MeetMULTIVAC: Field Service Technician
Introducing the team at MULTIVAC
11.08.2022
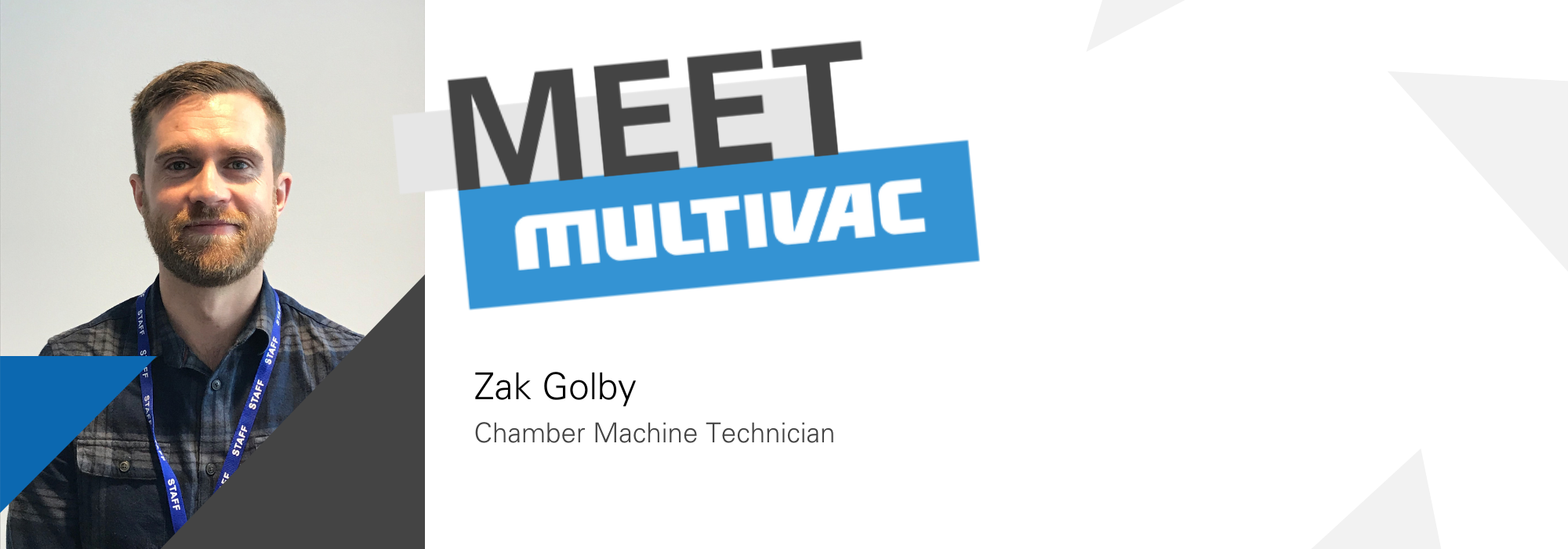
At MULTIVAC, our people share the same vision and values to help process and package what is valuable to your business, but how much do you know about the different areas of our business, and the people who make it all happen?
This year, we’re making business more human and introducing you to some of our hard-working, knowledgeable, employees from the various departments at MULTIVAC UK.
It’s our August installment of MeetMULTIVAC...
Zak Golby, Chamber Machine Technician
Tell us more about your role!
I service and repair chamber machines. Mainly I support customers in the London area, but I am often required to head further afield. I also train our customers on the operation of our chamber machines, teaching them the ins and outs and instructing them on how to use them.
What does your day to day look like?
My role at MULTIVAC is very autonomous and I primarily support London and its surrounding areas. Day-to-day I will respond to customer requests and visit sites where I attend a mixture of service calls and breakdowns. A lot of my jobs are a result of customers pulling a variety of mixtures into the mechanism pumps, and they usually don’t know how it got there. The most common sites I visit include restaurants, hotels, medical facilities or really, really posh houses.
How long have you worked at MULTIVAC in your role? Have you had any other roles at MULTIVAC?
I have worked in my role at the company for four years now and it has been my only role at the company.
What do you like about working at MULTIVAC? What is your favourite part of your job?
My role is very autonomous and I get to go to different places on a daily basis, I’ve never been one to be stuck in the same place for too long so I like the variety of locations I get to see. The support I get is also spot on.
What is a current problem out customers/industry are facing that you are seeing out in the field, and that MULTIVAC is aiming to fix?
