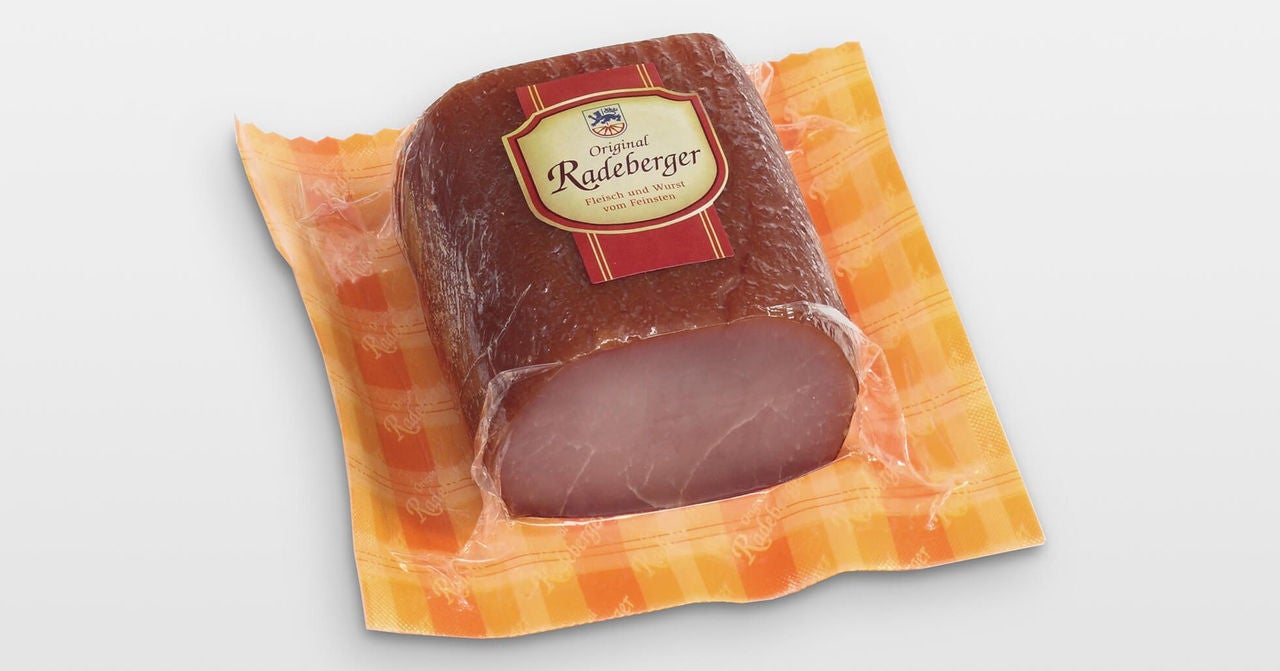
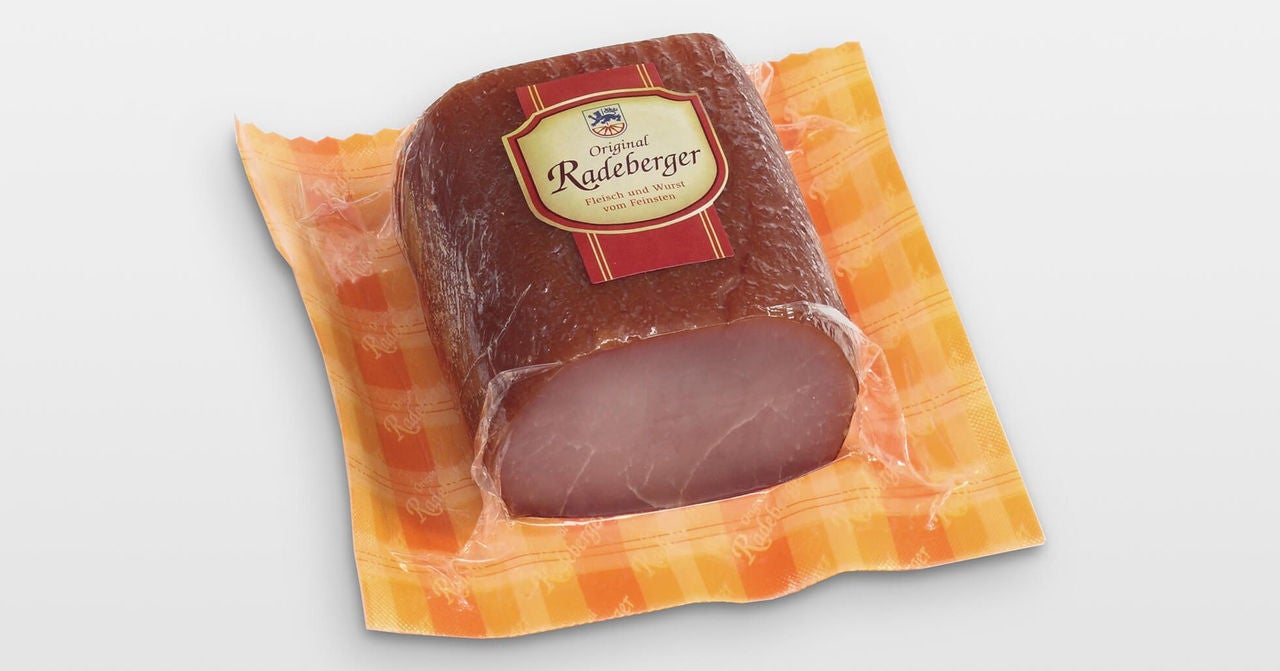
The company Radeberger Fleisch- und Wurstwaren Korch GmbH packs over 20 different types of sausage in 26 different product and format combinations - with just one fully automatic MULTIVAC packaging line.
