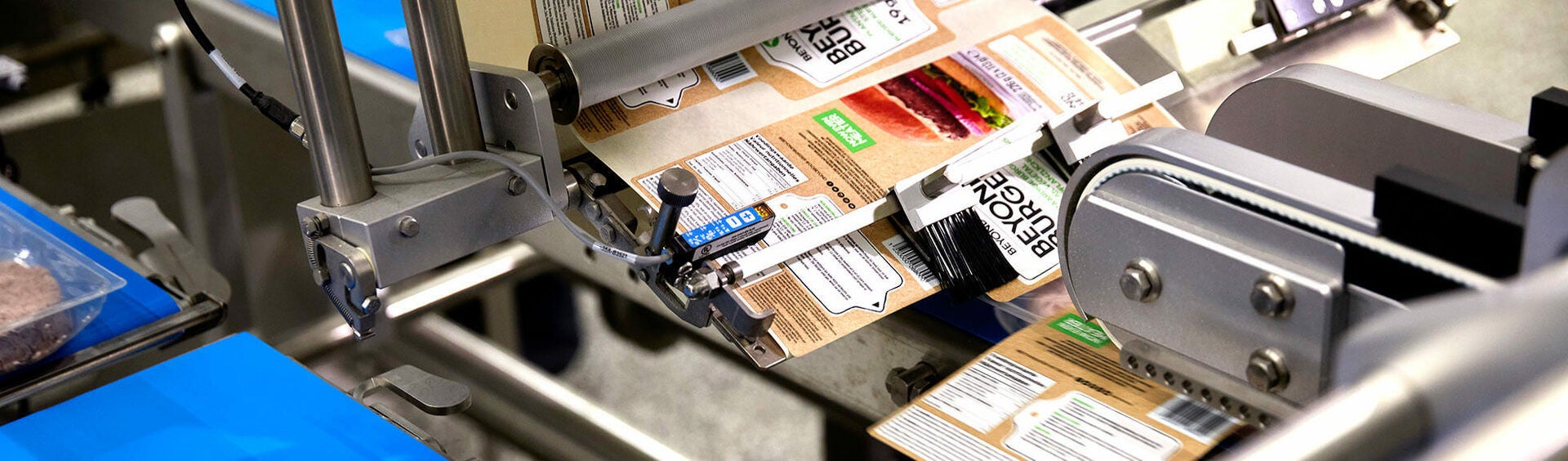
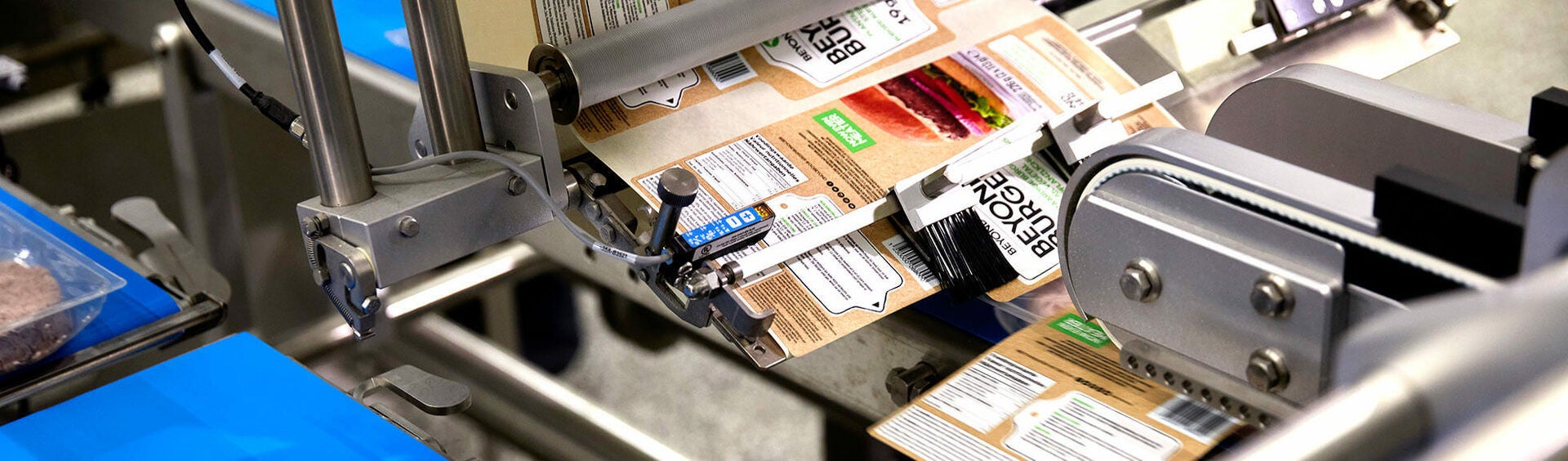
The New Plant is thoroughly satisfied with its choice of thermoforming packaging machine, and as Adriaan Figee emphasizes: “MULTIVAC not only has an impressive number of machine models (more than 150). Our partner is also able to offer complete solutions. The two R 535 thermoforming packaging machines, which are now in operation here, were specially developed for us. This includes automation of the packaging process. The MULTIVAC Team supported us throughout the entire operation. From the initial exploratory discussions through to the project consultation and right up to delivery, as well of course as after-sales and maintenance. We are more than satisfied.”
