MeetMULTIVAC: MUUK Processing Team
Introducing the team at MULTIVAC
09.11.2023
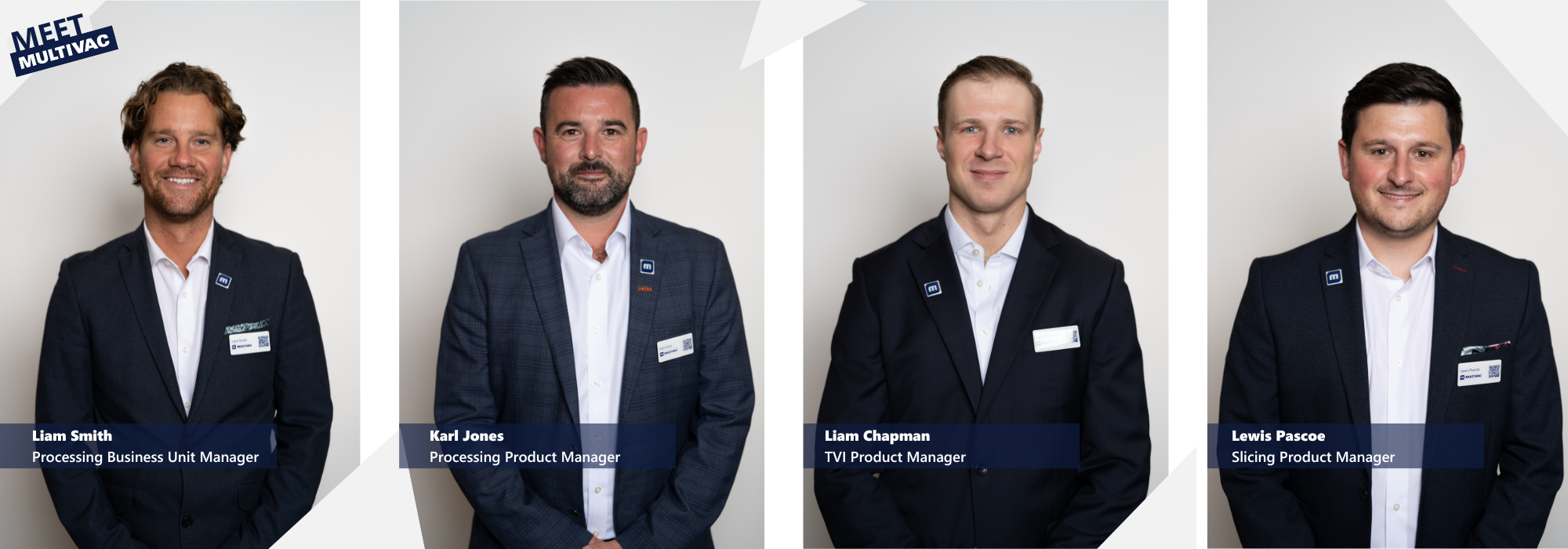
At MULTIVAC, our people share the same vision and values to help process and package what is valuable to your business, but how much do you know about the different areas of our business, and the people who make it all happen?
We’re making business more human and introducing you to some of our hard-working, knowledgeable, employees from the various departments at MULTIVAC UK.
It’s our November instalment of MeetMULTIVAC...
The MULTIVAC UK Processing Team
The Processing team at MULTIVAC UK....
Meet Liam Smith, Processing Business Unit Manager at MULTIVAC UK
Tell us more about your role at MULTIVAC!
I manage the entire processing business unit at MULTIVAC UK which includes portioning, slicing, curing and smoking, plus the processing section of meat preparation and filling solutions. My role is to ensure that the product management function for processing delivers the best service to our customers, this includes providing the very best subject matter experts in their fields, enabling customers to choose the optimum solutions with best-in-class support throughout.
What does your day to day look like?
The majority of my time is spent visiting our new and existing UK customers. This means that we can understand their daily issues and long term goals, allowing us to make recommendations on how we can bring the best technology to their factories. In order to facilitate this, some of my time is spent with our exclusive agents who are based across Europe to bring these technology advances to them. The remainder of my time is spent working from the executive shed home office putting into action the admin that makes all of this come together!
How long have you worked at MULTIVAC?
