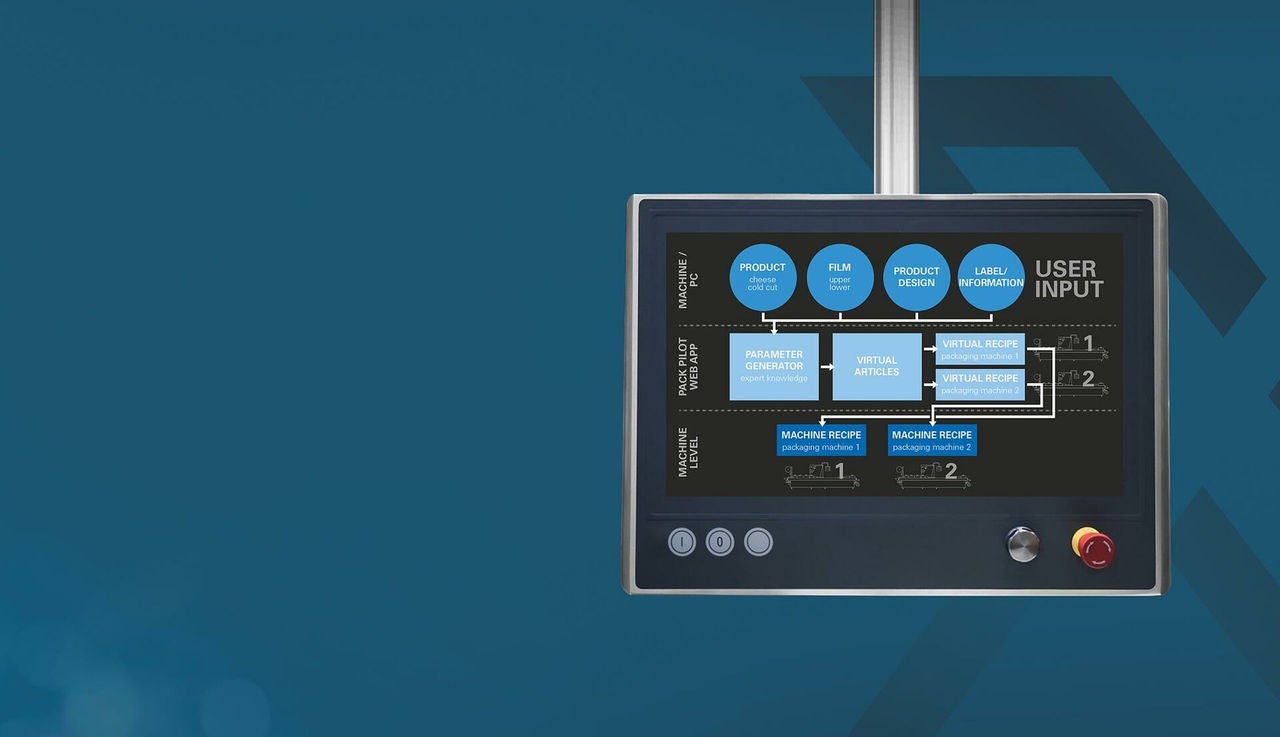
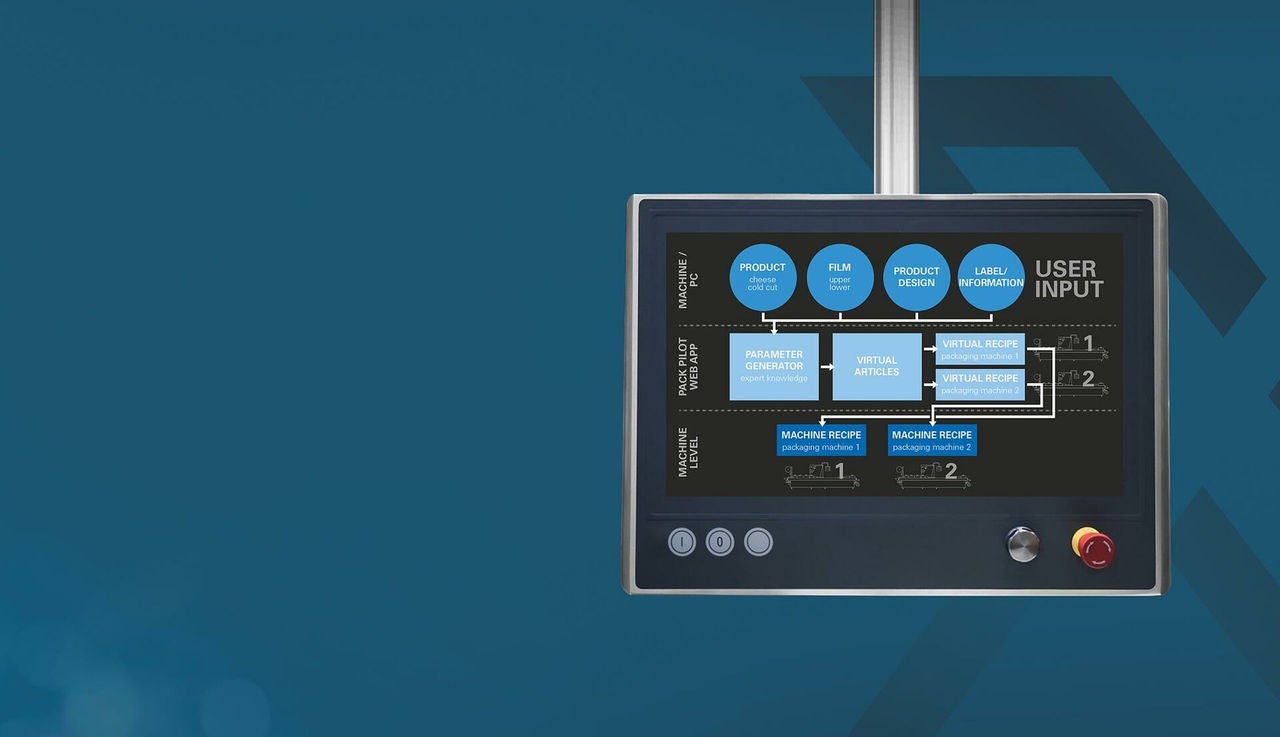
Lack of personnel, lower levels of operator expertise and unrelenting cost pressures are among the main factors, which today are leading to an increase in the degree of automation in all processing industries. Packaging machines must also be capable of being operated as efficiently and cost-effectively as possible. In the constant striving to achieve the maximum flexibility of packaging solutions, which is largely created by the product diversity demanded by the market, it is of great importance to have intelligent control of the machine processes.
