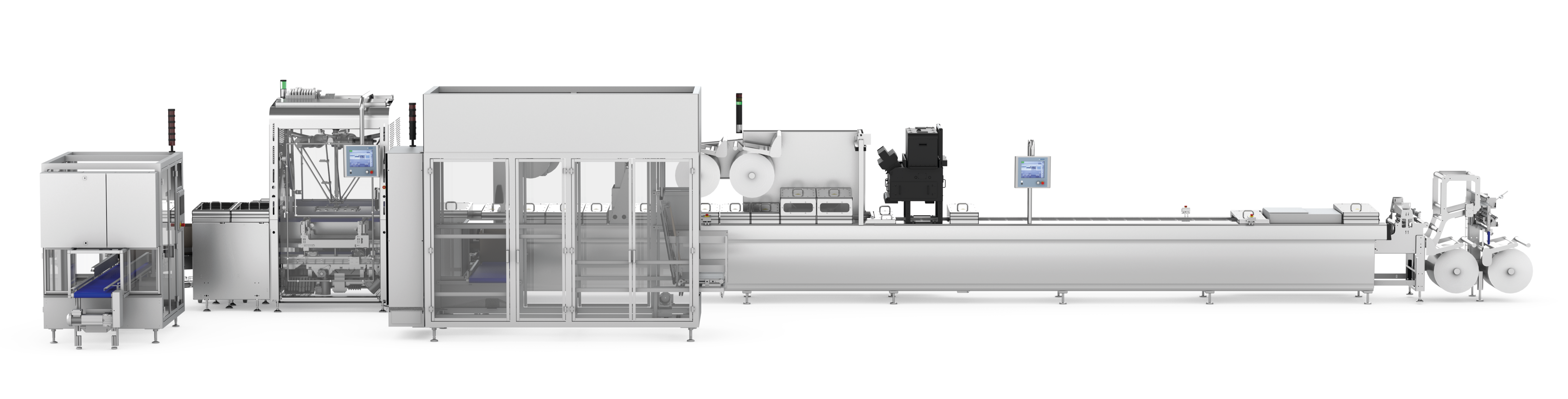
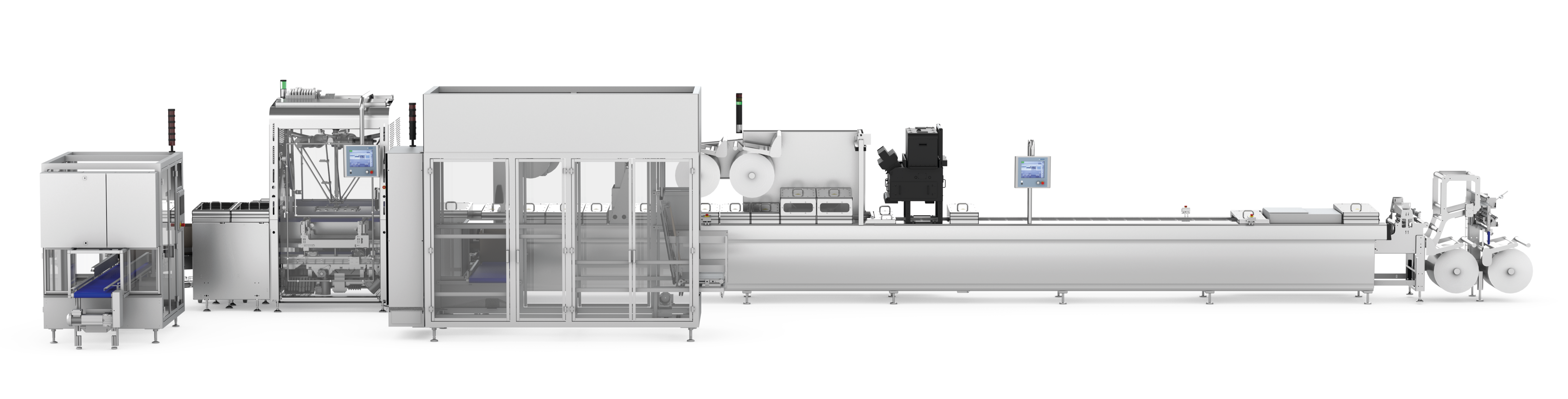
Supplying sufficient test swabs quickly during the Covid-19 pandemic: This was the challenge for PURITAN, one of the largest manufacturers of swabs worldwide, which increased its capacity in record time for orders from the US Government - to a peak of 300 million test swabs per month. The US company relied on MULTIVAC and invested in 36 automated lines to hygienically pack the much sought-after medical products.
Covid-19 rapid antigen tests, which are performed with test swabs, have since become part of everyday life for millions of people throughout the world. But this was not a matter of course in the early days of the pandemic. Even the largest manufacturers of these medical products such as PURITAN, which is based in Guilford in the US state of Maine, only produced a few million test swabs per month before the pandemic. Far too few for the demand that arose in such a short period of time. The US Government tasked PURITAN in March 2020 with manufacturing very large numbers of corona test swabs. And one of the most critical requirements: Speed. The company had to start expanding its capacity within just twelve weeks. And so PURITAN began to convert an old aircraft hangar into a medical production facility with cleanroom classification. And at the same time it looked for state-of-the-art machines and equipment for the production and sterile packaging of the corona test swabs.
