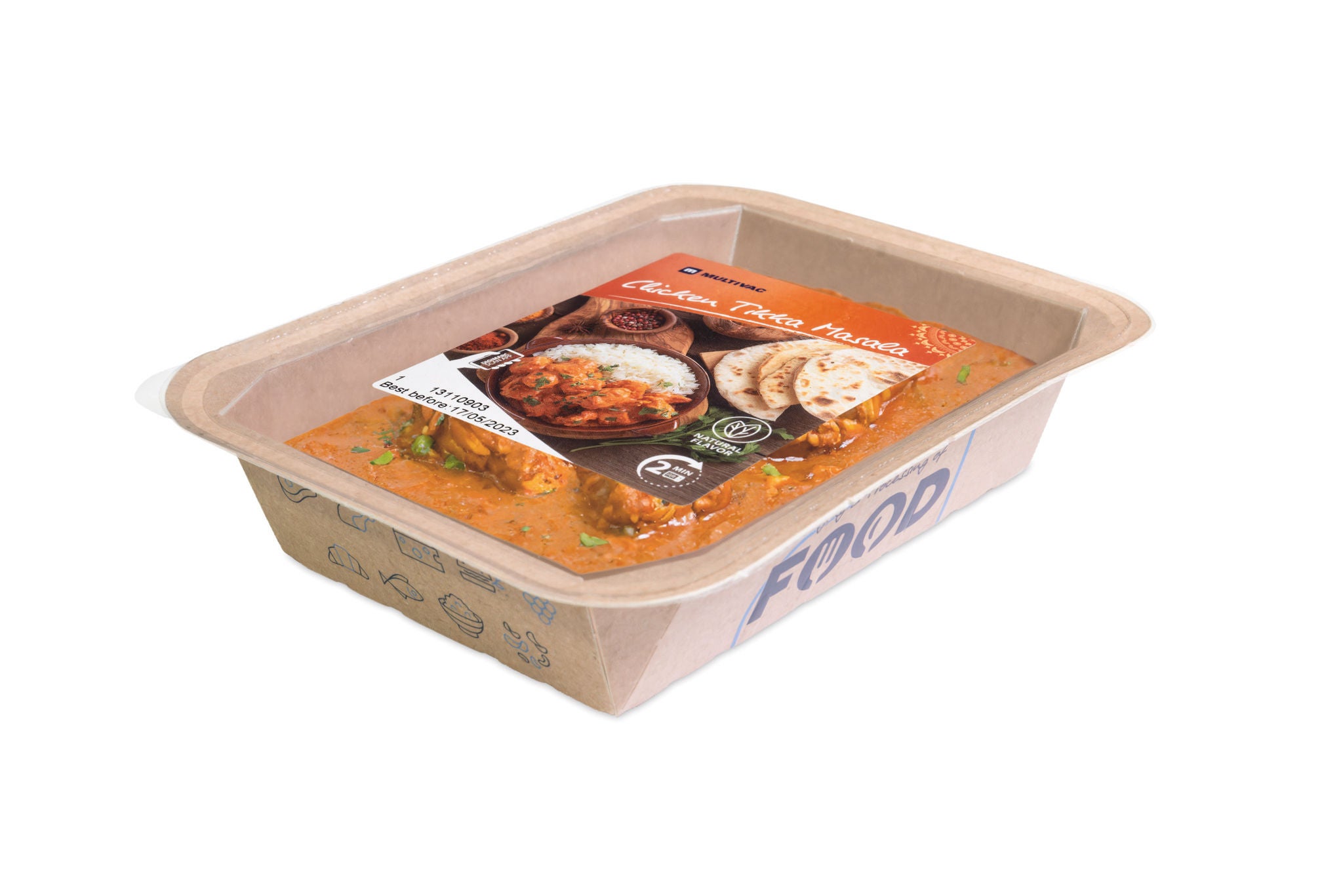
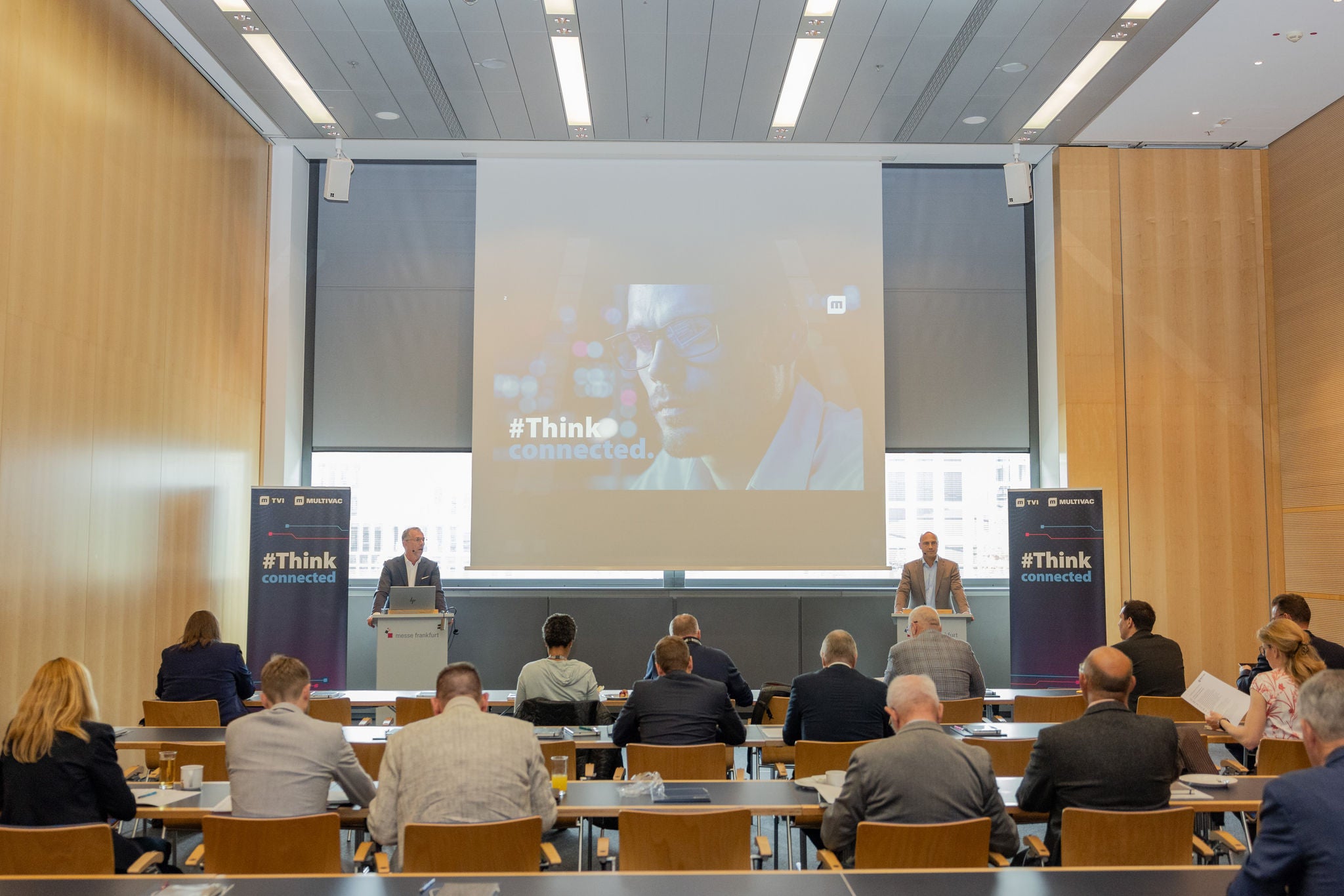
Bringing automation, sustainability and efficiency together in harmony
Press conference by the MULTIVAC Group at IFFA 2025
05.05.2025
Wolfertschwenden/ Frankfurt, 5 May 2025 – At the IFFA trade fair the Group Presidents, Christian Traumann (CEO), and Dr Tobias Richter (CSO) presented the latest developments and innovations from the MULTIVAC Group. Exhibiting under the motto #Think connected, the company is showing at the trade fair its wide range of equipment for the processing and packaging of fresh meat, processed meat products and alternative proteins. The focus is on solutions, which support food businesses of every size in increasing their efficiency. Recyclable packaging materials, optimised pack designs and more sustainable production processes all meet the demands for sustainability.
Stable turnover enables further growth to be achieved
Despite political and economic challenges, the MULTIVAC Group generated a stable turnover of 1.5 billion euros in 2024. “A solid financial result enables us to continue growing and investing in line with our strategy,” said Christian Traumann.
