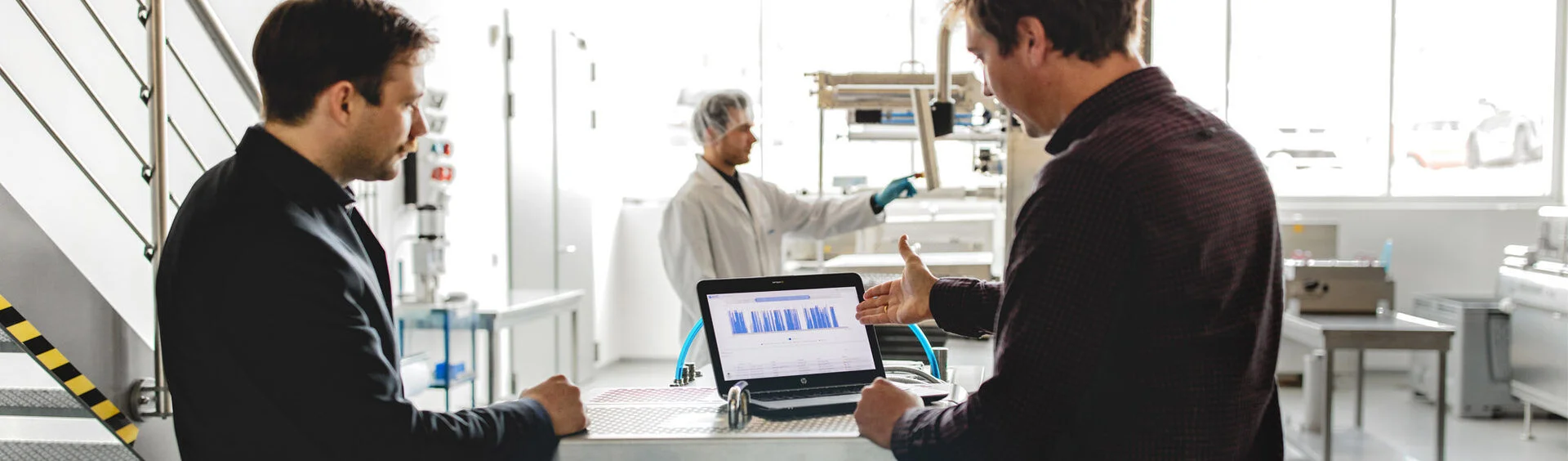
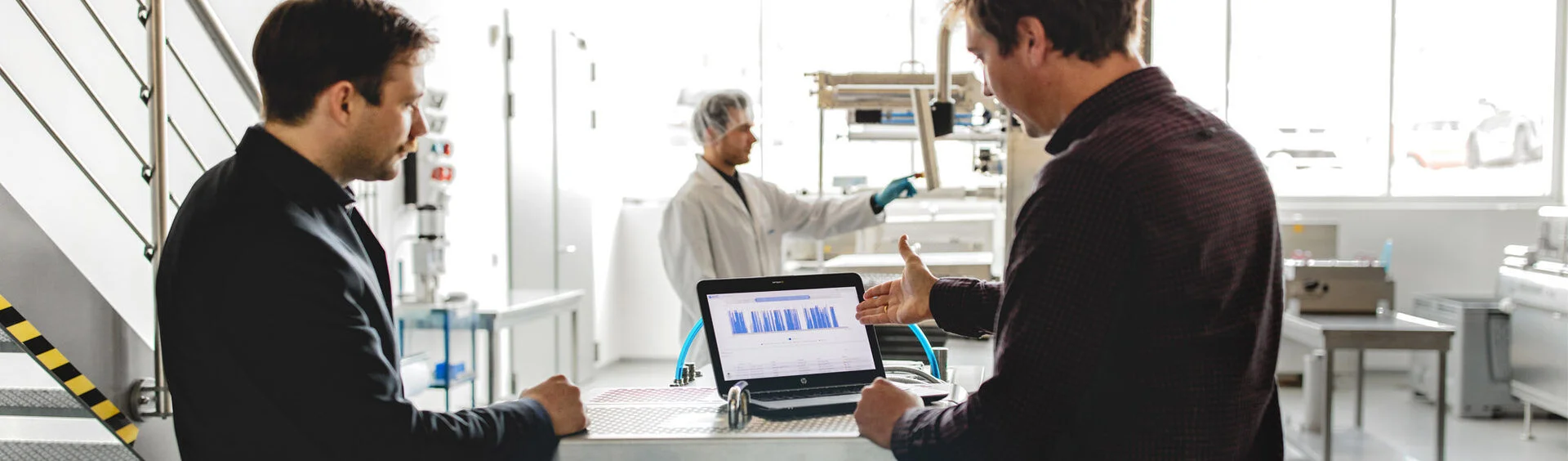
The story of Ter Beke began in 1948, when the Ter Beke dry sausage business was founded out of Francies Coopman’s butcher shop. Today Ter Beke is a major Belgian public limited company, which has developed into a highly successful food group. In total the Group has approx. 2,650 employees. In 2020 the turnover amounted to around 717 million euros.
