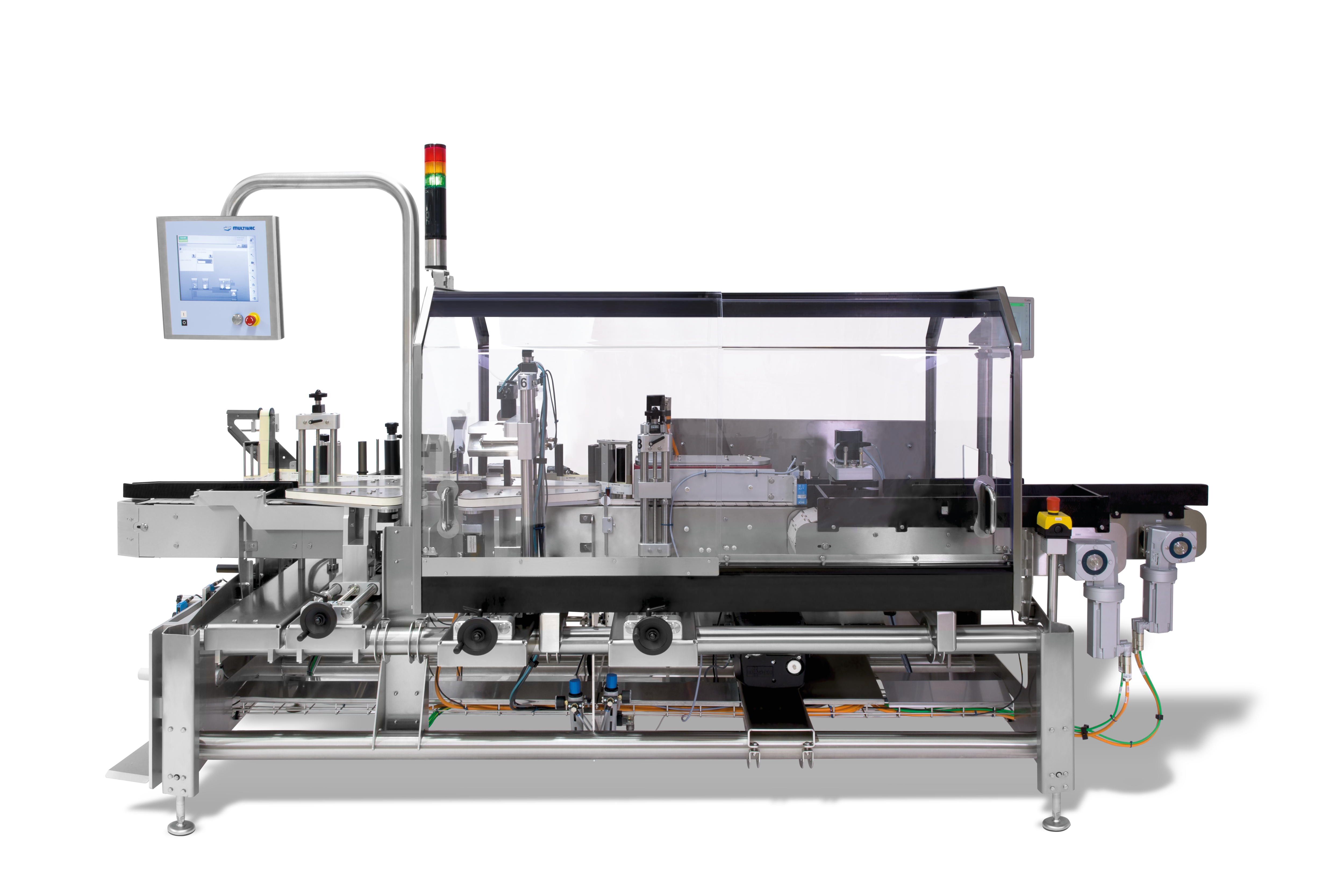
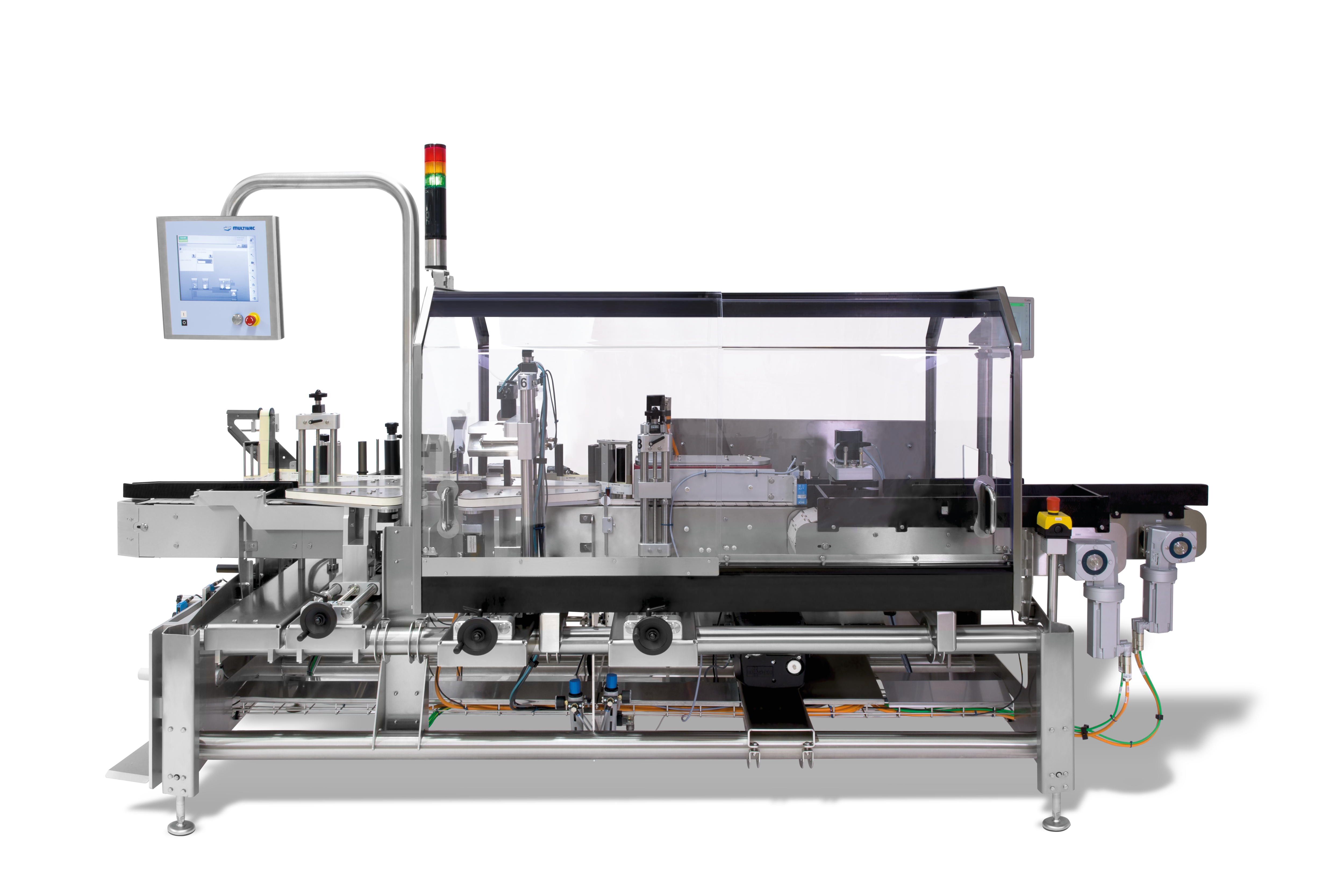
Since the beginning of 2018, the new L 320 at Dr. Wolff has replaced an aged, link conveyor labeller dating from 1991. “The objective was to replace the old machine which had become prone to breakdowns and was time-consuming to convert, with a reliable and flexible model, which also had a code reader and label presence detection,” explains Alexander Popp, Project Manager at Dr. Wolff. In addition to this, the output of the labelling system had to be increased by at least ten products per minute by using two of the latest servo-driven label dispensers – a cycle rate that in the end was actually exceeded.
