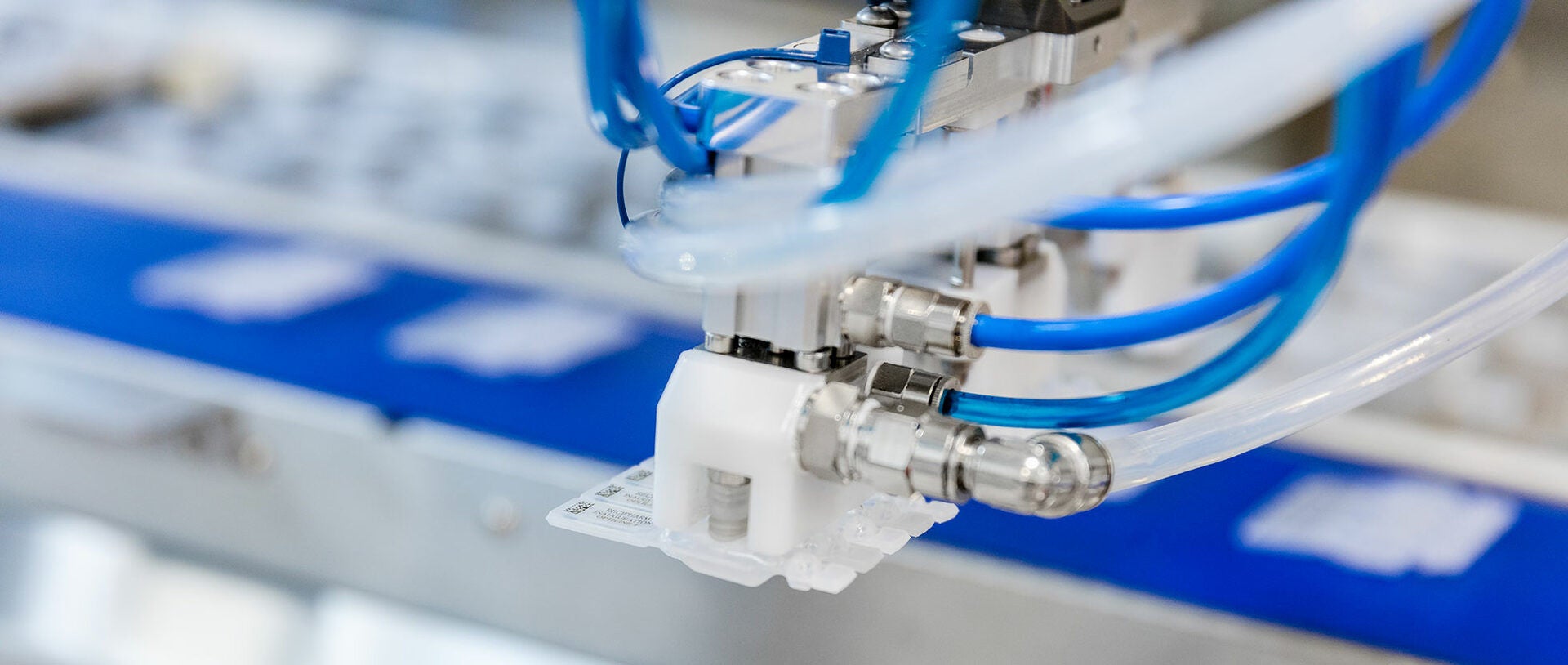
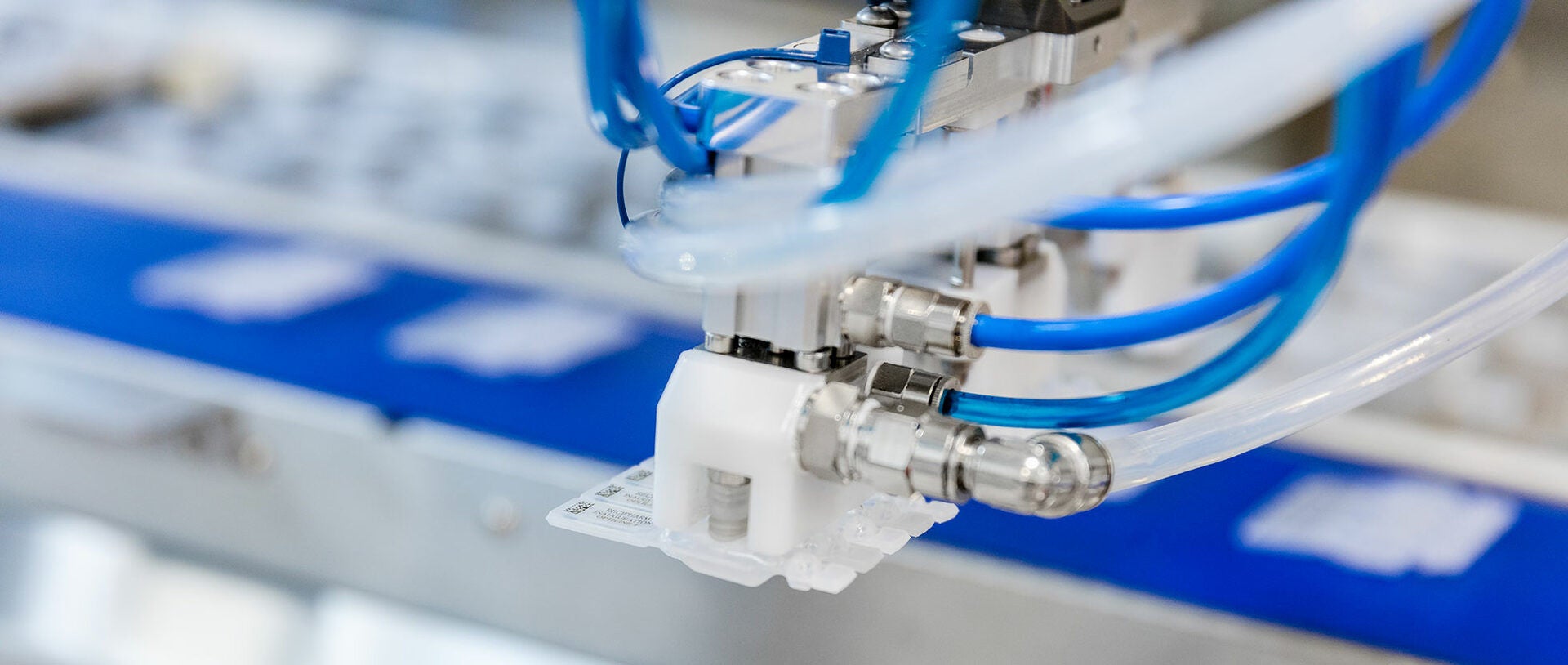
Um in Zukunft flexibel auf Kundenanforderungen reagieren zu können, beauftragte Recipharm das MCP-Projektteam von MULTIVAC mit der Entwicklung einer ausbaufähigen Lösung für das automatisierte Bündeln von Augentropfen-Ampullen sowie das Kartonieren derselben in Faltschachteln unter Zugabe eines Beipackzettels. Das modulare Konzept, das sich in der Zusammenfassung recht einfach darstellt, war für die erfahrenen Verpackungsspezialisten von MULTIVAC aus vielerlei Gründen eine echte Herausforderung.
Recipharm Kaysersberg Pharmaceuticals S.A.S. wurde 1935 in einer Drogerie gegründet, gehörte seit 2008 zur Novartis AG und wurde an den schwedischen Vertragshersteller Recipharm verkauft. Mittlerweile zählt das Unternehmen rund 330 Beschäftigte. 90 Prozent des Umsatzes werden im Export in derzeit 55 Ländern generiert. Hauptgeschäftsfeld ist das Abfüllen und Verpacken pharmazeutischer Produkte mittels Blow-Fill-Seal-Technologie (BFS). Hierfür stehen im französischen Kaysersberg Produktionsflächen von insgesamt 10.330 m² zur Verfügung. 2017 wurden ca. 400 Millionen Arzneimitteldosen in rund 15 Millionen Gebinden verpackt. Durch eine neue Verpackungslinie erhöht sich die verfügbare Kapazität auf 600 Millionen Dosen im Jahr 2018.
Bei Recipharm stellte man sich hierfür eine automatisierte Lösung vor, „die in verschiedenen Ausbaustufen mit unseren kontinuierlich steigenden Anforderungen mitwächst und mit der wir die unterschiedlichsten Kundenaufträge flexibel und effizient bewältigen können“, fasst Yves Buelens, General Manager bei Recipharm, die Projektziele prägnant zusammen.