The focus of the main division of the business is on the development, manufacture, production, slicing and packaging of high-quality processed meat, which can be found in retail outlets across Europe. The product range is very wide, extending from liver pâté through to cooked ham, sausages, salami, chicken and turkey products, and right up to meatloaf and minced roasts. Three of the six processing plants of the division are in Belgium, while the remaining three are located in the Netherlands. The products are sold under various retailers’ labels, but are also present on the shelves under their own brand names of Pluma® and Daniël Coopman®.
A second mainstay of Ter Beke’s business is the production of ready meals for the entire European market. Two factories for these products are in operation at the Belgian sites of Wanze and Marche-en-Famenne, while others are located at Mézidon-Canon in France, Opole in Poland and Deeside in the UK. Ter Beke is one of the market leaders throughout Europe with its lasagne meals under the brand names of Come a casa®, Vamos® and Stefano Toselli®, as well as many own-labels.
Up to 2016 the Ter Beke site at Veurne had not yet been working intensively with MULTIVAC, although there was a close relationship between both companies. For more than ten years, there had been two MULTIVAC machines for packing lasagna in operation at the Wanze site. “We realized during a factory visit in Wolfertschwenden, that MULTIVAC is the specialist for packaging and processing thanks to its groundbreaking packaging solutions and comprehensive expertise in lines and automation, and this makes it a highly competent partner for us,” says Technical Director Johan Meire, explaining the intensive collaboration that has since developed.
In 2018 the investment was made at Veurne in several new packaging lines from MULTIVAC. At the heart of each line is a R 535 thermoforming packaging machine, which is designed for packing large batches at high output. Each line also includes a H 050 handling module, as well as two MR 625 OP labelers and two MR 635 UP labelers for applying top and bottom labels to the packs. An additional handling module places the finished packs in boxes at the end of the line.
Sausage producers place great importance in particular on optimum product protection and extended shelf life for the products. An attractive pack design is also however very important, so that the product can be presented at the point of sale with the right brand image.
Here the lines are packing sliced products, such as raw and cooked ham, salami and cooked sausage, in so-called multilayer packs with two separate pack chambers, which enable just one part of the product to be removed as required from the opened pack chamber. The other half of the product remains sealed in the pack under modified atmosphere until it is next required, which means the product is ideally protected. This is not only user-friendly, but also helps to prevent food waste. The lower web is a paper fiber-based material, an APET/PE material is used as the upper web, and there are two opening aids on each pack.
The key to success however is not only a high level of product quality, innovative packaging ideas and the company’s particular agility. “We have orientated our production decisively towards Industry 4.0,” explains Johan Meire. The declared aim: Firstly, predictive maintenance to minimize unplanned downtime and increase machine availability, as well as ensure that the optimum performance of the lines is always achieved. Secondly, capturing and evaluating process-related data as an important requirement for quickly detecting the main factors in faults, and therefore being able to introduce suitable measures at the right time.