Since the market introduction of the new X-line machine generation, customers have an innovative solution in MULTIVAC Pack Pilot, which enables them to master the daily challenges of the packaging procedure in a way that is both convenient and reliable.
Against the background of insufficient know-how in many companies, as regards the knowledge necessary for operating packaging machines to the optimum degree, MULTIVAC Pack Pilot offers companies significant added value. Typical scenarios for the use of MULTIVAC Pack Pilot include for example putting a new machine into service, setting the new parameters when a product is changed, and supporting operators in detecting and correcting faulty settings.
When the packaging machine is put into service, MULTIVAC Pack Pilot offers the operator the optimum basic settings from the start. This significantly reduces the start-up curve to the point, where the optimum machine parameters are reached, which in turn minimises the start-up losses.
Since the packaging machine is already set by MULTIVAC Pack Pilot to the optimum degree when production is started, high-quality packs can be produced at high output immediately after the start of production. This leads to significant savings as regards product, packaging materials and production time. When creating new recipes, the operator simply selects the corresponding features of the pack, packaging material, and product. Working in conjunction with the data for the particular die set installed, the machine sets the parameters itself to virtually the optimum operating point.
MULTIVAC Pack Pilot is not merely fed from a database with defined parameters. But rather it has access to all of MULTIVAC's expert knowledge, which is derived from over 1,000 machine installations every year. MULTIVAC Pack Pilot generates the required parameters on the basis of a rule engine, which is a learning system and therefore ensures the particular machine parameters are continuously optimised. This also provides a very high level of process reliability.
Whereas previously the settings for the packaging machine had to be changed manually by experienced staff, when a new packaging material was to be run, the use of MULTIVAC Pack Pilot now allows the changeover to be made by less qualified operators. MULTIVAC Pack Pilot automatically provides the machine settings for the particular application, and these are as near as possible to the optimum operating point, while also taking into account the individual settings, which are made by operators from shift to shift.
If the new type of film and its associated machine parameters are already captured in MULTIVAC Pack Pilot, the operator simply selects the corresponding material in Pack Pilot, and this then loads the appropriate basic settings for the machine. These basic settings can be adjusted manually by the operator, if he chooses to revert to his own wealth of experience. When the parameters are finally defined, these are saved in the machine as the particular recipe. However, should the film not yet be included in MULTIVAC Pack Pilot, the operator can enter the required data for the film manually. Using the basis of the rule engine, it then defines the optimum setting for the machine and sets the parameters accordingly. Here too the operator can make a manual adjustment of the parameters if required. These parameters can then be saved as a recipe.
Since the basic settings for running the selected film are predetermined for the machine by MULTIVAC Pack Pilot, the time required for changing over to the new material can be reduced significantly. The parameters also ensure the film is run close to the optimum operating point, and this means a consistently high pack quality is always achieved. If tests on different trial materials are being carried out, for example alternative types of packaging material or thinner versions of existing films to reduce packaging volume, MULTIVAC Pack Pilot can contribute significantly to minimising time and test material. Even those operators, who have little experience in running different materials, can benefit from this know-how - they are spared the laborious effort of acquiring the knowledge. MULTIVAC Pack Pilot can actually make an important contribution to reducing the consumption of material when producing packs.
Another typical scenario is changing the pack depth. When a pack height is changed and the draw depth is altered, the packaging machine has to be reset, since new die settings for the film are required. Here manual adjustments can also be made to the parameters, and these are then saved as a recipe in the machine.
MULTIVAC Pack Pilot will continue in the future to be expanded with further knowledge. This will also include the different properties of products to be packed, as well as the resulting effects on the machine parameters. It is also planned that information about achieving the maximum shelf life for the particular product will become available. One example of this is individually matching the modified atmosphere in the pack to the actual requirements of the particular product.
Should the optimum parameters still not be set in the machine, then MULTIVAC Pack Pilot can detect the incorrect settings and replace these with the correct ones. This function can be used in the event of a conscious or unconscious tampering with the parameters. It is often the case that the operator himself can not independently determine, which settings in the machine are incorrect, particularly if there is a high degree of complexity with many variables.
With the development of its Pack Pilot, MULTIVAC has created an intelligent aid, which will continue to be systematically developed in future to meet new requirements in the market. MULTIVAC Pack Pilot will, for example, be able to assist machine operators in selecting the optimum packaging material for the different products, by displaying the required film and appropriate machine parameters for the particular product chosen. MULTIVAC customers will also benefit from new opportunities which arise from the development of future packaging concepts - one example already is the testing of new materials, which without MULTIVAC Pack Pilot can involve considerable material wastage and enormous time.
14.04.2019