Expansion of the Management Board
With effect from 1 July 2025 Dr Johannes Epple will assume responsibility, as Group President and Chief Financial Officer (CFO), for Corporate Finance, Controlling, Treasury and Corporate IT. “We are delighted to welcome such an experienced management figure as Dr Epple to our Management Board,” said Christian Traumann.
Strategic investments, local and global
Among the latest investments by the MULTIVAC Group is a new Slicing Center of Excellence, which was opened in the autumn of 2024 at Buchenau in the state of Hesse. “Due to the additional Application Center there in particular, we can now offer our customers an even better and more accessible consultancy service in that wider region,” explained Dr Tobias Richter. “Thanks to the expanded development and production capacity, we now have the best conditions for continuing to develop the Slicing Business Unit successfully and sustainably.“
And by 2027 there will also be new company headquarters, costing 78.5 million euros, for the subsidiary company FRITSCH in Franconia, where in future all the company's activities in dough machine manufacture will be combined on one site.
In July 2024 the MULTIVAC Group also acquired a majority holding of 80 percent in Italianpack S.p.A., a manufacturer of automatic and semi-automatic packaging machines, which is based in Como (Italy). “Thanks to this acquisition, we have been able to expand our portfolio by adding traysealers in the lower and medium price range, as well as fillers and peripheral equipment such as denesters and lid depositors,” explained Christian Traumann.
The largest investment for the future in the more than 60 years of the company's history is currently taking place with the construction of a second production plant at the Wolfertschwenden site: The factory, which is costing around 100 million euros, comprises a manufacturing facility and a Logistics Center for supplying spare parts to the subsidiaries worldwide. “A state-of-the-art Smart Factory is the basis for the automation of our global manufacturing processes. The moving-in of the