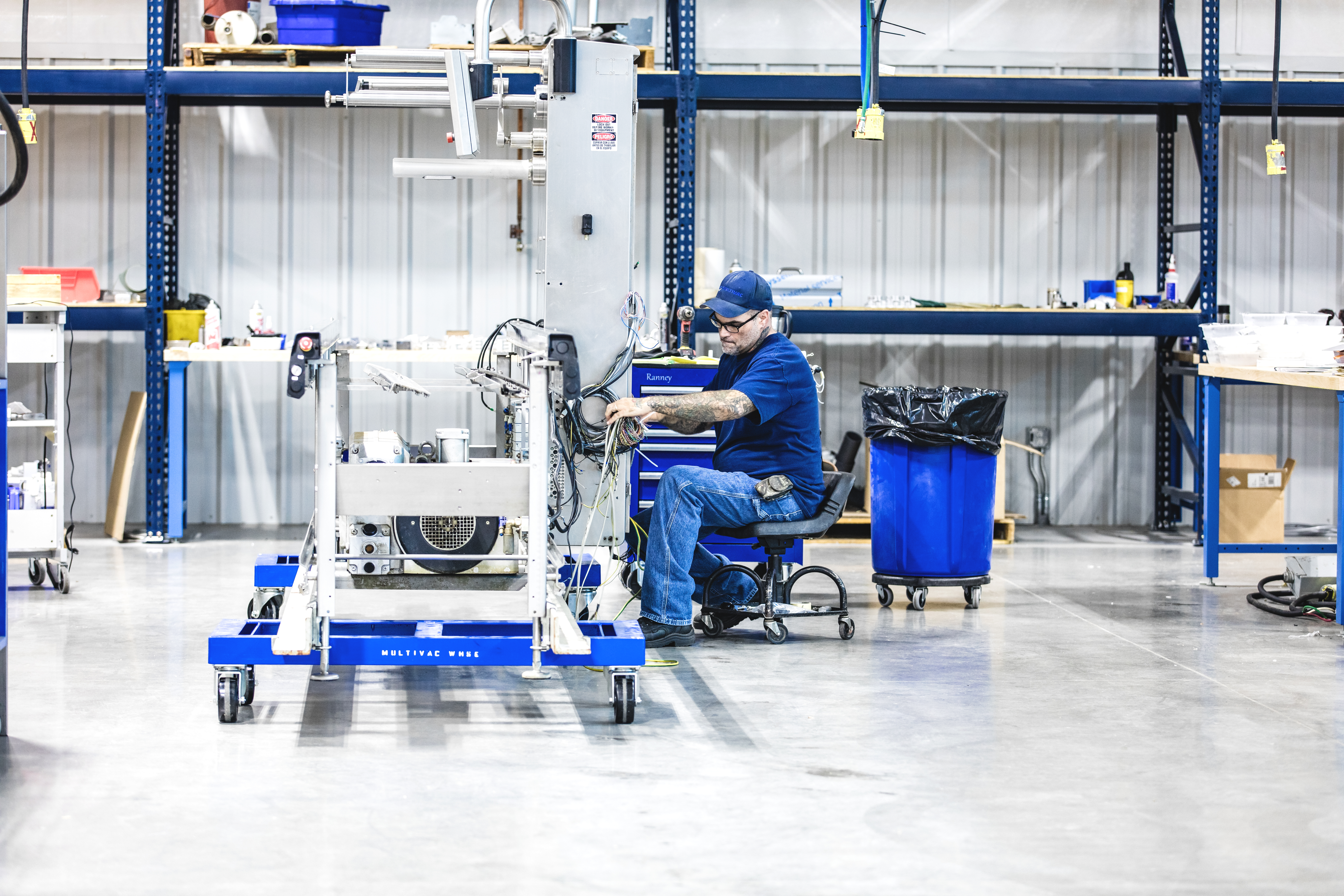
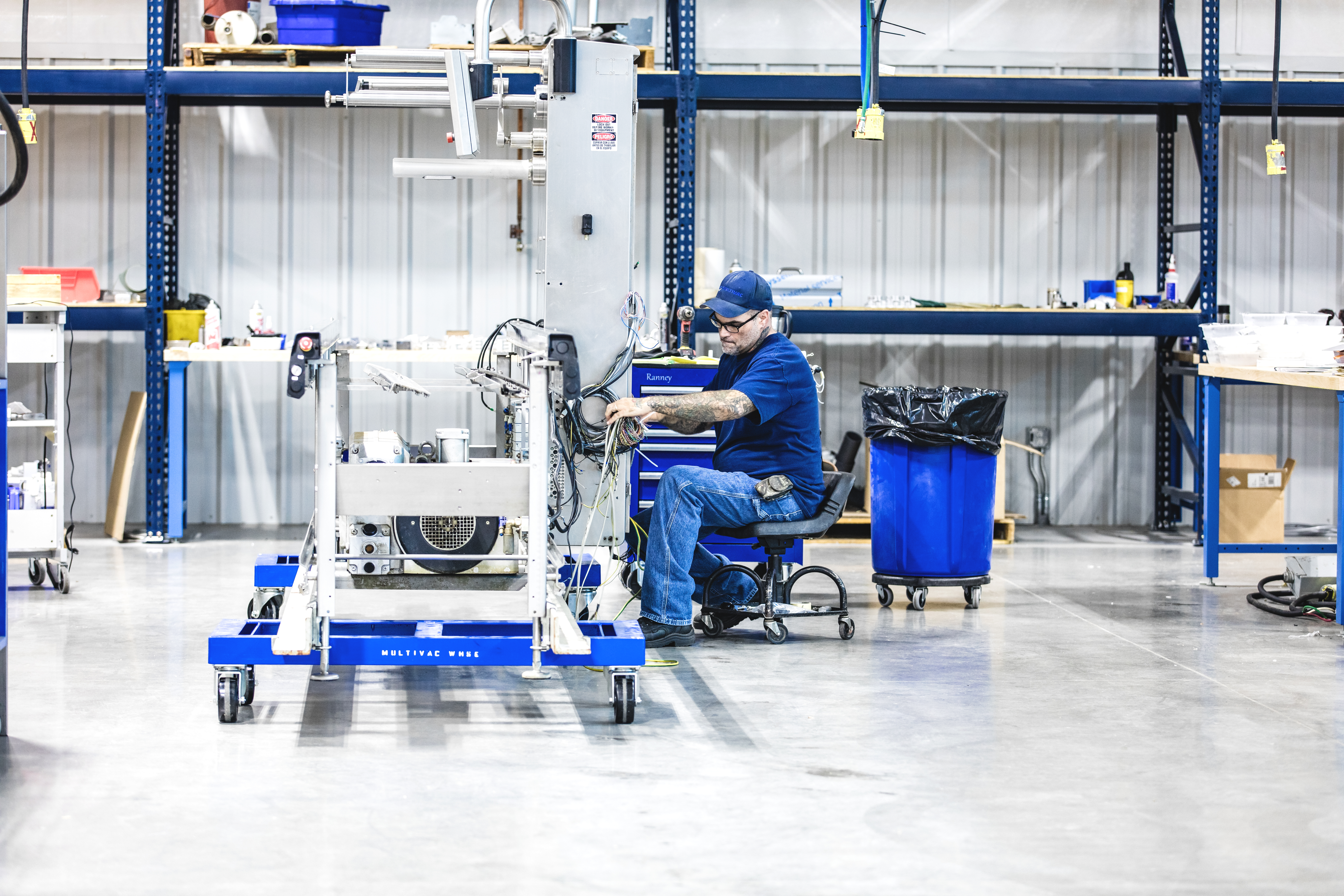
A study by BearingPoint and the University of Munich [1] shows that manufacturing companies in Germany are actually engaged in digitalisation within their production environment, but they are still far removed from complete implementation of the process. Those surveyed see the lack of time and financial means as the biggest hurdle. The barriers to credit are also high at the moment, particularly for medium-sized companies. Here retrofits offer an attractive alternative for bringing existing machines up to state-of-the-art technology in a cost-effective way. Which upgrade options are available for packaging machines?