Die neue Verpackungslösung sollte so konzipiert werden, dass die Ampullen in Abhängigkeit der jeweiligen Kundenanforderung umverpackt werden können – entweder in einer Faltschachtel oder alternativ in einer Tiefziehverpackung aus Aluminiumverbundfolie, die anschließend mit einer Faltschachtel umverpackt wird. Neben der direkten Bedruckung der Ampullen hatte das Konzept als zweite Kennzeichnungsvariante zudem die Möglichkeit zur Inline-Etikettierung zu berücksichtigen – ebenso wie eine weitere Ausbaustufe, die das Abpacken von „Lagerware“ in Plastikboxen ermöglicht.
Die erste Umsetzungsphase wurde im Februar 2018 erfolgreich abgeschlossen. Damit umfasst die Verpackungslösung jetzt neben den Systemen für die Zuführung, Ausrichtung und Vereinzelung der Produkte sowie zur Beladung der Faltschachteln auch unterschiedliche Qualitätsinspektionslösungen. „Am intensivsten beschäftigte uns bei Projektbeginn neben dem limitierten Platzangebot in der Fertigungshalle die Tatsache, dass der Abfüllprozess für Augentropfen ein kontinuierlicher Prozess ist, der nach Möglichkeit nicht unterbrochen werden soll. Deshalb musste bei der Entwicklung einer geeigneten Lösung auch eine Pufferfunktion für die abgefüllten Ampullen eingeplant werden“, bringt Karl-Heinz Weigele, Projektmanager für den Bereich MCP (Medical and Pharmaceutical Division) bei MULTIVAC, die diffizilen Anforderungen auf den Punkt.
Für das Befüllen der Ampullen setzt Recipharm die sogenannte Blow-Fill-Seal-Technologie ein. Die gefüllten Ampullen werden in 4er- oder 5er-Steifen bedruckt und über ein Transportband der anschließenden Umverpackungslinie zugeführt. Ein MULTIVAC-Vision-System, mit dem sich unterschiedlichste Detektions- und Inspektionsanwendungen realisieren lassen, prüft die aufgedruckten Daten, erfasst die Orientierung und meldet die Position über die IPC-Steuerung an ein Handhabungsmodul. Die zwei Robotersysteme greifen nacheinander die Produkte vom Band und platzieren sie exakt und orientiert in einem Trägersystem. Sind die Druckdaten allerdings nicht in Ordnung, werden die Produkte vom Roboter nicht gegriffen. Sie fallen in einen Abfallbehälter. Sobald dieser Fall dreimal hintereinander auftritt, stoppt die Anlage sofort.
Durch das Umsetzen der Ampullen vom Band in ein gegenläufiges Trägersystem sind sie nun für spätere Prozesse wie beispielsweise Etikettieren, Tiefziehverpacken und Kartonieren exakt ausgerichtet. Das Trägersystem hat also die Aufgabe, die Produkte von der unkontrollierten Zuführung zu einer kontrollierten Weiterverarbeitung zu führen. „Auch wenn die Komponenten Tiefziehverpacken und Inline-Etikettieren erst zu einem späteren Zeitpunkt in die Komplettlösung eingebunden werden sollen, haben wir sie jetzt schon in unserem Linienkonzept berücksichtigt. Hierfür wurde die Lösung mit entsprechenden Schnittstellen ausgestattet, die erforderlichen Prozessschritte sind bereits vorbereitet und implementiert“, fügt Karl-Heinz Weigele hinzu.
Der beladene Träger wird dann für den weiteren Prozess über Transportbänder abtransportiert. „Aktuell werden die Plastikampullen-Streifen noch unverpackt in jeweils unterschiedlich vielen Lagen in den Faltschachteln abgelegt. Für die Zukunft ist aber, wie bereits von Herrn Weigele erwähnt, als weiterer Verpackungsschritt das Verpacken in Aluverbundverpackungen über eine Tiefziehverpackungsmaschine geplant“, bestätigt Yves Buelens.
Im Kartonierprozess wird der Faltschachtelzuschnitt aufgerichtet und mit Heißleim verklebt. Bei dem Kartoniermodul handelt es sich um eine Systemkomponente eines Drittherstellers, die von MULTIVAC in die Linie eingebunden wurde. Jede Faltschachtel ist bereits mit einem Code vorbedruckt, der im IPC des Handhabungsmoduls H 242 hinterlegt ist und überprüft wird. Nur bei einem Okay wird die Schachtel weitertransportiert und ein Dispenser spendet den Beipackzettel (Leaflet). Kann der Code nicht gelesen werden oder fehlt er gar, erfolgt die Ausschleusung in einen Abfallbehälter. Im dem Fall, dass der Code zwar lesbar, aber falsch ist, wird der Prozess umgehend gestoppt.
