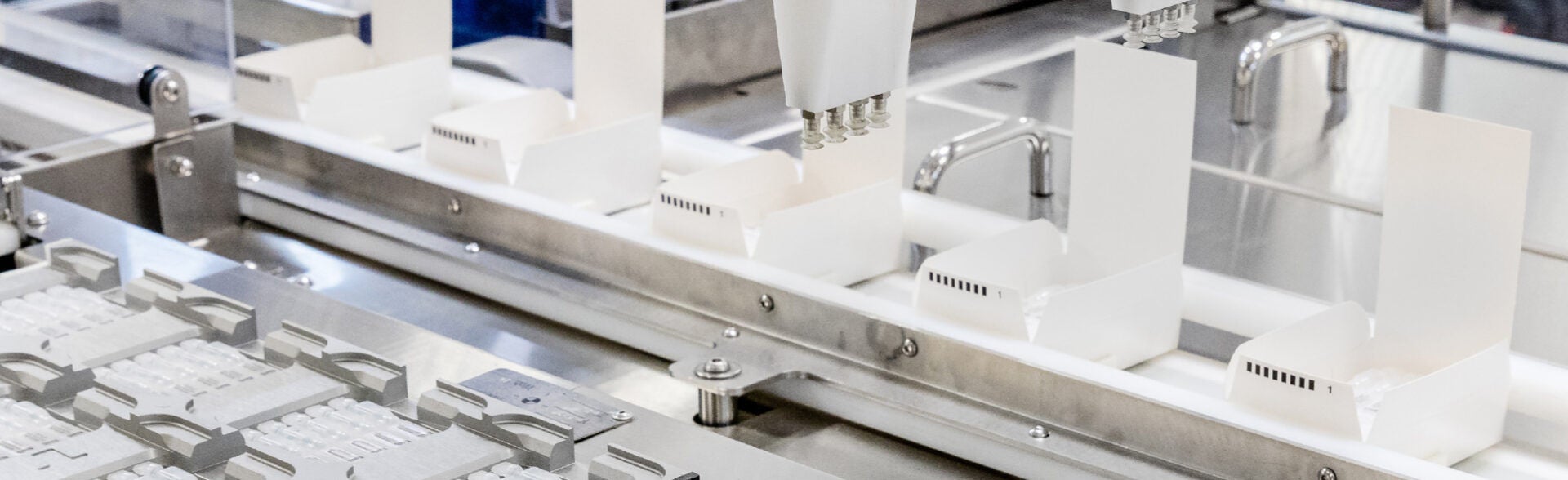
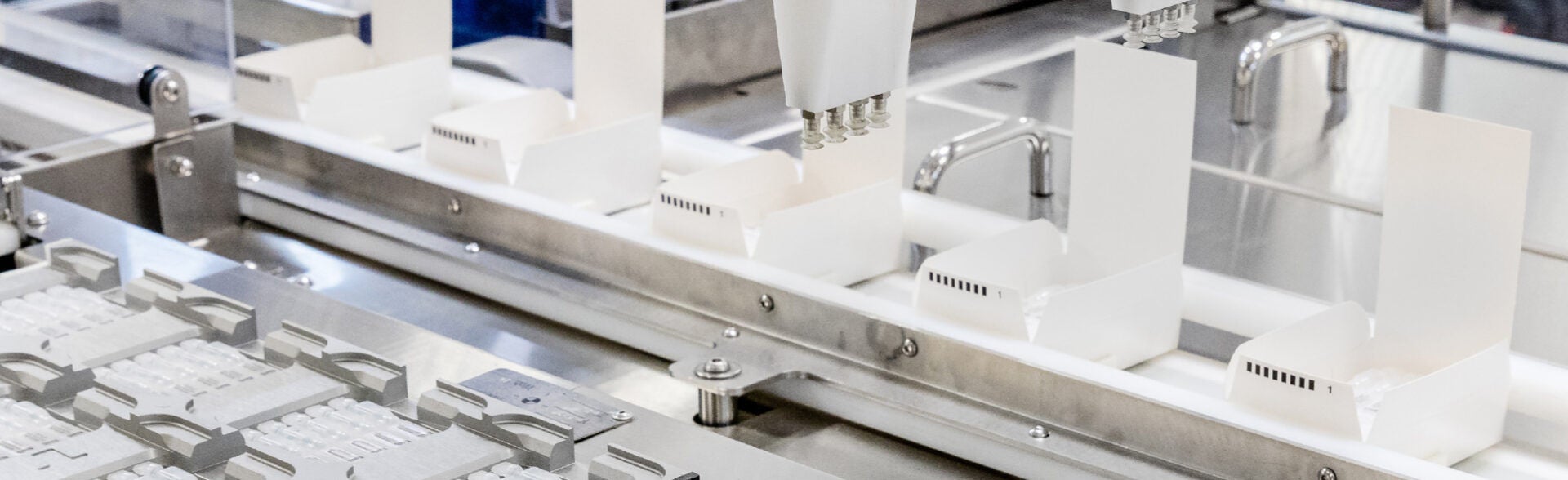
Automation saves costs. Generally, fewer people are needed when processes are automated, than is the case if manual processes are performed. Even more important is the fact that automation increases process reliability, reduces the number of errors and significantly improves hygiene since automation makes a major contribution to reducing the risk of contamination
Automation equipment also has a positive effect on ergonomics as well as health & safety, one example being the use of handling modules for automatically picking and placing heavy products. Another benefit, particularly in regard to product quality and security, can be seen in the use of systems, which transport unstable or potentially moving products through the entire packaging process in a secure and gently way.
There is considerable potential for optimising the process when sensitive medical and pharmaceutical products are being loaded, orientated and transported. Flexible gripper systems can, for example, be used in order to grasp each individual product without damaging it - an important factor in terms of quality, product safety and process reliability. Automation systems also ensure the product is placed precisely and securely in the pack cavity, and that it is orientated perfectly for downstream processes.
When it comes to transporting products very gently, there are in addition to various types of belt systems the so-called carrier concepts. Carrier denotes a type of object carrier, which for example transports the product during the assembly stage and then brings the finished product to the packaging process. Such a concept may also be considered for transporting sensitive products which can not be packed, transported or stored in bulk - or similarly for products made of glass which have to be transported and packed without any undesirable glass-to-glass contact.
The range of products, for which carrier systems are suitable as a transport solution, is very large - it extends from pre-filled syringes or other receptacles with an active ingredient, which form part of a combi pack, to assembled components such as injectors, tubing sets, catheters and suture material, as well as vials or plastic containers such as eyedrop ampoules. And carrier systems can also be used for transporting empty pre-formed trays, or those filled with product to the sealing process, and even transporting the finished sealed trays to a downstream secondary packaging station.
