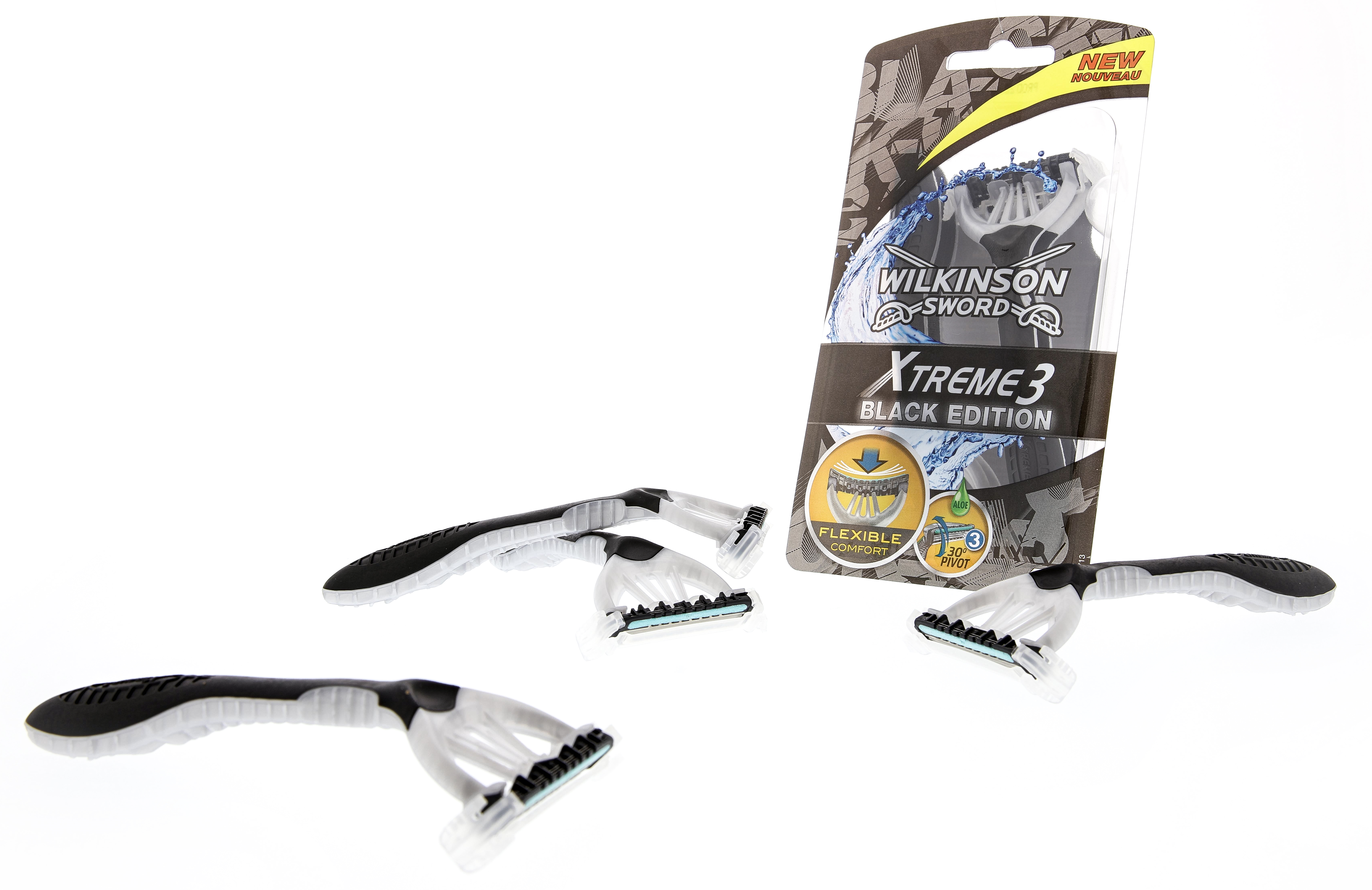
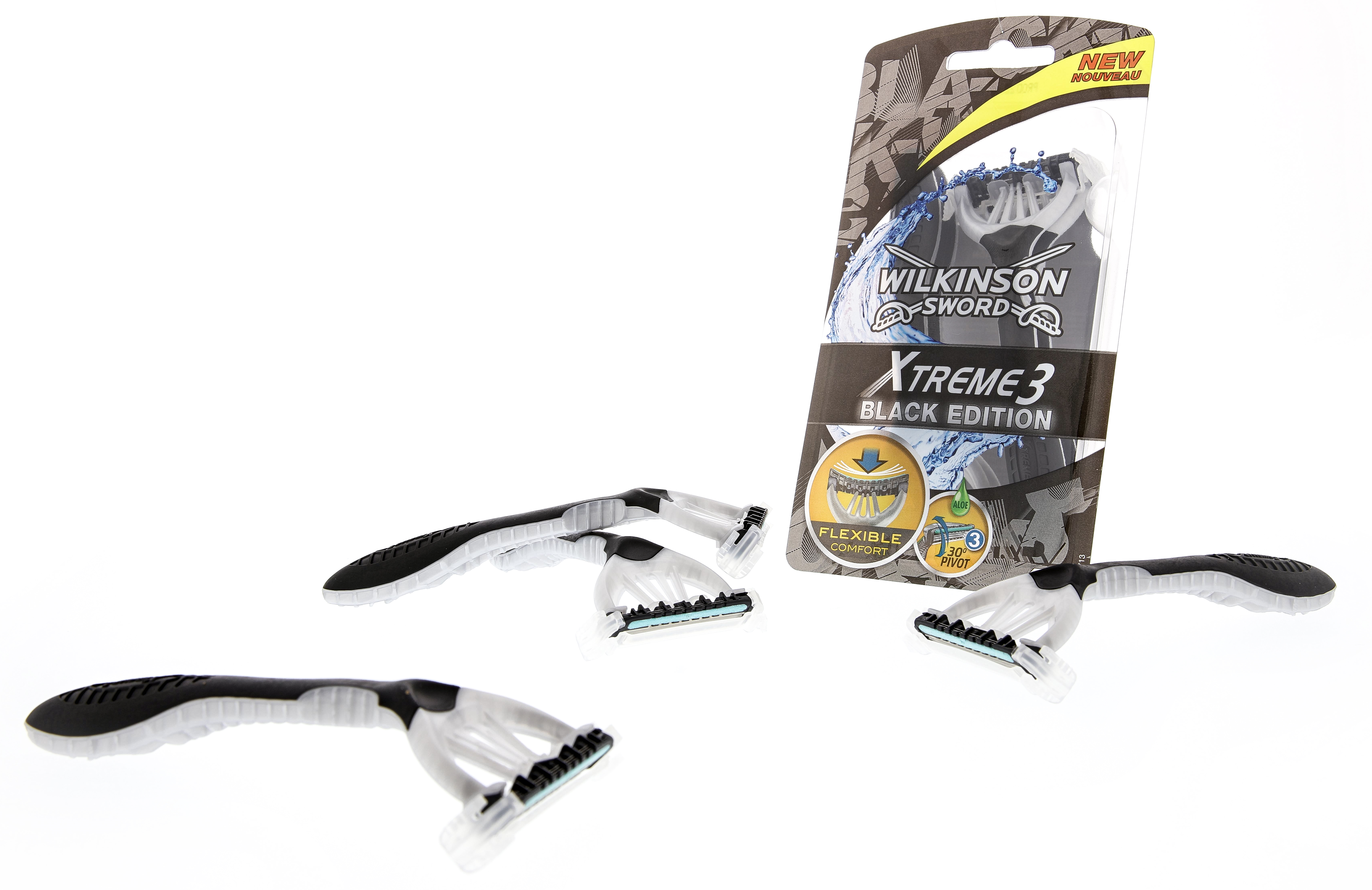
Als die Wilkinson Sword GmbH Teile ihrer Produktion von Solingen nach Teplice in Tschechien verlagerte, musste auch eine über zehn Jahre alte Verpackungsmaschine ersetzt werden. Die Aufgabenstellung für MULTIVAC: Absolute Liefertermintreue, Integration bestehender Linienkomponenten und vor allem die Garantie, dass die neuen Verpackungen für die Xtreme 3 Einweg-Rasierer nicht von den im Markt bekannten Produkten abweichen.
Seit mehr als 50 Jahren ist die Wilkinson Sword GmbH in Solingen ansässig. Das Unternehmen gehört zur amerikanischen Edgewell-Unternehmensgruppe, die 2015 aus einer Aufteilung des in den USA beheimateten Energizer-Konzerns hervorging. In der Bergischen Klingenstadt sind insgesamt 550 Mitarbeiter beschäftigt. Sie stellen rund 600 Millionen Rasierprodukte pro Jahr für den europäischen und internationalen Markt her. Die Produktpalette umfasst das gesamte Programm an Fertigrasierern und Systemklingen – von der traditionellen zweischneidigen Rasierklinge über drei- und vierschneidige Produkte bis zum 6-Klingen-Rasierer. Die Marke Wilkinson blickt auf eine lange Geschichte zurück. Bei den Verbrauchern ist sie bestens bekannt.