The two intelligent thermoforming packaging machines are characterised by their high degree of efficiency: “Thanks to the use of automation solutions, the packaging process is far less labour-intensive, and a very good level of hygiene as well as consistent speed are assured. The whole operation is much less prone to faults, since all the individual processes of infeed, transport, packaging, labelling, inspection and box packing are tailored precisely to each other. Thanks to the pack design, the consumption of packaging material has also been reduced by at least 50 percent.” As part of the product launch in Europe, the previous sleeve solution was replaced with full wrap labels, which have a significantly reduced material weight (130 g/m2 instead of 300 g/m2). Despite their low material weight, the new full wrap labels are still highly impressive with their large area for information and their high-quality look and feel, since the print design, shape and type of material can be individually adapted to the product and brand.
But the sustainable thinking behind it goes much further than that. “The more effective use of materials and the type of pack itself also have a positive impact on the logistics chain. Therefore less consumption and emissions. A win-win situation. A lot of money, time and energy was invested in the engineering. Both parties reinforced each other mutually, with the result that the thermoforming packaging machines are built for the future. They were developed in such a way, that later modifications to the machines, due to market changes for example, can be readily made. The machines could go on for many decades.”
Mart de Koning, Sales Director at MULTIVAC Netherlands, on the operation of the two thermoforming packaging lines at his customer: “The frozen products come out of a spiral freezer. There is a buffer system downstream of the freezer, which collects the products and buffers them if necessary, before feeding them to the MULTIVAC line. The products are aligned by means of a MULTIVAC Centrifuge Feeder. There then follow customised systems for the particular products, which assemble the burgers or sausages into groups of eight. A MULTIVAC handling module takes up a group of products and places it automatically in pairs into the pack cavities. The MULTIVAC R 535 thermoforming packaging machine packs the products at a speed of 120 to 160 packs per minute under modified atmosphere. A handling module at the outfeed of the thermoforming packaging machine takes the packs automatically from the machine, and it feeds them to a two-track weighing unit, which includes an integrated metal detector. There then follows a MULTIVAC full wrap labeller, which applies a label completely around the pack. The packs are subsequently packed into boxes.”
Looking to the future, Adriaan Figee sees two challenges both in the short and long term: “We are concerned about the long delivery times for materials and parts. A problem that occurs in many sectors worldwide. Partially caused by the corona virus and shortages in the market. It is also increasingly difficult to find suitable personnel. The demand for personnel is greater than the supply. It is therefore very good, that we have machines in use, which can perform the tasks largely automatically.”
The New Plant on its collaboration with MULTIVAC: “We know and understand each other. If there are technical problems or questions, the MULTIVAC Team is available immediately. I often hear the words: The answer is Yes, what is your question? This is exactly what MULTIVAC is all about. And we really appreciate that.”
Zandbergen World's Finest Meat in Zoeterwoude has been the exclusive sales partner of Beyond Meat since 2018, and it has also been the exclusive production partner in Europe since 2020 with The New Plant. The revolutionary Beyond Burger is the first burger produced on a plant basis, and it looks so good and tastes so much like beef, that it is sold in the meat cabinets of American supermarkets. Beyond Meat is continuing to work on replacing animal proteins with plant-based proteins. By focusing on protein products, Beyond Meat wants to have a positive influence on four growing global trends: human health, the environment, natural resources and animal welfare. The range of innovative products from Beyond Meat is already available in more than 94,000 retail outlets and catering businesses in 75 countries worldwide.
Zandbergen World's Finest Meat is a leading company in the international protein chain, and it has its headquarters in Zoeterwoude in the Netherlands. It sources its chilled and frozen meat from the USA, Argentina, Brazil, Uruguay, Paraguay, Chile, Thailand, Australia and New Zealand. It imports beef, lamb, pork and poultry meat from these countries, which it then supplies to customers throughout the EU as well as in Norway, Switzerland and the United Arab Emirates. In addition to this, the company has also offered alternative protein solutions since 2018.
When it came to labelling, the decision was made in Zoeterwoude to opt for the L 310 Full Wrap conveyor belt labeller from MULTIVAC. The main features of this robust and low-maintenance model are its performance, maximum labelling accuracy and high degree of automation. In addition to being able to apply just a simple top label, the L 310 can apply a label in a C shape over three sides of the pack or in a D shape over all four sides, and it is also possible to overlap the label on the underside of the pack. The labeller has virtually no limits in terms of the products to be packed, the label design and the pack formats. Given the high cycle speeds that had to be achieved at The New Plant, the L 310 was equipped with a zero-downtime function for even more output, efficiency and process reliability. This means that the labels can be changed during running operation, without having to stop the line. This is particularly important when packaging frozen products, since any interruption in the process is critical with these products. Thanks to the two-track version, an output of 140 packs per line can be achieved. In contrast to other sleeving solutions, this is achieved with a very small footprint. And last but not least, the full wrap label can be easily separated from the pack, so that the individual materials can be directed to the appropriate recycling stream.
20.09.2022