Since 1990 the company Radeberger Fleisch- und Wurstwaren Korch GmbH, which was founded by Georg Korch and which is located close to Dresden, has been producing high-quality sausage products. The meat processing company from Saxony offers its speciality products under the ‘Original Radeberger’ brand at its own local chain stores and in retail outlets throughout Germany. “We owe our success to the high quality and hearty taste of our products, but also to our intuition for trends in food,” says Michael Korch commenting on the company strategy. “When we develop new recipes, we address the wishes of our customers.”
When a new packaging solution for the ‘Original Radeberger’ scalded and raw sausages was being planned, the intention was also therefore to introduce a more user-friendly opening aid for the packs. “Initially we only wanted to equip our existing MULTIVAC packaging line with a new automation solution,” recalls the company boss. Since the solution based on the R 530 thermoforming packaging machine had already been in use for over ten years, the final decision was made to purchase a completely new packaging machine. This would also enable the desire of Radeberger customers for an improved opening aid to be taken into account at the same time.
Following the previously very positive experience with MULTIVAC, Michael Korch wanted to continue working with a solution from the packaging specialist, and he therefore sought advice about a more user-friendly pack. “The new design for the opening aids on the different pack variants was quickly found,” says Harald Knoflicek, who is responsible at MULTIVAC as Sales Manager for the food industry in Northern Germany. “The bigger challenge was presented by the requirement for automation, since a wide range of different packaging formats and sizes had to be included for the large ‘Original Radeberger’ product variety.”
The new line had to feature the ability to pack mini sausages as well as long beef sticks. For some sausages rigid film was more suitable for the packs, while for others flexible film was the better choice. In addition to this, the chambers of the duo-packs had to be filled with two different types of sausage. “MULTIVAC developed a fully automatic sausage packing line, capable of coping with a very complex set of tasks and a high specification level,” emphasizes Michael Korch.
Since October 2015 the company has been packing its speciality products on the automated packaging solution from MULTIVAC, using packs made from rigid film as well as flexible film - for every type of sausage there is the right pack. The packs are produced on a R 535. Thanks to a wide variety of equipment options, this high-output thermoforming packaging machine can be adapted to the customer’s individual wishes and the widest range of applications. “When it came to automation, the critical factor for us was being able to run the large product variety without problems,” explains Michael Korch. “Another area of focus was the shelf life of the scalded and raw sausages: the atmosphere in the pack is modified before sealing, allowing the product to remain fresher for longer.” An ergonomic drawer system accelerates the die change that is necessary for the different packaging materials and pack formats.
In order for the wide range of sausages to be packed on just one packaging solution, the line was systematically automated from beginning to end. The packaging procedure starts with an infeed system, which transfers the pre-sorted sausages from a storage container to the loading robots’ infeed system, while spacing them individually during this process. In the case of the duo-packs, the two chambers of the storage container are each filled with a different type of product. The complete product infeed is designed as two-track to separate the two types of product.
The MULTIVAC H 240 multi-robot handling module was integrated into the packaging line to place the sausages from the MULTIVAC product infeed conveyor into the pack cavities. Its modular construction and the changeable gripper systems of the three integrated HR 460 4-axis robots enable a wide variety of products to be handled. These robots can handle up to 3,500 g total weight at a time, as well as position the product exactly in the required place by means of 4-axis kinematics.
The 4-axis robots are controlled with the data from a MULTIVAC Vision System line scanner, which captures the position and spacing of the sausages at the beginning of the first belt segment, and which then transmits this information to the robots. The sausages, which are not picked up by the first two 4-axis robots and placed in the packs, run onto the next belt segment. A second
MULTIVAC Vision System line scanner captures the position and spacing of the sausages again, and the third 4-axis robot takes over the completion of loading.
After this there are only those sausages on the conveyor, which the inspection system has detected as being too long, too short or overlapping, and which it has not therefore communicated to the robots. They are ejected and fed back manually. An integrated counter determines the ratio of good to reject products for the purposes of internal evaluation.
The use of high-quality materials and the systematic MULTIVAC Hygienic Design™ enables a thorough wet cleaning of the packaging line to be carried out. “As a food processing company, we attach great importance to the aspect of hygiene,” explains Michael Korch and adds: “In 1996 we were in fact the first meat processing company in Saxony with a quality management system in accordance with DIN EN ISO 9001, and since 2005 we have been operating to the highest quality standard in the food industry - the International Food Standard.”
“The new packaging line runs just as reliably as the previous MULTIVAC line,” says the company boss with satisfaction. “The new packaging solution has also paid off financially, since it achieves around 20 to 30 percent more output than the previous one.” This provides the following benefit during daily production: personnel, who were previously engaged in manual tasks in the packaging procedure, are now available for other tasks in the Production department. “Our high expectations have been clearly exceeded. And our customers are pleased and the packs can be opened much more easily than before - in other word, success across the board,” says Michael Korch with delight.
01.05.2016