The systems can be used with thermoform packaging machines, as well as traysealers - and where traysealers are used, even small batch sizes down to batch size 1 can be packed. The pack cavities are loaded with high efficiency at one defined position, and several products can be loaded at the same time in one cycle.
Thanks to their modular nature, carrier systems are very flexible in their layout. They fit perfectly into production environments and can be designed in different directions and with a straight or rounded flow.
Carriers create a link between different process stages and enable products or packs to be transported in a controlled way along the entire process chain. Carrier concepts also have other beneficial aspects, for example in terms of process speed, since products and packs can be loaded at the same time into one object carrier. Clearly defined interfaces between stages, including upstream processes, also ensure a high level of process reliability is achieved.
If an additional buffer function is integrated, any stops in the overall process, for example, due to a breakdown in an upstream or downstream process, can be easily bridged and the processes decoupled, allowing a continuous product flow to be maintained. This is of considerable importance since such stops in automated solutions often cause a significant loss of overall effectiveness throughout the line.
A common application for carrier systems would, for example, be a production environment without a direct link between the upstream process and the loading of product into the pack cavities. In this application, the products can be fed in a controlled way during or after the assembly stage to the packaging machine by means of object carriers. Loading the products into folding cartons is also conceivable. The layout of the carrier system can be designed flexibly and adapted to the space available. This solution is possible in conjunction with either a traysealer or a thermoform packaging machine.
By using a carrier system, several components can be transported at the same time in the object carrier without the risk of sensitive products, such as glass syringes being damaged through contact during transport to a downstream station. The products are assembled at an upstream stage and in the same object carrier, in which they are transported to the downstream packaging machine. They are therefore already arranged in such a way, i.e. separated and orientated, that they can be picked up directly by a gripper and placed in the appropriate pack cavity. The carrier also assumes a buffer function during transport and can therefore compensate for micro-stops and faults. By using intelligent buffer functions, it is possible to prevent a complete stoppage in different parts of the process.