A running total of 13 years: 6 years as a service technician, 6 years as a processing product manager, and 1 year as the Processing business unit manager.
What’s your favourite part of your job?
Growing with our partners. Through working personally we get to see their factories evolve as they grow. Being able to revisit a factory and see the benefits being realised makes all the effort worthwhile. Also, everyday is a school day in processing! We are always learning the subtle differences in our customers‘ products and how that makes them unique.
What is a current problem our customers are facing that you are aiming to fix?
There’s lots! Sustainability, labour repurposing, health conscious convenience...
Sustainability is huge for everyone right now, and important for the global goals in any industry. There are often many ways to produce the same product so now we are really focusing on how to produce the same quality AND reduce carbon emissions.
Labour repurposing is important to ensure our factories have the guaranteed resource to fulfil their output requirements every day. This often means using processing machinery as a form of automation, and is surprising how often the right application can overcome this.
And finally, health conscious convenience is rapidly increasing and shows no sign of stopping. Convenience is king with the UK customer driven by fast paced lifestyle and Generation Z. If this is the ‘new form‘ of calorie intake, then it is important that we deliver on the best nutrition too – there are some really interesting projects coming up in this area.
What are you generally working on at the moment?
The dust is just about settling on our in-house event which took place in September, where the team had a strong focus on sustainability. From obtaining maxium yield from a steak, slicing without the carbon footprint of crust freezing, or grinding frozen product with minimum power consumption, the event presented our ideas around this and we are now working with our customers to bring them to life.
Our newest partners of 4 years, Metalquimia, also have some impressive cutting edge technology around curing and in-line air frying. This is really pushing boundaries even further on the health conscious convenience topic.
What do you enjoy doing outside of work?
When you don’t find me working I once would have described myself as being quite active in sports such as football and golf, however with two boys aged 10 and 13, a lot of this now revolves around their love for football and cricket – although they do have a bar at the cricket pitch so that’s my personal preference!
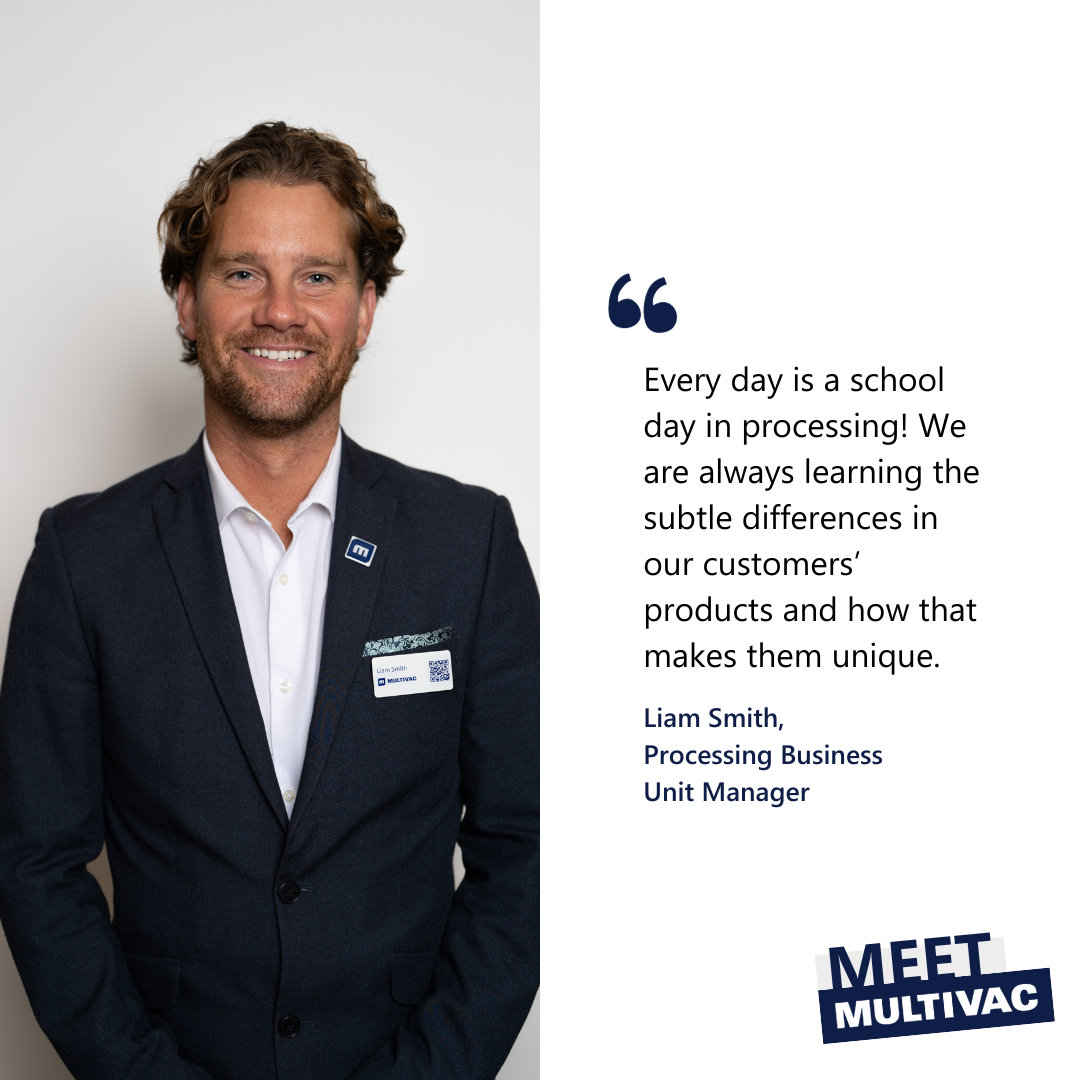
Meet Karl Jones, Processing Product Manager at MULTIVAC UK
Tell us more about your role at MULTIVAC!
I’m responsIble for looking after our third party processing suppliers, LASKA and Risco. This involves working together with them and our sales team to deliver solutions for our customers.
What does your day to day look like?
