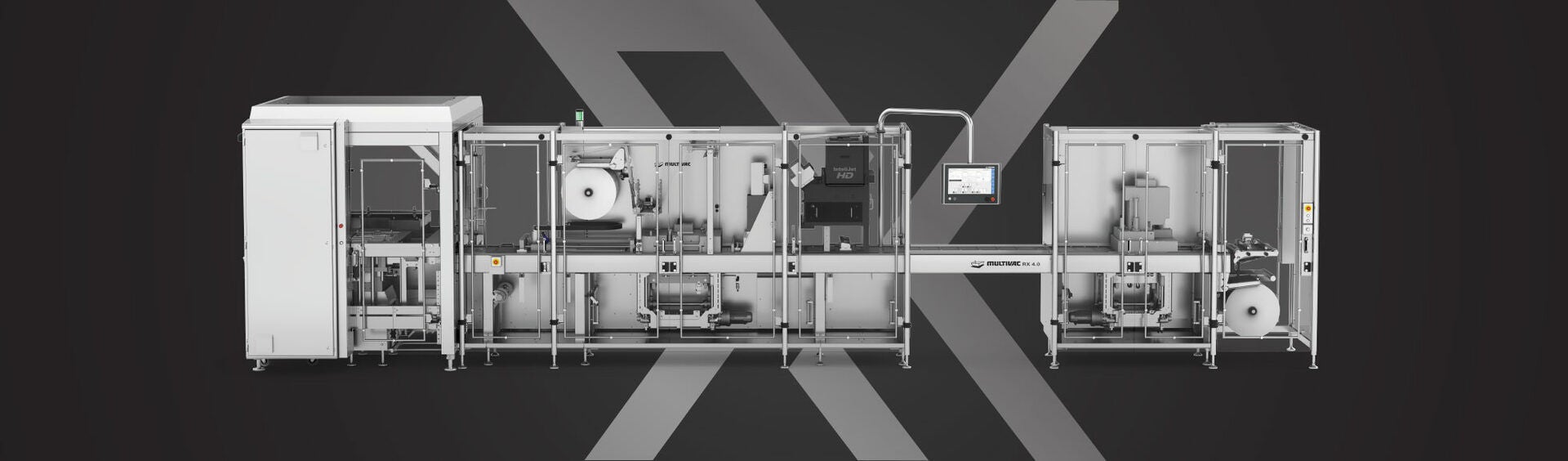
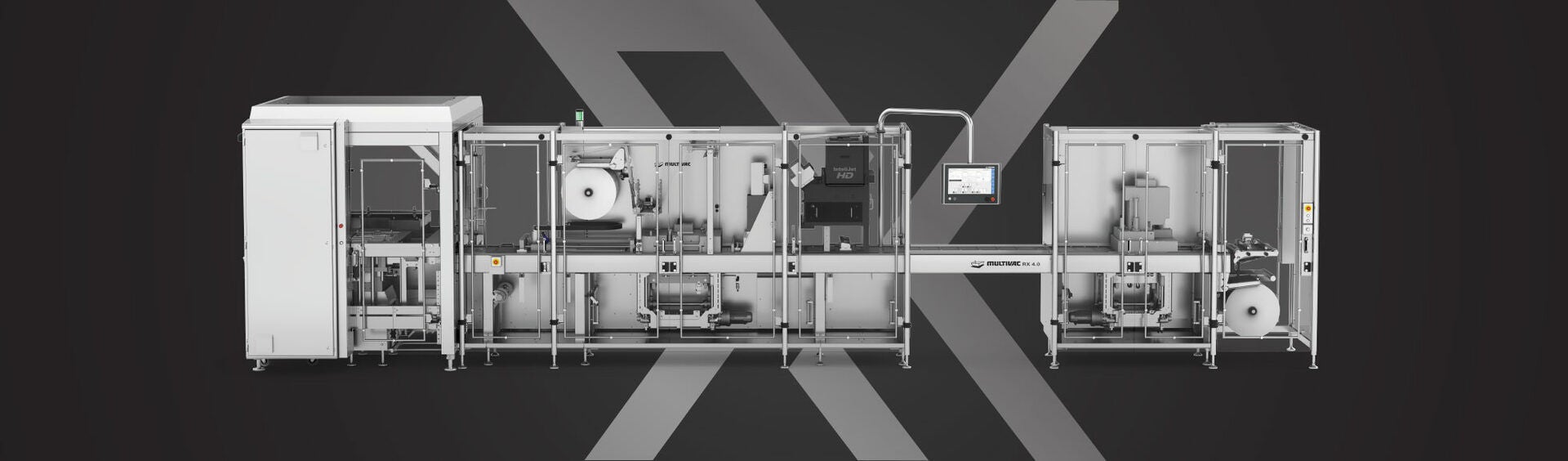
With its new X-line machine generation, MULTIVAC has developed a thermoforming packaging machine, which meets the growing demands of customers, legislation and the marketplace. Particular attention was paid during its development to implement the specific requirements of the medical and pharmaceutical sectors, and MULTIVAC also took into account the experience and advancement gained over recent years.
