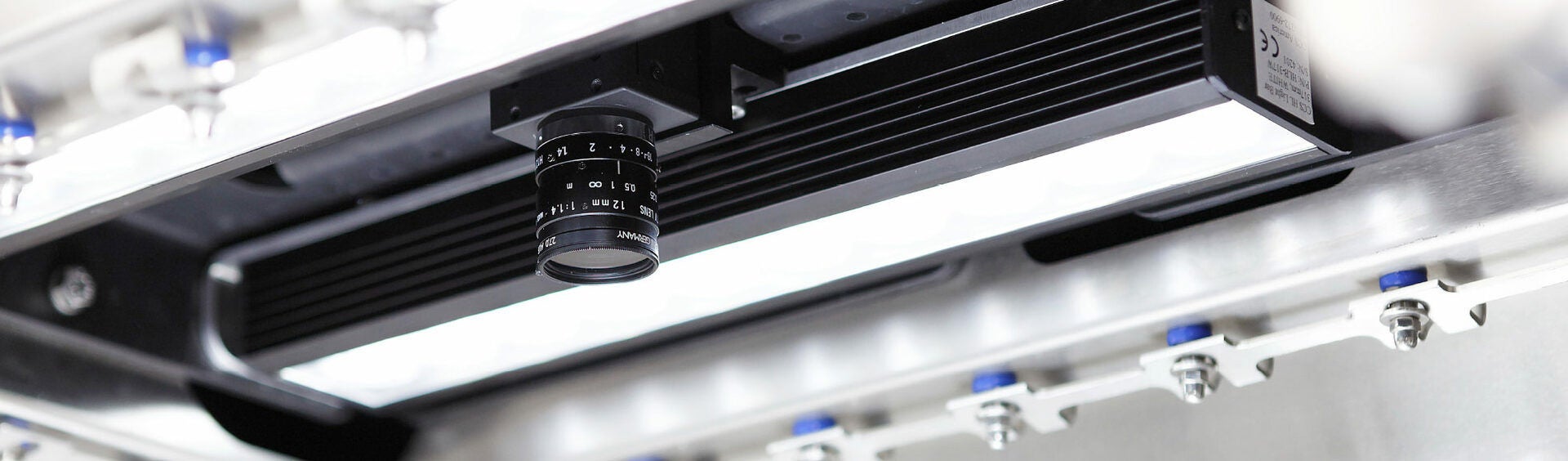
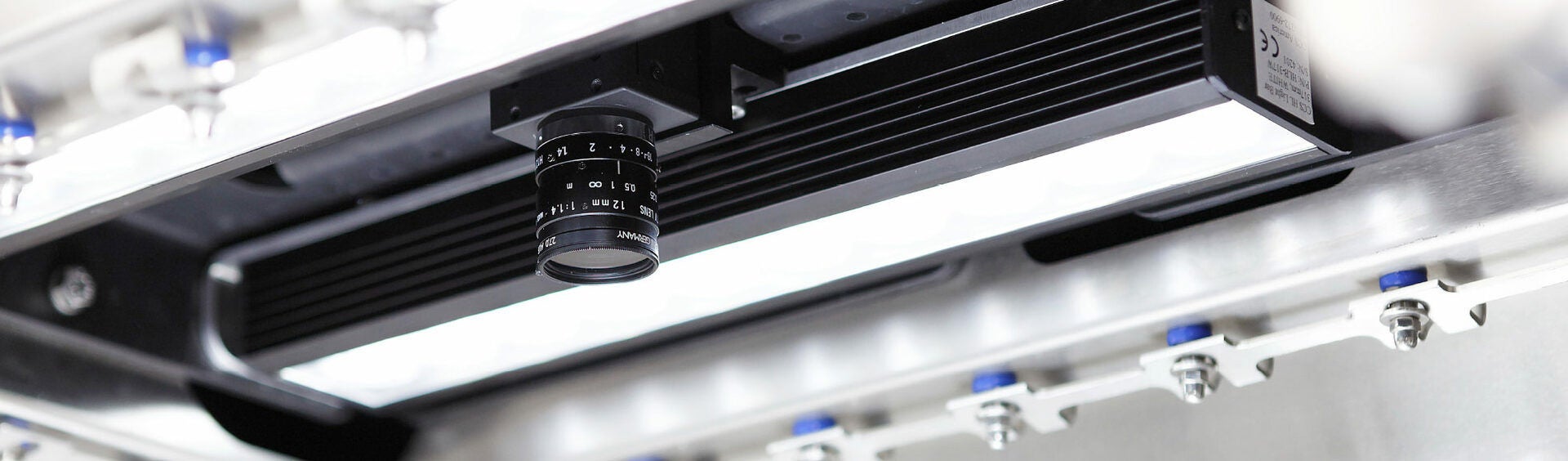
Higher output capacity with fewer personnel, as well as improvements in resource and cost efficiency, are just some of the factors that make investment in automatic packaging solutions economically sensible. Other aspects, such as consistently high packaging quality and attractive pack design, are also important factors, which make a major contribution to differentiating products at the point of sale and increasing turnover. Although inspection solutions have no direct influence on the product and its packaging or its success at the point of sale, they are an important aspect.
