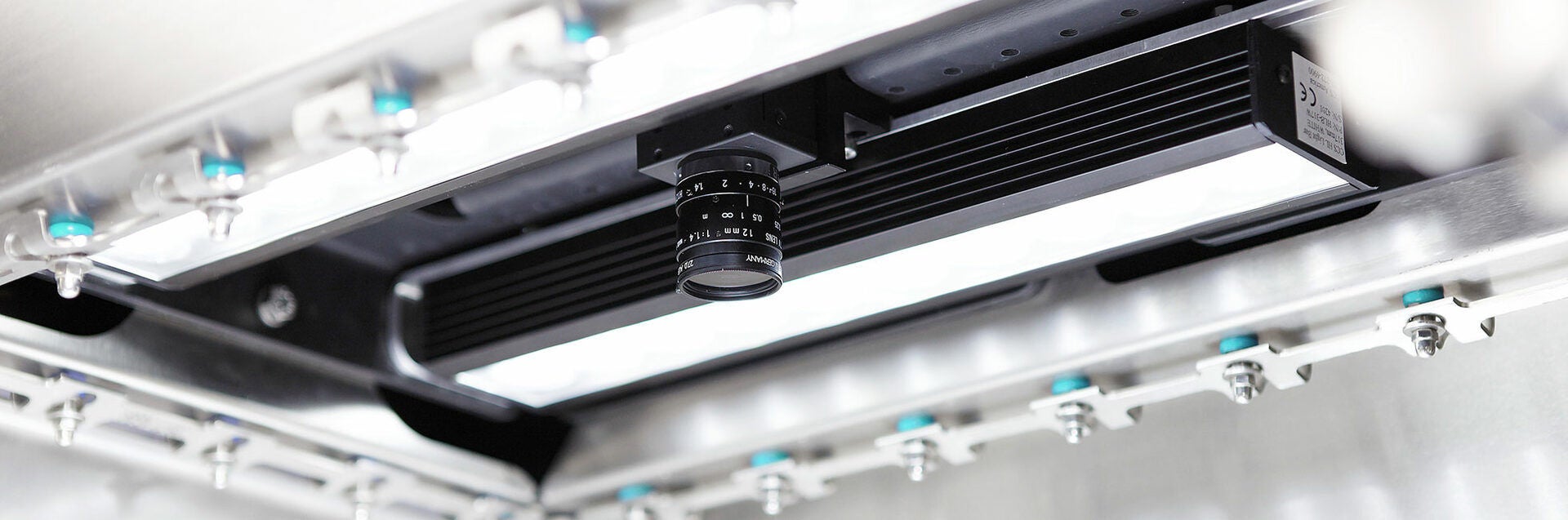
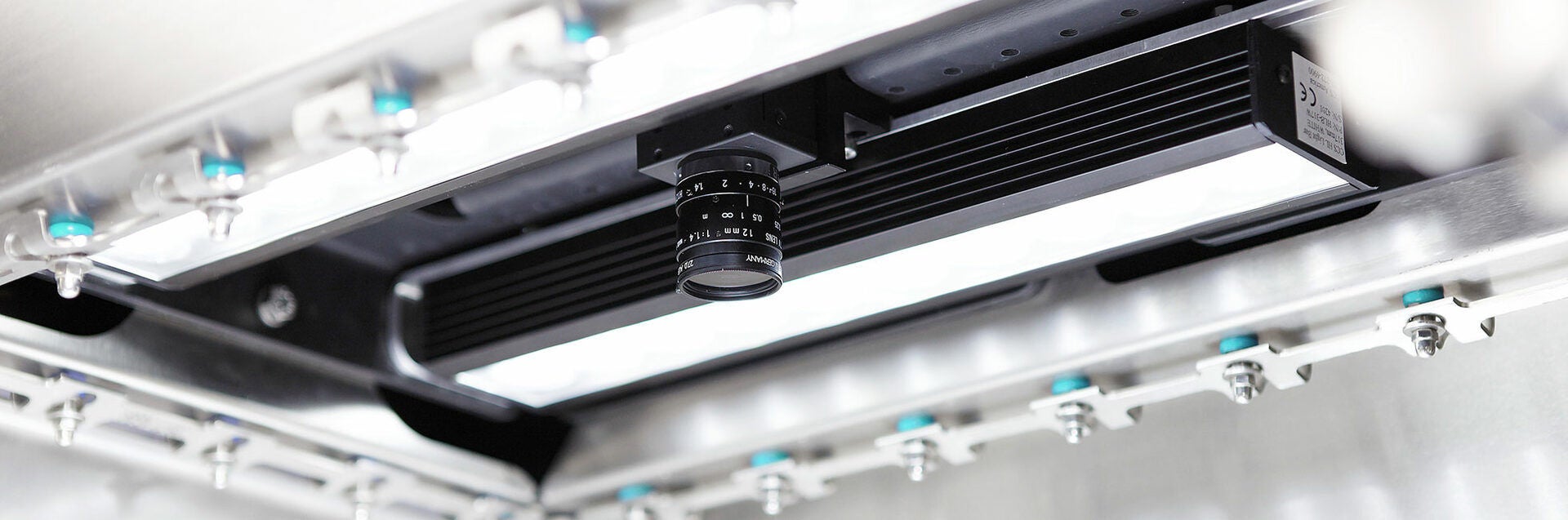
Users generally differentiate between two different requirements. On the one hand, quality control and on the other hand, security control for the process. Quality control comprises among others the following functions: product presence detection, checking the position and completeness of the product, and label presence detection, as well as checking the presence and accuracy of printed variable data and the legibility of codes. Security control, on the other hand, is intended to ensure the correct products in the correct colour are loaded into the pack, preventing cross contamination, for example. Other tasks include code reading and also checking, whether the correct materials are at the machine. This is particularly important in the case of pre-printed packaging materials, since films and folding cartons, for example, are generally marked with a 1D or 2D code, which has to be clearly assigned to the particular product.