Manufacturing department has been in progress since April 2025, while the Logistics Center is due to start operation in January 2026,” said Christian Traumann. “A project of this size is for us the future as well as a duty.“
In March 2025 a new company, MULTIVAC Technology Solutions India Private Ltd, was founded in Hyderabad (India), so that capacity in IT and digitalisation could be expanded through qualified IT specialists. “Our objective is to always be able to offer our customers innovative and intelligent solutions. Here digitalisation and highly automated, software-supported lines are of central importance. The expansion is therefore an important step, and it will significantly enhance our capacity to deal with enquiries and projects more rapidly and flexibly in the areas of IT and software development,” explained Christian Traumann.
Fully automated and networked line solutions
Examples of these highly automated, software-supported lines can be seen at the trade fair: One of the highlights is a high-output slicing line for raw ham products, which is designed for outstanding efficiency. A new function of MULTIVAC Line Control (MLC), so-called
"uninterrupted product change", enables operators to change seamlessly between different items during running operation – without having to interrupt production or run the line empty. “This enables downtime to be reduced by up to 95 percent,“ said Dr Tobias Richter. “At the same time, resources are used more efficiently, since product loss as well as the consumption of film, labels and energy are all minimised. All the modules in the line are automatically adjusted to the new item – from slicing through to feeding product to packaging and labelling machines, and right up to quality inspection. This minimises manual intervention, while also reducing the risk of errors.“
With its meat portioning line for trays, MULTIVAC is demonstrating how state-of-the-art meat processing works at the highest level of efficiency. “Thanks to digital networking, all components of the line can be seamlessly controlled and analysed via the MULTIVAC Line Control,“ commented Dr Tobias Richter. “The combination of the highest portioning quality, minimal