In order to meet statutory requirements for consumer information and traceability, it is absolutely essential that printed information on labels and film is both correct and legible. The constantly rising demands in food labelling inevitably leadto greater complexity in the labels.
In accordance with the EU Food Information Regulation (1169/2011), all mandatory information must be printed in a defined minimum size. In addition to the list of ingredients, these mandatory details include best-before date, allergy information and a consumer-friendly nutritional table in a precisely defined format. In addition to this, there is a wide range of other data such as batch numbers for traceability, various logos and seals of approval, barcodes for scanners as well as QR codes, which enable consumers to call up more product information via their smartphone.
The complexity is further increased by the trend towards an ever greater diversity of product types, as well as the requirement for having information on labels in various languages, which are often difficult to keep apart.
In parallel with the rising complexity of food labelling, there is also growing pressure on food manufacturers, particularly those involved in the export business. Labelling faults such as illegible barcodes, incorrect use-by dates or even an entirely wrong product label can lead to complete deliveries being returned. Manufacturers are then subjected to considerable direct and indirect costs, which can range from significant expense for logistics and disposal, right up to the expense of replacement production and even damage to the company's reputation. In the case of severe infringements, there can often be contractual penalties or even delisting of the affected products. But even small defects in appearance, such as a misaligned label, can also have an adverse effect, because they damage the brand image and suggest to the consumer, that the quality of the product is lower, and that there has been less care taken in processing and packing the product.
Even if labelling faults are discovered at the production stage, this can also incur very significant costs and effort internally within the company. Packaging lines are frequently automated from end to end as far as the secondary packaging stage. If, for example, a fault is only discovered during a random check at one of the final process stages, the whole batch may become unusable or require considerable reprocessing and repacking. The rule of thumb is quality inspections must be implemented as early as possible in the process.
In order to ensure only faultless packs actually get into the retail chain, there should be quality control at individual pack level, and this means random inspections in industrial-scale production and packaging processes are today no longer sufficient to guarantee 100% security. Due to the increasing output capability of packaging lines as a result of automation, it is no longer possible to perform comprehensive label inspection with the human eye, while the packaging process is in operation. It is for this reason that today food manufacturers, who operate at high cycle rates, can not avoid implementing quality control with automated inspection systems.
Common applications include checking the presence of print and the correctness of variable data, as well as inspecting the legibility of codes. But more complex inspection tasks, such as character recognition (OCR, Optical Character Recognition) and character verification (OCV, Optical Character Verification), as well as code analysis and pattern recognition for inspecting logos or defined label shapes, can also be performed with inspection systems. They ensure, even at high process speeds, every individual pack is inspected reliably in accordance with the particular demands of the product and pack. MULTIVAC offers a comprehensive range of solutions for all these label inspection requirements - from simple inspection tasks right up to the most complex and demanding challenges. When it comes to establishing label presence, sensors such as luminescence, colour or contrast sensors can be used. But barcode scanners and code readers can also check the presence of labels, as well as inspecting the legibility of their barcodes. The content of the code can also be analysed and compared with the corresponding reference data. However, in the case of complex or multifunctional inspection tasks, for example from character and pattern recognition right up to comprehensive image analysis, PC-based matrix or line scanner systems, for example MULTIVAC MVS, are the equipment of choice. The high-performance MULTIVAC I 420 inspection solution on a thermoform packaging machine can, for example, inspect markings on a pack for legibility and code content by means of character recognition or character verification. The label position and alignment can also be detected, as well as the shape of the label and defined pattern features. If print inspection is performed by means of a camera-based inspection system, MULTIVAC can also support its customers with a so-called "Optical Character Recognition (OCR) specification". The crucial minimum requirements as regards fonts, line spacing, contrast and other parameters, which are defined in this specification, ensure the labels can be read faultlessly by the inspection system, and they can therefore be checked with 100% reliability.
Depending on the application, there are several possibilities for integrating the inspection solution into the particular packaging line: if the pack is being labelled by a cross web labeller for example, the inspection system is installed on the outfeed of the packaging machine. Visual inspection systems can also be integrated into conveyor belt labellers, or they can operate independently of packaging or labelling systems, for example as a free-standing end-of-line solution downstream of a traysealer. It is also generally possible to retrofit inspection solutions to an existing packaging line without any problems.
In addition to this, integrated line control offers even more benefits. An inline quality inspection system, which is completely integrated into the line, can initiate the ejection of reject packs and even make it easier to adjust modules, while the packaging process is running. If, for example, a creeping deterioration in the print image is detected, or a gradually increasing displacement of a label, counter-measures can be taken to control the situation at an early stage, before the print image or label goes outside the tolerance range. Reject packs can therefore not only be detected quickly but even prevented completely.
As a supplier of complete solutions, MULTIVAC has extensive experience in visual inspection systems and their seamless integration into packaging lines. The wide range of expertise enables MULTIVAC to give its customers the most comprehensive advice and to meet their specific requirements with customised or specially programmed solutions. When viewed overall, an automated visual inspection system offers added value and security in every respect and, depending on the scope of the particular inspection solution, the investment is often amortised very quickly.
27.02.2020