The decision to implement MULTIVAC Smart Services for the first time was made at the beginning of 2018, when Ter Beke ordered four new packaging machines from MULTIVAC for the Veurne site. The machines were connected in August of the same year. “The installation itself lasted just a few days. Thanks to the pre-installation measures and the interfaces that were provided, the connection of the machines was also carried out very quickly. Only the adaptation for IT, i.e. the firewall, ports and similar, required a little more time, says Johan Meire.
In concrete terms, Ter Beke currently uses the Smart Production Dashboard, so that they can always keep an eye on the packaging process. This means for example, that differences in output between various shifts can be detected at an early stage, and long-term trends plotted, so that suitable measures can be taken quickly. Key performance indicators are visualized transparently and in real time – and also remotely and therefore very flexibly via a tablet or computer. In addition to this, it is also possible to compare the various machine configurations with each other, as well as the number of packs produced. The objective is to get a simple and quick overview of the current packaging processes.
The Smart Log Analyzer is also activated – for Ter Beke this is the most important instrument. This service provides a targeted fault analysis, by evaluating the machine’s log data and identifying the main reasons for any faults, which occur during the analyzed time period. These are sorted according to frequency, cause of the downtime and average duration of the downtime, and they are then depicted graphically. Thanks to the very clear visualization, it can be seen precisely, in which time periods the machine was in a producing or stopped state. This means that it can be quickly established, whether for example there are problems when starting up. In addition to this, the three most frequent faults are shown separately – and it can therefore be immediately recognized, which problems are to be viewed as particularly critical. Problems can therefore be eliminated in a targeted way, and the effectiveness of the packaging solution is increased significantly. MULTIVAC service technicians can also gain information in advance about the machine and its status, so that they can support customers in a targeted way. A typical example of this in the case of Ter Beke was a recurring fault with a safety error which was investigated by the Smart Log Analyzer. Thanks to the installation of an additional light barrier, it was possible to solve the problem permanently.
The MULTIVAC Smart OEE Analyzer is not currently used at the Veurne site, since the company’s own production software for overall equipment effectiveness is used for this purpose. The intelligent tool from MULTIVAC is however an effective aid for those companies, which do not already have the appropriate software, since it visualizes the overall equipment effectiveness (OEE) of a machine on an interactive dashboard, and this enables machine settings to be optimized very quickly.
If MULTIVAC Smart Services are activated at a customer, the main benefit is better and faster service for the particular packaging solution. The detection of frequent factors in faults is carried out remotely, so that it is not necessary for a service technician to be on site. This saves time, effort and also of course cost.
When seen overall, predictive maintenance and comprehensive MULTIVAC Remote Assistance are important preconditions for utilizing the full output potential of packaging lines, as well being prepared for any faults that may arise. And last but not least, the typical smaller faults as well as the first signs of more serious breakdowns can be prevented, while wearing parts can also be replaced in good time.
Those at Ter Beke regard the collaboration with MULTIVAC as being very constructive. The digital solutions have been a great help from the start, but further adaptations will of course have to be carried out on an ongoing basis, since MULTIVAC is continuing to expand its range of services in this area. “We are extremely interested in further developments of these services, and we are of course keen to be kept updated,” says Johan Meire.
The next stage will see the degree of automation further increased, enabling the human involvement to be successively reduced. The objective is to exclude operating faults and unplanned downtime as far as possible. This will always be a challenge for Ter Beke, given the potential for smaller faults inherent in the complexity of the lines, the wide product range and the sophisticated pack design.
The team leaders in the slicing and packaging areas, as well as the Technical Service department and top management, have complete access to the data and MULTIVAC Smart Services at Veurne. Reporting currently takes place on a monthly basis, but this is due to change. “It is only through regular analysis and the appropriate evaluation, that all the potential for optimizing the entire process can actually be exploited,” says Charles Van Lerberghe in summary.
In future one can expect at the Belgian sausage producer, that the data from all suppliers will be bundled together on one platform, so that any faults can effectively be traced along the entire line, and the specific production orders for the individual recipes can be amalgamated, enabling the entire production process to be optimized still further. Predictive maintenance is also due to be intensified by means of new tools and online services.
MULTIVAC is already however offering further tools, such as Smart Data Backup and Smart Machine Report, to meet the demand for digital solutions. Further developments are planned to create real added value for customers.
13.07.2021