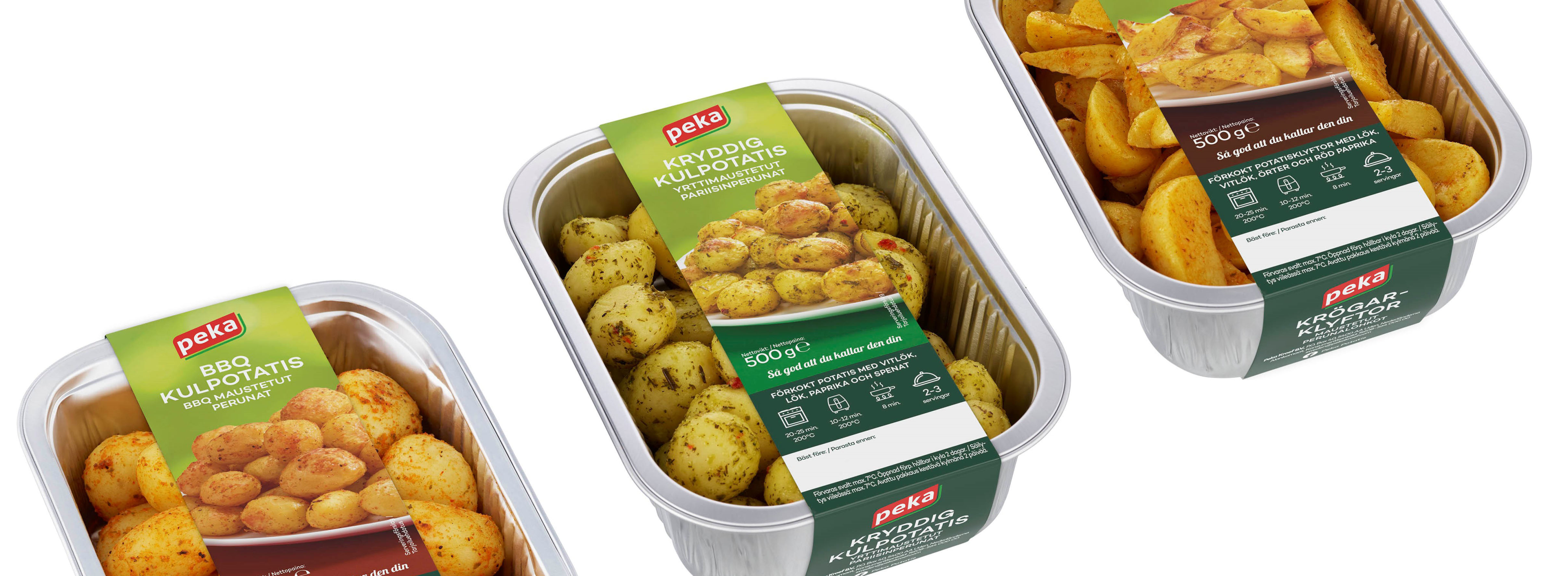
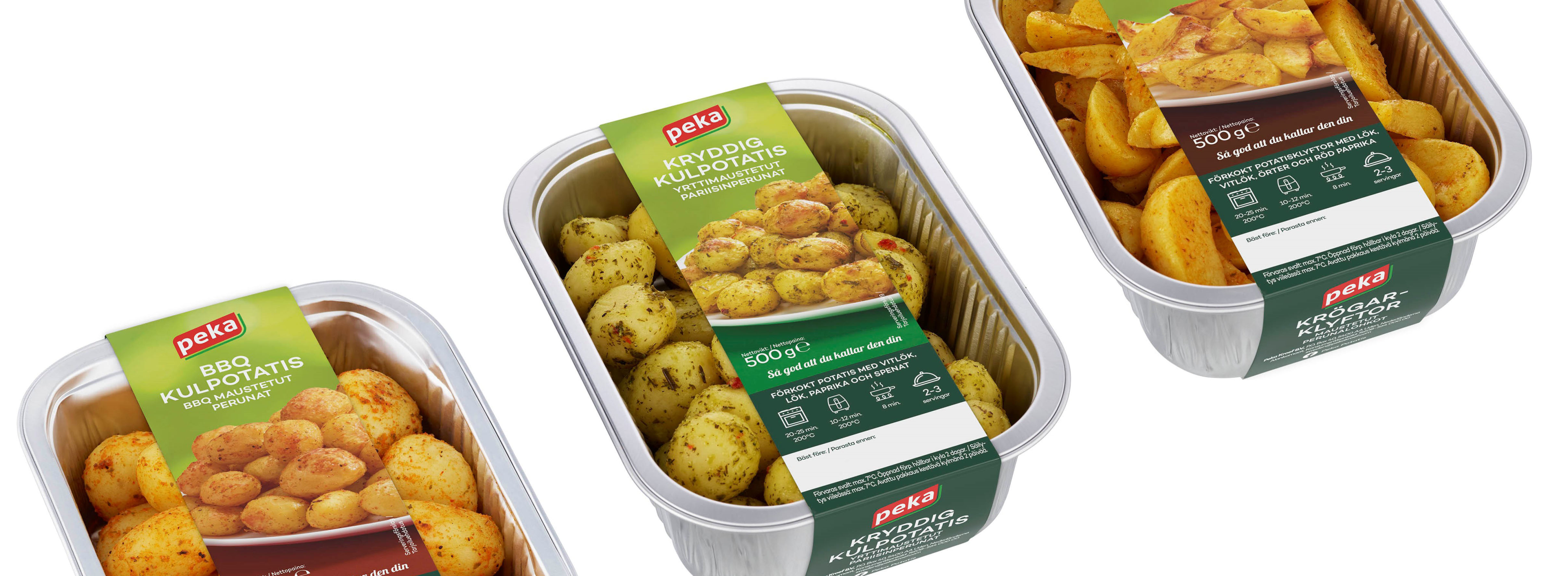
Peka Kroef has long made a name for itself in the potato industry worldwide. The Dutch family-owned company has an annual turnover of around 160 million euros with its potato products. The company counts on a high level of automation for its success. Some of the latest additions: Industry 4.0-compliant packaging machines in the TX 820 series from MULTIVAC.
