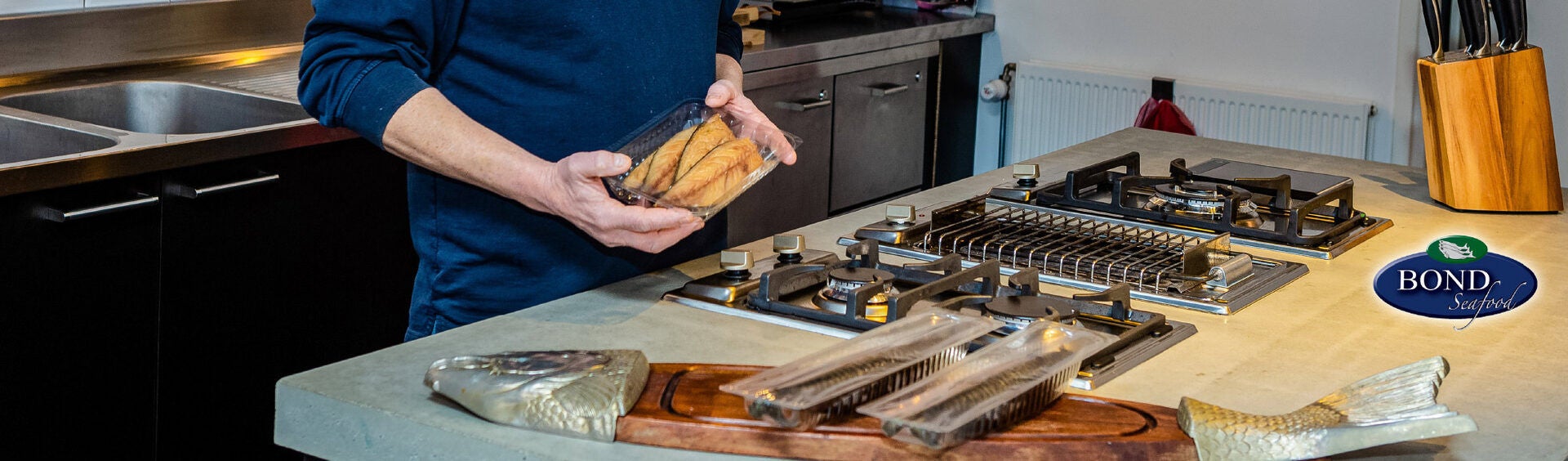
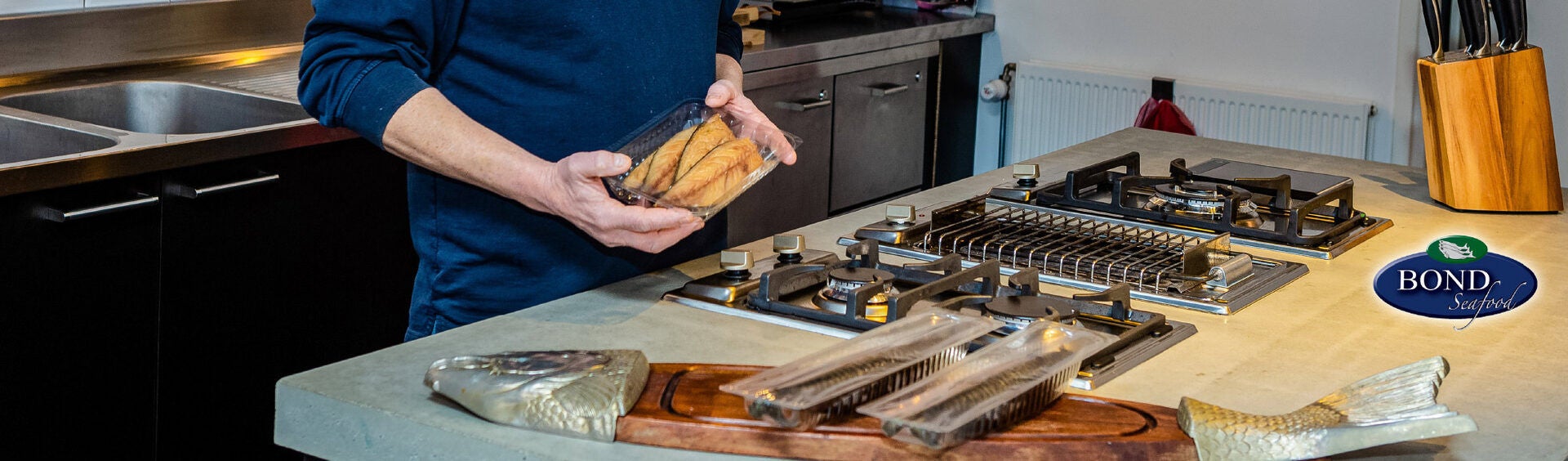
The fact, that this strategic action is directed towards long-term aims and not just short-term trends, is a guarantee of Bond Seafood's continuing success. The company, which was founded in 1741, is currently under the management of the family's seventh generation. Despite the awareness of its distinctive tradition, the company always reacts proactively to changing market demands and focuses systematically on its customers' requirements. In addition to offering herring, smoked salmon, trout, mackerel, sprats and shrimps, the company is constantly adding new products to its range in a wide array of flavours and spice combinations.