The products from Dr. Wolff are on sale in over 50 markets worldwide. The product portfolio includes cosmetics, medical products, and pharmaceuticals and features many well-known brands such as Alpecin, Plantur, Linola and Vagisan. The company, which has specialised in the research, development and marketing of highly effective products, and which works closely with the dermatological profession, was founded in 1905 by a chemist, Dr. August Wolff, in Bielefeld in the eastern part of Westphalia. Today the company is managed by the fourth generation of the family. The company feels it is well equipped for the future with “a full pipeline of new innovations and even its first participation in the digital MedTec sector”. In 2018 the company is targeting a turnover of 300 million euros.
The L 320 is mainly used to label the Linola Shower and Wash, Linola Oil Bath and Vagisan products. The round and oval bottles, available in three sizes for each product, are filled on a bottle filling and capping machine. A checkweigher is also used to check the product weights. An infeed conveyor brings the filled bottles from the primary packaging area to the 3000 mm long modular plastic belt of the L 320 in the secondary packaging area. All the transport conveyors are resistant to solutions containing alcohol, ether, or paraffin. The bottles are separated at the infeed of the labelling machine by means of a pneumatically operated spacing unit, allowing them to be fed singly to the labelling station.
After they have been separated, the cylindrical bottles are turned while stationary by means of a wrap-around applicator. This enables the label to be rolled on. MULTIVAC Marking & Inspection and Dr. Wolff decided on a wrap-around applicator in this case, ensuring maximum label accuracy is achieved with the smallest possible footprint. The tolerances of the plastic bottles can also be better compensated with this labelling procedure, and any spiral offset is largely minimised. Label presence detection can also be directly integrated into the wrap-around applicator by means of a colour sensor. Data about any bottle, which is to be ejected due to incorrect labelling, is sent to the ejection device via the line-motion control.
The oval bottles must be very precisely aligned before labelling, allowing exact label placement to be achieved. A motorised press-on unit (in an enclosure) presses the labels securely onto the front and back of the bottles.
At Dr. Wolff a total of just two label dispensers are required for all the tasks. These dispensers are the LD 100 model, which can be adjusted quickly and easily across the transport direction or at an inclined angle. Converting to other bottle formats or sizes therefore only requires a minimum of downtime. The labelling speed is up to 60 metres per minute. The labels are also printed with variable data by means of a hot foil printer.
The MULTIVAC L 320 conveyor belt labeller enables labels to be positioned particularly flexibly. Labels can be positioned on all sides, as well as over the pack edges or as wrap-around labels. The application of sealing labels is also possible.
The labels are applied to the top and/or bottom.
The labels are applied entirely or partially around the circumference.
The labels are applied to the front and/or back
The labels are applied to one or both sides of the top and then over the edge onto the side surface.
Label inspection is a new feature compared to the previous labelling solution. In addition to the colour sensor for label presence detection on the round bottles, there is a camera-based barcode reader for checking the pharma code (code legible / code correct?) as well as contrast sensors, which are fitted on both sides of the transport conveyor, for checking the label presence on the oval bottles. Any incorrectly labelled bottles are immediately removed from the labeller by means of a pneumatic ejection device, which monitors ejection via a light band. The ejected products are collected on a repository table.
A particular challenge for the labelling specialists was detecting the label presence in the case of transparent film labels on white plastic bottles: “We had to search for a long time to find a suitable sensor, which actually enabled reliable label presence detection to be achieved,” says Thomas Große, Project Manager for Medical Technology and Pharmaceutical Sales at MULTIVAC Marking & Inspection.
The L 320 can be operated easily and intuitively via the clear HMI 2.0 user interface with 12“ TFT touchscreen and explicit user guidance. The system enables up to 500 items to be saved, and these can also be backed up on a USB stick. The settings are very easy to reproduce. The modular, highly flexible and low-maintenance labeller also enables conversion to other bottle formats to be performed quickly and without tools. In the case of the oval bottles, only the alignment plate is a format part. “With this labelling solution there are many setting parameters, which do not have to be altered during conversion,” explains Thomas Große. The fact that the label rolls are quick and easy to change also contributes to the reduction in downtime. A further benefit is the fact, that the L 320 meets the GMP requirements as standard, which means that no specific adaptations for this are necessary.
At Dr. Wolff, everyone is highly satisfied with the labelling solution: “We are delighted. We now have stable and secure process sequences – from separation and alignment of the bottles through to labelling and the roll-on movement. The labelling results are also very impressive, since there is no deformation of the label,” says Project Manager Alexander Popp in summary.
10.06.2018