Denn schon 1898 wurden die ersten Rasierklingen produziert – nach 100 Jahren Schwert- und Pistolenherstellung. Die erste von vielen Innovationen war damals der „Pall Mall“ Sicherheitsrasierer. Weitere Meilensteine der Erfolgsgeschichte waren laut Carsten Meyer, Project Manager bei Wilkinson, „1962 die ersten Klingen mit dreifach beschichteten Schneiden. Damit starteten wir eine revolutionäre Entwicklung in der Klingentechnologie. 1992 folgte der Protector mit seinem ergonomischen Design. Und 1994 kam der erste Rasierer für Frauen in den Handel.“ Es folgen Quattro-Produkte und die Hydro-Serie und viele Weiterentwicklungen, die zu einem festen Bestandteil der täglichen Schönheitspfl ege wurden.
In Teplice kommt nun seit Januar 2017 zum Verpacken der Xtreme 3 Einweg-Rasierer eine Tiefziehverpackungsmaschine R 535 zum Einsatz. Die Rasierer werden, je nach Stückzahl, in unterschiedlich tiefen Blisterverpackungen aus Hartfolie mit einem hochwertigen Design verpackt. Hierbei handelt es sich um drei Standard-Verpackungen sowie zwei „Promotion Packs“, die zusätzlich zu den Rasierern ein Give-away, zum Beispiel in Form einer kleinen Rasierschaum-Dose, beinhalten. Für die Herstellung der Packungen werden Unterfolien aus APET in unterschiedlichen Dicken sowie zielbedruckte Oberfolien verarbeitet. Zwei Rundtellermaschinen sind an die Verpackungsmaschine angebunden. Diese waren, ebenso wie das Abführband zur Kartoniermaschine, bereits vorhanden und mussten im Rahmen der Implementierung der neuen Tiefziehverpackungsmaschine R 535 mit dieser gekoppelt werden. Das automatische Beladen der Packungskavitäten mit den Rasierern erfolgt durch ein Handhabungsmodul. Dafür werden die Rasierer mit einem Transportsystem für die Übernahme durch das Handhabungsmodul vorbereitet. Hierbei werden die Produkte separiert und seitlich ausgerichtet. Das Handhabungsmodul nimmt je Takt zehn Rasierer auf und belädt damit die Packungskavitäten.
Bevor die Packungsmulden mit den Rasierern beladen werden, spendet ein Kartonspender vorbedruckte farbige Kartoneinleger in die Packungskavität, auf welche die Produkte dann gelegt werden. Die Zuschnitte beinhalten mehrsprachige Produktinformationen sowie den EAN-Code für die Preisauszeichnung am PoS. Ein Barcode-Leser überprüft diese Information während des Verpackungsprozesses, so dass Abweichungen zwischen der Information auf dem Zuschnitt und dem Packungsinhalt direkt festgestellt und die betreffenden NiO-Packungen aus dem Prozess ausgeschleust werden können. Hierbei ist die gute Lesbarkeit des EAN-Codes eine zwingende Voraussetzung. In diesem Prozessschritt wird die Unterfolie mit einem Datumscode versehen, der in Höhe des Eurolochs angebracht wird. Dies erfolgt mit einem Direktdrucksystem. Nach dem Versiegeln der Packungen können die „Promotion Packs“ mit einem Schmucketikett versehen werden, die Standard-Packungen werden nicht etikettiert. Ein H 052 Handhabungsmodul entnimmt die Gutpackungen direkt aus dem Komplettschnittwerkzeug der Verpackungsmaschine und setzt sie auf ein Transportband um, Schlechtpackungen werden direkt vom Band ausgeschleust. Mittels einer Kontrollwaage erfolgt die Überprüfung des Gewichts und damit der Vollständigkeit der Packungen – es fi ndet dabei ein Abgleich zwischen der Information auf dem Kartonzuschnitt und dem tatsächlichen Packungsinhalt statt. Schon bei einer geringen Abweichung vom Sollgewicht werden die Packungen ausgeschleust. Sind sie in Ordnung, werden sie über das Transportband einem Kartoniersystem zugeführt und schließlich in einen SB Karton gepackt. Ein Palettierer macht die Kartons dann versandfertig.
