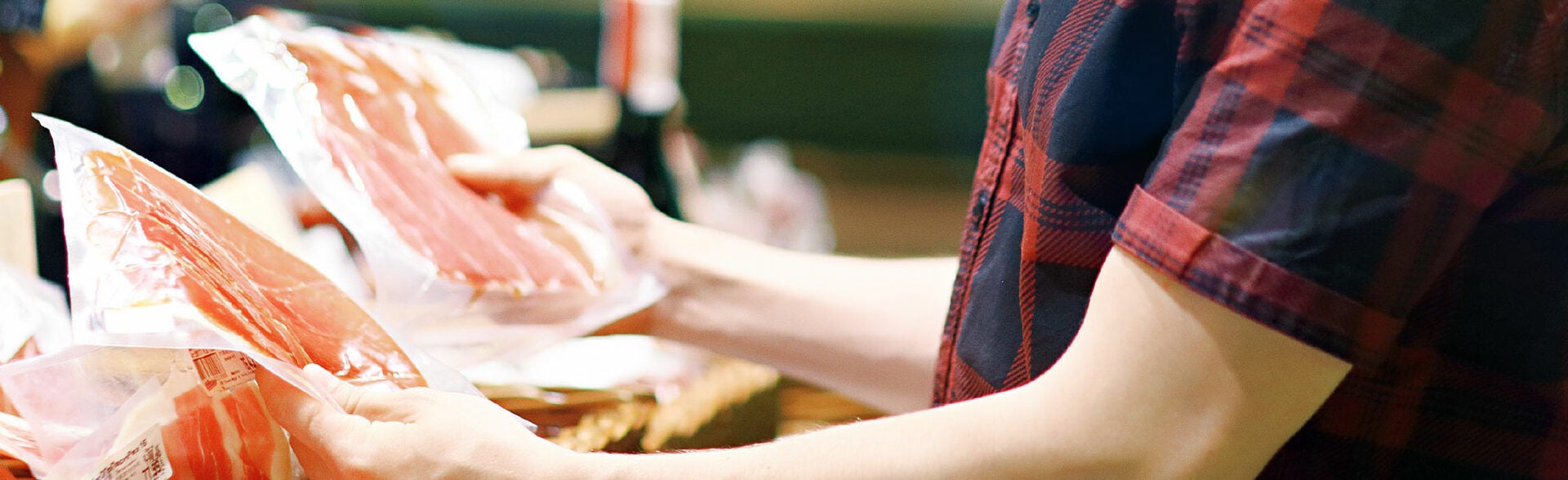
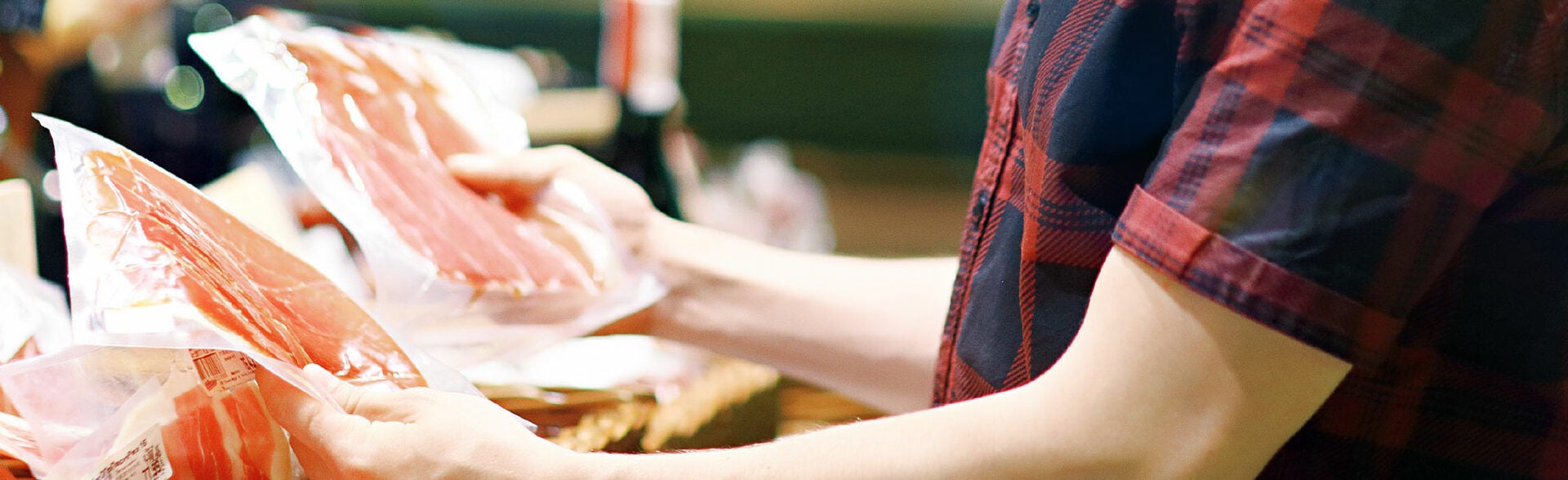
Previously each of our retail outlets had used EPS trays, which they wrapped in clingfilm and then labelled, to pack its own meat products, such as streaky bacon, roasting joints, chops, steaks, pig's trotters, and minced meat. We wanted to improve this concept by introducing a form of packaging which would assist us in minimising food wastage, while at the same time optimising our production processes. It seemed expedient to us that each retail outlet should continue to pack its own fresh product for the chill counter - but with the introduction of a skin packaging concept.
