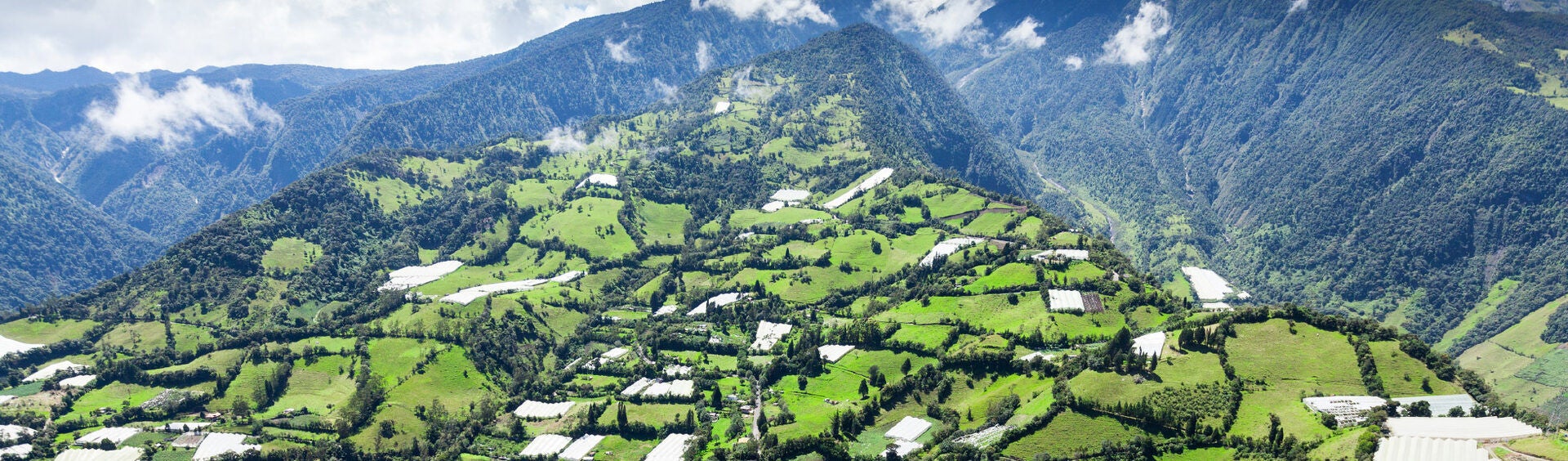
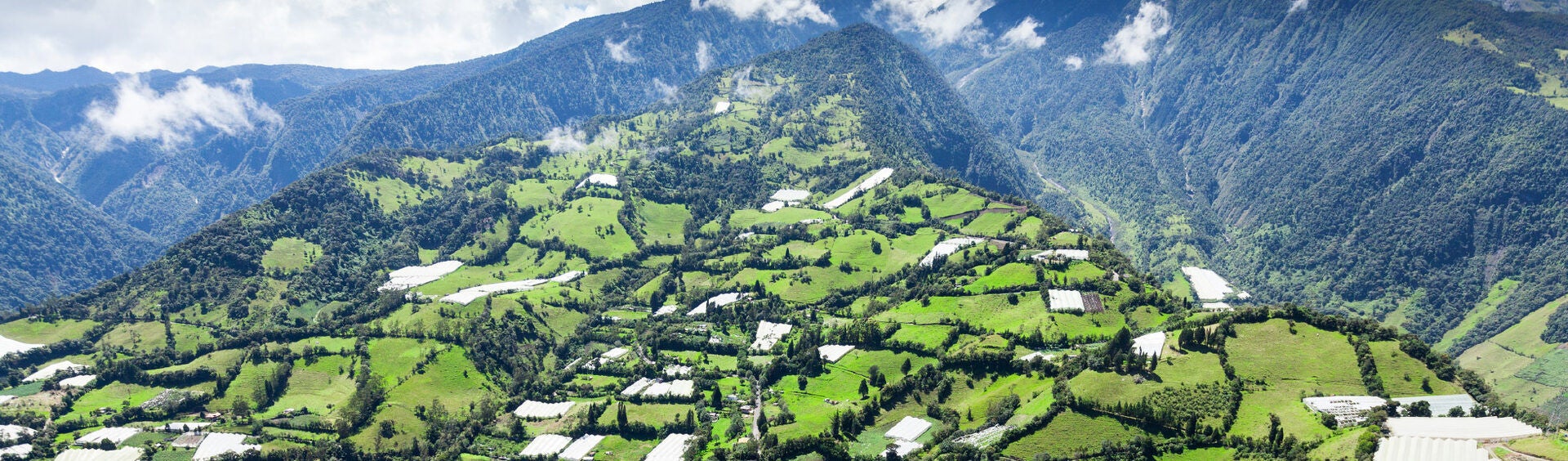
In 1957 at the instigation of his father Lodewijk Jan, Luis Bakker founded an import business for agricultural products on the family farm. The company, initially called India CA Industrial y Agricola, operated from the father's farm and soon developed very successfully as a business. As far back as 1965 the company was importing fledgling chickens for rearing, and it became the first company in Ecuador to introduce industrial-scale hatching methods.
In 1974, the INDAVES brand was established for producing eggs. Soon after this, other brands followed, as well as a major diversification into the production of seeds. In 1979 the name of the company was changed to Procesadora Nacional de Aves C.A., and this established today's name of PRONACA. This enabled the wide range of trademarks to be covered by one overarching company name, which has a high degree of brand recognition. In the 1990s the product range was expanded to include pork products. Since 1999 the acronym stands for Procesadora Nacional de Alimentos C.A. to reflect the company's diverse products, and these now also include cereals such as rice and vegetables like heart of palm and artichoke.
