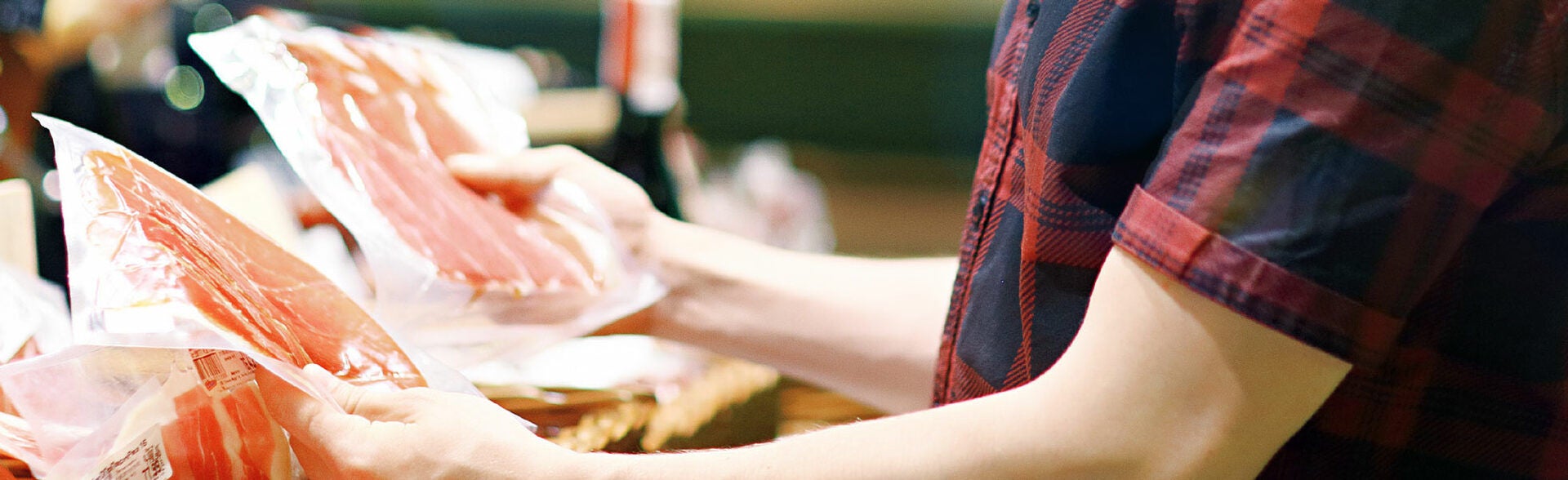
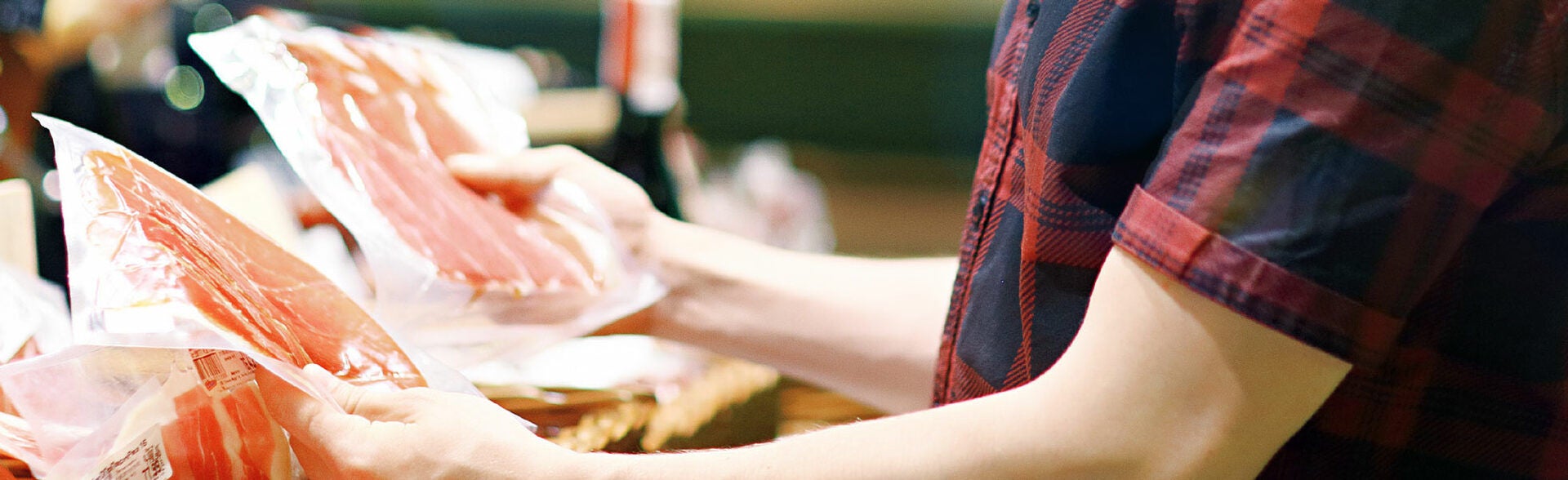
Bisher haben wir Fleischprodukte wie durchwachsenen Speck, Braten, Koteletts, Steaks, Schweinefüße oder auch Hackfleisch direkt in den Filialen in EPS-Trays verpackt, mit Cling-Wrap-Folie umwickelt und etikettiert. Dieses Konzept wollten wir durch ein Verpackungskonzept verbessern, das uns dabei unterstützt, die Verschwendung von Lebensmitteln zu minimieren und zugleich unsere Prozesse zu optimieren. Zielführend schien uns, dass jede Filiale selbst frische Ware für die Kühltheke verpackt – mithilfe der Einführung eines Skin-Verpackungskonzepts.