Als besonders hilfreich wurde bei diesem Projekt die Zusammenarbeit mit MULTIVAC bewertet. Carsten Meyer lobt hier insbesondere „die professionelle Projektbetreuung, das sehr gute Team und vor allem das kundenorientierte Problemlösungsverhalten.“ Thomas Wolzenburg, Sales Manager bei MULTIVAC, ergänzt: „Das Wilkinson-Projekt wurde bei uns in Wolfertschwenden durch zwei Projektleiter mit umfassender Praxiserfahrung durchgeführt. Während eine Projektleiterin sich auf die Verpackungsmaschine konzentrierte, verantwortete der andere Projektleiter die Anbindung der Automatisierungskomponenten. So konnten wir sicherstellen, dass die einzelnen Module perfekt auf die R 535 und die Anforderungen in Teplice ausgelegt sind.“ Zusätzlich waren Mitarbeiter unserer internationalen Serviceorganisation bei der Inbetriebnahme involviert, ebenso wie 94 | VERPACKUNGEN AUS ALLER WELT | WILKINSON SWORD GMBH | UPDATE ´17 4das lokale Service-Center vor Ort in Tschechien, das jederzeit ansprechbar war und zusammen mit den deutschen Kollegen für die reibungslose Integration der Verpackungsmaschine in die bestehenden Strukturen sorgte. Die Beurteilung der neuen Verpackungslösung fällt in Teplice durchweg positiv aus, obwohl die Maschine erst seit wenigen Wochen in Betrieb ist. Die in den Projektzielen vorgegebene Ausbringung von 210 Rasierern pro Minute wird erreicht. Thomas Wolzenburg ergänzt: „Die gesamte Taktleistung liegt hier permanent im Grenzbereich. Hinzu kommt, dass immer mehrere Produkte in eine hochkomplexe Packungsform eingelegt werden müssen.
Das ist nur mit einer Tiefziehverpackungsmaschine mit hoher Performance zu realisieren, die absolut zuverlässig funktioniert und Ausstattungsoptionen bietet, die für eine maximale Maschinenverfügbarkeit sorgen.“ Hinzu kommen die besonderen Anforderungen unter anderem an die Zuführung und Positionierung der Produkte, die extrem anspruchsvoll sind, aber für eine hohe Effi zienz des gesamten Verpackungsprozesses sorgen. Carsten Meyer konstatiert zudem deutliche Qualitätsverbesserungen der im Design unveränderten Verpackungen: „Zum einen ließ sich die optische Erscheinung der Siegelfl äche optimieren. Zum anderen haben wir nunmehr einen deutlich stabileren Blister auch in den Ecken der Verpackungen. Dies ist auf die Veränderung des Tiefziehverfahrens bzw. den Einsatz eines aufwändigen Formsystems, einem sogenannten Positiv-Formverfahren mit doppelter „Sandwich“-Vorheizung, zurückzuführen.“ Damit ist sichergestellt, dass die Produkte mit ihrer komplexen Form genau in die entsprechend geformte Verpackung passen. Ebenso wichtig sind zudem die gleichmäßige Ausformung der Tiefziehfolie, eine einheitliche Restfoliendicke sowie die Beibehaltung einer hohen Folientransparenz. Denn die Informationen und die Barcodes auf dem Kartoneinleger müssen gut lesbar sein. Ein weiterer Vorteil der Maschine: Da sich die Heizung für die Formstation im Maschinenstillstand öffnen lässt, kann sich die Folie nicht unkontrolliert aufheizen. Ein Stop-and-Go-Betrieb ist problemlos möglich. Auch die Bediener sind angetan von der soliden R 535, weil sie durch das benutzerfreundliche Bedienterminal mit Touch Screen einfach und prozesssicher bedient werden kann.
Die größte Herausforderung bei diesem Projekt bestand allerdings nicht nur in der Anbindung der Maschine an die bestehenden Linienmodule und der Beibehaltung des komplexen Packungsdesigns mit gleichzeitiger Verbesserung der Packungsqualität, sondern vor allem – und da sind alle Beteiligten einer Meinung – in der Einhaltung des straffen Zeitplans. Carsten Meyer: „Für uns war die Liefertermintreue unabdingbar, um Produktionsausfälle zu vermeiden. Die Supply Chain durfte während der Transferphase auf keinen Fall unterbrochen werden. MULTIVAC konnte uns dies zusichern – und hat das auch eingehalten.“
28.02.2017