Other main drivers for the investment decision were the extension of the product shelf life and the accompanying increase in product quality. However, another crucial factor was the reduction in the consumption of packaging materials. Thanks to the changeover to MultiFresh™ vacuum skin packs, we can now save considerably more resources when packing our products, enabling us to make a significant contribution to our environment.
Each of the individual packaging solutions comprises a R 105 MF thermoforming packaging machine, a Hyfra chiller, a downstream transport conveyor, and a GLM-EVO weigh-price labeller from BIZERBA. Depending on the space available in the particular retail outlet, the packaging line is designed in either a straight line or with a 90° transport conveyor in the production flow. The R 105 MF is a very good choice for us, since the compact entry-level model fits ideally into the existing production environments, and it produces high-quality vacuum skin packs with consistent quality.
The packaging concept meets the demand for extended product shelf life, since the biochemical degradation of the food is slowed down by the removal of atmosphere from the pack. The quality, freshness, colour, and texture of the meat in the pack are also presented in a natural way which enhances the appearance of the product to the consumer. Overall the packs also present a much better visual appearance. Both the upper web and lower web used at Bergendahls are supplied by WIPAK – and we planned and implemented the project in conjunction with the film manufacturer. Despite higher material costs for the use of skin films, the supermarket chain is today producing more attractive packs at an acceptable price.
Very much so. This is also reflected in the fact, that we have continued to achieve very good sales figures for the products, even though we have replaced a packaging concept, which was very familiar to the consumer. A new packaging concept could have had a negative impact on our sales turnover.
One of the most important aspects for us in this large investment was the increased shelf life of the products which has contributed to a significant reduction in food wastage. Another aspect was the changed production process, which has created a new workflow and an improved working situation for our staff. All of this is based on the concept of thermoforming packaging with material from the roll. Today we are in a position, in all 43 retail outlets, to react quickly to fluctuations in demand. Thanks to the continued use of packing on site, we can still ensure products are available constantly during our opening times between 7.00 and 22.00. And we are now also able to offer a wider range of products in the chill cabinet, or alternatively pack products immediately at the customer's specific request.
In parallel with this, food waste at our retail outlets has reduced significantly – by a total of 63 percent, which is very pleasing. Previously we had to destroy around 230 kg of meat per week in each supermarket, because, for example, the use-by date had expired. This corresponds to a total waste volume of 520 tons per year. Thanks to the new concept, and the accompanying significant reduction in food waste, we can now reach the break-even point for the considerable investment in 43 machines within roughly two years.
Overall the shelf life of our meat products and their quality have improved significantly – beef and pork products can now be kept for 14 days instead of four, while minced meat has increased its shelf life from 24 hours to six days.
Consumers also receive a fresh quality product in the portion size and composition, which meet their requirements. Thanks to the integrated easy-open corner, the packs are simple to open.
The changeover to the new packaging concept has had a particularly positive effect on our packaging material logistics and the production flow in the retail outlets. Whereas previously we had to buy and store a wide range of trays, as well as getting them on time to the right retail outlets, we are significantly more efficient today with reel-fed materials, and we are also more flexible as regards the shape and design of packs which makes us overall considerably more cost-effective.
In parallel with this, we have seen a reduction in time and effort by the staff involved in packing our products. The thermoforming packaging machines and the other line components are easy and reliable to operate via the intuitive HMI on the R 105 MF, and the changeover to other products and formats can be accomplished without great effort or time. Our staff were trained comprehensively by MULTIVAC on the new equipment, and we gave them thorough instruction on the changed packaging procedures.
MULTIVAC is the world market leader and technology innovator when it comes to thermoforming packaging machines - and it has its own subsidiary in Sweden. The distances are short and the market knowledge unparalleled. And with MultiFresh™ we have found a skin pack solution which meets our requirements exactly. Another crucial factor in the decision was the fact that the machines had to be installed in the retail outlets within a very short timeframe. There had to be an absolute guarantee that two machines per week would go into operation over a period of six months. MULTIVAC was the only supplier, which could give us this guarantee.
What were the greatest challenges in the project, Mr Källman?
The tight timeframe was naturally very challenging, but MULTIVAC is of course prepared for such demands thanks to its organisational structure. We also have comprehensive project experience, particularly in the food sector. When a new packaging concept is implemented, the production environment must always be taken into account as a matter of principle. The critical factors are, for example, the temperature range in which a line is operating, and whether the product flow has to be chilled during the packaging procedure. In addition to this, the complete line at each retail outlet had to be matched to the space available. Thanks to the modular construction of our machines and our wide range of infeed and discharge systems, this generally did not present too great a problem for us. In the case of Bergendahls/City Gross, it was also essential to carry out comprehensive pack tests since they were changing over to a completely new packaging format. We are always happy to offer our customers such tests, since it is only through these that we can guarantee the optimum packaging result.
14.04.2019