Weitere Haupttreiber für die Investitionsentscheidung waren für uns die Verlängerung der Haltbarkeit der Produkte und damit einhergehend eine erhöhte Produktqualität. Aber auch die Verringerung des Packstoffverbrauchs zählte zu den ausschlaggebenden Faktoren. Durch die Umstellung auf MultiFresh™ Vakuum-Skinverpackungen können wir nun wesentlich ressourcenschonender verpacken und damit auch einen Beitrag für unsere Umwelt leisten.
Unsere Lösung umfasst jeweils eine Tiefziehverpackungsmaschine des Typs R 105 MF, einen Chiller von Hyfra sowie nachfolgend ein Transportband und den Preisauszeichner GLM-EVO von BIZERBA. Je nach Platzangebot in den einzelnen Filialen sind die Verpackungsmaschinen in einer geraden Linie oder mit einem 90° Transportband im Produktionsfluss ausgeführt. Daher ist die R 105 MF für uns eine gute Wahl, denn das kompakte Einstiegsmodell fügt sich optimal in die vorhandenen Produktionsumgebungen ein und erzeugt hochwertige Vakuum-Skinverpackungen von gleichbleibender Qualität.
Das Verpackungskonzept erfüllt die Forderung nach einer verlängerten Haltbarkeit der Produkte, denn durch den Entzug der Atmosphäre wird der biochemische Verfall des Lebensmittels verlangsamt. Zudem werden Qualität und Frische, Farbe und Struktur des Fleisches in der Packung natürlich präsentiert, das Produkt erscheint den Konsumenten hochwertiger. Insgesamt zeichnen sich die Packungen also auch durch eine bessere Optik aus. Sowohl die bei Bergendahls verwendete Oberfolie als auch die Unterfolie stammen von WIPAK – wir haben das Projekt gemeinsam mit dem Folienhersteller geplant und ausgeführt. Die Supermarktkette produziert heute trotz höherer Materialkosten durch die Verwendung der Skinfolien attraktivere Verpackungen zu einem akzeptablen Preis.
In der Tat. Dies spiegelt sich auch in der Tatsache wider, dass wir weiterhin gute Umsatzzahlen erreichen konnten, obwohl wir ein Verpackungskonzept ersetzt haben, an das der Verbraucher sehr gewöhnt war. Ein neues Verpackungskonzept hätte sich auch ohne weiteres negativ auf unseren Umsatz auswirken können.
Zu den wichtigen Aspekten bei dieser großen Investition gehörte für uns die verlängerte Haltbarkeit, die zu einer signifikanten Reduzierung der Lebensmittelverschwendung beiträgt. Zudem ein veränderter Prozess, der zu einem neuen Workflow und einer besseren Arbeitssituation für unsere Mitarbeiter führte. All dies basiert auf dem Konzept des Tiefziehverpackens mit Material von der Rolle. Wir sind heute in allen 43 Filialen in der Lage, schnell auf Bedarfsschwankungen zu reagieren. Durch das Verpacken vor Ort können wir auch die kontinuierliche Verfügbarkeit der Ware während der Öffnungszeiten zwischen 7.00 und 22.00 Uhr sicherstellen. Und wir haben die Möglichkeit, ein breiteres Produktspektrum in den Kühlregalen anzubieten oder direkt auf Kundenwunsch Ware zu verpacken.
