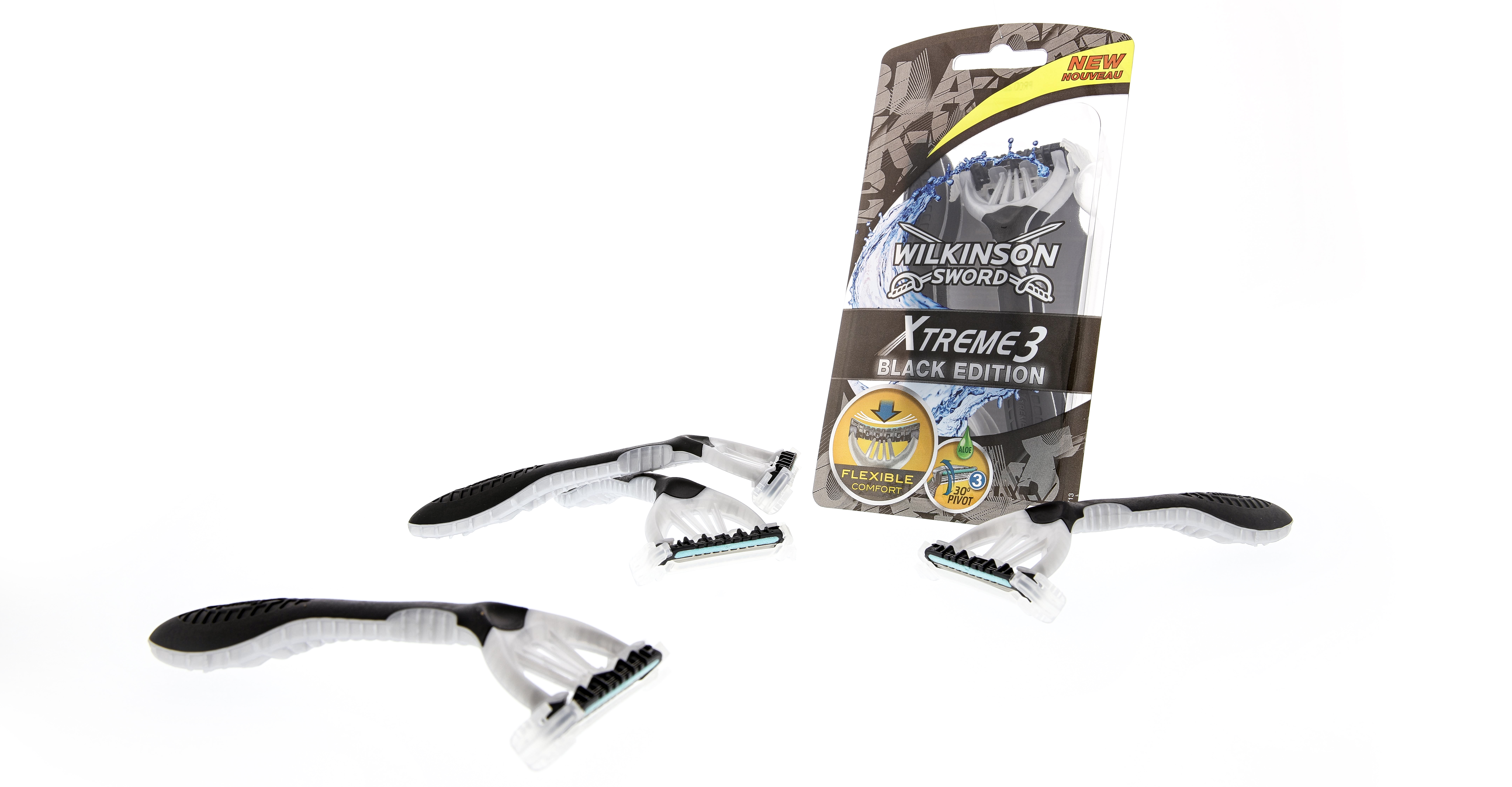
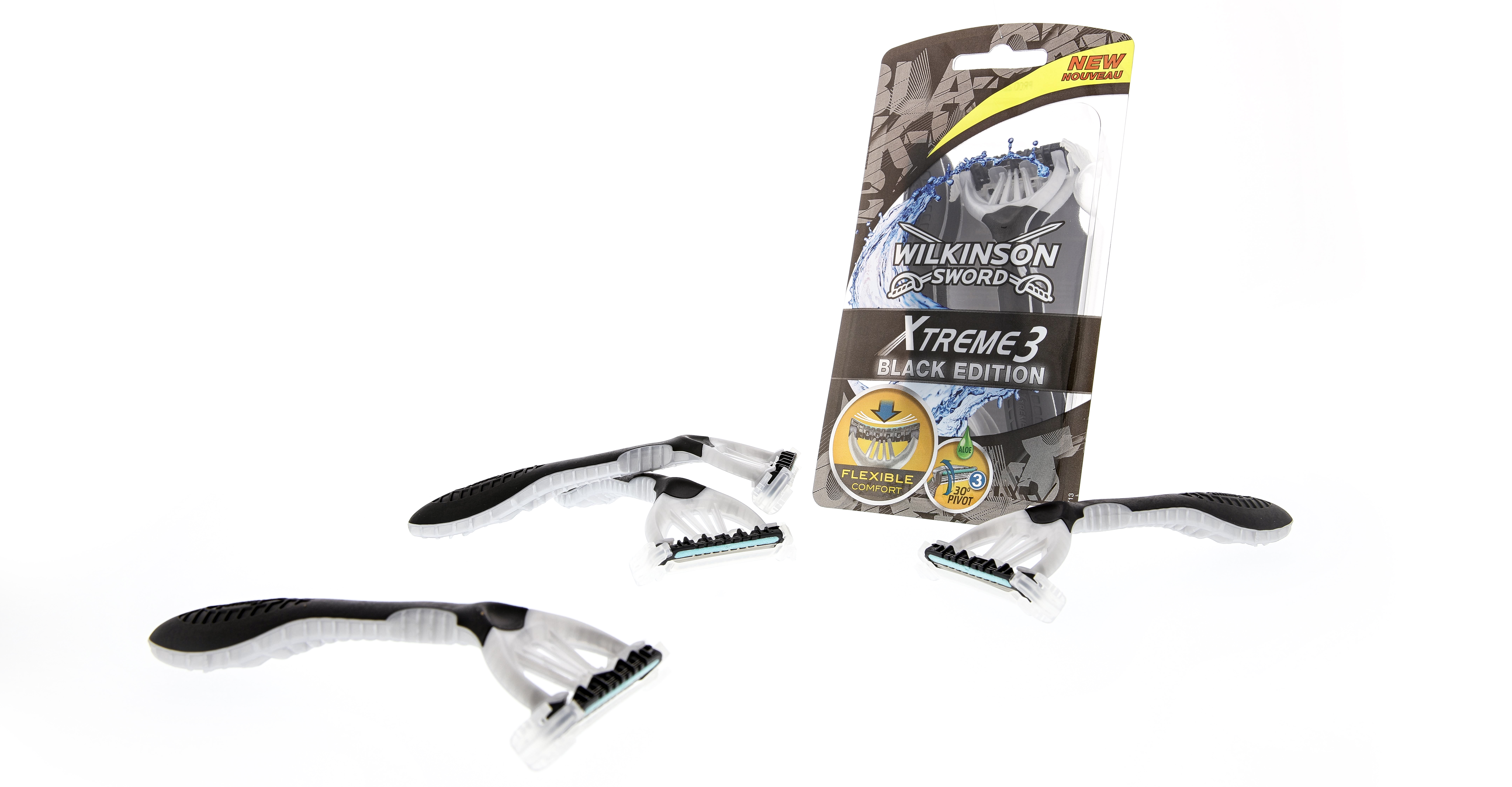
When Wilkinson Sword GmbH moved parts of its production from Solingen to Teplice in the Czech Republic, it was also necessary to replace an old packaging machine, which was more than ten years old. Defi nition of the tasks for MULTIVAC: Absolute adherence to delivery date, the integration of existing line components and above all the guarantee, that the new pack for the Xtreme 3 disposable razor would not be any different from the products, which were already well known in the market.
Wilkinson Sword GmbH has been based in Solingen for more than 50 years. The company is part of the American Edgewell Group, which arose in 2015 from the splitting of the US-based Energizer company. A total of 550 staff are employed in Solingen, known in Germany as the “Bergische Klingenstadt” because of its blade-making industries. The company produces around 600 million razor products per year for the European and international markets. The product range comprises the entire collection of razors and blade products – from the traditional twinbladed razor up to three- and four-bladed products and even a six-bladed razor. The Wilkinson brand looks back on a long history. It is very well known to consumers.
The company produced its fi rst razor blades in 1898 – after 100 years of manufacturing swords and pistols. The “Pall Mall” safety razor was the fi rst of many innovations. According to Carsten Meyer, Project Manager at Wilkinson, “other milestones in the success story were the development in 1962 of the fi rst three-coated blades. This enabled us to start a revolutionary development in blade technology. In 1992 there followed the Protector with its ergonomic design. And in 1994 the fi rst razor for women was launched on the market.” There then followed the Quattro products and Hydro series as well as many other developments, which have become a fi rm part of daily grooming and beauty care.
