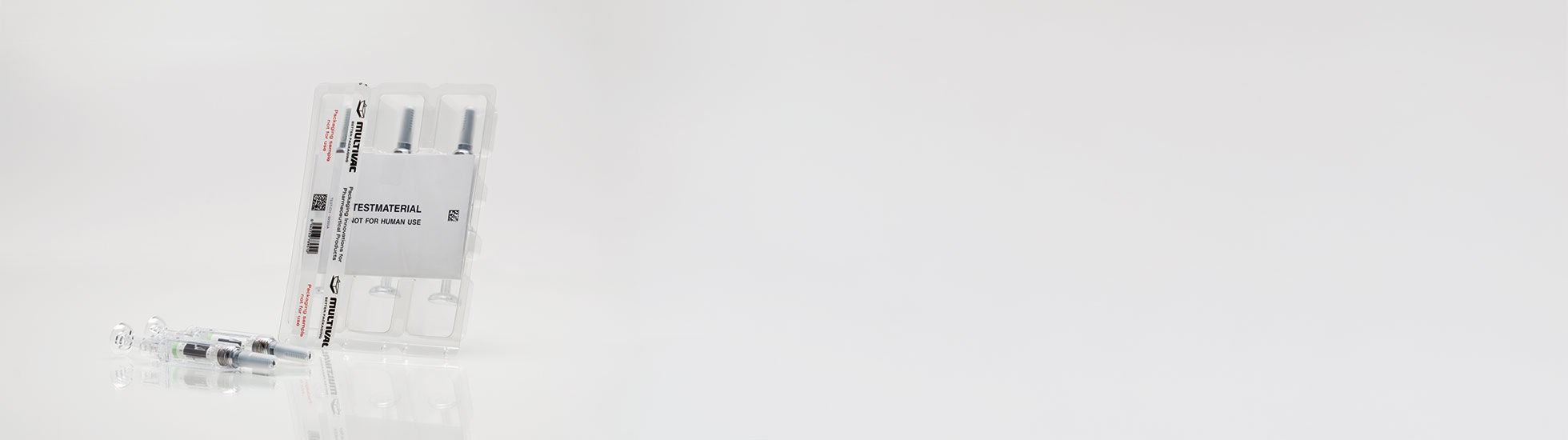
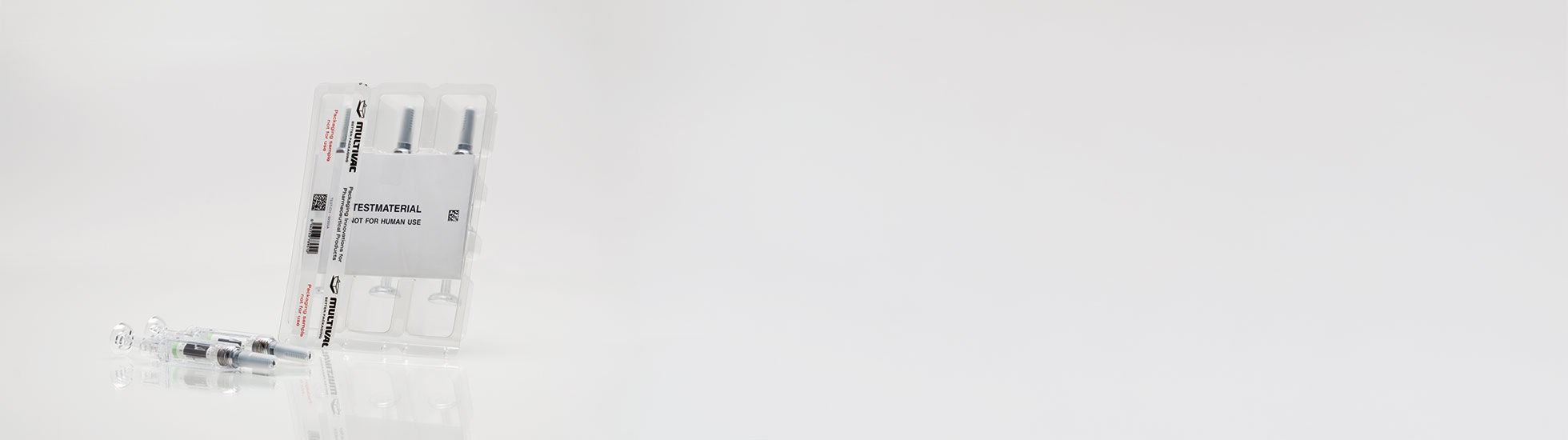
Depending on the particular application, MULTIVAC offers various packaging systems, capable of being equipped with different infeed and loading solutions, such as thermoforming packaging machines with modular automation systems, which enable various products to be packed at different throughputs. The possible types of product infeed include linear vibrating units, universal infeed systems with belts, inclined conveyors, centrifuges and transport systems with object carriers.
When producing combi packs for pharmaceutical products, the top priority is to ensure the packs are loaded completely and that the individual components are securely protected in the pack. Products, which are filled with active ingredients, must not of course get lost or be damaged during the packaging procedure, and the individual substances must also be prevented from being activated or mixed with each other when being packed. It is also an essential requirement, that any damaged products are safely ejected from the packaging procedure.
Depending on the product characteristics, it is usually necessary to separate and align the products during the infeed process by means of different systems. Those parts for example, which are delivered as bulk products, can be separated and orientated by means of vibrating units, while filled syringes are usually fed in on carriers or belt systems. Loading the particular products into the pack cavities requires loading systems, which ensure the products are precisely picked, placed, and positioned with great accuracy in the pack cavities.