Parallel verringerte sich der Lebensmittelabfall bei uns signifikant – erfreulicherweise um insgesamt 63 Prozent. Bislang mussten wir rund 230 kg Fleisch je Supermarkt pro Woche vernichten, weil beispielsweise das Haltbarkeitsdatum abgelaufen war. Das entspricht insgesamt einem Abfallvolumen von 520 Tonnen jährlich. Durch das neue Konzept und den damit verbundenen, deutlich reduzierten Lebensmittelabfall können wir nun bei der beachtlichen Investitionssumme für die 43 Maschinen den Break-Even, grob geschätzt, nach etwa zwei Jahren erreichen.
Insgesamt haben sich die Haltbarkeit unserer Fleischwaren und damit auch die Produktqualität signifikant verbessert – Rind- und Schweinefleisch ist nun statt vier insgesamt 14 Tage lang haltbar, bei Hackfleisch erhöhte sich die Haltbarkeit von 24 Stunden auf sechs Tage.
Die Verbraucher erhalten zudem ein frisches Qualitätsprodukt in einer Portionsgröße und Zusammensetzung, die ihren Bedürfnissen gerecht wird. Dank der integrierten Peelecke ist die Packung leicht zu öffnen.
Die Umstellung auf das neue Verpackungskonzept wirkt sich insbesondere auch auf unsere Packstofflogistik und den Produktionsfluss in den Filialen positiv aus. Mussten wir bislang eine Vielzahl an Trays für die unterschiedlichen Produkte einkaufen, bevorraten und zielgerichtet zu den Filialen bringen, sind wir heute mit Material von der Rolle deutlich effizienter im Prozess, deutlich flexibler hinsichtlich der Formgebung bzw. des Designs der Packungen und damit insgesamt deutlich wirtschaftlicher.
Parallel dazu verringerten sich der Personalaufwand und der Zeitaufwand im Bereich Verpackung. Denn die Tiefziehverpackungsmaschinen sowie die Linienkomponenten sind einfach und sicher über das intuitive HMI der R 105 MF zu bedienen, die Umstellung auf andere Produkte und Packungsformate lässt sich ohne größeren Zeitaufwand realisieren. Unsere Mitarbeiter wurden von MULTIVAC auf den neuen Anlagen umfassend geschult und von uns in die veränderten Produktionsprozesse eingewiesen.
MULTIVAC ist Weltmarkt- und Technologieführer im Bereich Tiefziehverpackungsmaschinen – und in Schweden mit einer Niederlassung vertreten. Der Abstimmungsweg ist also kurz, der Markt bestens bekannt. Und mit MultiFresh™ haben wir eine Skin-Lösung gefunden, die genau unseren Vorstellungen entspricht. Ausschlaggebender Faktor für die Entscheidung war zudem, dass die Installation der Maschinen in den Filialen innerhalb eines sehr kurzen Zeitfensters erfolgen sollte. Es musste unbedingt gewährleistet sein, dass über sechs bis acht Monate hindurch jeweils zwei Maschinen pro Woche in Betrieb gehen können. MULTIVAC war der einzige Anbieter, der uns dies garantieren konnte.
Das enge Zeitfenster war natürlich anspruchsvoll, doch MULTIVAC ist aufgrund seiner Organisationsstruktur auf solche Anforderungen ausgelegt. Zudem verfügen wir über eine umfassende Projekterfahrung insbesondere im Lebensmittelbereich. Grundsätzlich ist bei der Implementierung eines neuen Verpackungskonzeptes jedoch stets die Produktionsumgebung zu berücksichtigen. Entscheidende Faktoren hierbei sind beispielsweise, in welchen Temperaturbereichen eine Linie arbeitet und ob der Produktfluss während des Verpackungsprozesses gekühlt werden muss. In jeder Filiale ist die komplette Linie darüber hinaus an die räumlichen Gegebenheiten anzupassen. Durch die modulare Bauweise unserer Maschinen und aufgrund unseres breiten Portfolios an geeigneten Zu- und Abführsystemen stellt dies aber in der Regel kein größeres Problem für uns dar.
Bei Bergendahls/City Gross waren darüber hinaus durch die Umstellung auf völlig neue Packungsformate umfassende Verpackungstests unabdingbar. Solche Tests bieten wir unseren Kunden gerne an, denn nur so können wir am Ende ein optimales Packungsergebnis sicherstellen.
14.04.2019