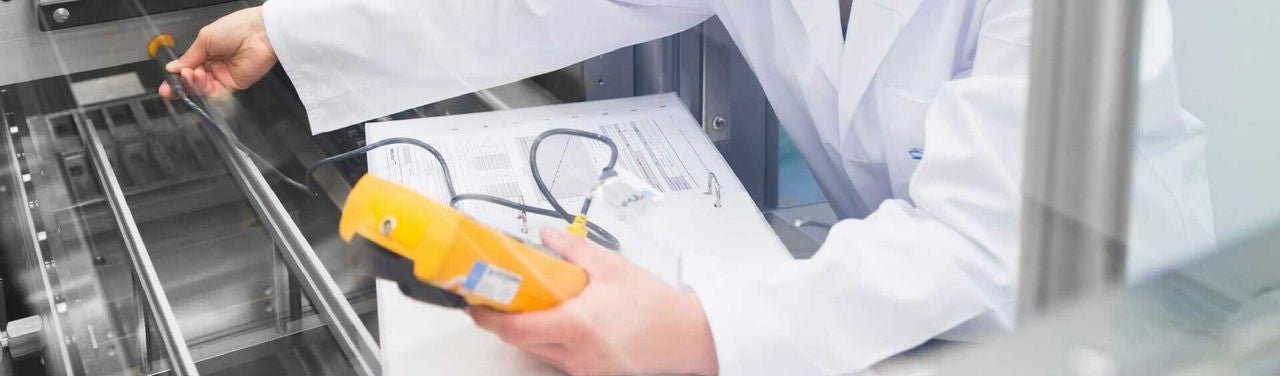
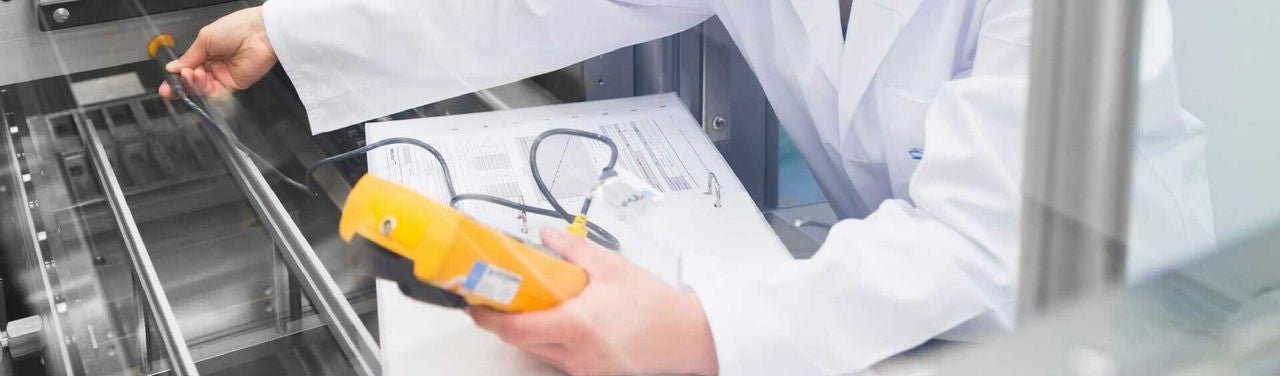
In order to guarantee the quality of a medical product, it is necessary to take its complete life cycle into consideration. This begins in the initial phase with the design of the product, and it only ends at the moment, when the product is removed from the market and replaced with another.
Process validation is understood as the documented proof that the manufacturing process is consistently meeting the defined quality requirements specified during the design phase of the product, with a high level of reliability and reproducibility. Process validation is subject to continuous verification during the complete life cycle of the product, and it consists essentially of three phases: the process design phase, the process qualification phase and the process verification phase.
The process design phase begins with the design of the product. The qualification phase starts before production. Verification takes place during production. Process validation has to be performed not only for every new product introduced, but also carried out from the start for any change to an item or process stage.
The process is defined during this phase. Process design takes into consideration all the results from the basic research, as well as knowledge gained during the development of the product.
The main objective of this phase is to identify the process variables necessary for the defined and expected product quality. These process variables in a thermoforming packaging process can, for example, be parameters such as sealing temperature, sealing time and sealing pressure.
The procedure is made up in the first instance from the definition of the quality requirements and the resulting critical quality features. One example of the "patient safety" aspect is the quality requirement for pack sterility. The necessary quality features here include a specified residual film thickness for the formed lower web, as well as a complete seal seam and a specified seal seam strength.
After the quality features have been defined, all the process stages necessary for reliable manufacturing of the product are then compiled. There then follows a risk analysis for each individual quality feature and process stage, so that it can be assessed, at which point there is a high, medium or low risk.
In the case of all process stages with a high risk potential, a suitable monitoring strategy is developed, which flows into the definition of the appropriate process parameters. If, for example, the sealing process in a thermoforming packaging machine is rated as critical for the sterility requirement, the quality monitoring strategy demands critical process variables are defined within a certain tolerance range.
One concrete example is specifying the temperature range for sealing. If, for example, during trials a sealing temperature in a range of 160 - 180 °C has been defined for a faultless seal, a temperature range that moves within this tolerance would be specified for the monitoring strategy.
Only when it has been established that the monitoring strategy includes all the relevant parameters, are all the values specified in this process stage adopted into the User Requirement Specification for the new equipment.
Process qualification is the next phase in the validation process. This phase's main objective is to produce proof that the processes fulfil the defined quality features and are reproducible to be used for commercial production. Process qualification is performed before the start of commercial production. Risk analysis forms a very important part here.
Process qualification usually begins with the creation of the User Requirement Specification, which represents the basis for the design and layout of the equipment. After the equipment is completed and following a successful factory acceptance test, it is then taken into the production environment. After the equipment has been installed at its destination, the site acceptance test and subsequent calibration of the equipment take place. The installation qualification (IQ) ensures the machine equipment has been correctly delivered and installed as specified.
During the operational qualification (OQ), the packaging line is tested and checked to ensure all the defined process parameters are satisfied. It includes the basic functional tests for all the relevant machine components. The performance qualification (PQ) takes place at a subsequent stage. This involves an extended test run, in which the packaging line produces several batches of the actual product based on commercial batch sizes in production. After the PQ has been conducted, the process qualification for the equipment is completed, and commercial production can then begin.
After a new or altered product has been launched on the market, it is essential to permanently monitor the production process and continue with the process documentation. Process verification ensures all the required quality specifications for the overall process are met during the entire life cycle of the product. Implementing a strategy for monitoring all the critical quality features of the process is indispensable. The objective of this phase is to maintain trust in the process. This includes continuous testing and measuring procedures, so the production process is kept to a monitored status.
If there is any change to a product, process or piece of equipment, it must be ensured that the new parameters can similarly be reproduced consistently. Based on a new risk analysis, it must also be defined whether re-qualification is necessary. In this case, it should be ensured that all the changes, which have led to this re-qualification, are seamlessly documented. Finally, it is necessary to regularly carry out the equipment's calibration to make sure no other changes or alterations have occurred in the process.
Digitalisation of the processes makes an essential contribution to process validation. This ensures that ever more comprehensive process data is made available, which makes monitoring easier and contributes to a greater understanding of the processes.
The effort and the complexity of the subject, which are an integral part of process validation, provide manufacturers of medical products with a challenge that usually implies a significant overhead. As a supplier of complete solutions, specialised in fulfilling the particular requirements of the medical products industry, MULTIVAC is able to provide its customers with professional support - not only thanks to the decades of experience in packing medical products, but also due to its knowledge of the market and its high level of expertise in medical applications.
16.11.2020