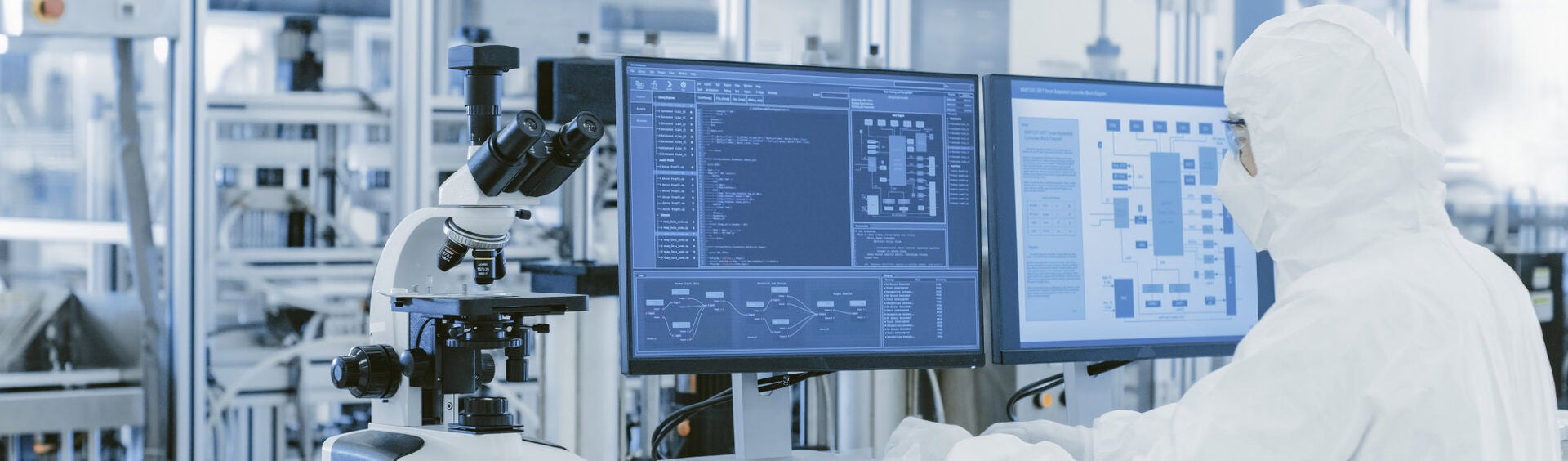
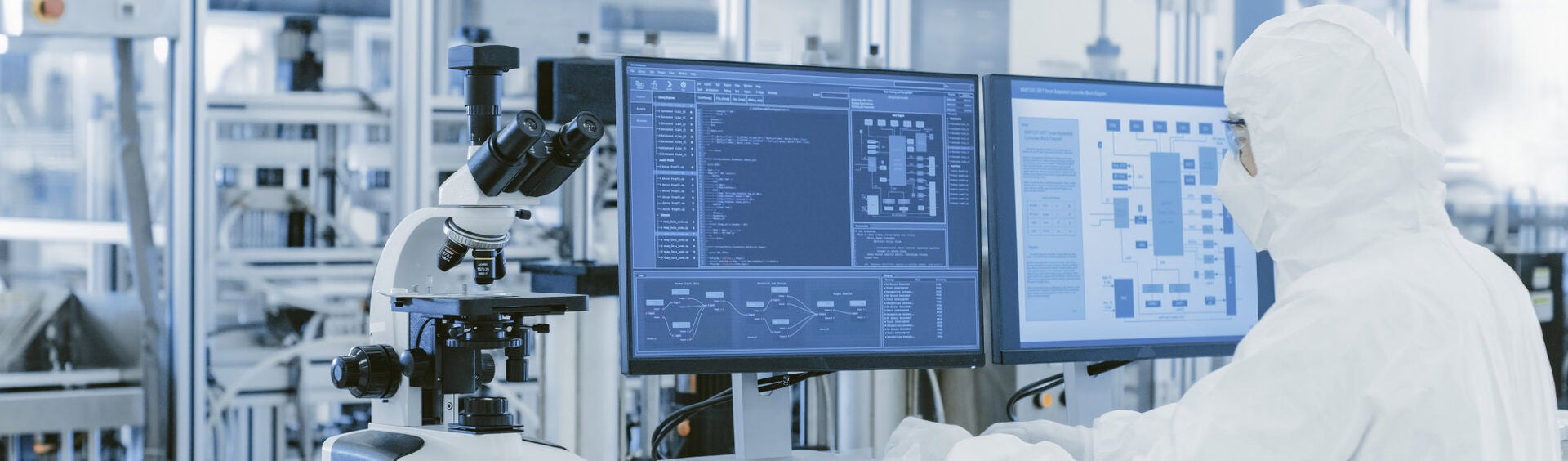
As the leading manufacturer of packaging solutions for the medical products industry, MULTIVAC is working on the development of suitable digital solutions and services, so we can offer companies extra added value. Given the expectation, as well as the significance and scope of this digitalisation megatrend, there seems to be no real consensus within the sector - and this is reflected in the diverse opinions within individual companies.