Today PRONACA has more than 20 different brands and serves over 98,000 customers. The products on offer are aimed not only at the end consumer but also at the food service, animal feed and petfood sectors. With approx. 7,700 employees at 17 production sites in Quito, Guayaquil, Santo Domingo and Bucay, the company generates an annual turnover of close to one billion US dollars, and it is therefore one of the most important food manufacturers in South America.
The company has also pursued the objective from the start of using its own business success to promote social development in Ecuador, particularly in the agricultural sector. In 1997 the charitable foundation, Fundacion San Luis, was founded to help children and adults in Bucay and Villa Hermoso gain access to educational qualifications, and this organisation also supports 25,000 needy people in the region with food donations.
Sausages are an important product category at PRONACA. The decision was made in the middle of 2018 to no longer produce small sausages from pork and chicken meat, which were marketed under the names Mr. Pollo and Plumrose, at the two existing production sites, but rather in future to operate just one central site in Pifo for these products. This required a packaging solution with considerably higher output than the two existing production lines. The company also saw significant potential for increases in efficiency, particularly in the area of product loading since this had been done manually up to now. The automation of the loading process also had to contribute to harmonising the product flow and ensuring all the line components operated to the optimum degree.
“When selecting suitable suppliers to meet these requirements, it was particularly important for us to choose a complete line supplier. This company had to be able to support us throughout the whole process, from the planning right through to the successful installation of the complete line, and it also had to have the necessary product range from the infeed stage right up to pack marking,” explains Luis Ojeda, COO for sausage production at PRONACA.
MULTIVAC was therefore the partner of choice, since “this manufacturer sets itself apart from the competition, thanks in particular to its outstanding expertise in automation and packaging lines, as well as having extensive practical experience in very complex projects.” Following a planning and project phase, which lasted around one year, the new line was put into operation at PRONACA in April 2019.
The heart of the new packaging line was procured as part of the larger investment project, is a R 245 thermoforming packaging machine, producing twelve vacuum packs per cycle. Each pack contains four sausages, 25 grams each, packed in a high-barrier film made of PA/EVOH/PE. An easy-peel corner makes it easy for the end user to open the pack.
A MR 296 direct web printer from MULTIVAC applies all the product information directly to the packaging film with excellent print quality. Juan Carlos Agudelo, Operations Center Manager at the Pifo site, is very satisfied with the thermoforming packaging machine, since “the R 245 represents for us a significant improvement in terms of efficiency and sustainability.” Thanks to an intelligent pack design, the company has also succeeded in significantly reducing the material used in the packs by tailoring the pack size exactly to the product.
However, the real technological leap was in the loading of the sausages. “Up to that point, the sausages were loaded manually into the pack cavities,” recalls Juan Carlos Agudelo. The previous solution was not only unsatisfactory in terms of its productivity, it also created a high rate of reject packs due to contaminated seal seams - and this in turn created a significant need for manual reworking of the packs.
The loading of the sausages into the pack cavities is now performed in the new packaging line by a MCF 100 MULTIVAC Centrifuge Feeder in conjunction with a H 244 handling module.
The MCF 100 transports the sausages via an inclined conveyor to the centrifuge plate that is constantly turning. There, they are orientated at the outside edge of the plate by the centrifugal force and are taken up individually from the centrifuge ring. Then a conveyor transports them to a downstream compartment conveyor that carries each product, individually and precisely aligned in a separate compartment, to the H 244 handling module. The handling module is designed for an output of up to 120 pick & place cycles per minute. This enables the loading solution at PRONACA to achieve an output of more than 450 sausages per minute.
The new packaging line overall also meets all the requirements in full. With fewer operators than before, the line achieves significantly higher output and is not only more productive but also more cost-effective than the previous solution. It has also been possible to significantly reduce the number of reject packs, and this has resulted in less packaging and product waste.
Another benefit is the more gentle and significantly improved product handling - a critical factor for PRONACA, since this makes it considerably easier for the food manufacturer to maintain its high standards as regards product quality and process hygiene.
“The loading components have also enabled us to achieve an even product flow along the whole packaging line,” says Juan Carlos Agudelo with satisfaction. “The sausages can now not only be fed to the packaging process considerably faster, but the constant process speed with significantly fewer variables than before also improves the ease of planning enormously.”
The new high performance packaging solution also had an effect on the overall productivity at the site, optimising the downstream logistics processes in order to meet the increased output and adapt to the requirements of the altered pack design - and this in turn has exploited further potential for cost savings. “We are particularly pleased that thanks to the new solution, we now hold the top position in the market as regards innovation and competitiveness,” says Luis Ojeda summarising the success of the project.
However, such an impressive result is not based on the quality of the individual components alone or the outstanding system expertise of the supplier. PRONACA has also been able to benefit from the profound know-how and quality of advice provided by the packaging specialist. Of particular value for Luis Ojeda was the help in increasing the process speed, as well as optimising the use of resources and materials. In order to ensure the optimum output capability of the line would be achieved, extensive test runs were first carried out at MULTIVAC in Germany. After the line was approved and installed in Pifo, specialists from the local MULTIVAC subsidiary and MULTIVAC Germany were on site to perform the last fine adjustments to the line.
PRONACA already has concrete plans for the future: by using dedicated packaging lines for each product, Luis Ojeda would like to increase the level of automation still further over the medium term, so the product flow and production processes can continue to be improved. He also sees great potential as regards the pack design: “Thanks to the new line, we have optimised the pack features, particularly in terms of material usage without the end user perceiving any great change,” says Luis Ojeda. “In the future, however, we also want to introduce new and innovative pack concepts in the market, allowing us to achieve an even higher level of recognition at the point of sale.”
05.04.2020