product loss and maximum personnel efficiency sets a new benchmark in industrial-scale food production. A central component of this optimisation is the live data evaluation of the individual line segments, which creates full transparency across the entire portioning and packaging process.”
And by using vision systems, they can automate pack inspection and the checking of labels and print - even at high production speeds. The AI-supported vision systems from MULTIVAC can classify products according to predefined criteria, as well as monitor portions and inspect the content of packs. Thanks to automation measures such as these, it is possible to increase line efficiency and production capacity, even with limited personnel resources.
Dr Tobias Richter summed up: “Rising costs, staff shortages and strict sustainability requirements demand solutions, which focus on all aspects of the added value chain – from raw material processing right up to packaging. Smart processing and packaging technology is a real factor in competitiveness: It helps not only to optimise the sustainable operation of the machine, but also makes it possible to achieve agile production, which can be adjusted to the growing demands of a changing market.“
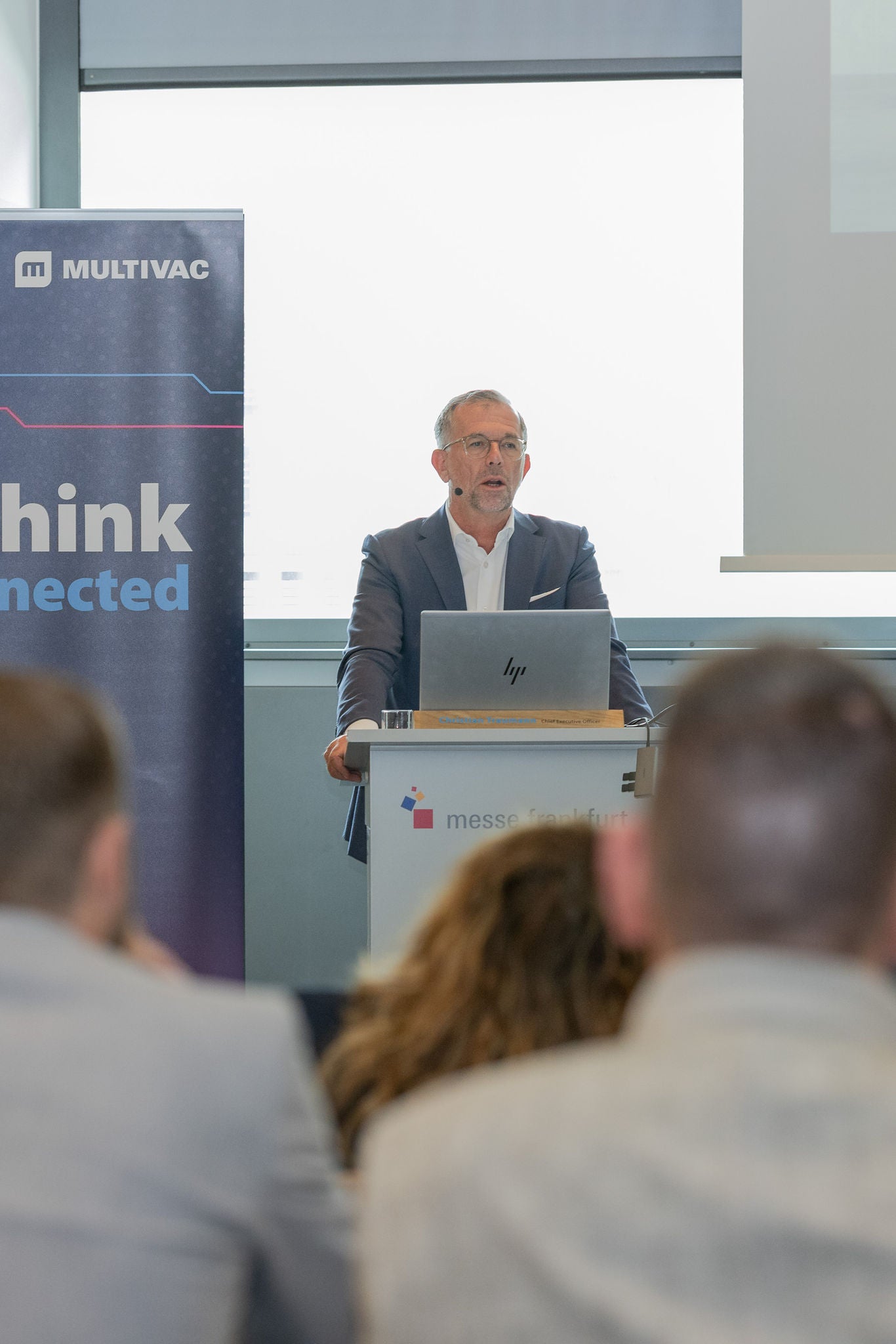
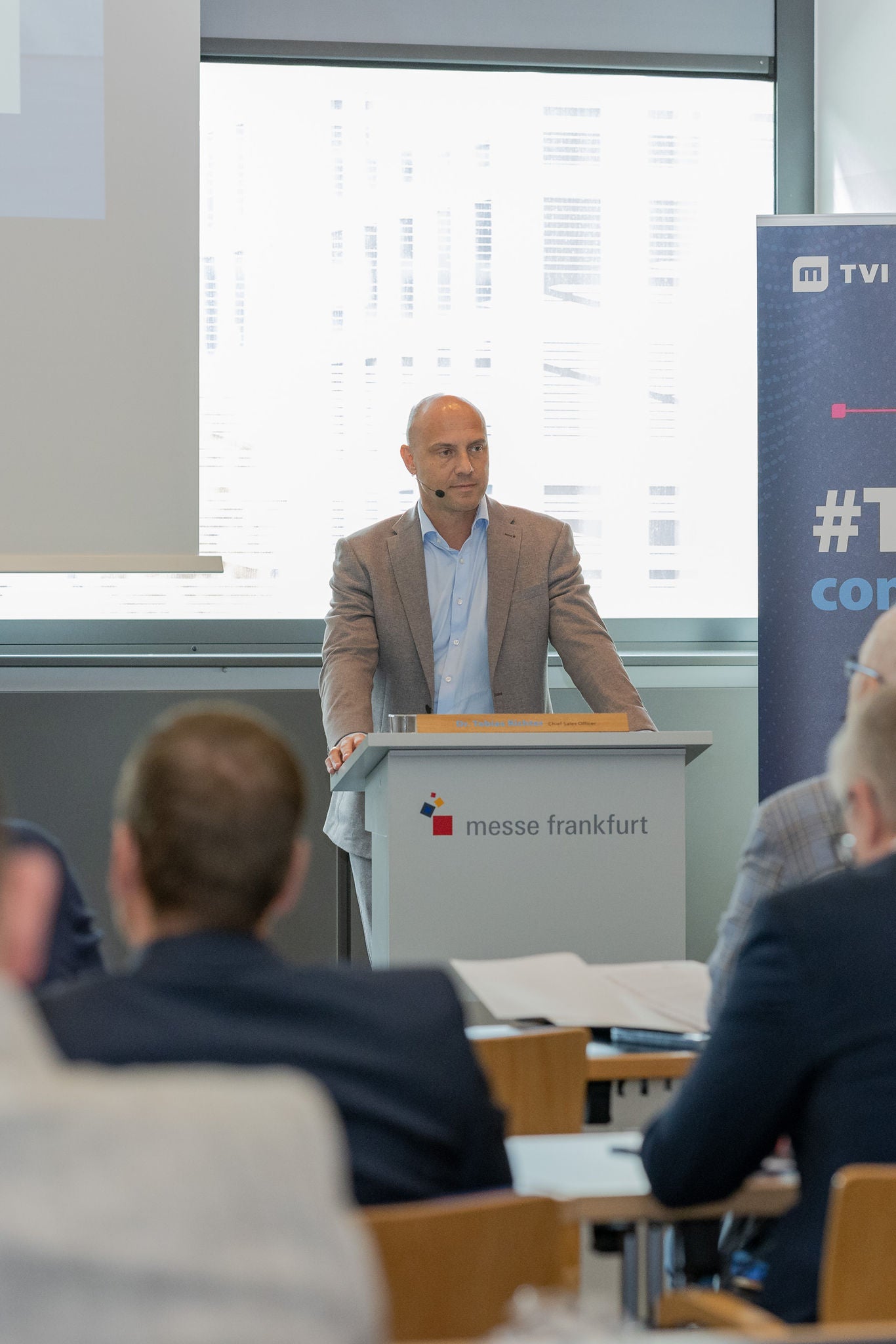
Press Release
Bringing automation, sustainability and efficiency together in harmony
- Size
- 167 KB
- Format
Latest News
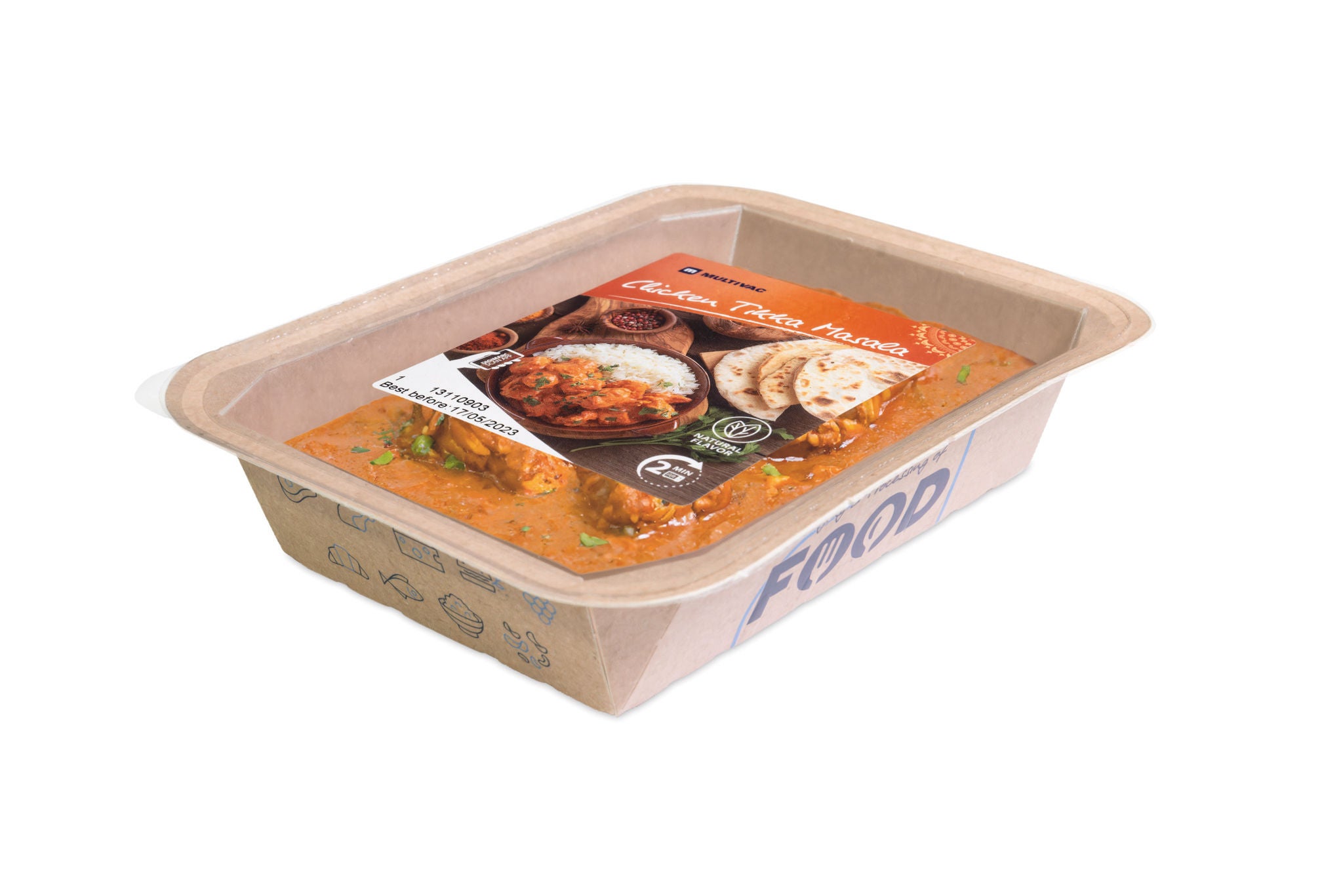
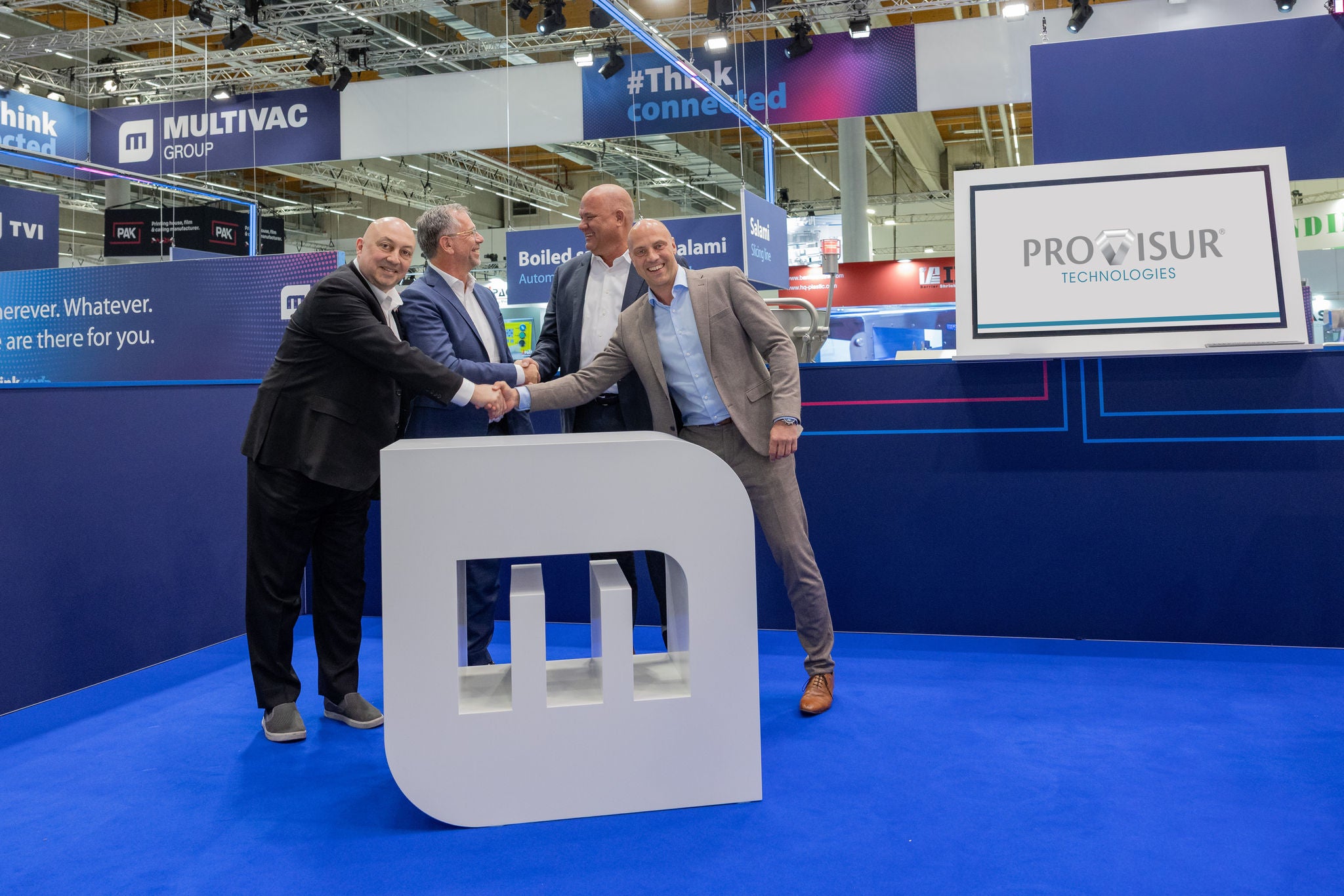
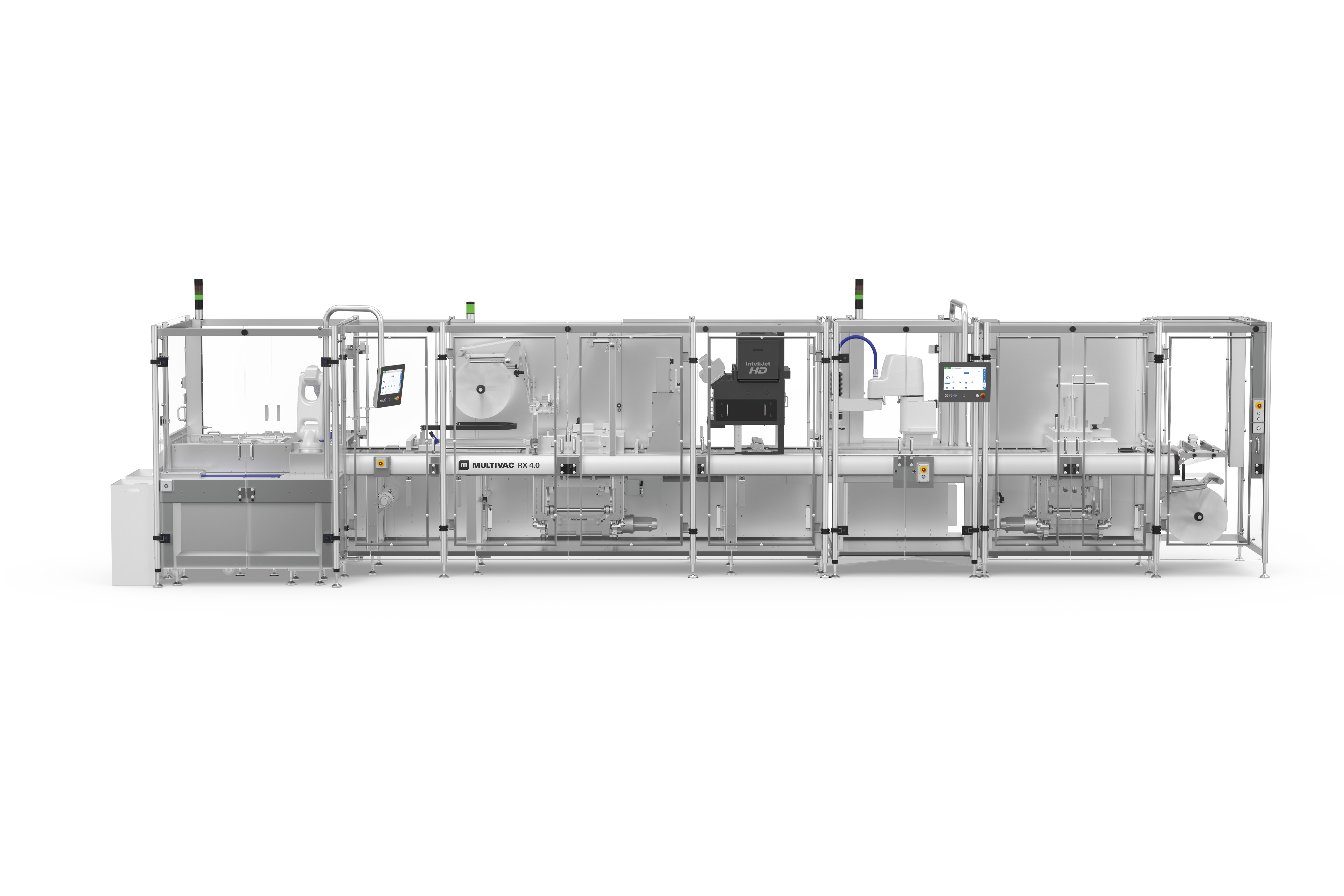
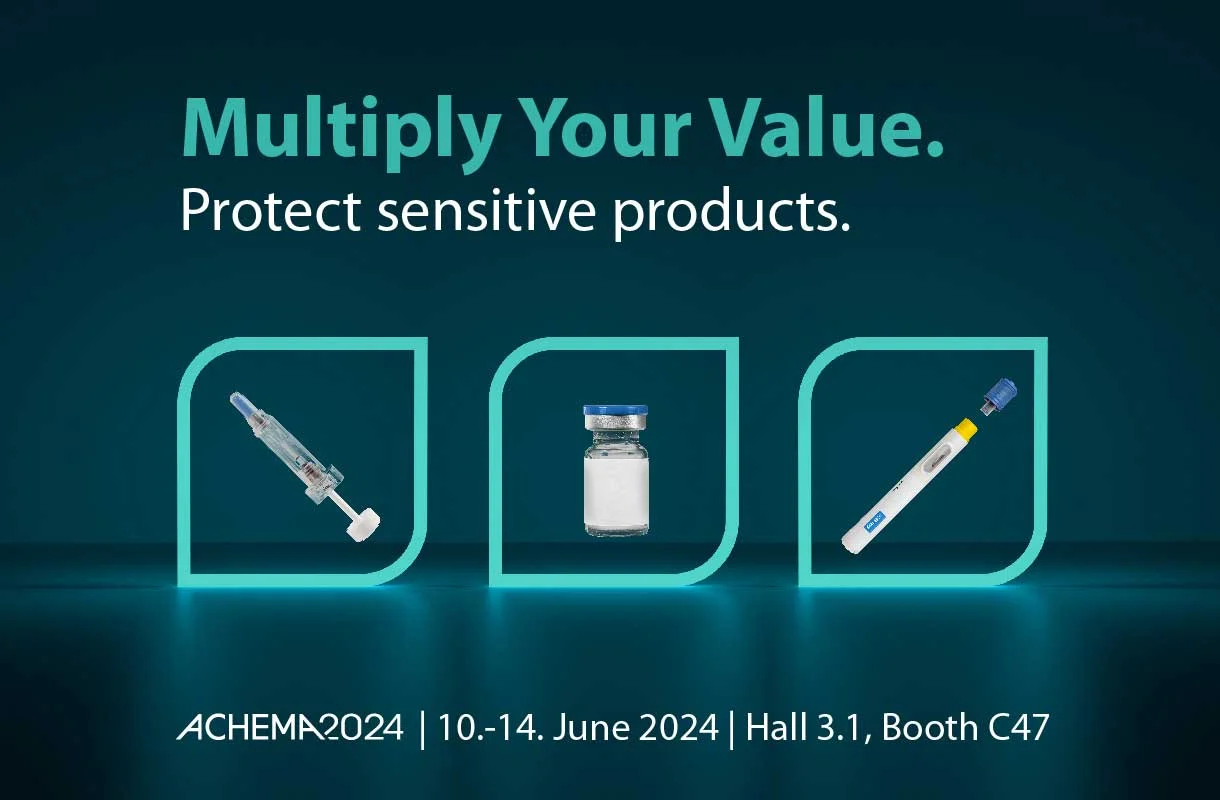
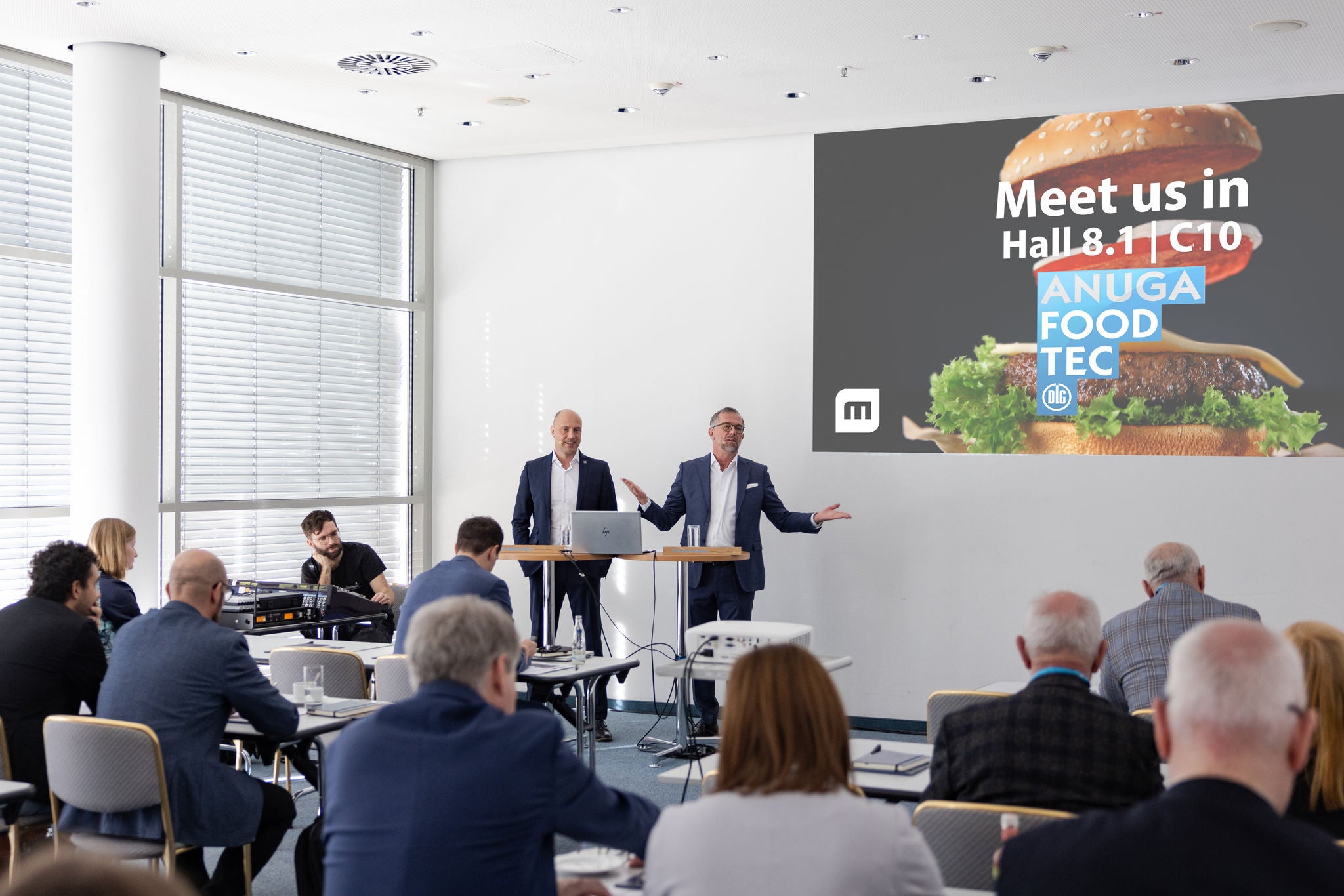
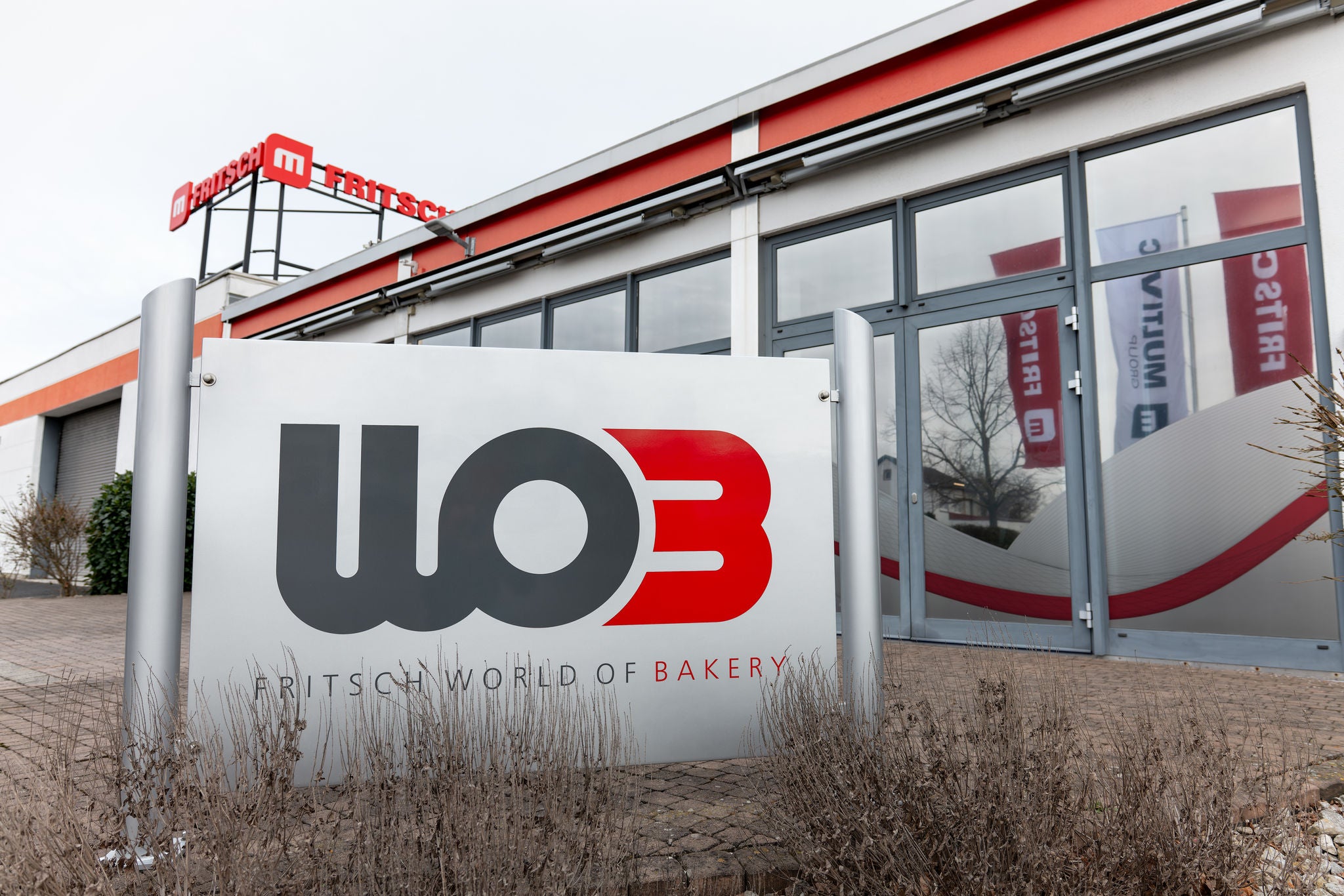
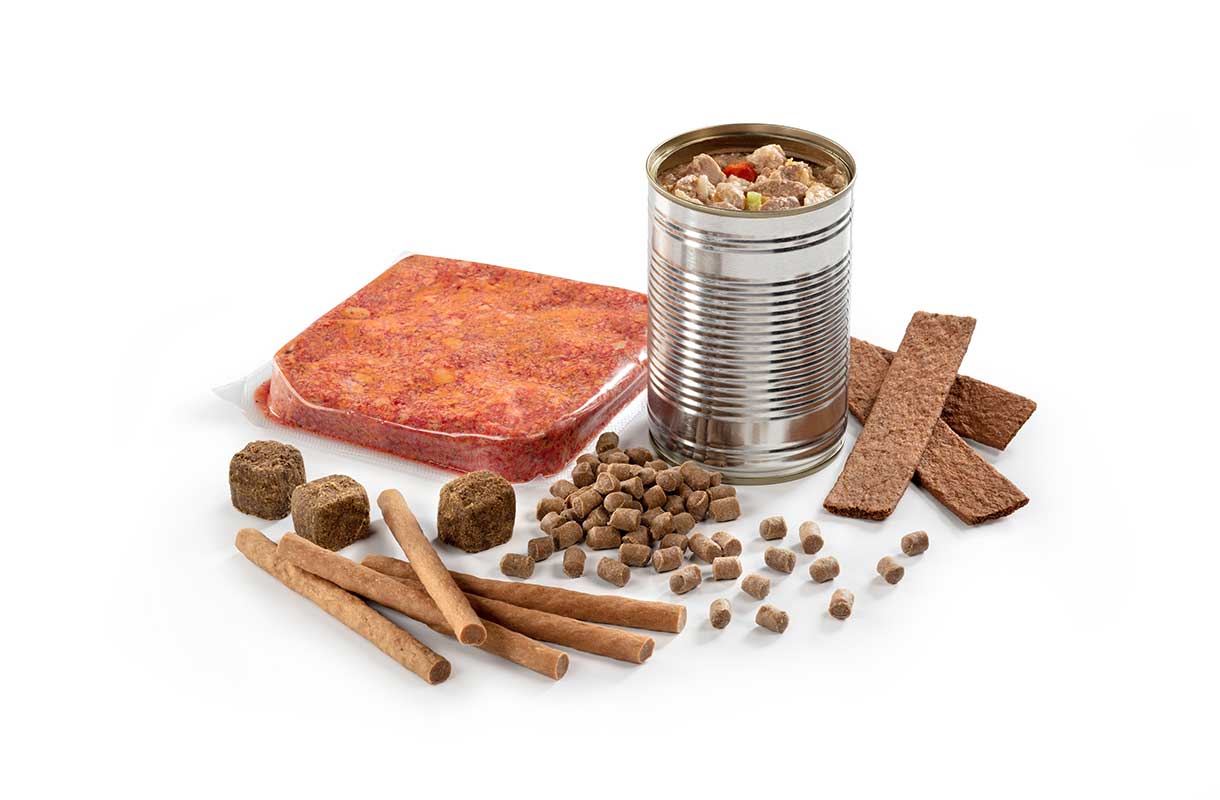
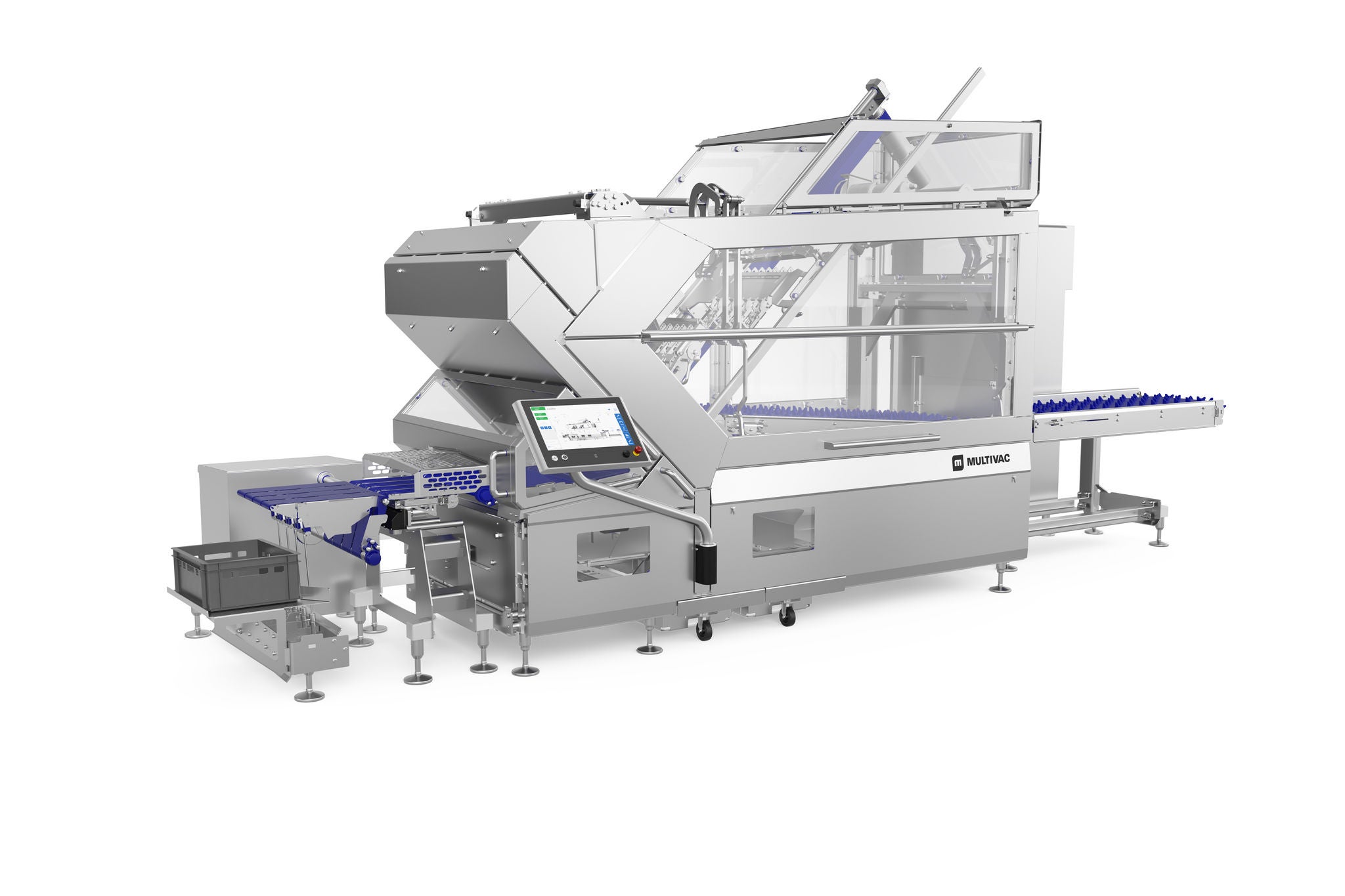
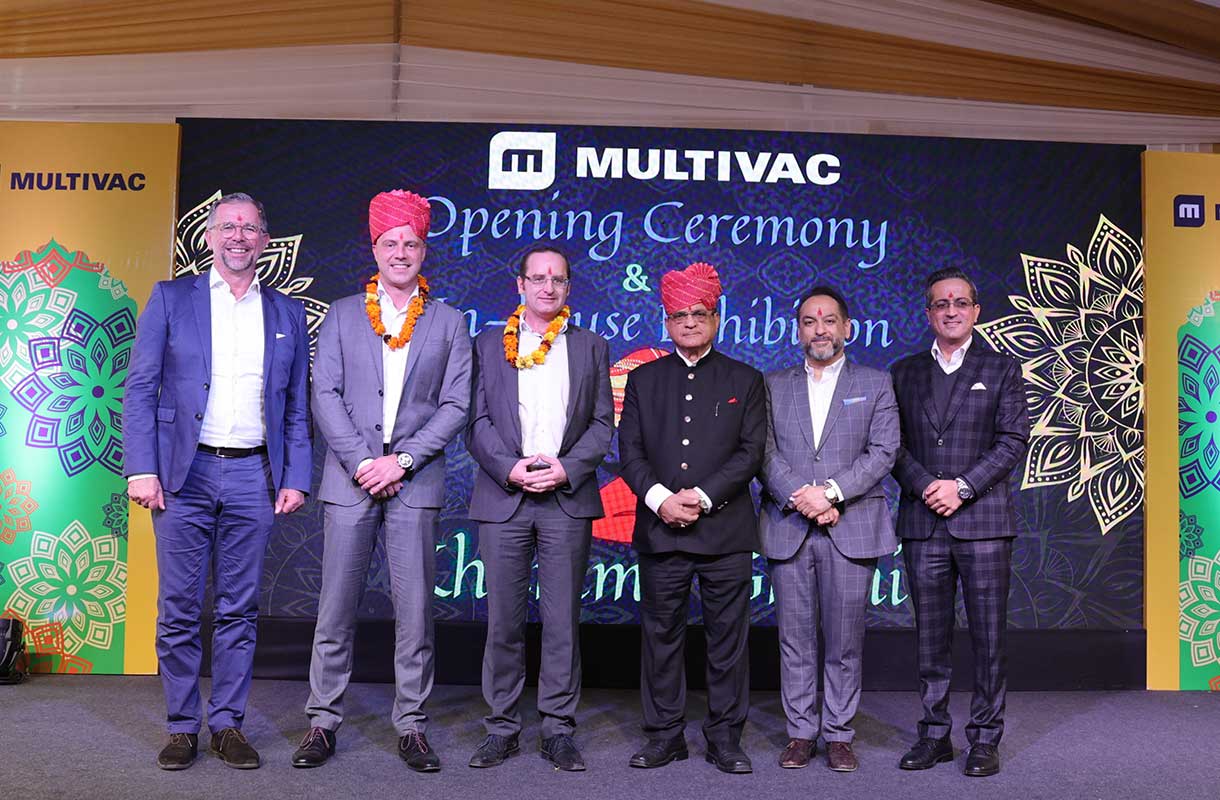
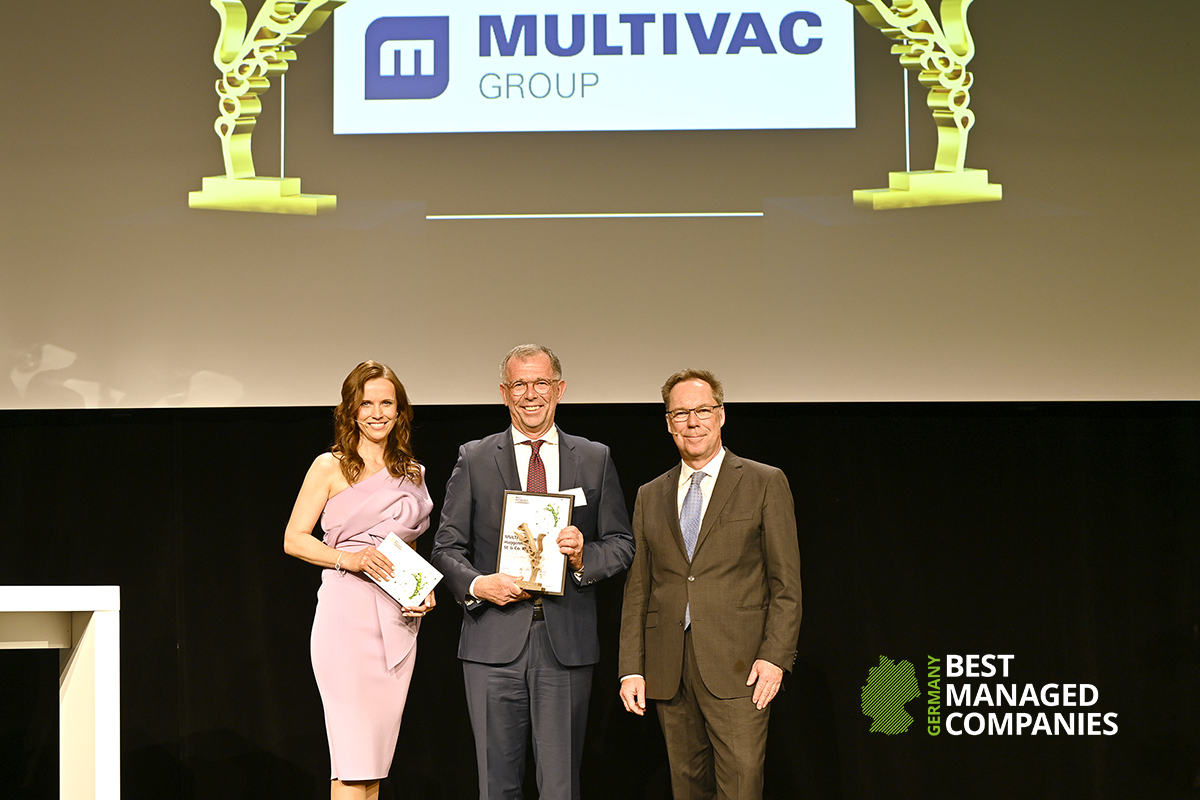
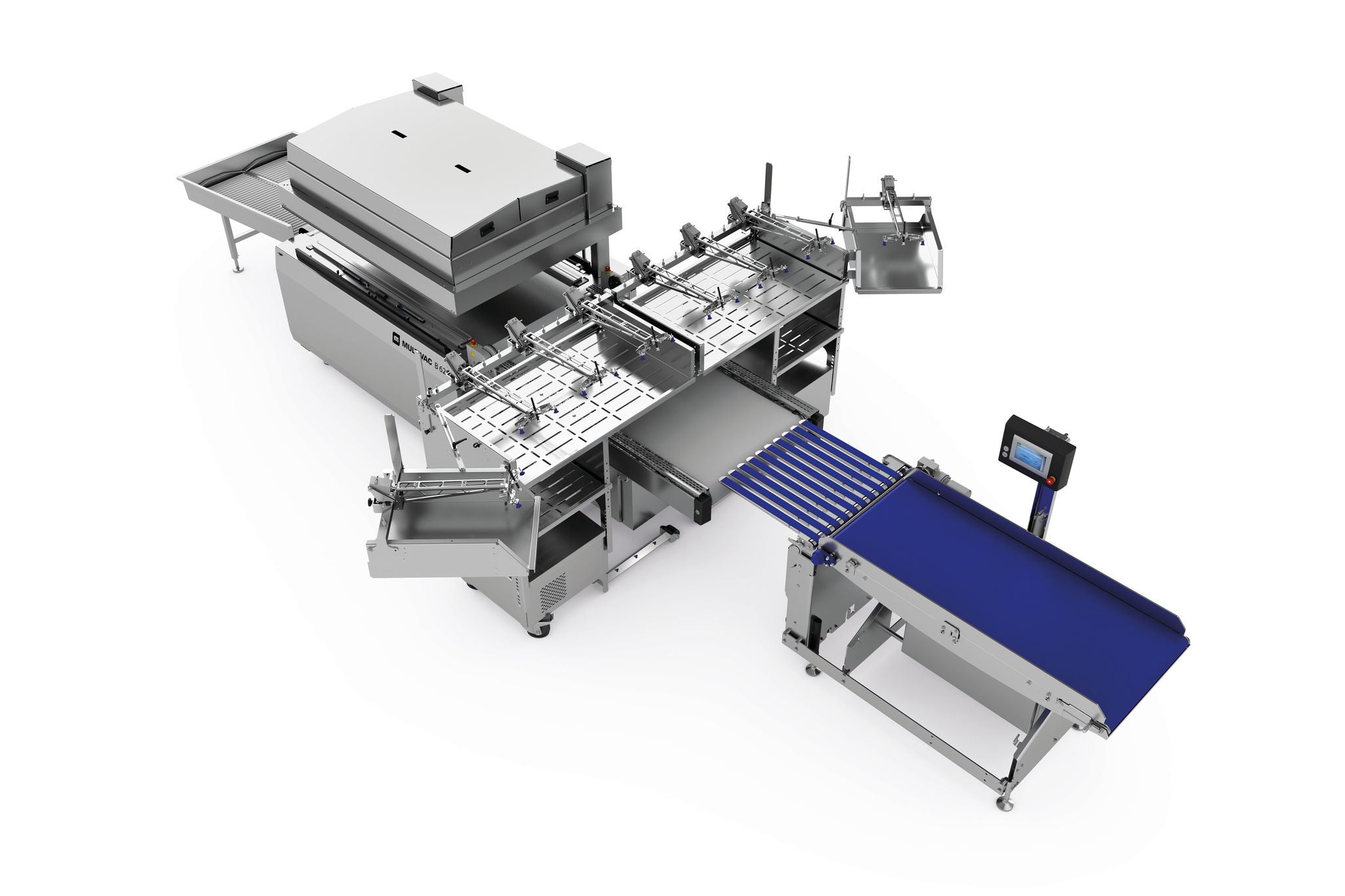
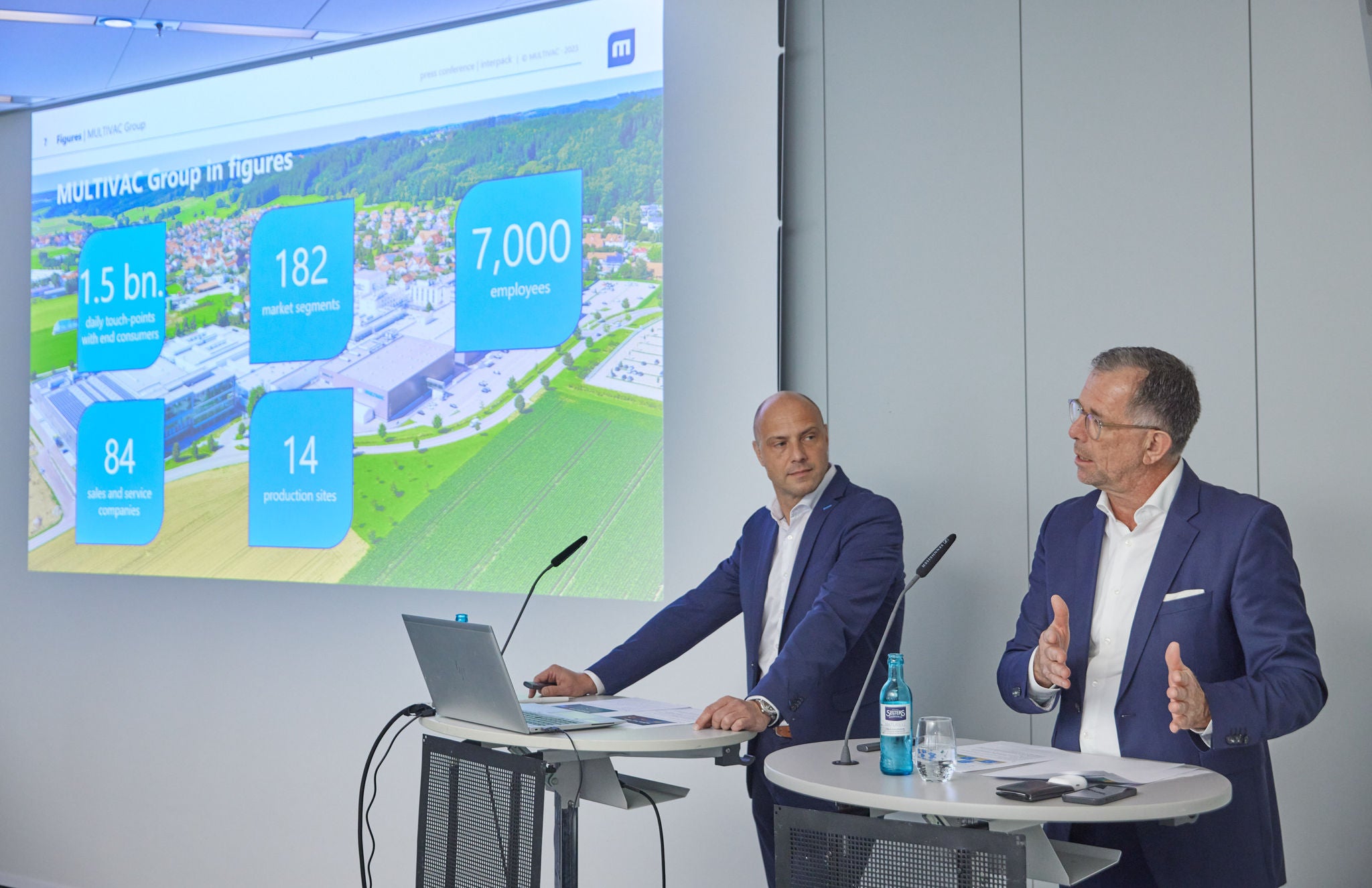
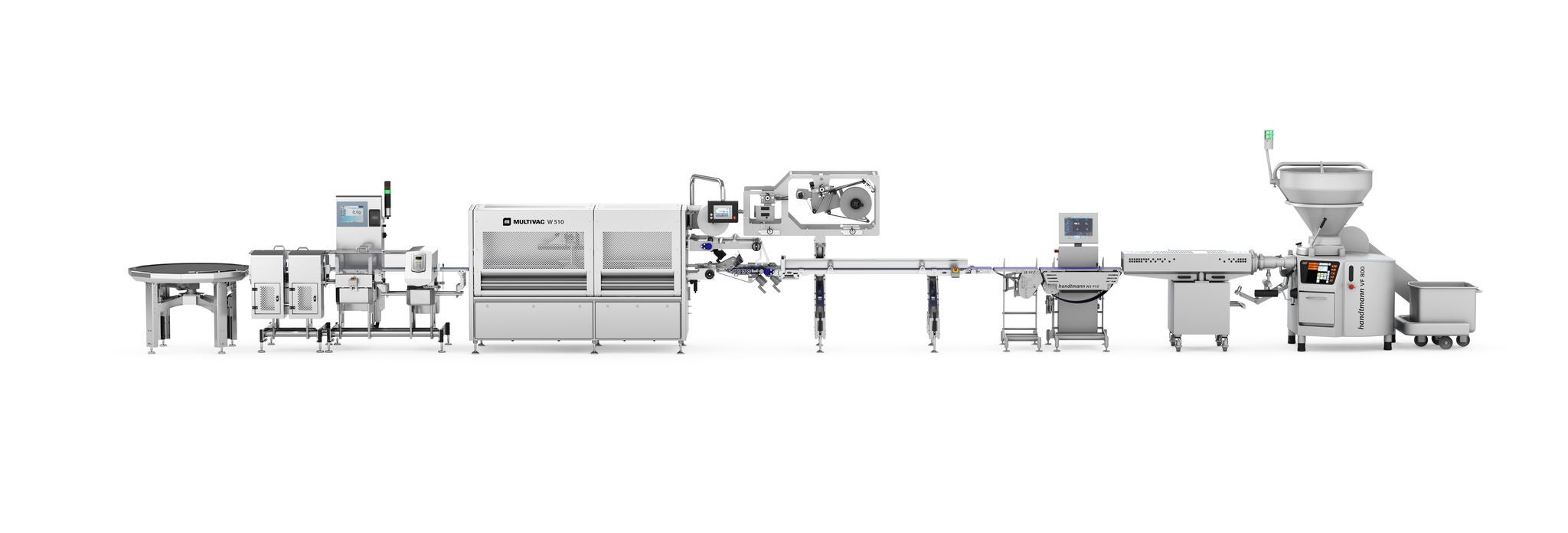
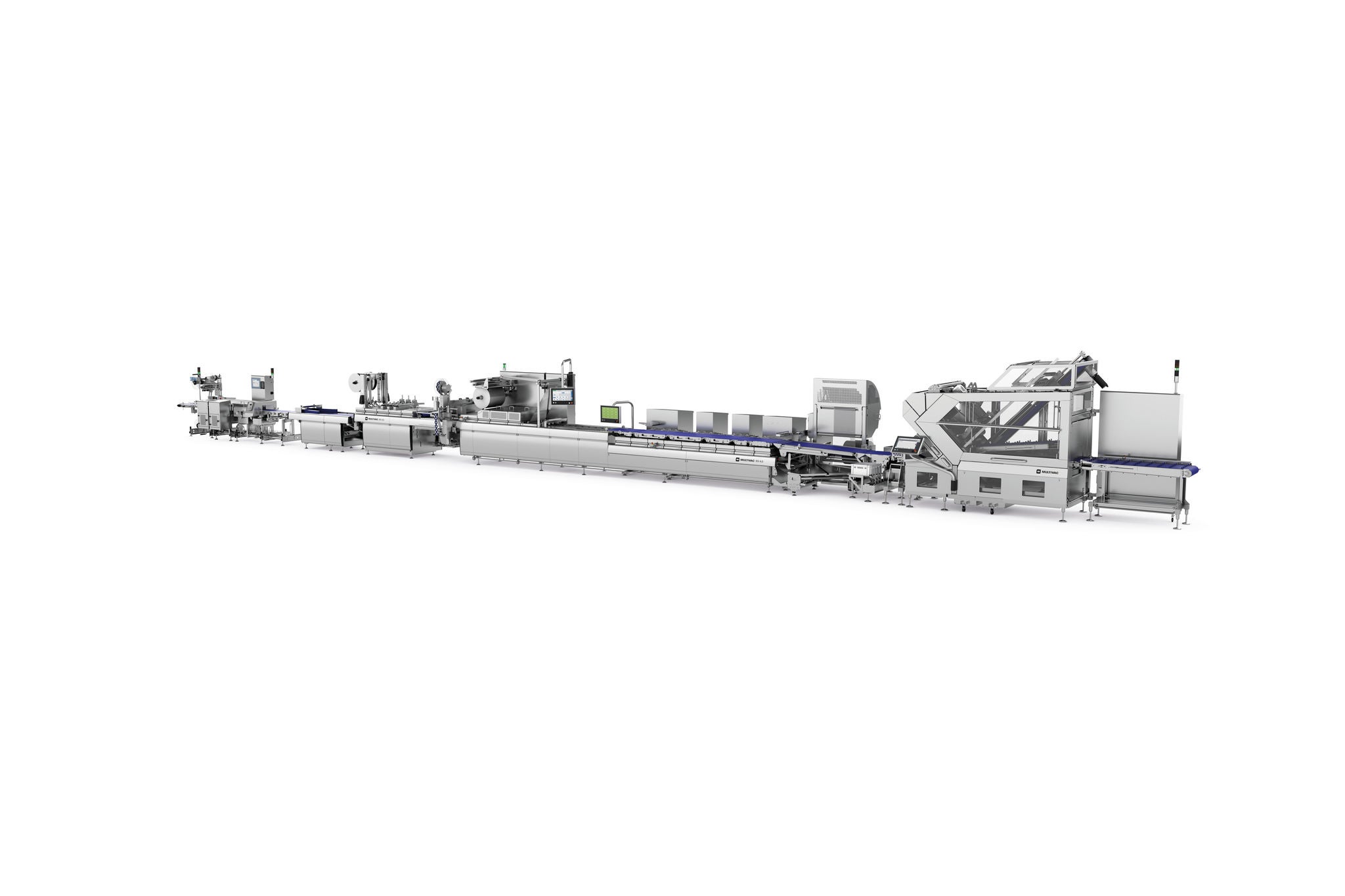
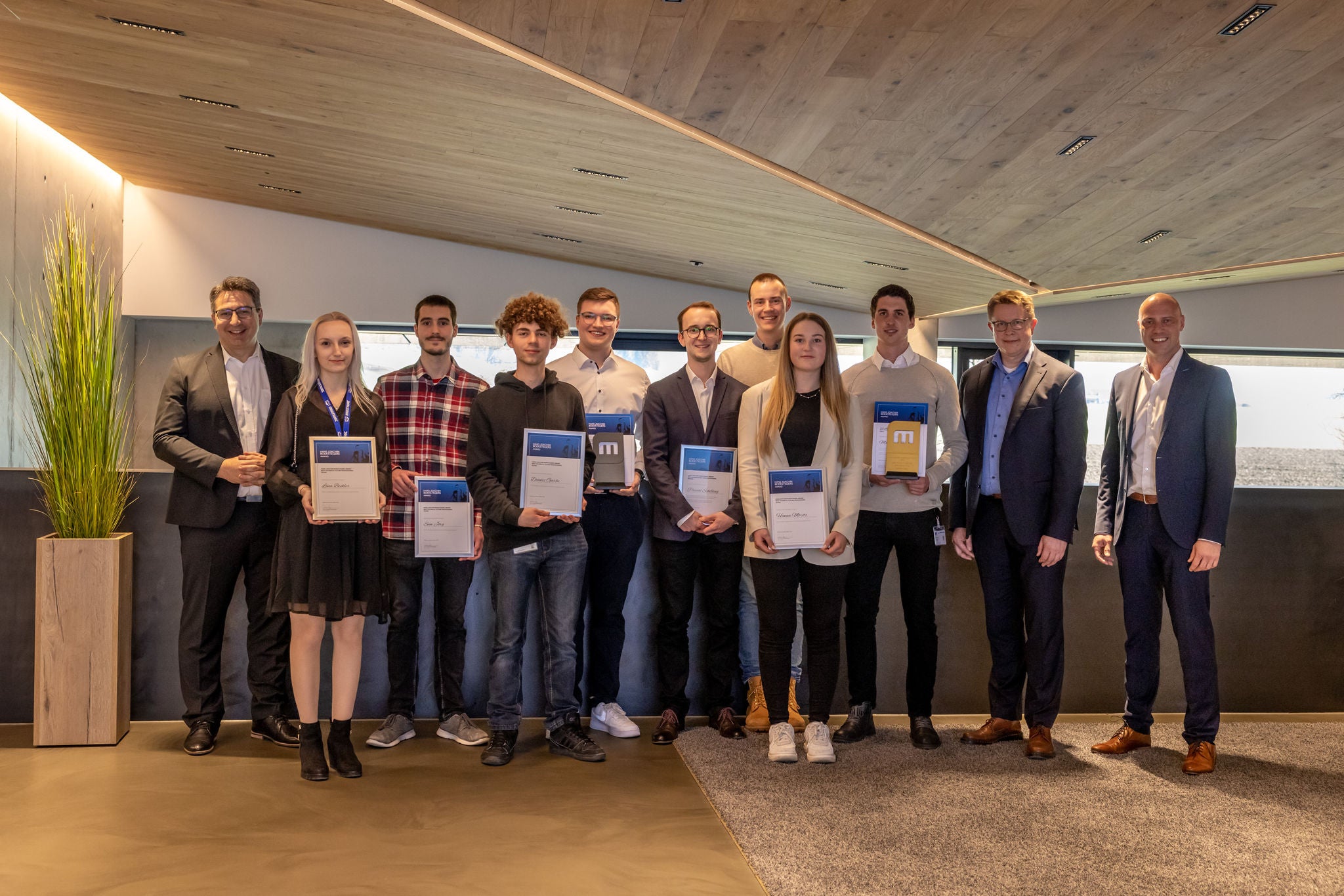
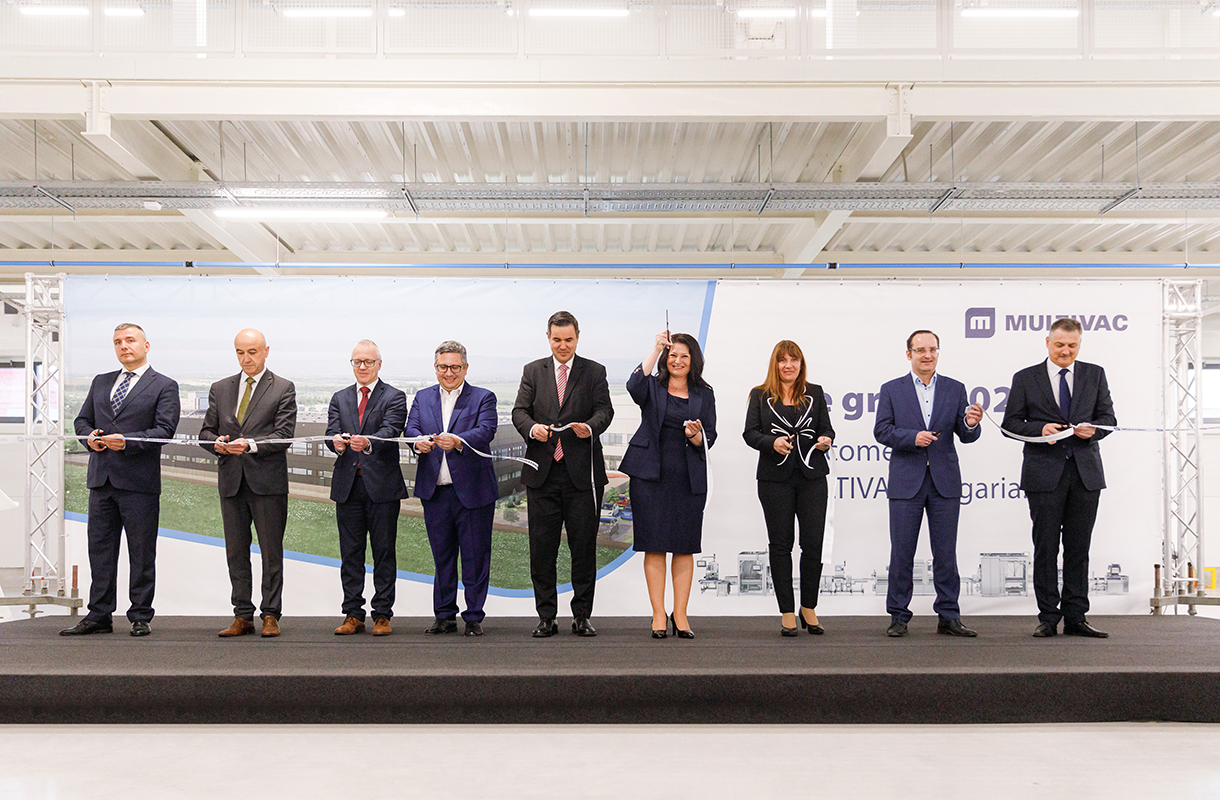
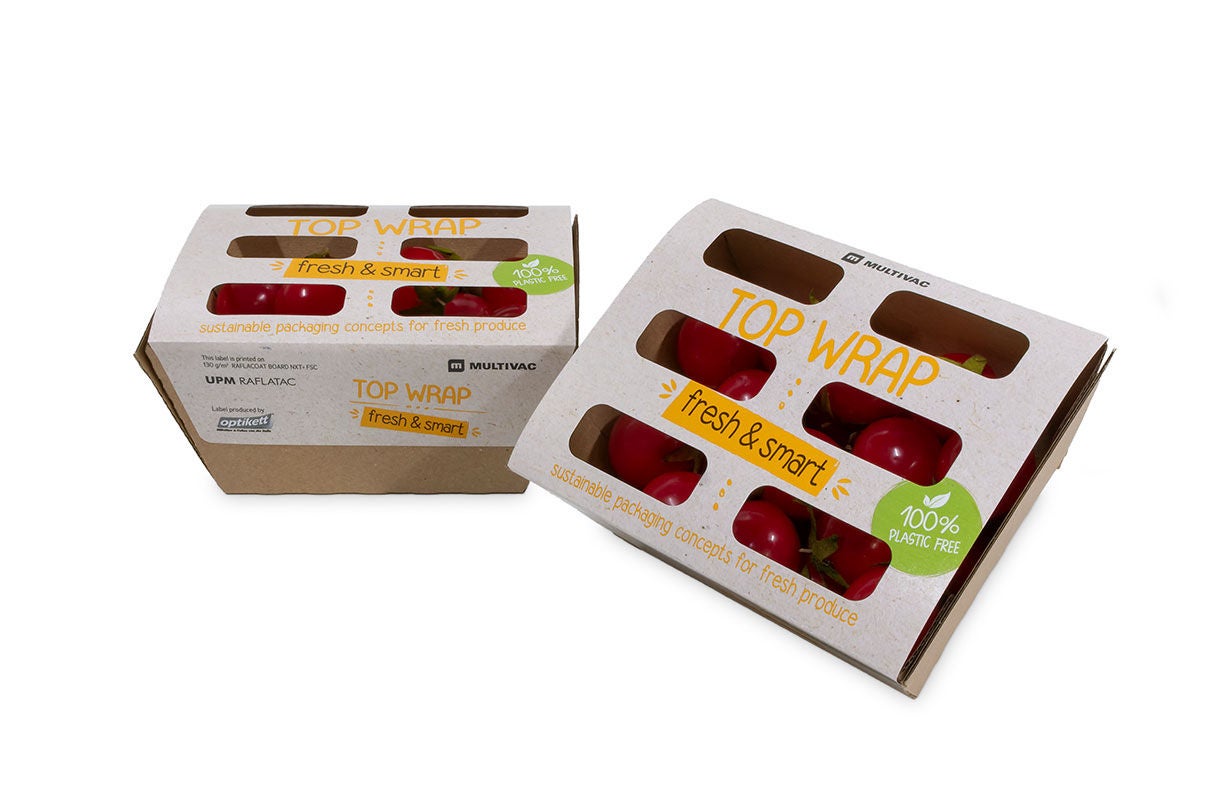
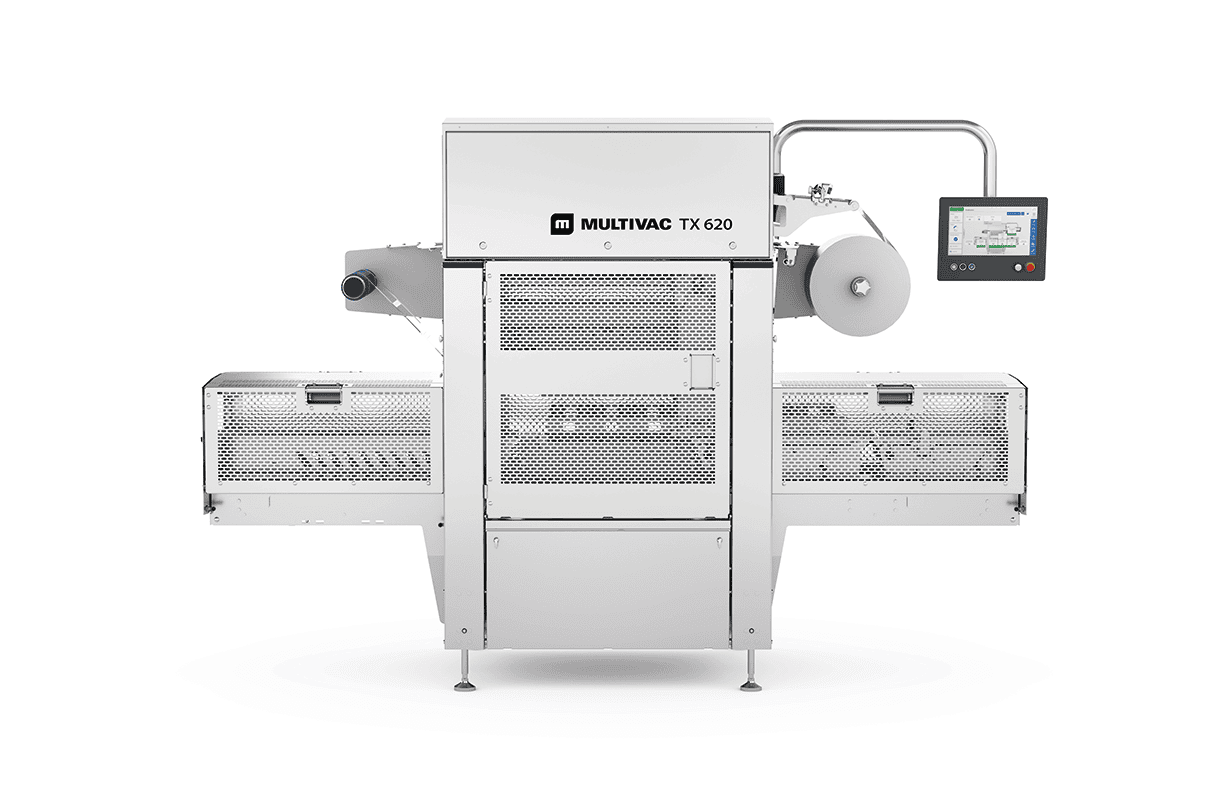