Auch der Beipackzettel ist mit einem ebenfalls im IPC des H 242 hinterlegten Code vorbedruckt. Hier wiederholt sich das Szenario: Stellt sich bei der Überprüfung heraus, dass der Code richtig ist, wird das Leaflet durch einen Spenderarm in die Faltschachtel gelegt. Kann der Code nicht gelesen werden oder fehlt er, erfolgt auch in diesem Fall das Ausschleusen in den Abfallbehälter. Ist er lesbar, aber falsch, wird der Prozess wiederum angehalten.
Das automatisierte Beladen der Produkte in die Faltschachtel übernimmt ein weiteres Handhabungsmodul H 242. Dabei werden jeweils zwei Stripes auf einmal vom Sauggreifer gegriffen und in den Faltschachteln abgelegt. Das System ist so flexibel ausgelegt, dass es viele verschiedene Produktkonfigurationen gewährleisten kann. Nach dem Befüllen wird die Faltschachtel automatisch mit Heißleim verschlossen. Anschließend erfolgt das Verwiegen der Schachteln. Bei fehlgewichtigen Schachteln erfolgt die sofortige Ausschleusung. In einem abschließenden Prozessschritt können die Faltschachteln bei Bedarf mit einer Straffbanderoliermaschine gebündelt werden. Hierfür stehen einerseits einfache Banderolen oder Schrumpfbanderolen zur Verfügung. Über ein Transportband gelangen sie schließlich zu einem Casepacker und einem Palettiersystem. Hier werden die Faltschachteln automatisch in weitere Umkartons verpackt und die verschlossenen Kartons auf Paletten gestapelt.
Bei Recipharm fand insbesondere die hohe Flexibilität der MULTIVAC-Lösung Anklang. Denn das ganze Konzept bietet aufgrund seines modularen Aufbaus vielfältige Erweiterungsmöglichkeiten und ist darüber hinaus einfach zu bedienen und zu warten. „Ein weiterer Vorteil besteht darin, dass Mikrostopps innerhalb des Systems kompensiert werden können und sich durch die berücksichtigten Puffer die Effektivität erhöhen lässt“, erklärt Yves Buelens.
Der Pufferfunktion kommt bei dieser Lösung eine besondere Bedeutung zu. Sie wurde von Anfang an eingeplant und ist auch in der ersten Ausbaustufe wichtig für die vorgelagerte Maschine, die nicht gestoppt werden darf, falls eine nachgelagerte Maschine ausfällt. „Oft führen kleine Stopps in automatisierten Lösungen zu erheblichen Effektivitätsverlusten der gesamten Linie“, weiß Karl-Heinz Weigele.
Bei Recipharm gibt es zwei sogenannte Puffertürme: Der erste Turm ist für beladene Träger gedacht, der zweite für leere Träger. Der erste Pufferturm kommt nach dem Beladen der Plastikampullen in die Träger zum Einsatz. Hier werden die befüllten Träger gepuffert, falls eine nachgelagerte Maschine, etwa ein Etikettierer, eine Tiefziehverpackungsmaschine oder ein Kartonaufrichter, stoppt. Wenn ein beladener Träger in den Puffer gelangt, wird aus dem zweiten Pufferturm ein leerer Träger nachgeführt, da es sich um ein geschlossenes System handelt.
Vor dem Pufferturm für leere Träger ist eine sogenannte Reject-Station zur Überwachung installiert. Sie stellt sicher, dass die Träger, die in den Pufferturm gelangen, auch sicher leer, also ohne Produkte sind. Alle Kavitäten der Träger werden hierzu mit einer Lichtschranke überprüft. Sollte ein Ampullenstreifen im Träger vorhanden sein, wird dieser Träger mittels der Reject-Station aus dem System genommen. Er muss dann manuell geleert und auch händisch dem System wieder zugeführt werden.
Das gesamte System ist steuerungstechnisch und konstruktiv so offen gestaltet, dass sich die geplanten wie auch zusätzliche Funktionalitäten problemlos integrieren lassen. Die Lösung kann also den künftigen Anforderungen jeweils individuell angepasst werden und wächst mit.