Proven components, such as those for monitoring and recording the forming and sealing pressure parameters, which make a major contribution to improving process reliability, are installed as standard in the new RX 4.0 machine.
The packaging machine is equipped with a comprehensive sensor system, which has been further developed from that of the previous machine generation. Using closed control circuits, MULTIVAC's Multi Sensor Control constantly captures all the relevant process parameters, such as those for forming and sealing. This enables the RX 4.0 to run permanently as near as possible to the optimum operating point, as well as ensuring the process times are continually optimised - for example by overlapping some processes, running them in parallel or starting them earlier. The relevant values are determined by detailed measurement and analysis of the process times. This creates a higher level of process reliability overall, as well as contributing to an improvement in the output and efficiency of the packaging machine.
Another benefit of the new machine generation is the fact that, thanks to the optimised operating sequences overall, there is more time available for those critical processes, such as sealing for example. This means a better sealing result can be achieved due to a longer sealing time - an aspect that is of particular importance with regard to producing the optimum seal seam on a pack. Only a consistently complete seal seam can ensure a sterile barrier is achieved for the packaged medical product.
Compared to the previous machine generation, there have also been design alterations in the sealing technology, which have resulted in higher sealing forces and better distribution of sealing pressure, allowing greater pack quality and seal integrity to be achieved. In addition to this, the separate pressure chambers for the forming and sealing processes are monitored individually, and the heating circuits are also controlled via sensor modules. The system automatically detects, if one of the heating circuits fails, since the strength of the current for each phase is constantly measured by the sensor module and reconciled with the target data.
And last but not least, the innovative die system and redesigned operating concept also contribute to a high level of process reliability. One of the many standard features of the new operating concept is the fact that each particular operator can log onto the machine by means of a RFID chip card. The intuitive user interface with its Multi-Touch function is high-resolution, and it is equivalent to the operating logic of today's mobile devices. It enables the operating processes to be controlled even more easily and reliably, and it can be individually set to the particular user. This includes different access rights and operating languages. All the relevant machine parameters are clearly displayed on one screen page.
All the die elements of the RX 4.0 are coded and can be identified by the packaging machine. Sensors monitor the top sections of the so-called X-tool dies, so that it is guaranteed during every die change, that the correct format part has been used. RFID chips can also identify the bottom sections of the dies, so errors are avoided here. If the die is correctly installed, the machine automatically sets its own parameters, which ensures the optimum process control is achieved. Operating reliability is therefore increased significantly, particularly for machines with frequent format changes.
MULTIVAC Line Control (MLC) enables the machine to be operated particularly efficiently within an overall packaging line. With just a single command at the control terminal, the central stop/start function allows the user to stop, activate or run empty all the components of the entire line at the same time, and it even allows the recipe to be changed in the same coordinated way. MLC also forms the basis for the simple linking of a packaging line to the customer's ERP, MES, MRP or PPS systems.
The RX 4.0 is designed in its entirety for the demands of digital production. Process data, which is continuously generated thanks to the comprehensive sensor system, can be transferred for far-reaching analysis, so other opportunities are created for using digital services. These extensive, data-based services range from analysis of overall equipment effectiveness and benchmarking to recommendations on servicing and crucial machine settings, as well as including smart services, such as predictive maintenance and condition monitoring. They offer a high level of added value for customers, particularly in the case of complex production lines. Today's data-based services make it possible to create a status analysis of the packaging machine, and to make packaging processes as efficient and cost-effective as possible, so packs of the maximum quality can be consistently produced.
By using the dashboard, both the operator at the machine and the management have real-time access to all the relevant information about the current performance of the packaging solution. How many packs should have been produced? What trend is apparent over a certain time period? From the user's perspective, the dashboard is effectively the control centre of a digitalised machine like the RX 4.0. It can be run not only on a large flat screen beside the machine, but also viewed remotely if required on a PC in an office. The benefit lies in the significant reduction of communication channels and reaction times.
Thanks to its GMP-compliant design, one of the many features of the RX 4.0 is its ease of cleaning, which means it can also be used in a cleanroom. The machine is available in various versions - without enclosure, with partial enclosure or with complete enclosure, and either polycarbonate or safety glass can be used for the construction of the enclosure. The areas of product processing and machine technology are separated from each other. In addition to offering secure line clearance, this also ensures a high level of security against losing products.
With the development of its RX 4.0 model, MULTIVAC has created a futuristic digitalised thermoforming packaging machine, which meets all the requirements for a high level of process reliability, and which is also a significant step forward towards the self-learning machine. Thanks to its systematic data capture and evaluation, the machine is able to set its parameters itself at virtually the optimum operating point, as well as automatically correcting itself, if the parameters deviate from their target value. Since the machine is continuously measuring and analysing the relevant process data, the operator is always kept informed about the packaging machine's current status, which means that he knows precisely where the process has deviated from the specified parameters and how the machine has taken countermeasures.
04.11.2020