Generally the individual types of inspection for product and pack monitoring are performed by means of visual inspection systems. When it comes to establishing label presence, sensors such as luminescence, colour or contrast sensors are used, as well as barcode scanners and code readers. Depending on the version of the model used, the content of the code can also be analysed and compared with the corresponding reference data. More complex or multifunctional inspection tasks can be performed reliably by vision sensors or intelligent, PC-based camera inspection systems such as the MULTIVAC MVS. Their range of application extends from a simple presence check through to barcode inspection, and right up to character and pattern recognition or even comprehensive image analysis. The powerful and versatile MULTIVAC I 420 inspection solution on a thermoforming packaging machine can, for example, inspect markings on a pack for legibility (grading) and code content by means of OCR character recognition (Optical Character Recognition) or OCV character verification (Optical Character Verification). The label position and alignment can also be detected, as well as the shape of the label and defined pattern features.
Areas of application for product inspection include checking the completeness and position of the product. In the case of pack inspection, it can also be established whether the labels meet the defined criteria. The range of applications extends from presence and position inspection through to checking the print image. This, in turn, is divided into pattern recognition or character recognition and checking, and can also include inspection of the content or legibility of codes.
“Generally, the rule of thumb is that inspection should be performed as early as possible in the process,” explains Thomas Große, Project Manager at MULTIVAC Marking & Inspection. Depending on the type of inspection to be performed, inspection systems are placed at various positions in the packaging line or sometimes in the packaging machine itself. If a high level of flexibility is required, such as being moved between two or more lines, a stand-alone unit should be used, which can be integrated into modular belt systems. MULTIVAC can also offer customers additional benefits by completely integrating belt systems into the line control.
Product inspections and completeness checks are mostly installed after the packaging machine’s loading area. Pack inspections can be performed before or after sealing. Important aspects here are the seamless integration of the systems in the line, reliable data exchange between the individual modules and within the entire IT system, and if possible, control of all the systems via one single user interface. In order to guarantee reliable system control, MULTIVAC connects line scanners, which are available as black/white or colour systems, directly to an industrial PC (IPC) via an interface, and these are generally able to handle the most complex of tasks. “In the best scenario all the components can be operated with the same standardised IPC control via the HMI of the packaging machine. The settings or configurations are then called up immediately when the recipe is loaded,” adds the Project Manager.
The statutory requirements, as well as the company’s expectations and wishes determine which types of inspection are sensible or necessary. “The feasibility and practicality first have to be tested,” advises Thomas Große. In addition to being influenced by the required tests themselves, the choice of inspection is also affected by various factors, such as the material and shape of the pack and label, the processing speed and number of cycles, the system environment, the tolerances during product infeed, the ambient conditions such as brightness and lighting, as well as the type of packaging machine being used.
There also needs to be broad agreement as to how the data is transferred within the system and how this is connected to the company’s wider systems. The customer requirements are usually described in a so-called “User Requirement Specification” (URS). Sometimes every inspection task is listed in detail in the so-called “Scope of Work” (SOW). In such cases MULTIVAC requires samples for evaluation, with which the relevant feasibility studies are performed. The customer then receives the results of these in written form as the basis for discussion.
If required, MULTIVAC also supports customers with a so-called “Optical Character Recognition (OCR) specification”, if there is a requirement for reliable print inspection by means of camera inspection systems. The critical minimum requirements as defined are the fonts, the character features, the line spacing, the free area around the text, the contrast, the background, and the text colour. The maximum size of the area to be inspected depends primarily on how large the smallest feature is that needs to be detected. As regards PC-based cameras, areas of up to 400 x 700 mm per camera can be inspected as standard.
Print image inspection of the upper web is usually carried out from above. Product inspection is either performed from above or below, depending on the requirements. In the case of print image inspection, so-called reflected light is used as the lighting. Depending on the requirement, product inspection can be performed either from the camera side (reflected light) or from the opposite side (transmitted light). The encased line scanner is connected to a rotary shaft encoder, which converts the movement of the thermoforming packaging machine into signals and sends these to the camera. This takes the image in the course of each cycle, before the image is then fed to the IPC via a direct data line, where it is checked by the evaluation software. If the detected results from the image deviate from the target value, the packs are marked as reject in the line motion control of the thermoforming packaging machine, and they are then ejected in accordance with the specific requirements.
Thomas Große sees a trend towards ever greater automation. “In the near future, scenarios are conceivable, in which data is exchanged with external PCs, including the automated provision of the evaluation results in databases, and where this is automatically saved by the customer. We must also systematically develop satisfactory solutions for high-resolution systems since the print data to be inspected is becoming ever smaller and more complex.“ Other key features for him include reflecting the HMI menu on external PCs, line control stands and quality management. It is also sensible to consider 3D detection for inspecting the forming of the pack cavity or evaluating quality features of the pack or print, allowing critical process parameters to be identified in advance. This enables targeted servicing to be performed, as well as the timely exchange of consumable materials, aiding in the prevention of costly downtime. “To name just one example, we are currently working on a replacement solution for a simple matrix camera, which we can establish as a standard. The solution used to date is too slow and not capable of audit trails. In addition to this, our agenda also includes the further development of the HMI menu, as well as the transmission and provision of evaluation images and their results.
07.06.2018