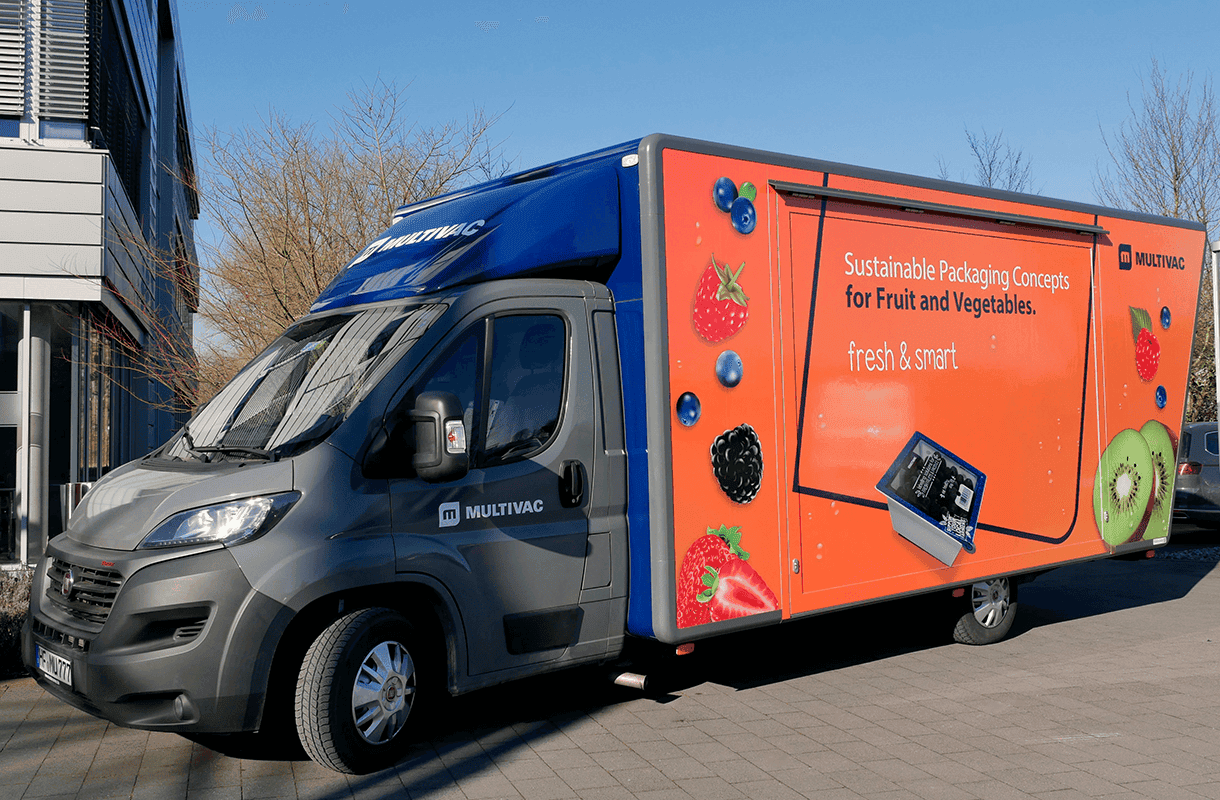
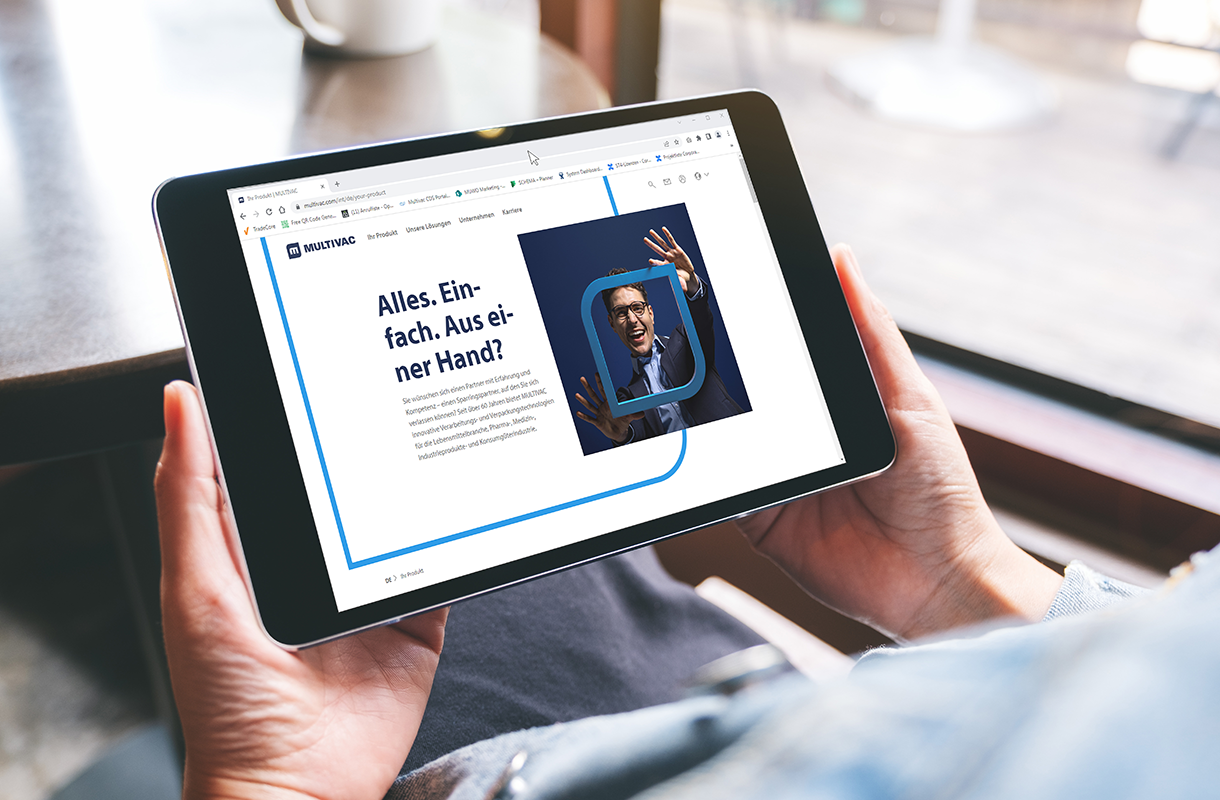
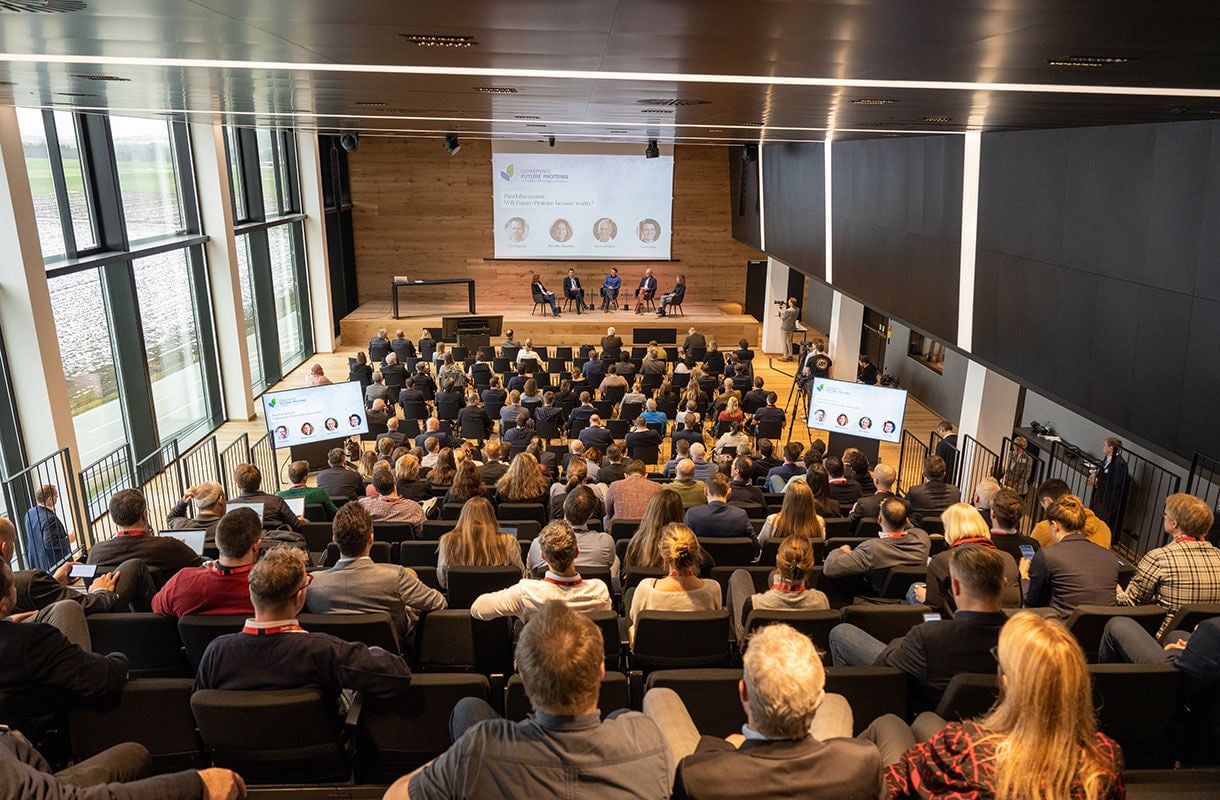
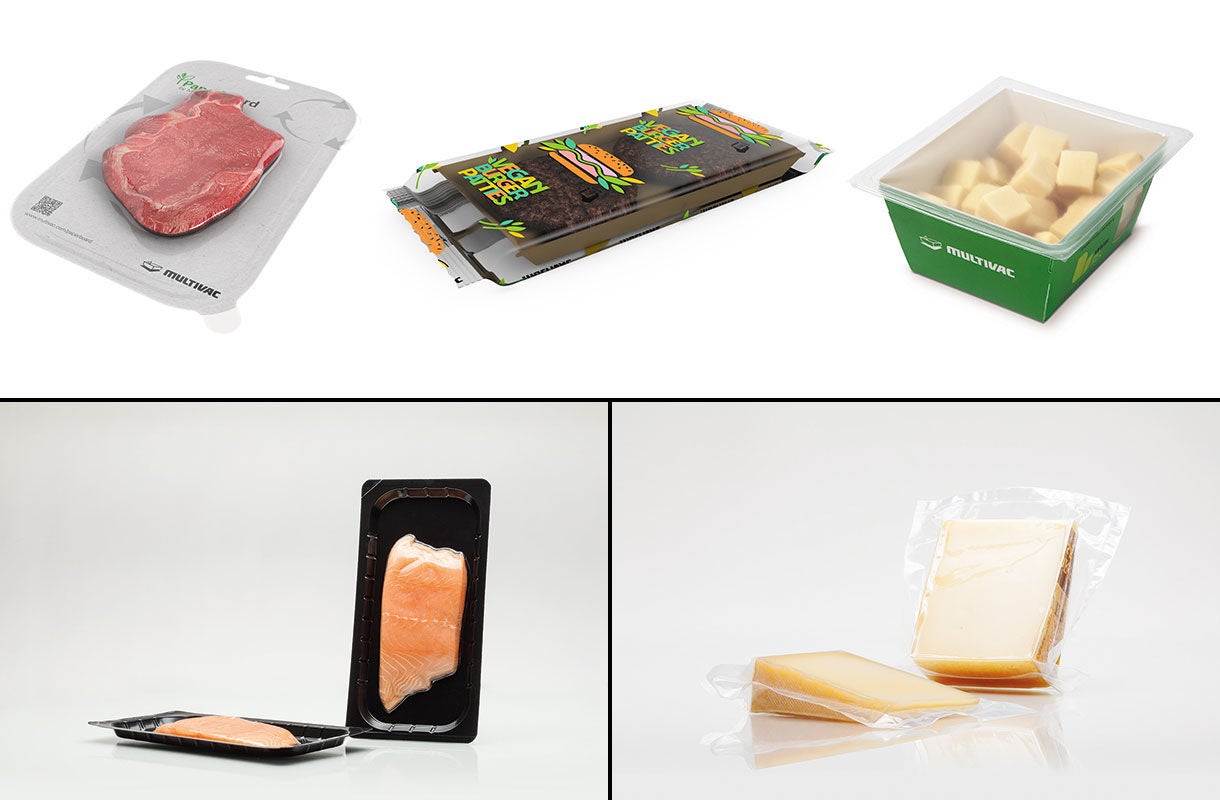
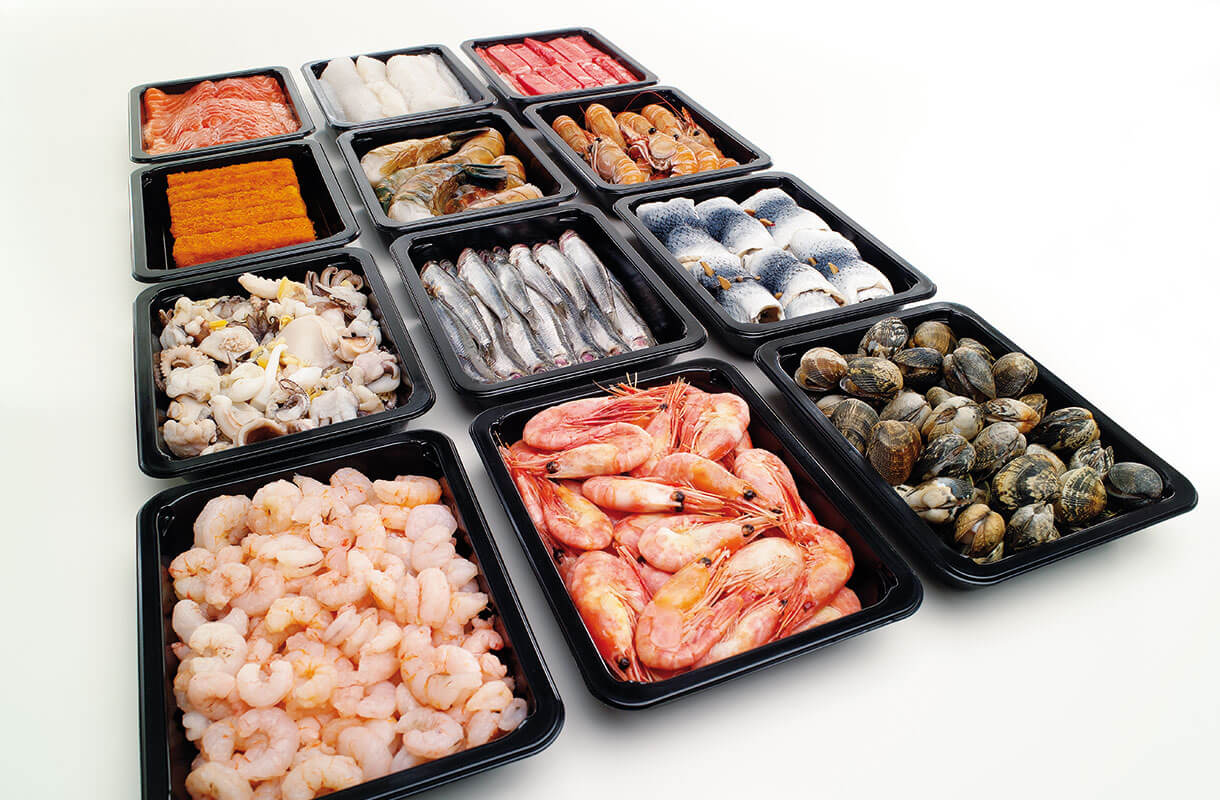
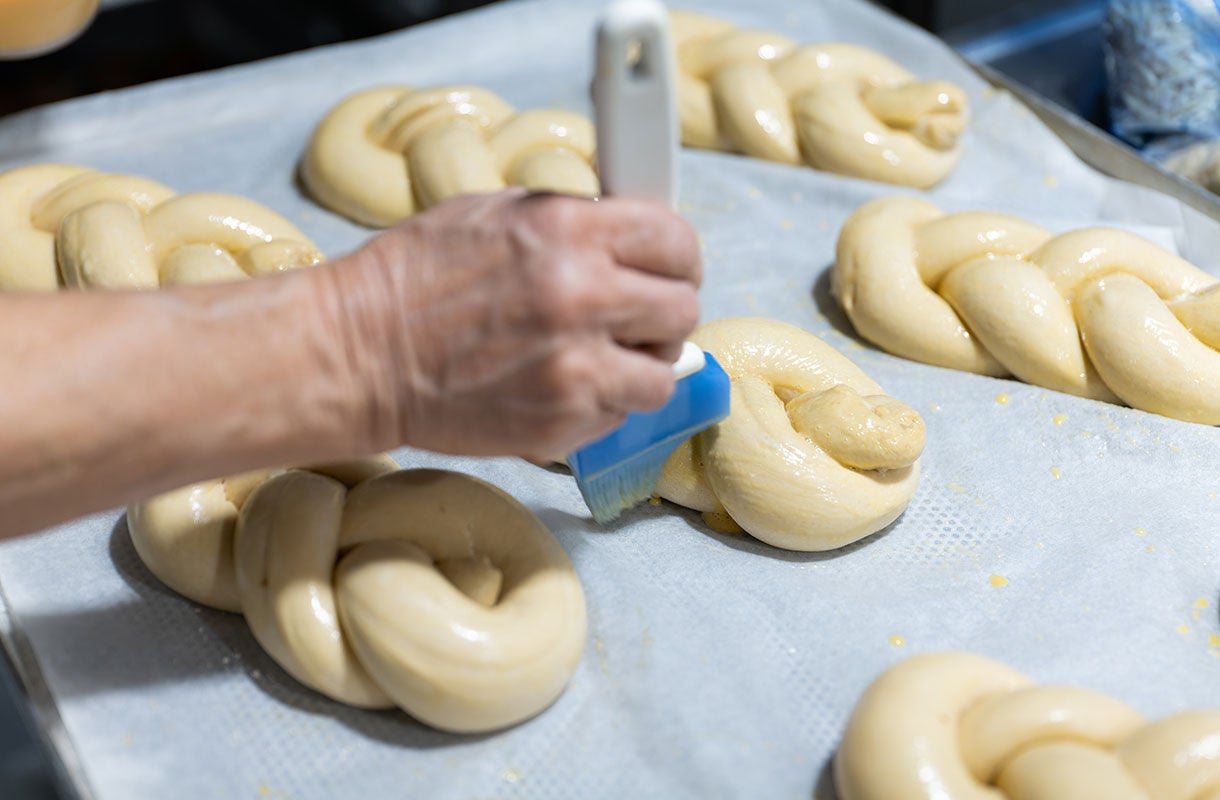
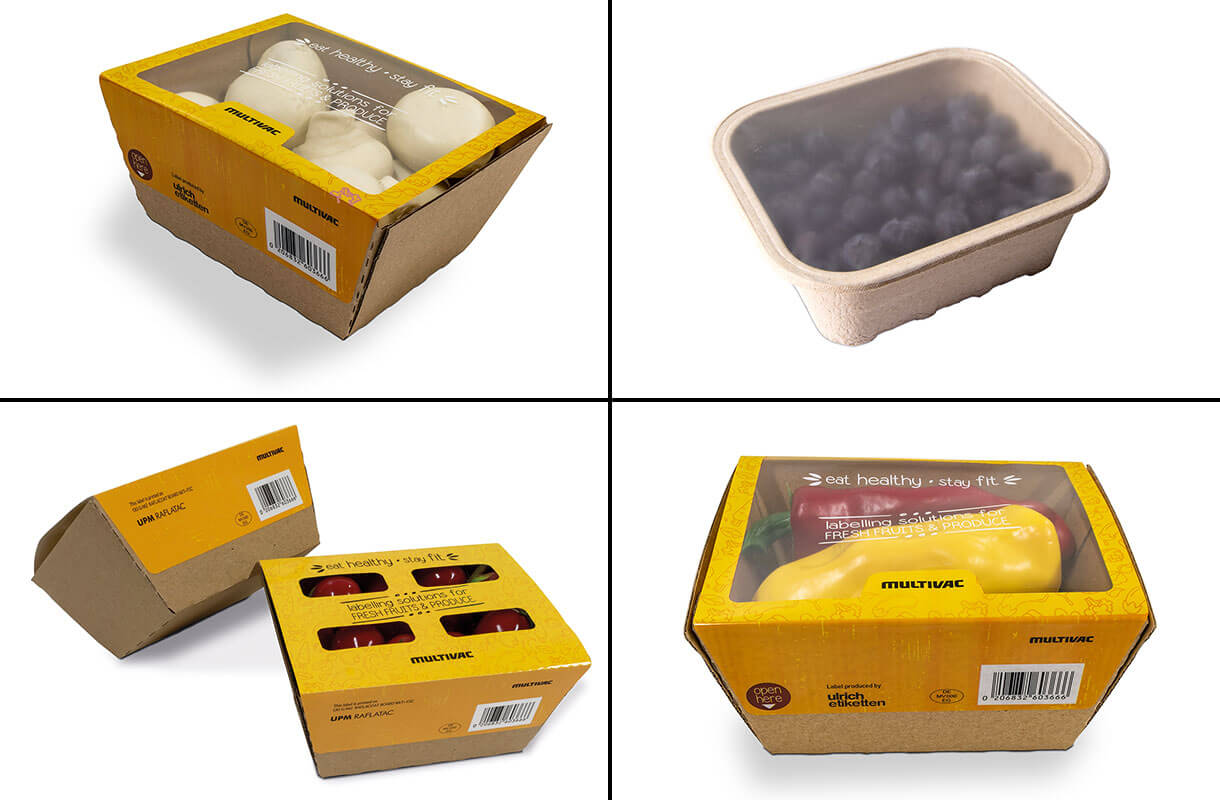
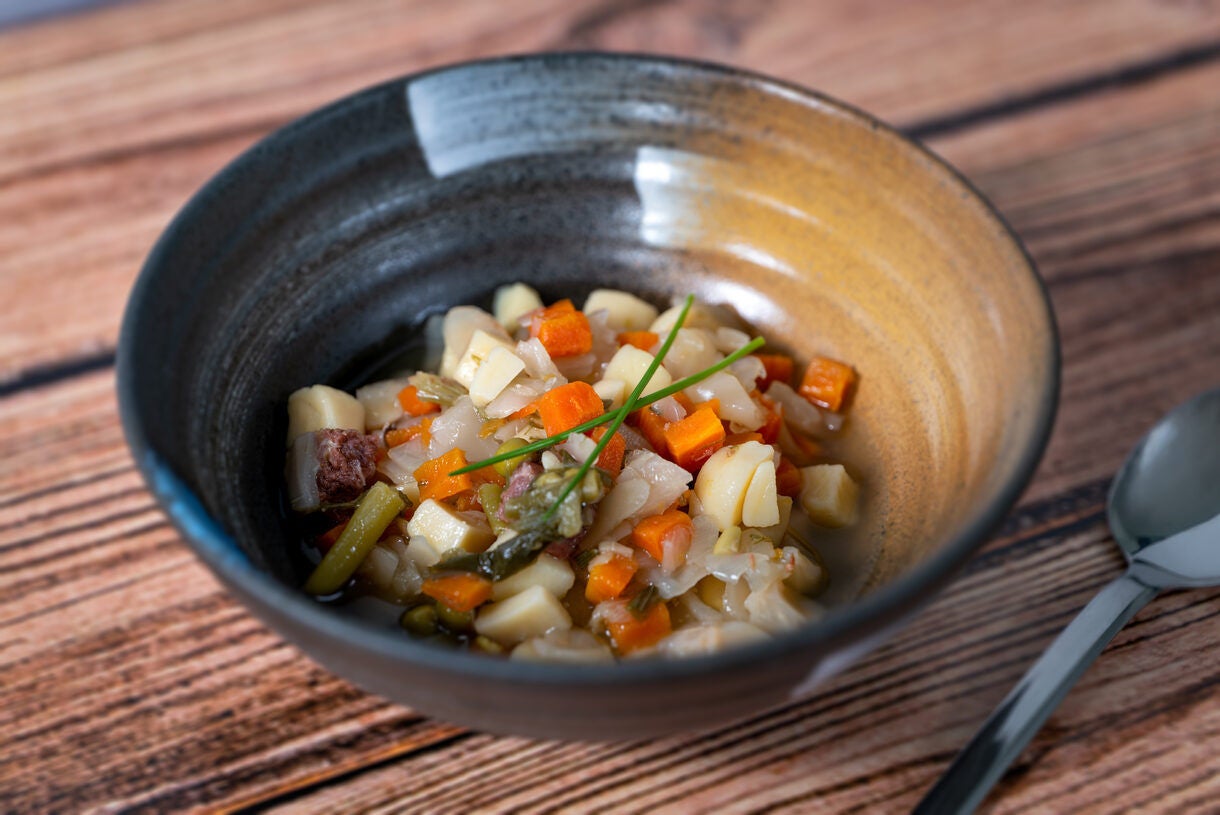
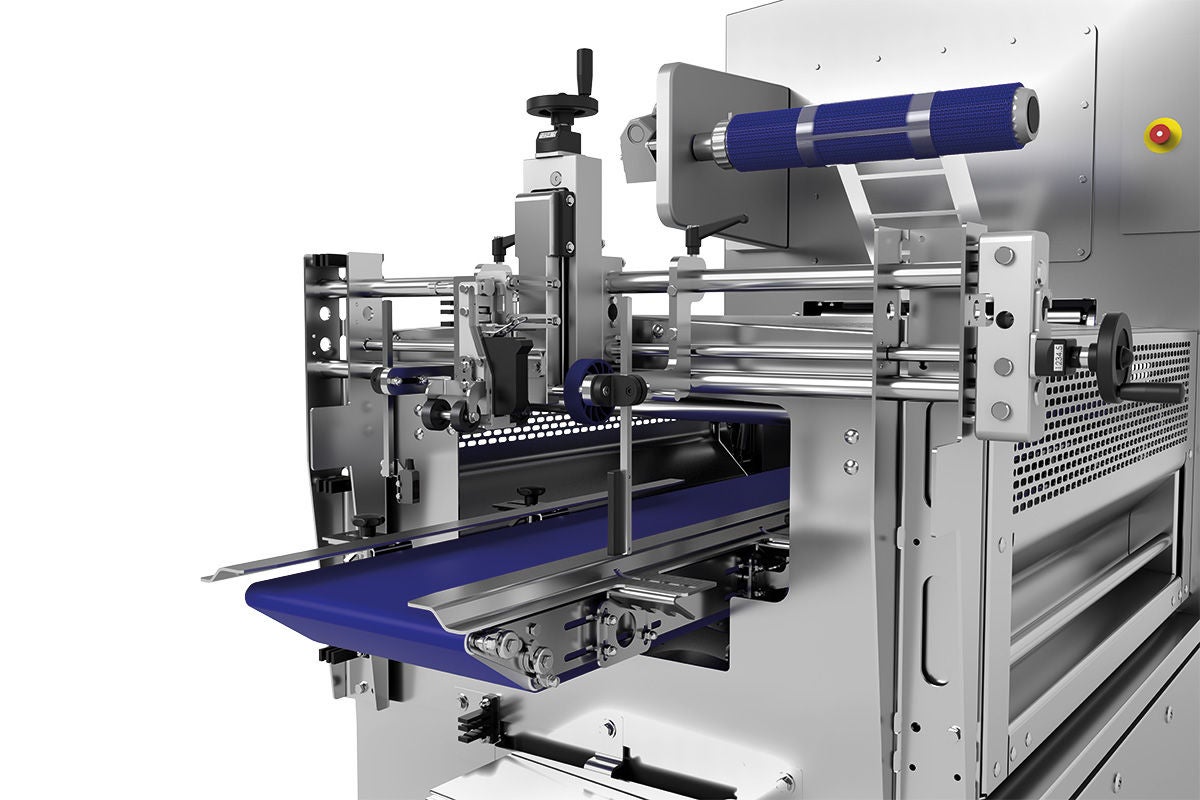
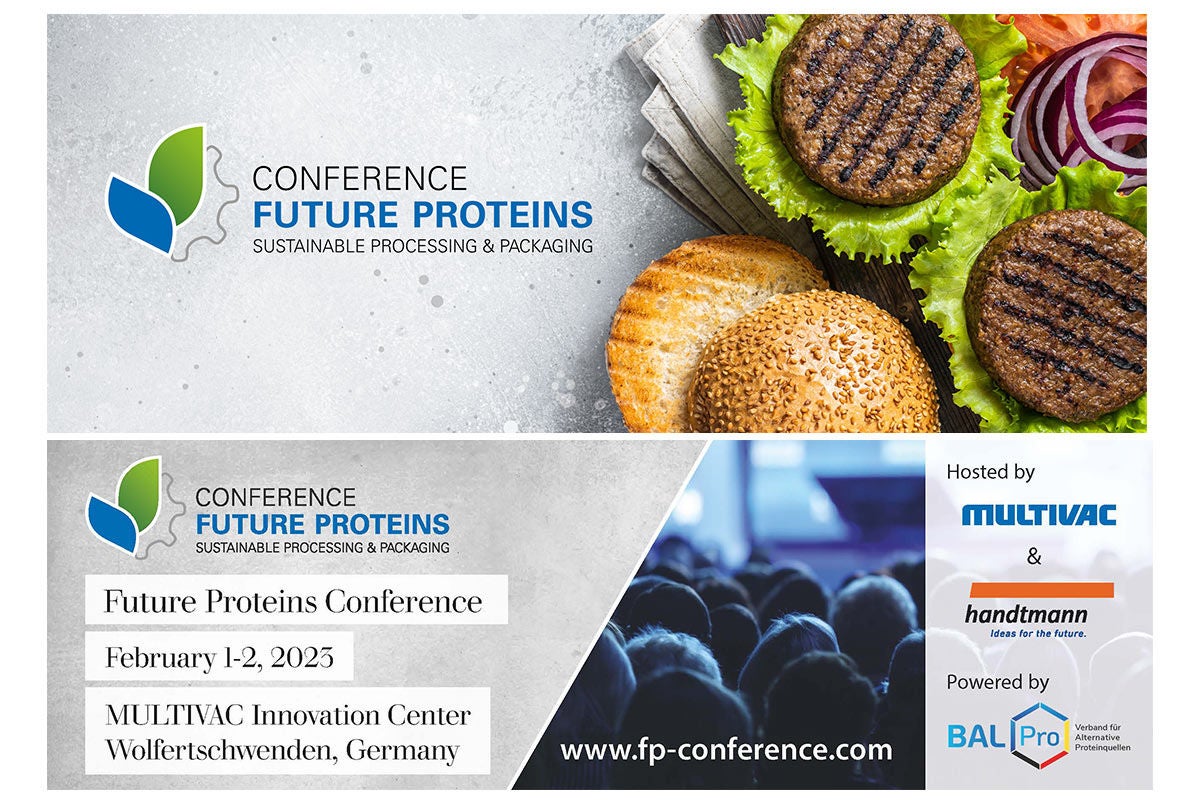
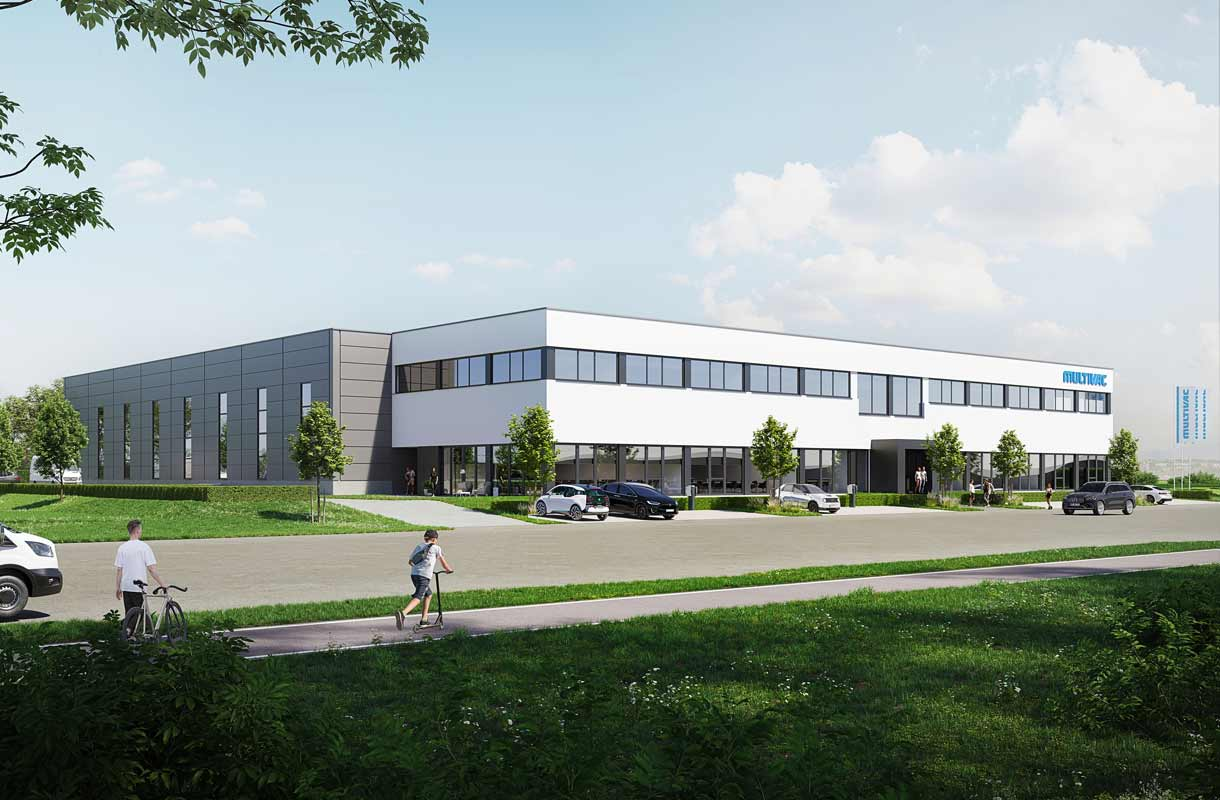
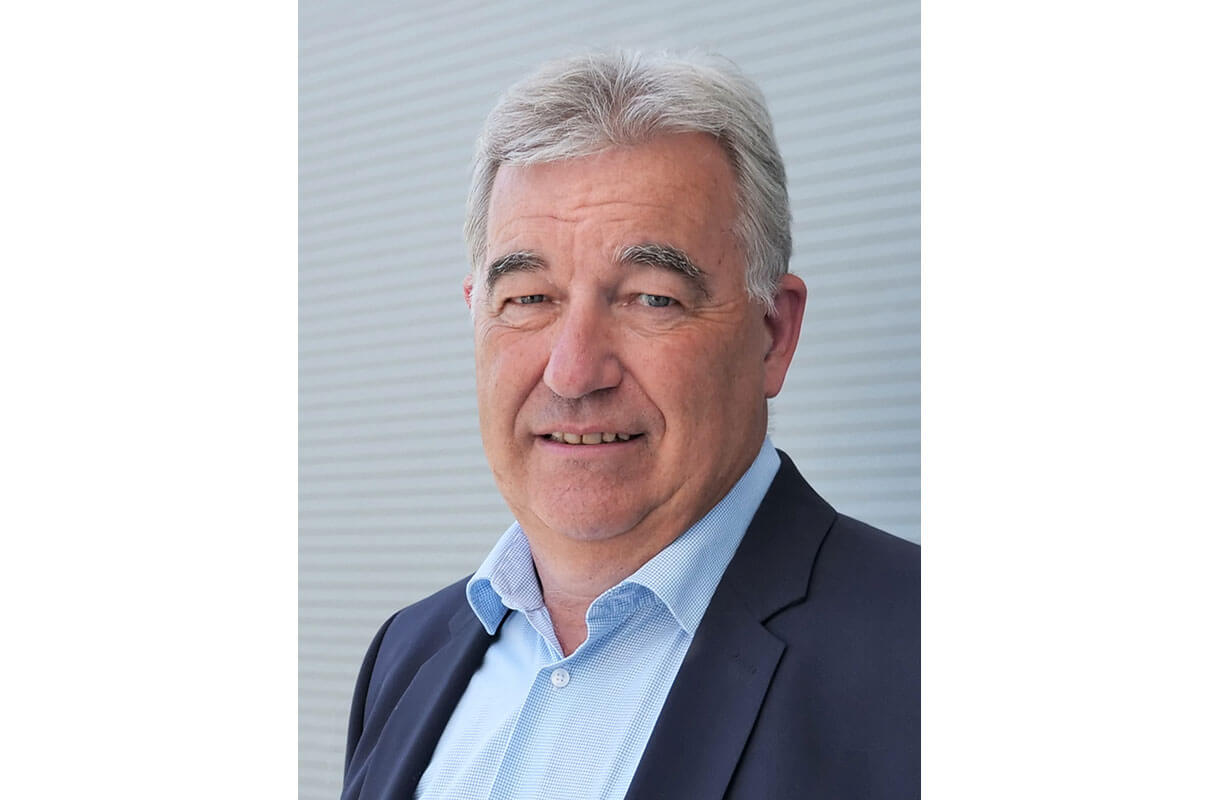
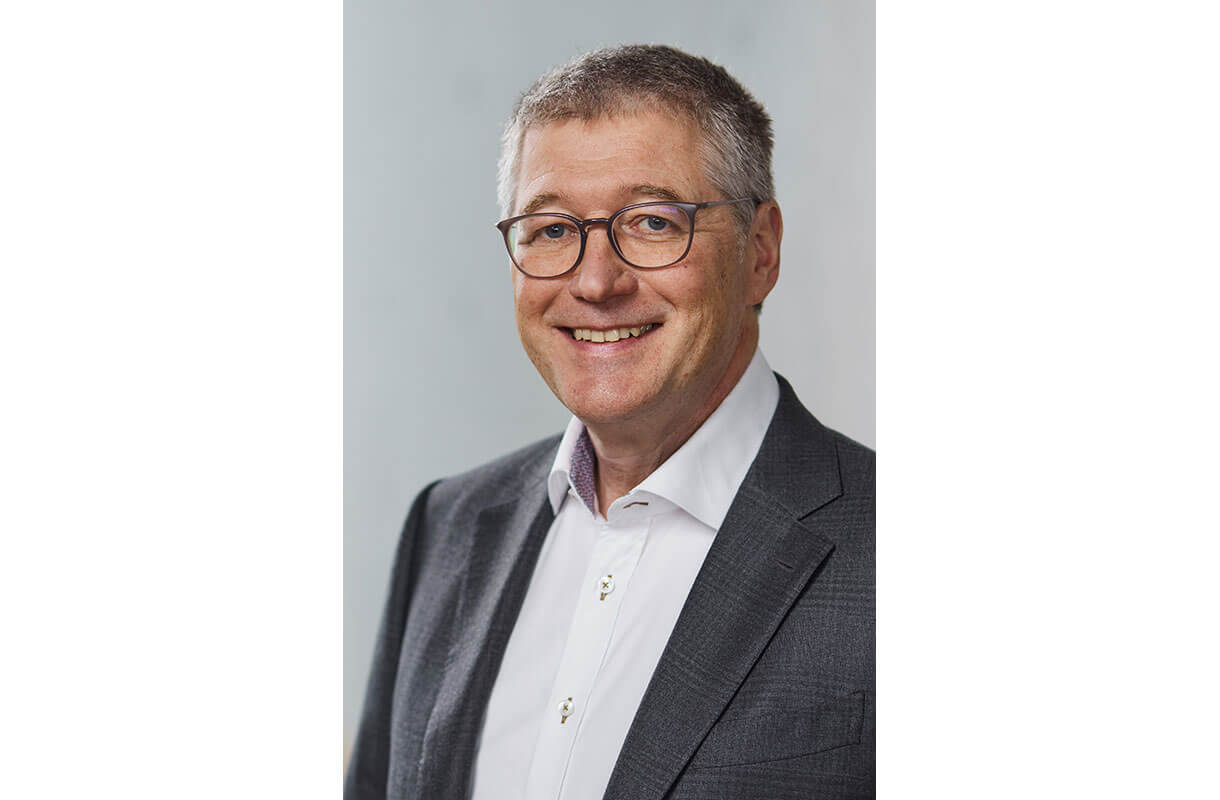
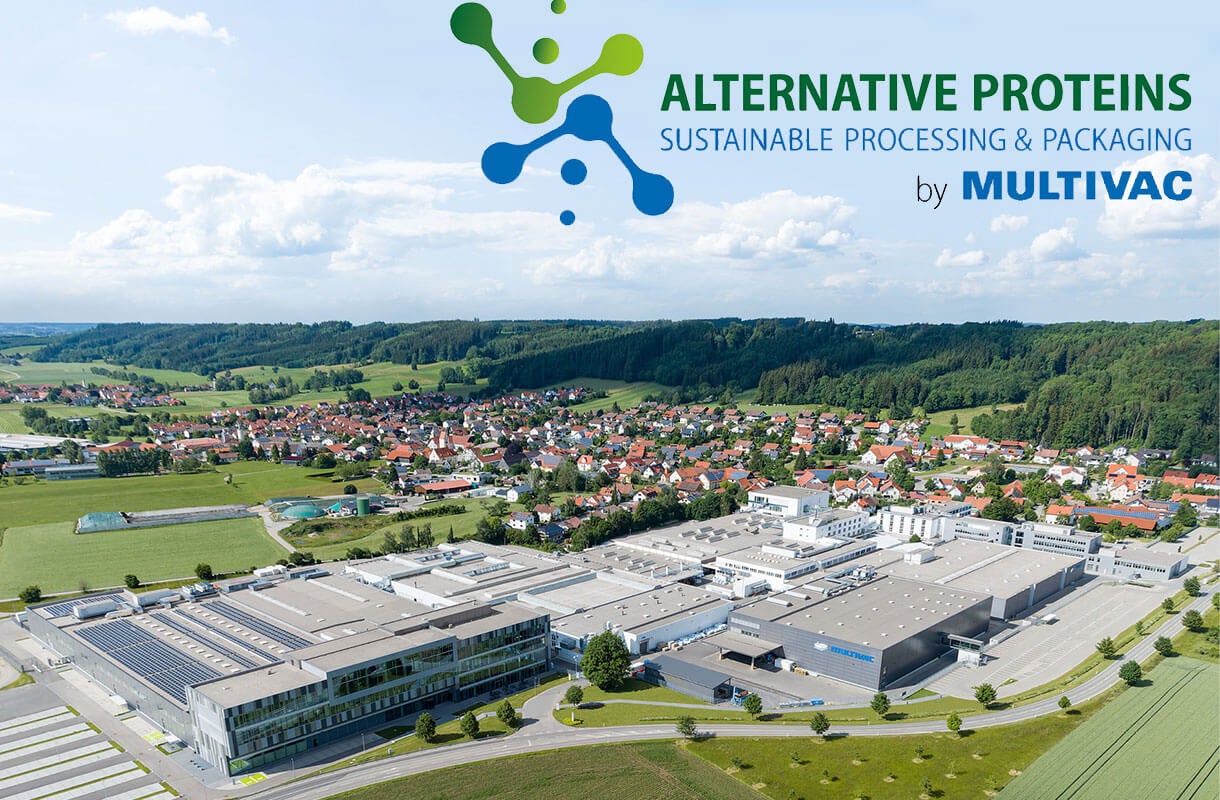
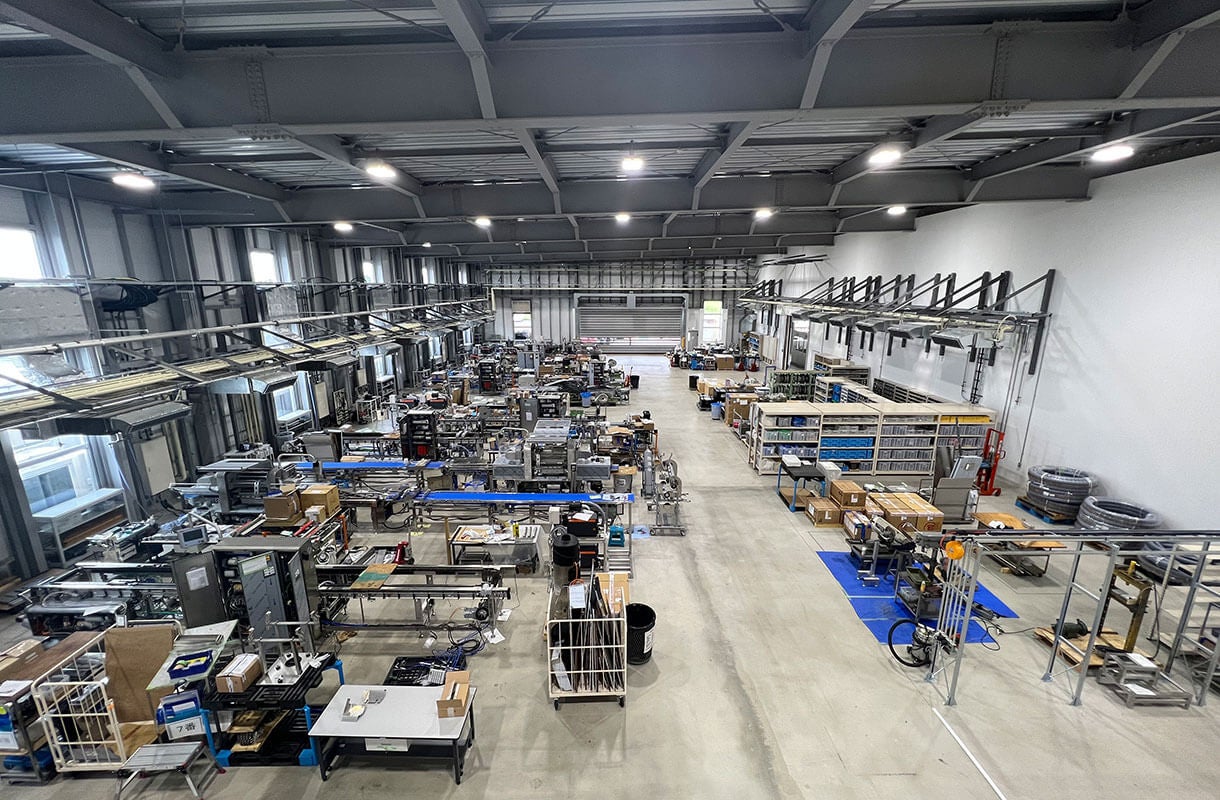

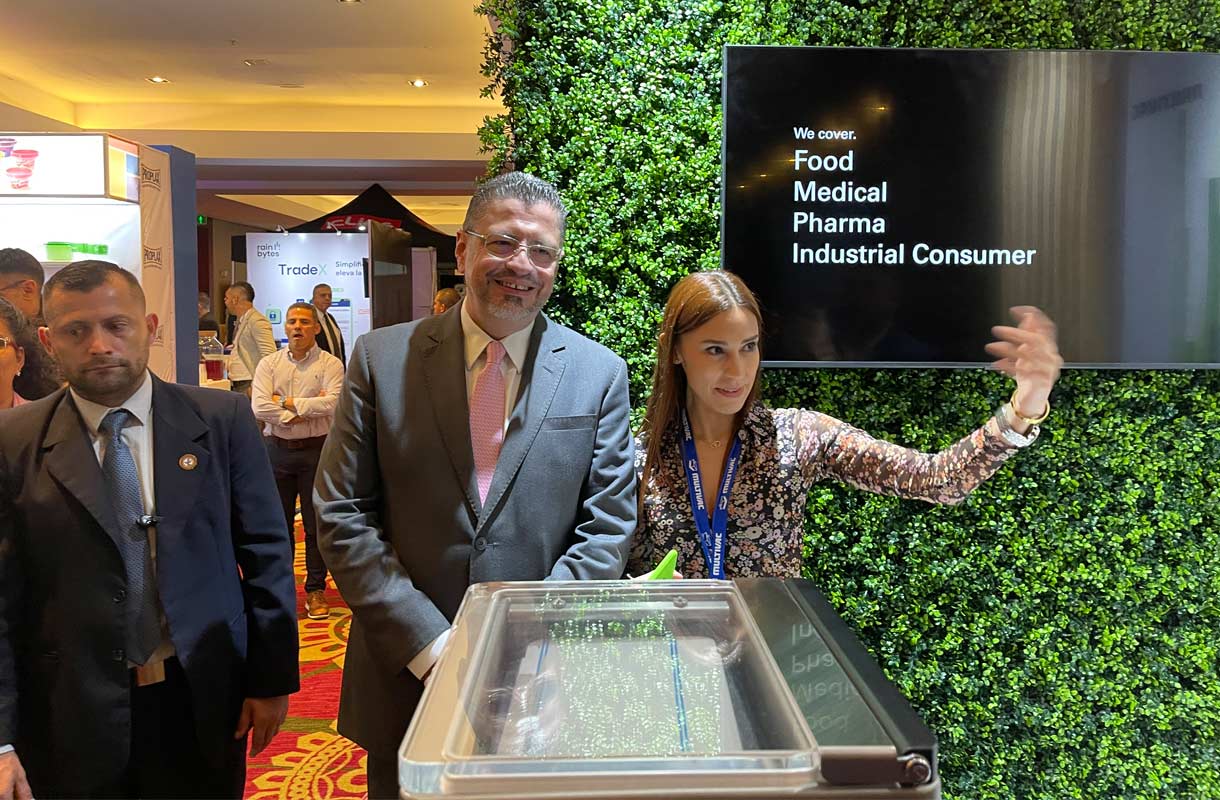
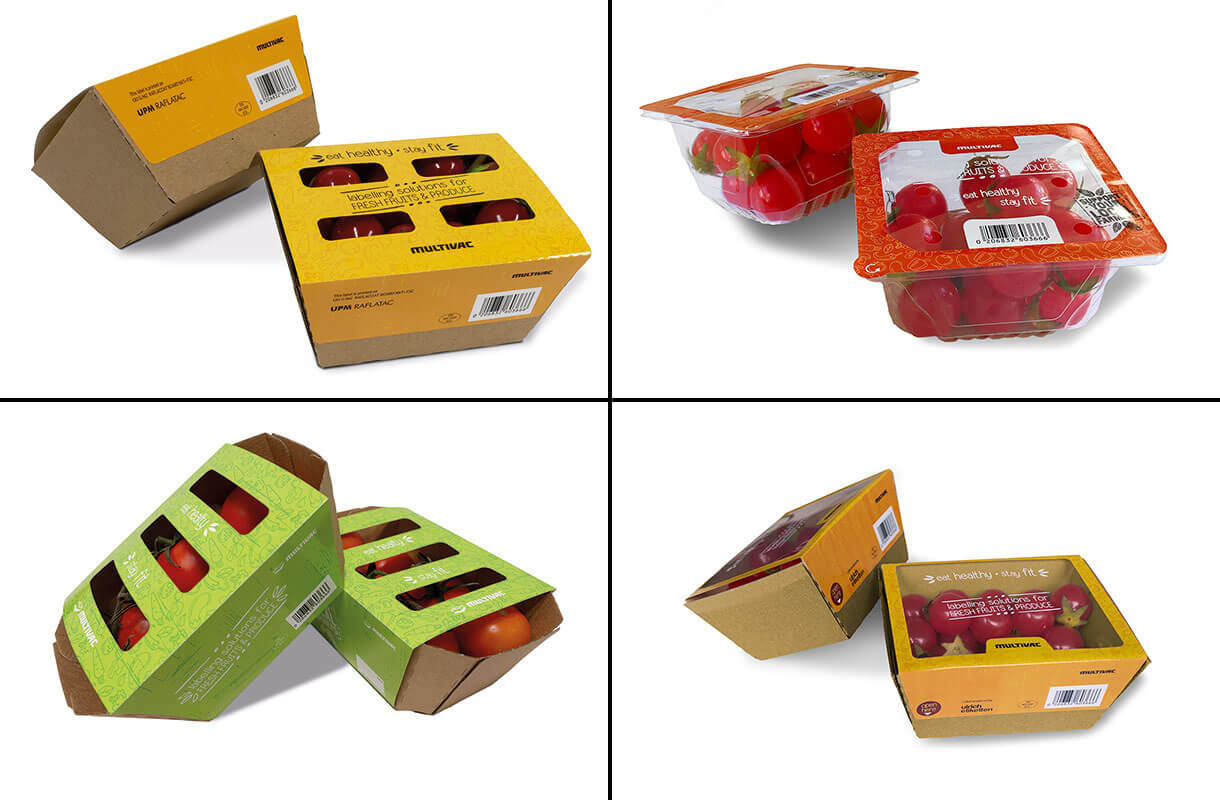
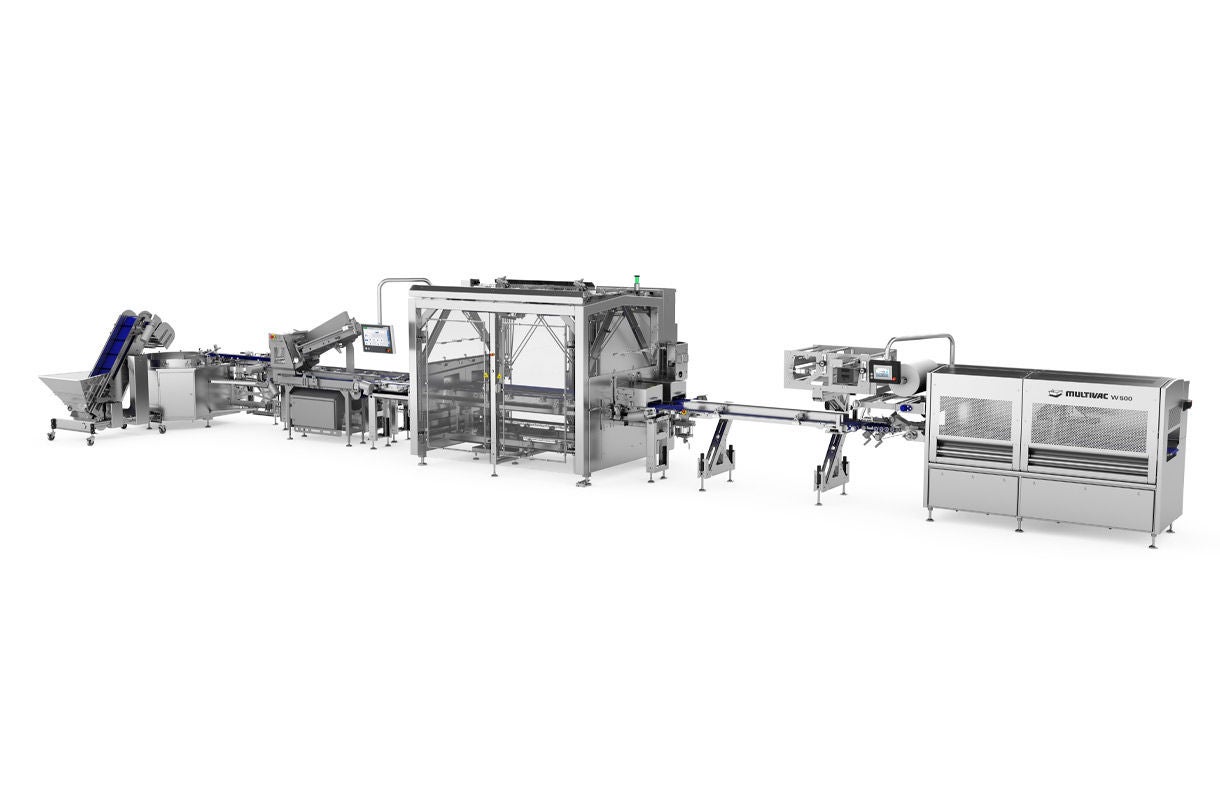
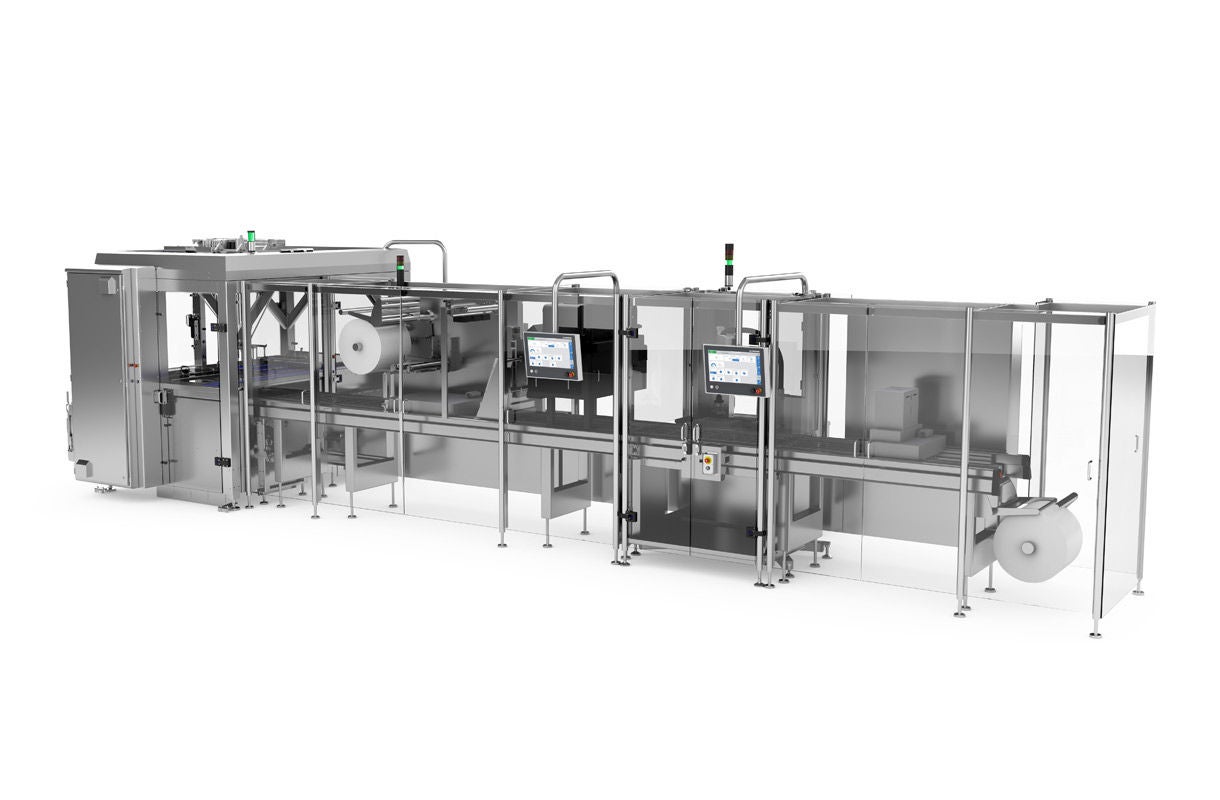
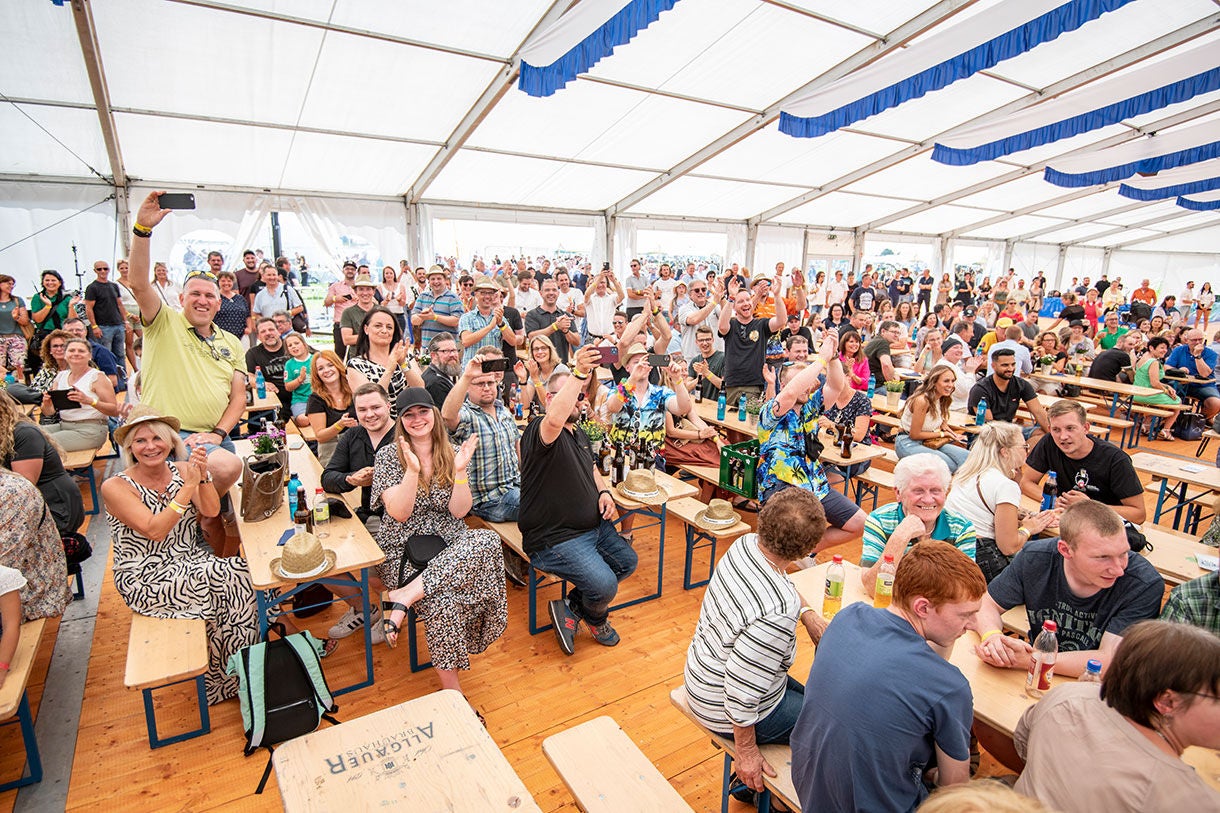
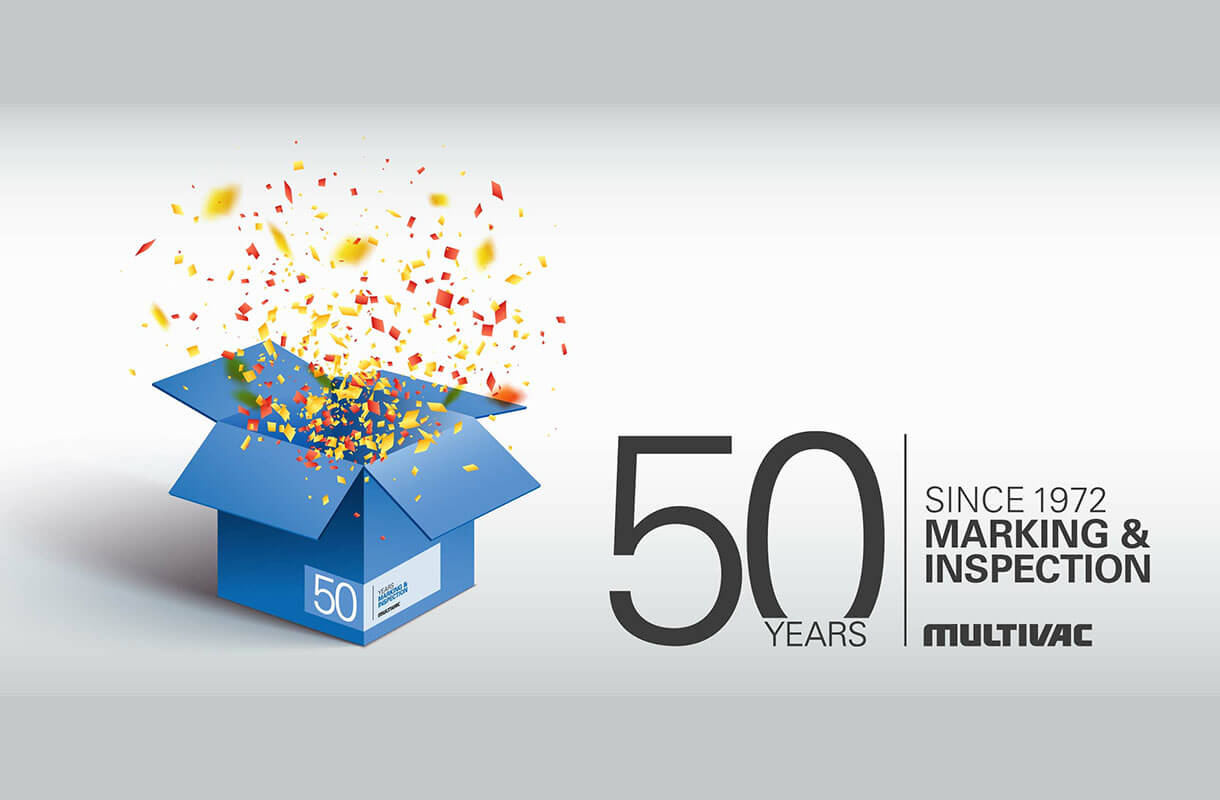
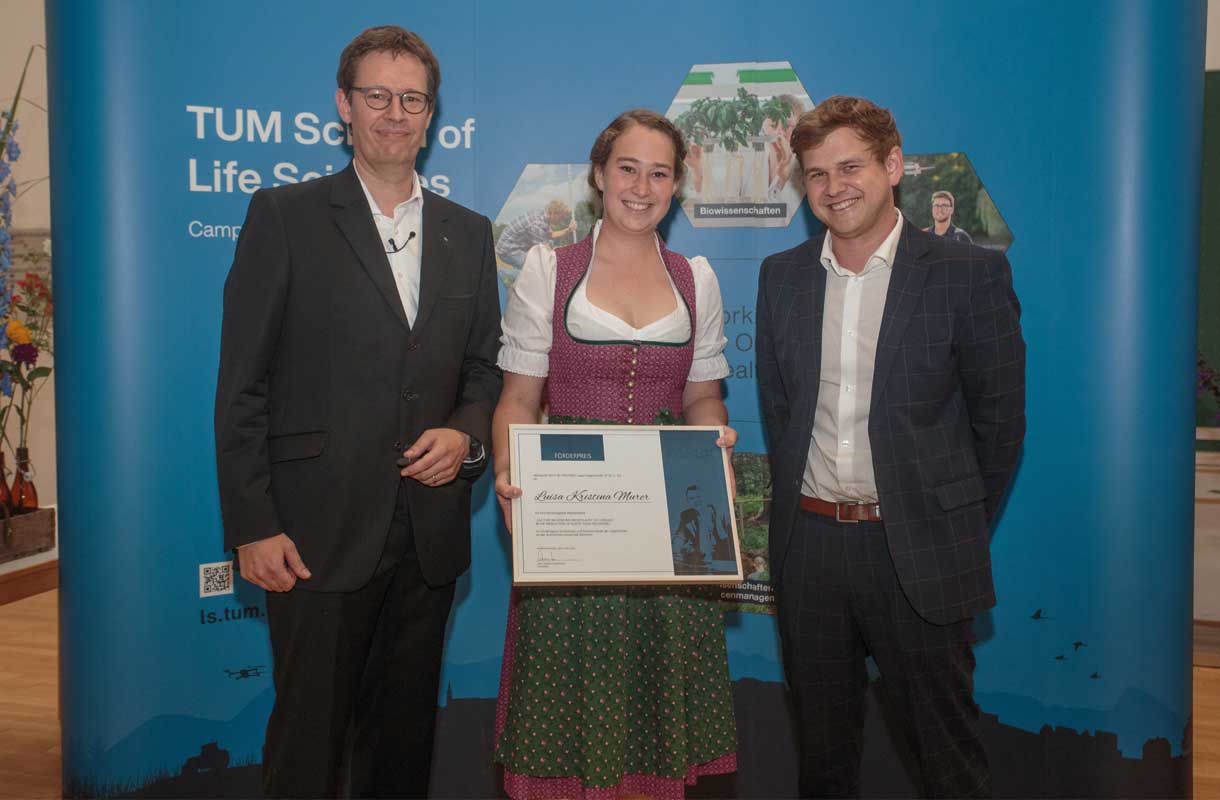
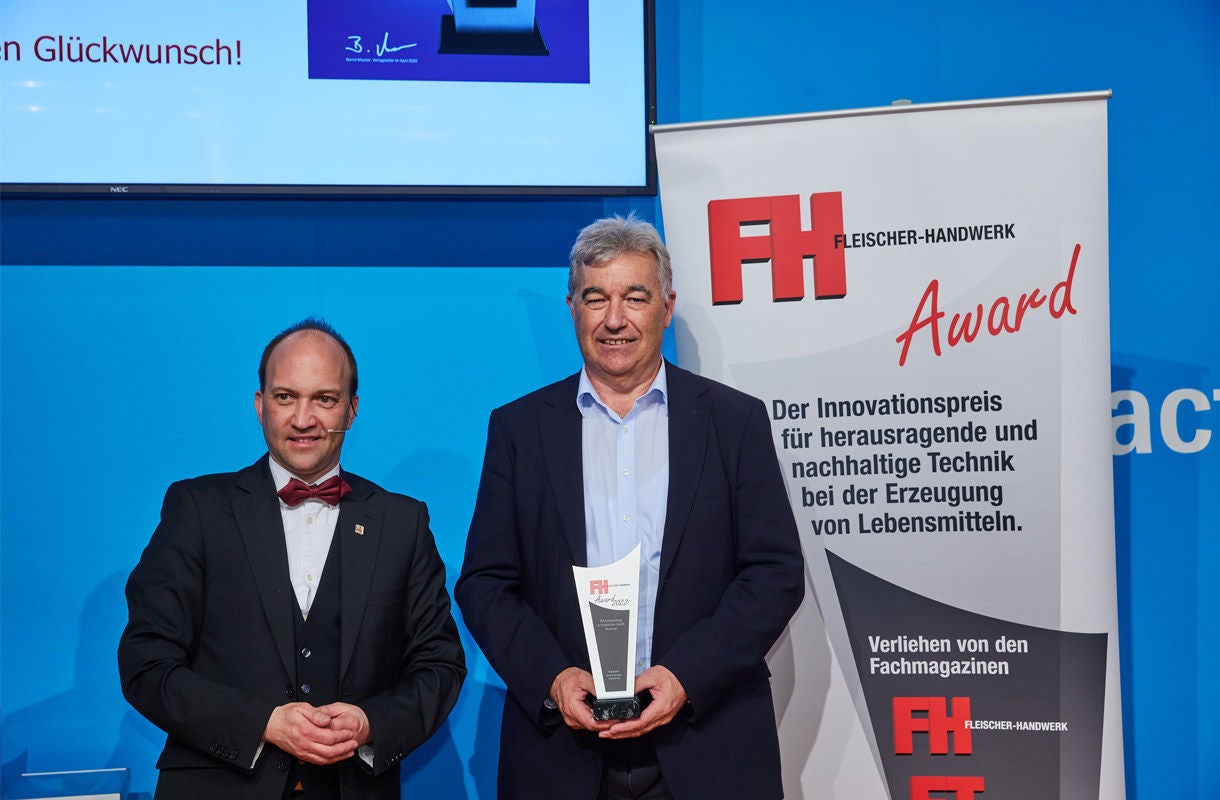

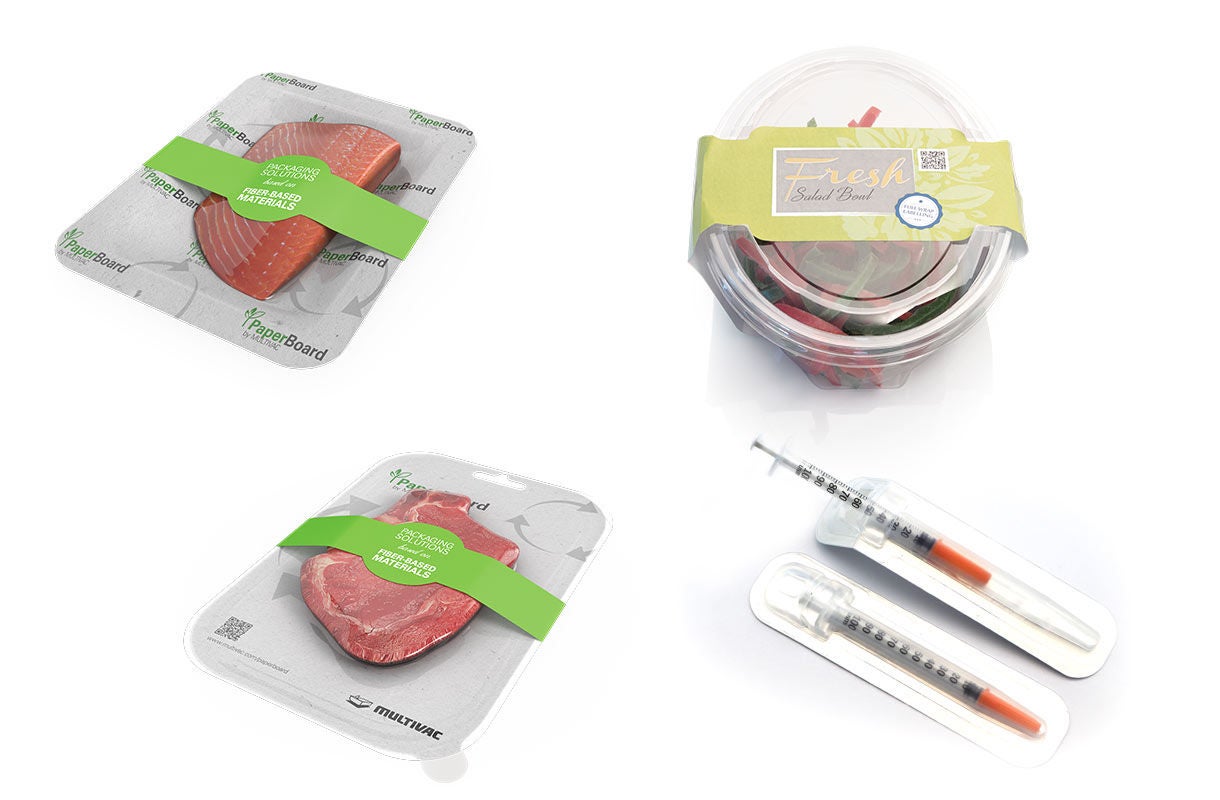
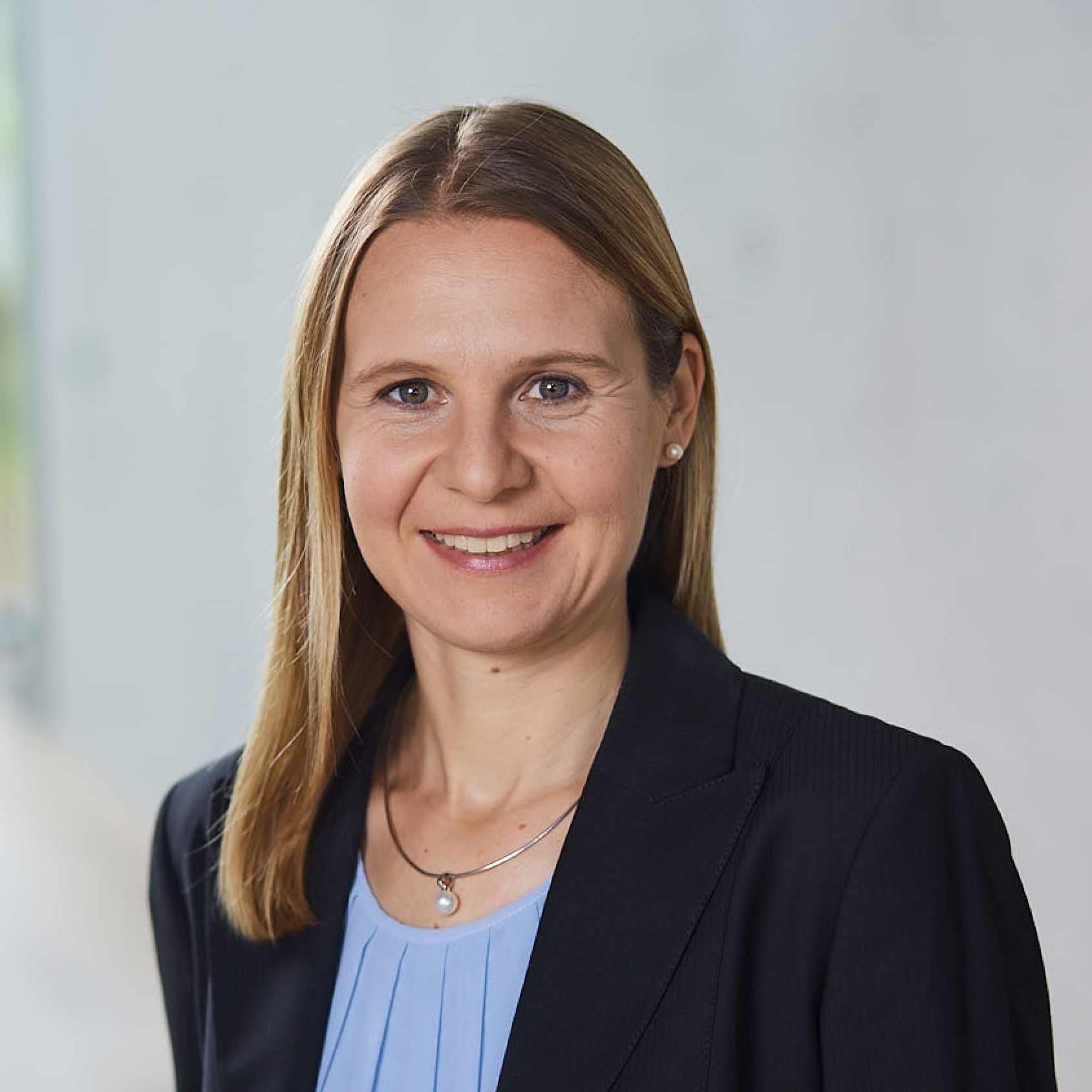
Tanja Böck
Public Relations Manager
Tel: +49 8334 601-0
Mail: press@multivac-group.com