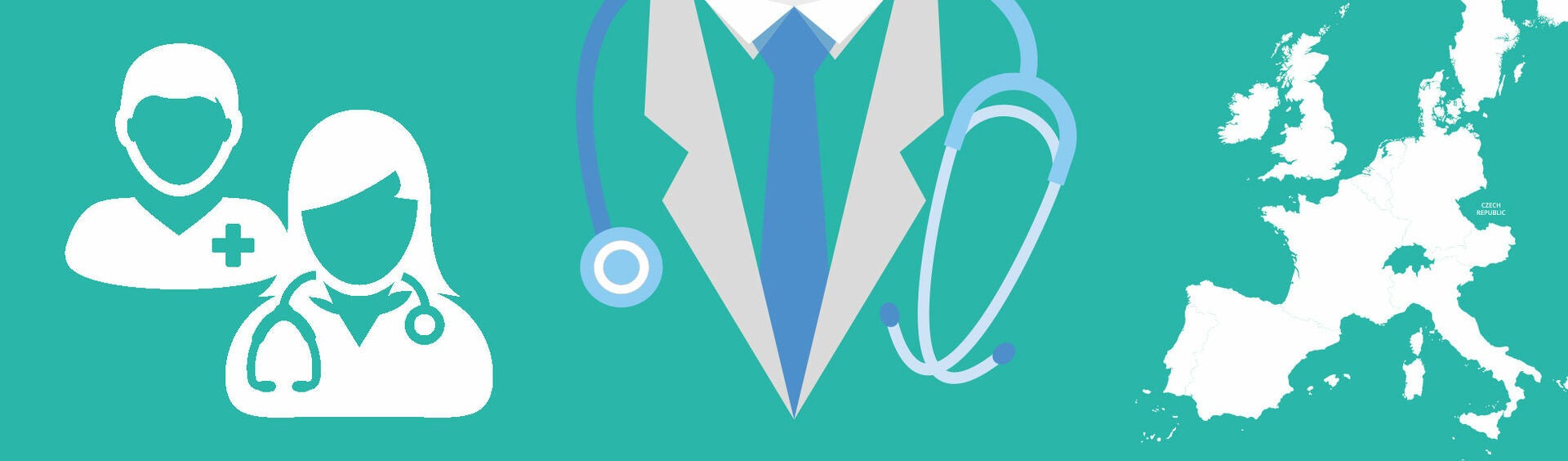
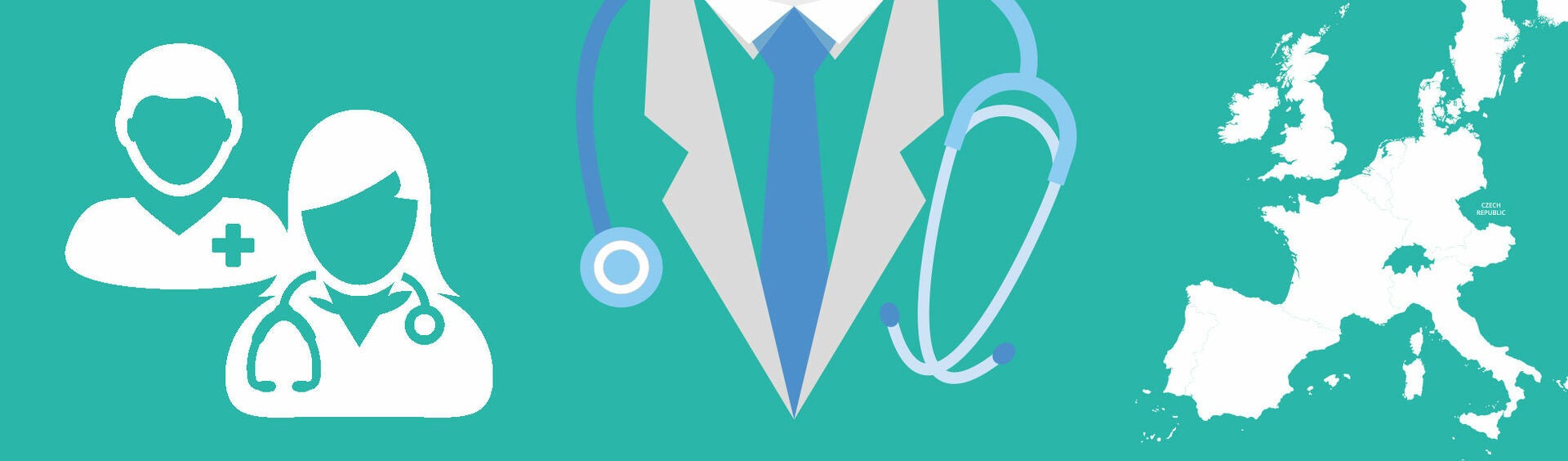
Following the introduction of the new MDR, there will be some changes in the general conditions for packers of medical products. The major change is the widening of the manufacturer's responsibility up to the point of use for bringing these products into circulation. Can you briefly outline for us which measures the manufacturers and packers must now adopt in order to meet this change?
Essentially those points, which were already anchored technically in the applicable standards, but which were not explicitly required in the legislation, are now being incorporated into the MDR. As long as they have already been following the technical standards, there are few changes for manufacturers in their production. However, there are changes in the type of evidence required to prove that a pack can maintain its sterility up to the point of use.
As the usage of the word "use" implies, the handling of the packaged product up to the point of aseptic administration is an important factor for the sterile packaging system. Therefore, the "suitability for use" depends on some of the pack's design features. Usability tests are now also anchored in the technical standards, for which evidence has to be provided.