It all started on a farm in the North Brabant region of the Netherlands in the 1950s. Piet Kroef discovers the business on his own: he buys potatoes from the local farmers, sorts them, and then sells them. This is how he laid the foundation for Peka Kroef, a family-owned company, that has since developed a name for itself in the worldwide potato industry. The heart of the business: The so-called Hansa potato, which is cultivated by more than 100 potato growers in the region. Peka Kroef processes the potatoes into fresh, pasteurized specialty products – in many shapes like wedges, small potatoes, gratins, and purees. The company exports its products to over 15 countries. To supermarkets, restaurants, and catering companies. With growing success. Employing over 300 staff, the family business now has an annual turnover of around 160 million euros.
In order to be able to process and pack millions of potatoes each year, Peka Kroef relies not just on highly qualified staff members, but also on a high degree of automation in production and warehousing. Factory equipment, which in many cases is several storeys high, automatically sorts and grades the potatoes, washes, and steam peels them, before cutting and processing them into the end product - for example into a potato puree or gratin. The entire production process is monitored and controlled by experts in a control room, equipped with a wall of monitors. Primary aim: To increase efficiency in production and logistics. This also applies to a line, which packs marinated potatoes in aluminium trays. Here too Peka Kroef saw room for improvement. “We were looking for more capacity and flexibility so that we can run our production process around the clock,” recalls Arjen de Groot, Engineering Project Manager at Peka Kroef. “We wanted a line, which saves us time. A packaging machine that doesn't miss a cycle, and where the supply of aluminium trays is continuous, as well as offering labelling as an integrated part of the packaging process. The new TX 820 can do exactly that.”
The new TX 820 traysealers from MULTIVAC are installed at the production sites in Odiliapeel and Asten. The machines are used to pack and label marinated potatoes. The only human involvement is putting aluminium trays in stacks of around 150 onto an infeed system. From this moment onwards the machine takes over. The stacks travel into a holding device. There the trays are separated singly onto a further transport conveyor, which is situated one level lower. At the next stage, the marinated potatoes drop into the trays via a dosing system. When the trays are filled, they are sealed to the upper web in the traysealer. The sealing die, the so-called X-tools, ensures that there is an even distribution of sealing forces on the trays. This guarantees a uniform and secure packaging result, even at high cycle outputs and on a multi-shift basis. After the trays have been sealed, labelling then takes place. The L 310 Full Wrap conveyor belt labeller from MULTIVAC is used for this purpose. It dispenses the elongated label, which includes nutritional information, a photo of the product and the company logo, onto the upper side of the film. Two mechanical devices, one mounted on each side of the transport conveyor, then press the ends of the label downwards, so that it encloses the pack on all four sides. The packs of marinated potatoes are now finished. Ready for shipment.
It was not only reliability and output, which persuaded Peka Kroef to work with MULTIVAC on the project. When exchanging the existing machines for the new ones, the commissioning of the lines also had to involve the shortest possible interruption in production. Here it was of enormous benefit, that MULTIVAC had since developed from a pure machine manufacturer into a supplier of complete solutions, since this made "one-stop shopping" a practical reality. MULTIVAC's customers get completely integrated lines, consisting of individual machines with perfectly matched interfaces. The principle of "Everything from one source" guarantees less synchronisation work and accelerates the phases of the project. From conception of the project right up to putting the machine into service and including subsequent maintenance work. Particularly so when companies pull together like MULTIVAC and Peka Kroef. “Our operators and engineers travelled to the MULTIVAC factory in Germany to plan the preparation phase. There we sat down together and discussed our requirements,” says Josjo Uithol, Commercial Manager at Peka Kroef. “The exchange of the lines was prepared very carefully in advance. A detailed test schedule was also produced. We wanted to know exactly, how the exchange of the lines would proceed. We left nothing to chance.” And successfully so. Completion of the exchange plan ran very quickly and smoothly,” emphasizes Arjen de Groot. “The machines were purchased in July 2021 and installed in a very short period. Old machines out, new machines in. In Asten we achieved this in 24 hours. In Odiliapeel in 72 hours. A magnificent performance and great cooperation by MULTIVAC and Peka Kroef.” This was also confirmed by Ton van den Bosch, Key Account Manager at MULTIVAC. “The intensive cooperation between the Engineering Teams of Peka Kroef and MULTIVAC is typical of our approach to turnkey projects.”
Alongside the upgrade of the packaging machines, Peka Kroef has also driven forward the digitalisation of the company. The MULTIVAC lines are equipped with sensors. And these are integrated into the company's higher-level computer system. By using data analysis, Peka Kroef is able to optimise the packaging process in real-time, as well as detect bottlenecks and potential faults at an early stage. “Our operators have told us, that they are also very happy with the simple operation of the lines,” says Arjen de Groot. This is done via a touchscreen control terminal, which uses graphics to assist users. All the machines in a line can be operated and orchestrated from one central point. This also leads to higher productivity. “We look back at the project with satisfaction. Both company cultures fit each other well: hard work, practical and objective working methods. This sits well with a family business like Peka Kroef, which has been in existence for more than half a century.”
06.09.2023