MULTIVAC Line Control
Simple. Central. Networked.
MULTIVAC Line Control (MLC) is an innovative and pioneering solution for controlling lines and optimising production. It simplifies operation and significantly increases the efficiency of the line.
Recurring operating processes, such as starting, stopping, standby, running the line empty and changing products become standardised and reproducible processes throughout the line thanks to MLC, and they can be performed from each control terminal within the line.
Using the constantly growing number of functions for line diagnostics, item management and batch handling, MULTIVAC Line Control makes an important contribution to the quality and reliability of the processes within the line, as well as the traceability of packs and products.
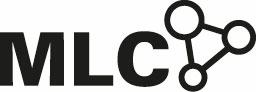
Batch handling for food
Reliable traceability of food products
In the food industry the safety and quality of products have the highest priority. Here MULTIVAC Line Control batch handling makes a crucial contribution to fulfilling the highest quality standards, and ensuring that seamless traceability is maintained – for every pack along the production line from the unprocessed product to the finished pack.
- Seamless traceability
- Consistent product quality
- Efficient packaging processes
- Complying with legal regulations
- Strengthening customer trust and your brand reputation
Batch handling for medical and pharmaceutical products
Focus on patient safety
Patient safety has the highest priority with medical and pharmaceutical products. Batch handling with MULTIVAC Line Control makes a significant contribution to transparent and secure processes, as well as for tracing products and packs.
- Traceability and transparency
- Consistent quality
- Efficient packaging processes
- Regulatory requirements