“It should first be clarified, what the term "digitalisation" means from the customer's perspective,” advises Luc van de Vel, Vice President of the MCP (Medical, Cosmetics and Pharmaceuticals) Business Unit at MULTIVAC. “The first stage is to clarify, whether a consensus exists in the particular company, about which digital topics could have an influence, and in which way, on the company, its processes and its areas of business. The objectives to be achieved through this digital transformation must also be defined.”
In terms of the packaging process itself, digitalisation is already viewed by MULTIVAC customers as a proven tool for increasing product reliability and efficiency, as well as generating process transparency. A higher level of automation within the packaging line, and particularly a fully automated process, can make a major contribution here. The most important objectives to be achieved by digitalisation are seen by MULTIVAC customers as being to maximise output, reduce downtime at product and format changes, gain access to process data in real time, and minimise or ideally exclude completely any faults due to operator intervention.
The systematic capture of data within the individual parts of the process also enables widely ranging analysis to be generated, which can then be made available to users in a simple and visualised form. Luc van de Vel assesses this very concisely as “one of the most relevant tools for being able to react at short notice to discrepancies within the process, and also therefore to be capable of implementing long-term improvements.”
Even those concepts for preventative maintenance for example, which can contribute significantly to improving machine availability, are based on the capture of electronic data. Digitalisation also opens up the opportunity for paperless documentation of the different processes.
Product safety and therefore the safety of patients is the most important driver in the medical and pharmaceutical sectors. Digitalisation is an indispensable tool, which can be used via real-time measurement to gain ever greater levels of reliability through reproducibility of the individual processes. This increases trust in the process sequences. In the event of discrepancies or discernible trends, it is possible to react more quickly and regain a safe level of production. Digitalisation also helps in being able to meet the stringent requirements in terms of seamless product traceability along the entire process chain. Detailed key indicators can, for example, serve as the basis for batch documentation of different batches.
One basis for increasing the overall equipment effectiveness is the measurement and analysis of the individual stages within the packaging line. From this can be derived recommended courses of action, which contribute to increasing the line efficiency. The collected data can also be used for troubleshooting, defining service intervals and as the basis for proactively purchasing wearing parts. In addition to this, the real-time data can be used to check all the process parameters in real time, as well as reduce the reaction time in the event of discrepancies or serious faults in the process.
With its new X-line machine generation, MULTIVAC is offering its customers an important basis for fulfilling all the requirements mentioned above. Thanks to its comprehensive sensor system and seamless digitalisation, the RX 4.0 thermoform packaging machine creates a completely new dimension in terms of maximum packaging reliability and consistent pack quality. The X-line is also pre-prepared for networking with the MULTIVAC Cloud, and this offers even more potential uses in digital services for example.
A fundamental component of the new machine generation is its Multi Sensor Control, which captures, checks and if necessary adjusts all the relevant process parameters. This ensures the machine is run permanently as near as possible to the optimum operating point, since the individual part-processes such as forming, evacuation and sealing are optimised within closed control circuits. The captured process data also forms a valuable basis for the provision of digital services, such as predictive maintenance, condition monitoring, benchmarking analysis of overall equipment effectiveness and even intelligent fault detection, all of which mean real added value for customers.
In addition to this, the RX 4.0 has with its new X-tools an intelligent generation of dies, which increases still further the level of product and process reliability. The dies for forming and sealing are integrated into the machine's sensor control via electronic sensor modules. The process stages are coordinated to the optimum level, and any product- or system-related discrepancies are automatically compensated where possible, and even faulty settings by operators are independently detected and displayed. In addition to this, all the die elements are coded and can be identified automatically by the thermoform packaging machine. Since the die is always installed correctly, this enables the optimum process control to be achieved, which in turn has a very positive effect on performance, particularly in the case of machines with frequent format changes.
EU Directive 2011/62/EU made serialisation obligatory for companies in the pharmaceutical sector within the EU from February 2019. Prescription-only medication must now be clearly marked with a serial number, which guarantees its unique identification and therefore protects it effectively against counterfeiting. The UDI Directive (Unique Device Identification) in the medical products industry also makes it obligatory to mark products and packs uniquely, so that traceability at individual pack level is assured.