Since January 2017 a R 535 thermoforming packaging machine has been in use in Teplice for packing the Xtreme 3 disposable razor. Depending on the number of razors, they are packed in different depths of blister packs, which are made of rigid fi lm and an upper web with a high-quality design. There are three standard packs as well as two promotion packs, which in addition to the razors contain a “give-away”, such as a small container of shaving foam. APET lower webs of various thicknesses and register-printed upper webs are used to produce the packs. Two turntable machines are linked to the packaging machine. The turntables, together with the discharge conveyor to the boxing machine, were already present and had to be integrated with the new R 535 thermoforming packaging machine as part of the installation. A handling module automatically loads the razors into the pack cavities. The razors are prepared on a transport system for being picked up by the handling module. This involves separating the products and aligning them sideways. The handling module packs up ten razors per cycle and loads them into the pack cavities.
Before the packs are loaded with razors, a card loader dispenses pre-printed, coloured card inserts into the pack cavities, and the products are then placed on the inserts. The pre-cut inserts contain multi-language product information and the EAN code for pricing at the point of sale. A barcode reader checks this information during the packaging procedure, so that any discrepancies between the information on the insert and the pack content can be detected immediately, and the faulty packs are then ejected from the process. This means good legibility of the EAN code is essential. During this process stage, the lower web is provided with a date code, which is applied in the area of the euro slot. This is done with a direct web printer. After the packs have been sealed, a decorative label can be applied to the promotion packs; the standard packs however are not labelled. A H 052 handling module removes the good packs directly from the complete cutting tool on the packaging machine and places them on a transport conveyor, while the reject packs are ejected immediately from the conveyor. The weight and therefore the completeness of the packs are checked by means of a checkweigher – there is also at this stage a comparison between the information on the card insert and the actual pack content. The packs are ejected even if there is only a small discrepancy from the target weight. If the packs are OK, they are fed via a transport conveyor to a boxing system, where they are packed into boxes. A palletiser then makes the boxes ready for dispatch.
The cooperation from MULTIVAC was seen as being particularly helpful in this project. Carsten Meyer praises here particularly “the professional project support, the extremely good team and above all a customer-focused attitude to solving problems.” Thomas Wolzenburg, Sales Manager at MULTIVAC, adds: “The Wilkinson project was carried out here in Wolfertschwenden by two project managers with extensive practical experience. While one project manager concentrated on the packaging machine, the other focused on the linking to the automation components. This meant we could be sure that the individual modules were perfectly designed for the R 535 and the requirements in Teplice. In addition to this, staff from our international Service organisation were involved when the machine was put into service, and the local Service Center in the Czech Republic ensured that, together with their German colleagues, the packaging machine was integrated smoothly into the existing line structure.” The assessment of the new packaging solution by all those in Teplice is already very positive, even though the machine has only been in operation for several weeks. The output of 210 razors 94 | PACKS FROM AROUND THE WORLD | WILKINSON SWORD GMBH | UPDATE ´17 4per minute, which was specifi ed in the project objectives, is consistently achieved. Thomas Wolzenburg adds: “The cycle output is however constantly at the limit. This is due to the fact, that in all cases several products are being loaded into a highly complex pack cavity shape.
This can only be achieved by a high-performance thermoforming packaging machine, which functions absolutely reliably and offers equipment options that guarantee maximum machine availability.” To this are added the special demands, particularly the infeed and positioning of the products, which are extremely challenging but ensure a high level of effi - ciency is achieved throughout the entire packaging procedure. Carsten Meyer also confi rms the signifi cant quality improvements in the unchanged design of the packs: “The visual appearance of the seal area has been optimised. We also now have a signifi cantly more rigid blister, even in the corners of the packs. This is due to the change in the thermoforming process and the use of a sophisticated forming system, the so-called “positive forming process”, together with double “sandwich” preheating.” This ensures the products with their complex shape always fi t precisely into the accurately formed pack. Equally important is the consistently even forming of the thermoformed fi lm, as well as the uniform residual fi lm thickness and a high degree of fi lm transparency. The information and barcodes on the card inserts must be easily legible. A further benefi t of the machine: since the heating for the forming station is open when the machine is still, the fi lm can not heat up in an uncontrolled manner. Stop-and-go operation is therefore possible without problems. The operators are also very keen on the solid R 535 machine, because it is easy and reliable to operate thanks to its user-friendly control terminal with touchscreen.
The biggest challenge with this project was not only linking the machine to the existing line modules and retaining the complex pack design, while at the same time improving the pack quality, but also above all – and all those involved are of one opinion – adhering to the very tight time schedule. Carsten Meyer: “Adherence to delivery date was crucial to us, so that we could avoid production loss. The supply chain could not be interrupted during the transfer phase. MULTIVAC was able to assure us of this – and also adhered to it.”
28.02.2017