But it is not just in its product range, that Bond Seafood relies on its strength of innovation and proven track record. When it comes to packing its products, the company has put its trust in MULTIVAC for more than 20 years. “Just as we can rely on MULTIVAC's outstanding machine quality and technological leadership, we can also rely on their outstanding expertise when it comes to implementing ambitious new projects,” explains Marcel Bond, the company's CEO.
A total of four MULTIVAC packaging machines are in daily use in Bond Seafood's production halls. The majority of the packs are produced on a T 800 traysealer and on one of MULTIVAC's most proven and successful models, the R 245 thermoforming packaging machine. In addition to these, Bond Seafood also has two R 105 thermoforming packaging machines, one equipped for Isopak and one for MultiFresh™, both producing attractive vacuum skin packs of selected products. The Isopak process is suitable for products not exceeding a height of 20 millimetres. The MultiFresh™ process is used for products with a greater height, such as whole smoked herring and trout, and in both processes the upper web is draped over the product without tension, providing the maximum natural product presentation in terms of shape and colour.
The high-output T 800 traysealer is designed to produce MAP packs and MultiFresh™ vacuum skin packs in large batches. It enables trays to be packed with a product protrusion of up to 20 mm with a particularly attractive pack appearance. This model, which can be scaled to particular requirements, has energy-efficient drive systems, can be washed down and allows for quick die changes. Thanks to the IPC06 machine control with touchscreen, its operation is exceptionally user-friendly.
In order for the company to remain in harmony with its convictions and retain its pioneering role in the market, the decision was recently taken to adopt a packaging material concept for its high-quality fresh products, which was designed to better fulfil the current requirements on recyclability. “We see sustainability not as a single project but as a continuing process. We are one of the leading companies in our sector, and we want to be in the vanguard with a good example and set a clear sign for the market,” says Marcel Bond.
The trays made of multi-layer materials, which had been used on the T 800 up to that point, have been replaced since January 2020 with trays made of mono material. These are supplied by MULTIVAC in conjunction with Bliston Packaging, a well-known manufacturer of packaging materials in the Netherlands. Bliston Packaging has a strategic partnership with MULTIVAC, as well as many years of collaboration with Bond Seafood. The trays can be run without any problems on the traysealer at Bond Seafood, and the packs can simply be directed to the correct recycling stream by the consumer after use.
In addition to substituting the tray material, it was also a high priority to reduce the overall film usage. “The MultiFresh™ concept is the perfect choice for this, since the upper web is very thin but still very stable. It offers the required barrier properties and ensures the product shelf life and protection, which are essential for us, are met in full. The highly transparent film is draped like a second skin over the delicate fish products without deforming them,” explains Marcel Bond.
The use of these new materials required only minor modifications to the packaging machine. Both MAP packs and vacuum skin packs are produced on the basis of mono APET film, which consists of 70 percent recycled material and 30 percent new material. The packs are very attractive and allow a good view of the product. They have also been perfected in terms of user-friendliness. For example, an easy-peel corner makes it simple for the end user to open the pack.
In Marcel Bond's view, the project for sustainable production methods is by no means complete yet. The multi-layer films used on the thermoforming packaging machines are currently in the process of being replaced with films made of mono materials. “With MULTIVAC at our side we have a partner with expertise, who can also support us effectively with future requirements,” explains the company CEO, who not only takes a holistic view of the subject of sustainability, but also wants to strike a blow on behalf of plastics as a material: “The substitution of plastic films, as well as reduction in weight, should be right at the forefront for everybody today. One must not forget that plastic packs make a major contribution to product protection, and for many products, they cannot simply be replaced with alternative packaging concepts. I would particularly include fish products, such as those we produce. Whatever sustainable packaging concepts we decide on today and in the future, we consider it our duty to handle the materials and food products responsibly.”
05.04.2020