Digital printing systems, which are integrated in the packaging line and receive the data for the particular print job from a higher-level ERP system, can be used for marking each individual pack with the corresponding code.
Inspection solutions also make a significant contribution to a high level of pack safety and process reliability. MULTIVAC offers, in this area as well, a large number of solutions for a wide range of inspection tasks.
The spectrum also includes a range of visual inspection systems, which can perform either simple or highly complex inspection tasks depending on the particular version - even at maximum output. Depending on the requirements, it is possible for example to check the presence, completeness or correctness of the particular product in every pack, and the print image can also be inspected for legibility or completeness.
The comprehensive inspection of the product, the pack and its marking ensures all the statutory requirements are met, and that only good packs reach the downstream process. Digitalisation in the form of high-performance sensor systems, comprehensive data capture and processing, as well as intelligent control of all line modules via a uniform operating concept, forms the basis for a reliable and high-quality packaging process.
Luc van de Vel also addresses another aspect, which is essential for MULTIVAC customers. “In addition to the benefits outlined above as regards process analysis, rapid reaction, long-term improvements and higher output, our customers always associate the term "digitalisation" with an increase in their overall efficiency. Here the focus is not only on the higher output capability of the machine, but also in particular on a reduction in the time, effort and cost caused by different types of machine downtime.”
Systematic data capture ensures new or recurring faults are quickly detected, analysed and then solved as rapidly as possible. The data that is captured also forms the basis for providing smart services such as predictive maintenance, for example. Predictive and proactive servicing of machines makes a major contribution to keeping downtime and resulting costs low, as well as ensuring the machines have a long lifespan.
Another benefit of digitalisation is the fact that troubleshooting or service and support can be provided with far less cost and effort, for example by implementing remote assistance solutions. If evaluation of the machine data has already given advance notice to Technical Service about fault messages or the scope of the service work required, the necessary spare parts and tools can be prepared prior to the service deployment, and work can then start immediately on site.
As Luc van de Vel says, “Our customers can save considerable costs in this way, even if our specialists have to travel to the job location. One should not forget, that long periods of downtime create costs. When packing sensitive products, where a continual product flow must be assured throughout the entire production and packaging process, this can even lead under certain circumstances to a complete batch being discarded.”
If fault messages and information on machine faults are visualised for the user on the control terminal of the packaging machine or via a suitable app, these can easily be recognized and the reaction time is quicker, since detailed interpretation is no longer required. It is possible, even for less trained staff, to trace the particular problem. Recommendations on a course of action can also help in eliminating the fault quickly.
When developing packaging concepts or managing a project, the use of virtual reality can provide a sensible source of support. Virtual reality in advance of an investment can, for example, make the decision easier by clarifying whether the packaging machine will be able to meet all expectations, or whether it is capable of fulfilling future requirements in the course of the project. And all this with a high level of transparency and without great effort or high costs. A common scenario in future could be the digital pre-factory acceptance test of the packaging line at the manufacturer. This would provide the proof that all the technical and quality-related requirements in terms of the packaging machine and its complete functionality had been met, before the machine is delivered to the customer.
“Digitalisation has many facets.” says Luc van de Vel in summary. Every company faces the task of intelligently implementing digitalisation as an integral part of its business processes. The degree, to which digitalisation is adopted in a particular company, depends on the individual circumstances and the willingness of the company to invest in digital processes and technology. “Those who invest today in intelligent machine technology such as our new X-line machine generation, which is equipped for the future thanks to its innovative features like X-tools and Multi Sensor Control for real time measurement, are already able to benefit from a packaging process that is as reproducible, efficient and secure as possible.”
The objectives, which a company pursues with digitalisation, have to be established in detail in each company. The following opportunities are available for the packaging process:
The requirements of traceability can be met more easily, if detailed identification and key figures are available. They are the basis for batch documentation for each particular batch. The UDI requirements can be implemented with digital printing.
The large number of sensors in the packaging machine offer the opportunity of running the machine permanently as near as possible to the optimum operating point. Sensor modules on the forming and sealing dies deliver input for controlling the machine. Faults are detected at an early stage and can be eliminated more quickly with the help of remote assistance solutions.
The RX 4.0 thermoform packaging machine is pre-prepared for digital services such as predictive maintenance, condition monitoring, benchmarking, analysis of overall equipment effectiveness and intelligent fault detection.
10.03.2020