So ist beispielsweise als Alternative zum jetzigen Bedrucken der Ampullen das Aufspenden eines Etiketts durch einen Inline-Etikettierer möglich. Hierfür müssen die sehr kleinen Produkte allerdings exakt ausgerichtet und positioniert sein. „Diese hohe Positioniergenauigkeit der Produkte in die Träger war in der Tat eine der größten Herausforderungen bei der Umsetzung mit dem Handhabungsmodul. Das exakte Ablegen der Produkte konnten wir erfolgreich lösen, sodass diese Option bei Bedarf direkt realisiert werden kann“, resümiert Projektleiter Weigele von MULTIVAC.
Darüber hinaus kann der Verpackungsprozess so gestaltet werden, dass die bislang unverpackten Ampullen als mögliche Variante in Aluverbundpackungen mittels einer Tiefziehverpackungsmaschine verpackt werden. Hierfür sieht das Konzept von MULTIVAC vor, dass die befüllten Ampullen über das Transportband von der BFS-Anlage zur Tiefziehverpackungsmaschine transportiert werden und von dem Handhabungsmodul in den Träger gesetzt werden, wo sie liegend etikettiert werden. Anschließend erfolgen automatisch die Entnahme und das Einlegen der etikettierten Ampullen in die Kavitäten der Tiefziehverpackungsmaschine. Dort werden die Stripes tiefziehverpackt, schließlich automatisiert aufgegriffen und in den Träger abgelegt, mit dem sie zur Umverpackungsstation gelangen und automatisiert in die Faltschachtel gepackt werden.
Für die White-Stock-Lösung werden die bedruckten, mittels Transportband zugeführten Produkte vom Handhabungsmodul übernommen und in Plastikboxen abgelegt. Diese Boxen gelangen dann in das Lager oder zur manuellen Verpackung. Für Recipharm war diese Option bei der Konzeptionierung besonders wichtig, denn manchmal erfordert der Markt eine Qualitätskontrolle der Ampullen in Form einer Dichtigkeitsüberprüfung, die erst nach einem gewissen Zeitpunkt nach der Abfüllung der Augentropfen erfolgen kann. Dafür müssen die Ampullen in Kunststoffboxen in ein Lager unter definierten Temperatur- und Luftfeuchtigkeitsbedingungen ausgelagert werden. Nach erfolgreicher Prüfung werden die getesteten Ampullen dem Verpackungsprozess wieder zugeführt.
Eine Variante der „Lagerware“ ist das anschließende manuelle Verpacken von kleinen Chargen. In beiden Fällen werden die bedruckten Ampullen nach der Befüllung per Handhabungsmodul in Plastikboxen gelegt. Der Inhalt der Box wird entsprechend gehandhabt – entweder weiterverpackt in kleinen Chargen oder für spätere Qualitätstests gelagert.
Ein weiterer Aspekt, der bei der Entwicklung der MULTIVAC-Lösung unbedingt berücksichtigt werden musste, ist die sichere Line Clearance, denn die unterschiedlichen Produktionslose müssen bei einem Lohnverpacker wie Recipharm unbedingt auseinandergehalten werden. „Daher war auch die Integration der Inspektionslösungen in die Linie für uns so ungeheuer wichtig“, bekräftigt Yves Buelens. Zur Kontrolle der Line Clearance wird ein farbig gekennzeichneter Träger eingesetzt. Ist dieser Träger einmal durch das komplette System gelaufen und sind alle Puffer geleert, kann die nächste Charge begonnen werden.
Die prozesssichere Anbindung und Steuerung aller Komponenten, auch von Komponenten von Drittanbietern, stellte für MULTIVAC kein Problem dar – „auch wenn die Schnittstellen zu den Scannern, welche die 2D-Codes auf dem Leaflet und den Faltschachteln überprüfen, schon deutlich umfangreicher sind, da sie mehrere Betriebszustände wie Lesbarkeit, Korrektheit, nicht lesbar, nicht vorhanden usw. erfassen müssen“, fasst Karl-Heinz Weigele die Anforderungen hinsichtlich der Schnittstellen zu den Drittkomponenten zusammen.
Insgesamt betrachtet entspricht die Lösung voll den Erwartungen von Recipharm. „Aus heutiger Sicht scheint das Konzept von MULTIVAC natürlich etwas überdimensioniert, aber wir denken bereits an morgen. Denn für die künftigen Anforderungen wollen wir gerüstet sein – mit einer zukunftsfähigen Lösung, die wir sukzessive um weitere Funktionalitäten erweitern können“, resümiert Yves Buelens.
07.06.2018