It is also sensible to use a carrier concept in conjunction with a fully automatic traysealer, such as a MULTIVAC T 700. The pre-formed trays with several pack cavities are dispensed into the tray carriers either manually or automatically by means of a MULTIVAC Tray Denester, and they are then transported to the packaging machine on belt systems. The trays can be made from a wide range of materials - a typical example is an APET blister, which is sealed to an upper web of paper or Tyvek®. The tray cavities are designed in such a way that the individual products are firmly fixed in the tray and can not slide around or be mechanically damaged.
The different products to be packed, which are fed to the machine on systems individually designed for the particular product, are then automatically loaded into these pre-formed trays on the traysealer's infeed conveyor. Pre-filled syringes, for example, are transported on their own object carriers. Small components such as caps, sleeves or needles are generally supplied as bulk products to a vibrating unit, where they are separated and aligned. Products, which arrive from an upstream process stage such as a marking or labelling solution, are fed in via a roller conveyor or belt system.
The object carriers with their trays are usually loaded by means of pick & place solutions. Depending on the product and required cycle rate, MULTIVAC's modular handling modules are equipped with one or more robots. Using suitable grippers, they pick up the particular products and place them precisely and reliably in the corresponding tray cavity.
The filled trays, which are often unable to stand on the own due to their complex forming, are then transported with their carriers to the sealing station, after which the packs are removed. It is there that a handling module removes the sealed packs from the carriers. Depending on the requirements, the trays are either removed singly or as multiples.
The benefit of this individually configured carousel, which uses several carrier systems to first transport the empty trays for loading and then the filled trays to the end of the packaging line, is its very high level of flexibility. It can be used for either individual production in very small batch sizes (even from batch size 1), or alternatively for producing much larger numbers of a particular product. In the case of small batch numbers, the loading is usually manual, while it can also be automated for a larger number of products. If small batches are being produced, the circulating carrier system can be equipped with just one tray carrier, while for higher cycle rates it can be equipped with several tray carriers.
Depending on the scale of investment and the individual requirements of the particular company, the carrier concept can be implemented in stages and the level of automation increased gradually. Its modular nature enables automation to be expanded successively in various stages, until a fully integrated packaging concept is achieved, in which all the components are perfectly tailored to each other and can be controlled via a uniform operating concept.
Carrier concepts can also be used for packing products, which arrive in an uncontrolled way from a process stage upstream of the packaging machine. Here, the carrier system enables the products to be transported to the packaging machine in a controlled way by means of object carriers. One example is eyedrop ampoules made of plastic, which are usually fed in an uncontrolled way from the process stage upstream of the packaging machine.
Here it is also sensible to integrate a buffer function, allowing micro-stops and longer stoppages can be bridged. In the event of a fault, the carrier system can accommodate the object carriers in one or more buffer units. If the line is equipped with two buffer units for example, it is more sensible to use the first buffer unit, after the plastic ampoules have been loaded into the carriers. The filled carriers can then be buffered in case a downstream machine, such as a labeller, thermoform packaging machine or box erector, breaks down. As soon as a loaded carrier gets to the first buffer unit, an empty carrier is fed from the second buffer unit, so a closed system is maintained, in which the individual object carriers are kept in circulation.
Another application for carrier systems is assembling finished products in a closed process. This can, for example, be pre-filled syringes, which are assembled in an upstream process and then orientated and separately placed in an object carrier. This carrier, which can also serve as a transport pack, is then fed in a controlled way to the packaging process via conveyors. At the packaging machine, a gripper picks up the products from the carriers and places these into the pack cavities either individually or in groups.
With its wide range of automation solutions and individually designed carrier concepts, MULTIVAC offers needs-based and cost-effective solutions for virtually all requirements in the medical, pharmaceutical and cosmetic industries. The market leader's high level of expertise in automation and complete systems ensures every project is approached holistically, and that its comprehensive range of equipment from one source provides perfectly tailored components in the most complex of projects. An end-to-end system of line-motion control, which includes all the modules in the line, ensures a reliable process and optimum product flow, as well as maximum efficiency and transparency with minimum effort, are always achieved. Each product and every pack is monitored continuously, immediately detecting any faults.
10.03.2020