“One of the first tasks was to quickly find a manufacturer, who could deliver lines within a few weeks rather than several months,” recalls Timothy Templet, Executive Vice President for Worldwide Sales at PURITAN. But in addition to speed of delivery, the issue of automation was also a critical factor in the search. Because this was the only way to guarantee the required output in the unsafe times of the pandemic with potentially high levels of staff sickness. “Our objective was to ensure, that the machines could operate as completely automated lines, from the loading of the test swabs into the packs right up to the palletising of the shipping boxes.” The choice was made in favour of MULTIVAC, the worldwide packaging specialists. “MULTIVAC not only has high-quality machines, but also a committed and rapid-reaction service team. This meant that MULTIVAC's US subsidiary in Kansas City was able to undertake the installation and project management of the lines completely. For this reason we decided to enter into a partnership with the company, so that together we could increase the production of Covid-19 rapid antigen tests to 300 million per month.” Since then there are now 36 new lines operating in PURITAN's factories. Twelve lines are installed in Maine, and a further 24 in Nashville.
The beating heart of each automated line is a R 535 thermoforming packaging machine, which is designed for operation in cleanrooms. In order to prevent contamination and microorganisms from gaining any foothold on the surfaces of the machine, the MULTIVAC Clean Design ensures that there are no hidden corners or voids and no large clearance gaps. The cables and other lines are fed through closed ducts. This applies to all four stations of the thermoforming packaging machine: forming station, loading area, sealing die and cutting area. This ensures that the test swabs are packaged hygienically in their 25 x 190 mm packs - in compliance with the ISO and FDA requirements. As the first stage, the forming station of the R 535 makes the lower web formable through the effect of heat. By using compressed air and vacuum, the subsequent thermoforming operation produces 40 pack cavities per cycle at the same time. As the next stage in the process, the pack cavities are automatically loaded with the swabs in the loading area: a pick & place robot with a suction gripper picks up 40 corona test swabs simultaneously from an infeed conveyor and places them in the pack cavities. The pack cavities loaded with product are then advanced into the sealing station. The lower web is sealed to a medical paper in the sealing die, which uses high temperature and pressure. The last station on the thermoforming packaging machine is the cutting area, where the 40 packs containing the corona test swabs are first perforated longitudinally, so that the individual packs can easily be torn apart. As the second stage of the cutting process, four individual rows of ten packs are created by means of cross cutting units.
But the line can do more than just pack. In order to provide a system solution from one source, MULTIVAC augmented the thermoforming packaging machine with equipment from partner companies and third-party suppliers. An InteliJet HD digital printer from the US manufacturer Bell-Mark is for example integrated into the line, and this prints variable data onto the top of the packs. And an inspection system from MULTIVAC Marking & Inspection subsequently checks the print for correctness. At the end of the line there is a MULTIVAC H 130 pick & place handling module, which then takes the 40 packs of corona test swabs from the discharge conveyor of the thermoforming packaging machine, before placing them into a box in 25 layers: the boxes are automatically erected by a case loader and then sealed with adhesive tape after loading. A palletising unit then stacks the boxes, each with 1000 test swabs, on top of each other.
“The line requires just four seconds for a machine cycle with 40 test swabs. This means that it is possible to pack 600 test swabs per minute,” says Dr. Thomas Kafka, Product & Business Development Manager Medical & Pharma Solutions at MULTIVAC. “The machine concept creates a very lean manufacturing process with an extremely small amount of packaging waste,” adds Timothy Templet. “We are currently producing the highest-quality packs in the history of the company.” All the lines are operating on a double-shift basis of ten hours each for four days per week. By adjusting the shift times, the output quantity can be increased very flexibly. This enables up to 300 million test swabs per month to be packed.
One reason, why MULTIVAC was able to deliver the lines so rapidly, was the company's expertise in the line business. “Our project managers, who have many years of experience, are able to combine the perfectly honed technology of several manufacturers into one individual line, which guarantees a high degree of automation and product safety as well as process reliability, so that ultimately patient safety can be assured,” says Kafka. Our project managers work closely with customers in a very trusting relationship. At every phase of the project. From the decision-making process, where they visualise ideas with product simulations and virtual 3D models, right through to the machine installation and process validation in accordance with the requirements of ISO 11607, ISO 134 and FDA CFR 21. “MULTIVAC's Validation Department was able to create all the compliance documents at the right time and remove the pressure from our team,” says Timothy Templet. And another huge benefit in terms of time was the fact, that the experts from MULTIVAC provided training to the PURITAN technicians on handling the machines. “The biggest challenge for us in the future is now to adapt to the changing markets. We will continue to rely on MULTIVAC, when it comes to retrofitting the lines if pack requirements change.”
31.03.2023