The time delay in getting certain spares is causing an issue for some of our customers. Although this is a problem that can’t be helped, it can result in leaving a customer without an integral piece of kit. MULTIVAC aims to help customers with this issue by holding a number of spare parts in stock and holds up to £2m worth of spare parts in stock!
How has MULTIVAC’s equipment technology changed since you first started at MULTIVAC vs. now?
The technology hasn’t changed while I’ve been in my personal role, although I understand it has company wide. The main question I get asked at the trade shows I attend is about a cheap alternative to single use plastics; this is something our materials team has been working on, and I understand we sell fully recyclable pouches for our chamber machines.
What do you enjoy doing outside of work?
I love the outdoors, so hiking, running and cycling tend to fill a lot of my time.
What did you want to be when you grew up when you were younger?
At first I wanted to be a police woman after meeting one as a kid when my house was burgled, no one had the heart to break my dream. When I realised that wasn’t possible I wanted to join the Army.
Tell us something we don’t know! A surprising or fun fact about you...
While I was furloughed, a disaster relief charity called OP:React asked veterans to volunteer and assist with certain tasks. I ended up working in a temporary mortuary in London and doing alive and well checks in Norfolk.
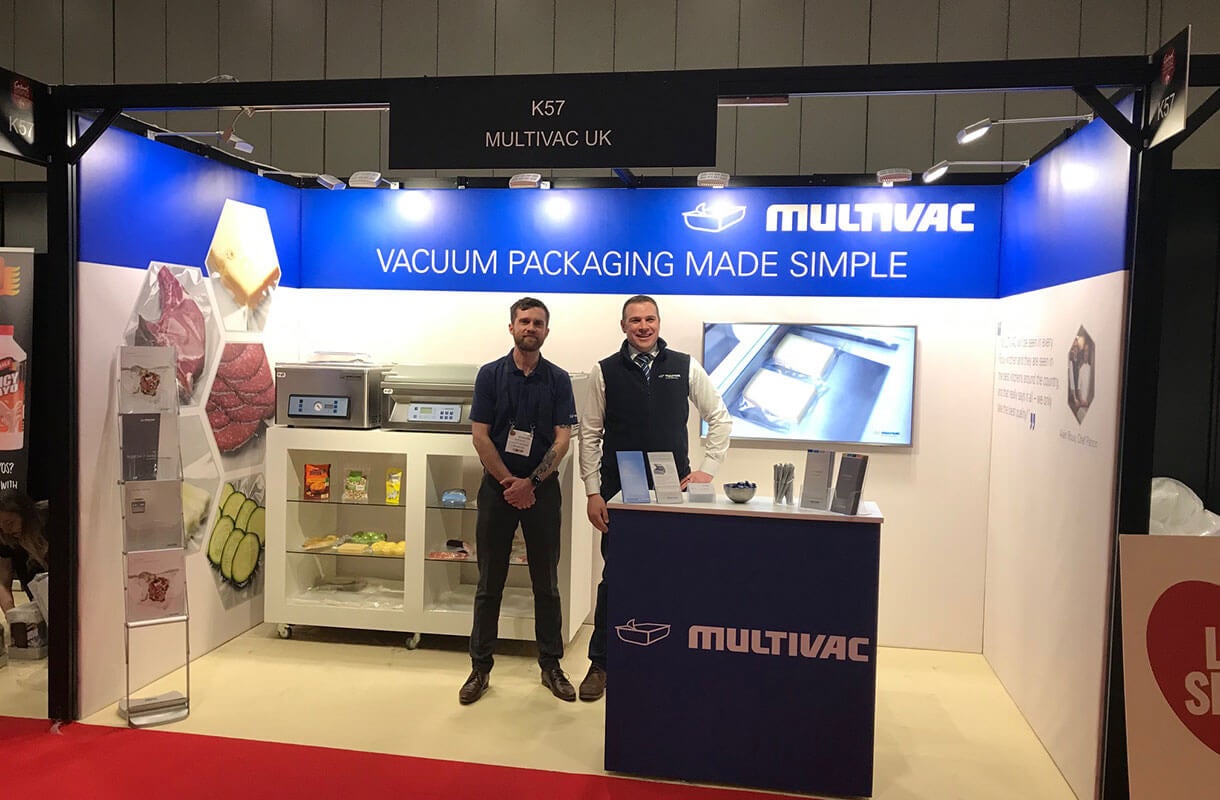
Stay tuned for next month‘s instalment of MeetMULTIVAC!
For more information on any of our materials and packaging solutions, please do not hesitate to Contact Us.