A typical application is the packaging of several products with a leaflet in a complex combi pack forming. A very high level of process reliability is required. Increasingly, product manufacturers are demanding packaging solutions from one source, into which modules from third-party suppliers can also be integrated if required. With its exceptional expertise in packaging lines and automation, MULTIVAC is the right partner.
Combi packs are usually assembled from product components consisting of materials with different characteristics, such as soft, hard, adhesive, or non-adhesive materials. Each individual component must be gently and securely placed in the position provided for it in the pack. This means the thermoformed pack must be equipped with different cavities, in which the products can be correctly positioned and firmly located. The use of a forming system with plug assist can optimise the precisely tailored forming of the pack cavity. The product components are generally loaded automatically, allowing a high level of process reliability to be achieved.
When developing the appropriate packaging solution, the following requirements must also be taken into account: in addition to ensuring the content of the pack is complete, the sensitive products have to be firmly located in the pack and incapable of being able to slide around. In the case of high-value products in particular, it must be ensured that they do not get lost during the packaging procedure. It must also be possible to check the completeness of the combi pack and the print image on the upper web during the packaging procedure.
The production process for a combi pack with various small components is explained in the following example.
One part of the product is supplied as a bulk product and transported to the handling module via a universal infeed system. During this process a “brush”, which rotates above the transport conveyor, separates the partly clinging or overlapping products, so they are now lying separately on the transport conveyor. The position and orientation of the products are captured via a vision system, and these are signaled to the gripper on the pick & place robot. The robot uses suction grippers to pick up the products from the transport conveyor and place them in the pack cavity provided. All products, which the gripper does not pick up, fall into a collection container and are fed back to the system.
A further component is also supplied as a bulk product, but this is transported into a centrifuge via an inclined conveyor. The individual products are separated and orientated in this centrifuge. They then arrive via a rail system at a turntable, onto which two products can be placed each time. The turntable rotates alternately counter clockwise and clockwise, and at each rotation movement one product is dispensed onto the turntable. Light sensors check the presence of the products. A suction gripper then picks up the products from the turntable and positions them in the particular pack cavity. The turntable rotates again during this pick & place procedure, and a new product is then ready for picking.
Before a further, high-value product component is loaded into the pack, a presence check is performed on the two other products by means of a vision system. The high-value product component is only loaded into the pack, when the two earlier components have been loaded completely into the pack and also positioned correctly. The high-value component is delivered by an inclined conveyor and separated by means of vibrating rails. A rail system is used to orientate the products into a vertical position and then transport them onwards. A 90° deflection rail ensures that at the end the products are horizontal again and all positioned in the same alignment. This means they can be individually removed from the carrier plate by means of a dispensing system and then placed in the pack cavity. In the meantime, a new product is positioned. The leaflet is then loaded automatically by means of a leaflet dispenser to complete the pack.
An important requirement for such automatic packaging procedures is the possibility if required of being able to intervene manually in the process and subsequently position the products correctly. The packaging lines are generally therefore designed in such a way, that sufficient space is left after the automated loading station for manual loading of missing products, for example.
The individual good cycles and reject cycles are visualised by means of coloured light signals, which are in the form of lights installed in the frame: a green light means a good cycle, a red light means a reject cycle. Reasons for a reject cycle may, for example, be a pack cavity that is not completely formed. A red light also however shows the operator, when the film has been too long under the hot heating plate (dwell time monitoring), or if a product is missing.
If the packs are correctly and completely loaded, they are transported to the sealing station. Unprinted paper, Tyvek® or plastic film is used as the upper web. Immediately before being sealed, the upper web can be printed by a thermal transfer printer with variable data such as LOT number or production date etc. A vision system can also be used in this area, and after the sealing station it inspects the print image for presence, legibility, and correctness.
After the sealing process has been completed, the packs are separated by means of cross and longitudinal cutters. The finished individual packs are then transported onwards by means of belt conveyors and are subsequently picked up by a handling module. In order to optimise the footprint of the packaging solution, this module can be integrated into the packaging machine and installed on the machine frame. The suction grippers remove only the good packs from the belts and then transfer them to a further conveyor, which is connected at a 90° angle. The packs are removed on an individual pack basis. The conveyor then transports the good packs to the next process stage, which is generally transferring them into secondary packaging boxes. The reject packs run out of the line via individual belts and are collected in a waste box. Line-motion control ensures all reject packs are ejected properly, and this is also carried out on an individual pack basis. The removal of good packs complies with the “good philosophy” principle - it guarantees that no reject packs can be among the good packs.
In order to meet the requirements of the pharmaceutical sector in full, as regards process reliability and pack security, the packaging solution can also be equipped with other features. The line can be completely housed in transparent polycarbonate sections, in which the large doors are very easy to open. This means the entire process is GMP-compliant - operators have a very good view into the interior of the machine and can quickly detect and remove products that have got lost. Secure line clearance ensures no substances or products remain in the system after the end of the batch, which means the risk of contamination or machine stoppage is very small.
In addition to this, the thermoforming packaging machine can also be equipped with hinged die top sections, which can be opened electrically, for the forming and sealing stations. These enable the dies to be fully inspected for any damage or contamination. And last but not least, the vision systems check, whether the packs are loaded completely and correctly, as well as ensuring the print on the packs is faultless.
10.06.2018