[1] BearingPoint and the University of Munich, “Industry 4.0: The incomplete revolution“, January 2024.
By using sustainable processes and recyclable packaging materials, as well as generating their own energy, manufacturing companies can make a significant contribution to improving the eco-balance. Retrofits play a crucial role here, since the long life of machines means the sustainable use of resources.
The consumption of resources in the packaging process can be reduced considerably through the use of modern machines, for example by optimising the pack geometry or reducing the film thickness. It is also possible to optimise the pneumatic components, so that the consumption of expensive compressed air is minimised, or even to replace pneumatically driven components with electric ones, which reduce the overall compressed air consumption still further. The installation of monitoring tools helps to identify and replace inefficient systems within the machine, and this further reduces the consumption of resources.
Since market requirements are constantly changing, conversions and modernisation of machines or lines should be as simple as possible. Maintenance contracts provide additional regular maintenance, and this enables machines to be operated at a high technical level for many years and even decades.
Digitalisation exerts a significant influence on the demand for retrofits. The demand for upgrades of control systems has multiplied in recent years, since an increasing number of companies want to network and digitalise their machines – particularly in the case of thermoforming packaging machines. These upgrades increase efficiency, and this leads to higher productivity, as well as reducing energy consumption and operating costs. The lifespan of a machine can be virtually doubled through the use of modern technology, and it is estimated that this will be available for the next 15 years.
Long-lasting and consistently running machines are a basic requirement of efficient food production. Excellent after-sales service also plays a crucial role in the buying decisions made by companies. There is the motto: “The first machine is sold by Sales, each additional machine by Service.“
The retrofit process begins with a fundamental analysis of the existing machines and their requirements. Frequent reasons for modernisation include the changed market requirements of customers, the availability of spare parts, the need for productivity increases, new statutory requirements, or the connectivity to other systems in the line as part of Industry 4.0. At MULTIVAC the number of retrofit orders is three to four times higher than the orders for new machines.
MULTIVAC offers standardised modernisation packages, which include all the necessary components and modifications - from mechanical, electrical and pneumatic parts right up to new software programs and complete machine controls. Working closely with customers, the experts at MULTIVAC also develop individual retrofit packages, which are tailored to their specific needs. In the case of more complex modernisation programs, there is a specialised project team consisting of Sales personnel, designers, control technicians and Service or Helpdesk staff, who ensure that the retrofit process runs smoothly.
As a basic principle, machine manufacturers should always remain in regular contact with their customers, so that they can proactively suggest potential updates in technology. The obsolescence of components provides one of the greatest challenges to the machine construction industry. Machine manufacturers should therefore announce "last orders" in anticipation of discontinuation of specific components by third-party suppliers, so that the availability of parts can be assured for as long as possible.
The aim is to keep the downtime as short as possible, while machines are being modernised. The duration of interruption in production depends on various factors, particularly the type of modernisation and the machine itself. Thorough preparation before the conversion, as well as the optimum scheduling of the various assemblies supplied, make a major contribution to ensuring that downtime is as short as possible. And continual exchange of information between the Sales, Design and Service departments makes sure, that potentially long conversion times are taken into account for future projects.
Every modernisation project must meet the current statutory requirements. Where required, the machines must be adapted to the latest safety standards. A comprehensive testing and documentation process ensures, that all the safety requirements are met.
Older machines can also be upgraded with digital products and services. This offers companies the opportunity to monitor, analyse and maintain their machines more effectively, and this leads to greater efficiency and productivity. Digital services are available via the MULTIVAC Cloud from any location. Transparent processes and process data in real time make an important contribution to the cost-effectiveness of machines and lines.
Examples of digital services are:
The importance of retrofits will continue to increase in future, since the pressure for digitalisation and the demands of sustainable processes will also continue to grow. Thanks to digital retrofits, food manufacturers can develop new strategies and establish more efficient process sequences in their production environment. Current research projects are using artificial intelligence to make predictions about the optimum type of sensor system and the best approach for digital retrofits. This means that modernisation projects will be tailored even more effectively to the objectives and requirements of customers. Digital retrofits have the potential to offer many medium-sized companies an organic entry into Industry 4.0.
18.12.2024