In addition to this, another factor in the performance of the pack is that its sterility is maintained. This implicitly means the packaging process must provide evidence during validation that packs are being produced with a probability of a sterilisation breach of a maximum 1:106. This also includes the relevant transport and storage conditions after manufacture.
Those in the added value chain manufacturing these sterile packs or packaging systems in full or in part, such as suppliers of pre-sealed packs, therefore have a direct influence on the performance aspects of the pack. The manufacturing processes used for this must be validated in accordance with the latest technological standards, and they must also be under the control of the legal manufacturer within the meaning of the MDR. As regards the necessary documentation, the legal manufacturer is obliged to provide evidence that the performance aspects are met. It must therefore be ensured that the corresponding data in accordance with the MDR is present at the legal manufacturer, and that access can be gained to this data.
In order to provide all the evidence required, it is absolutely essential to have traceability along the entire manufacturing chain. This also demands comprehensive quality regulations, which go right back to the manufacturer of the packaging materials. It must be ensured that the materials do not change in their characteristics, and that they do not pose any risk in terms of biocompatibility due to replacement, for example, of certain components in the recipe, or because the manufacturing process is using untested substances, which could leave a residue in the packs.
This means for example, that Change Management must have access to the different stages of the manufacturing process, allowing it to detect any changes which may have an effect on the medical product, and to minimise the risks accordingly. Certification in accordance with the relevant quality standards is often a precondition for the manufacturers of medical products.
The MDR will probably draw on the same standards, which already apply under the Medical Products Directive. In the case of certification under the MDR however, a new conformity assessment must be performed in accordance with the assessment procedure selected by the manufacturer, and here the technical documentation has to be checked on the basis of the latest state of technology. This evaluation must also include any additional legislative requirements that may be relevant. This means there must be complete availability of data for all the technical documentation, particularly in the case of validation for those manufacturing processes, which always have to be revalidated at defined intervals.
When it comes to validation, there is often important information missing about the history at the manufacturer. Sometimes machines have been added, which were interpreted as being equivalent, or there has been no specific validation at all for these machines. This would lead to a deviation from the standard, meaning conformity could not be confirmed.
Such historical oversights also apply to the evidence data under the old test standards, which may contain a delta in regard to the current test standards. In order to close this delta, it is necessary to have a justification in accordance with the current state of technology. There are also frequently discrepancies in the calculation of aging data, which can then lead to significant delays in approval.
A prominent example of standards which often show discrepancies, is transport validation that is not present for every packaging system, and this means the performance of the product can not be completely proven in regard to its transport.
In the case of manufacturers of special products in batch size 1, validation is actually a very problematic area, which has a high degree of relevance, specially when customised products are being produced. One example of this is 3D-printed medical products. Here, there are unfortunately very few guidelines from the legislators. It can therefore be expected that there will be conflicts in this area, and this means the various statutory bodies could have different interpretations, about how the tests are to be implemented. So-called "bracketing" approaches are frequently pursued in these types of areas, but there are however no specifically binding stipulations, since the basic requirements of the standards are mostly aimed at manufacturers of large batches. Despite this however, the manufacturing parameters that are used must be tested to a depth, which is sufficient to meet the statistical criteria, so products can be supplied that satisfy the requirements.
Manufacturers of packaging solutions have a very deep understanding of the technical limits of their machines, and they are often able to offer specific solutions for particular applications. Manufacturers and packers of medical products do not usually have this background knowledge, and are therefore largely dependent on the support of machine manufacturers.
As a general rule, it is important in my view, that manufacturers of medical products approach their suppliers at an early stage, so the right points are set on the track for each project at the correct time. Manufacturers of medical products on the other hand have the understanding of the regulatory requirements, which may be influenced by the actions of the machine. This therefore requires an intensive exchange of information between the two parties. One typical area, where today there is already a very intensive exchange, is the risk management of the particular medical product, and this has to reflect all the potential manufacturing risks in regard to patient safety. Direct interaction between the manufacturer and supplier is therefore absolutely necessary.
One of the most critical features is a pack opening design, which is intuitively understood by the user. The shape, as well as the printing and colour, play an important role here. In the case of peelable packs, it is also essential to have a defined opening force, preventing the medical product from falling out when the pack is opened.
Today, the requirements in this area are already clearly regulated, and a change in the current standards is not expected. More problematic, however, are the many so-called "grandfathering" products where evidence in the technical documentation is missing, and changes in the standards have not been reproduced over the life cycle of the product, so the documentation is consequently not complete or up-to-date.
It is frequently the case that the pack itself does not form part of the core expertise of the medical product manufacturer. This aspect of the sterile pack is also often taken into consideration much too late, when new medical products are being developed, and this can lead to very high costs for the overall project. The packaging machine manufacturer generally has much greater expertise in this area and is therefore a very valuable partner in the design and implementation of the pack.
Problems, which frequently occur during conformity assessment, include missing evidence and an absence of data traceability, both of which are absolutely essential for confirming product conformity. The depth to which products are tested under statistical criteria during validation is also a point of discussion, often leading to discrepancies when auditing is being performed. In many cases, the change management process is also not brought into line with the regulatory changes in the conditions (NBOG BPG 2014-03 under MDD / new MDCG 2020-03 under MDR). Changes to the process or the machines must be tested and approved by the relevant body, since they can have a direct influence on sterility.
When implementing any measure regarding medical products, a suitable change to management processes should be introduced in advance. This ensures no new process risks can arise and that critical processes, which could affect the sterility of the pack, are tested and approved by the relevant body at an early stage.
25.10.2020