My day to day involves supporting our sales team by being the subject matter expert in all things processing! You can largely find me attending customer and internal meetings to help get the right solution for our customers, FAT’s and SAT’s also play a big part in my daily work.
How long have you worked at MULTIVAC?
Although I only joined the processing team in January this year, I started at MULTIVAC as a Technical Support Engineer in 2017, then in 2021 I took over as the Product Manager for Chamber Machines, and here we are today!
What’s your favourite part of your job?
My favourite part of my job has to be running customer trials on machinery at our facility in Swindon, you never know what product you might be running one week to the next and it’s almost always a messy job!
What is a current problem our customers are facing that you are aiming to fix?
For meat processing, especially frozen, the main challenges are around power consumption. Grinding frozen blocks at -18 ͦC takes an enormous amount of power, which is why LASKA are always looking to improve the efficiency of their machines by using less power and being faster.
What are you generally working on at the moment?
A large part of my role at the moment is working with our projects team on some big production line installations with LASKA. It’s always satisfying to see these projects through from point of specification and order, to seeing the product being produced on site.
What do you enjoy doing outside of work?
Outside of work I enjoy football, fishing, boating and holidays. But I have two young girls so they take up most of my time these days!
Tell us something about you that we don’t know.
One of my hobbies is boating and we go on regular family trips down the river Thames, of course stopping in each and every pub on the way (and the way back!).

Meet Liam Chapman, TVI Product Manager at MULTIVAC UK
Tell us more about your role at MULTIVAC!
My primary responsibility in my role is overseeing the TVI range of machinery, a comprehensive portfolio that provides turn-key solutions for meat portioning. This includes tempering, crust freezing, fixed weight portioning, and other complementary solutions for automatic portion-to-pack processes. As the main sales point of contact in the UK for the TVI range, I collaborate closely with our technical team, which compromises six dedicated TVI technicians. Together, we aim to provide UK customers with unparalleled consultancy, helping them achieve improved yields, minimise giveaway, and maintain top-quality products, all while reducing labour requirements.
What does your day to day look like?
My days vary significantly! Most of the time you can find me on-site, using a scale to weigh steaks as I audit processes to determine potential areas for improvement or optimisation. As many in the industry will know, it’s essential to be hands-on in this role to truly understand both the process and the meat (site to site, there are differences in the cut and butchery techniques). This approach is where we can offer the most valuable insights to our customers. Unfortunately, this level of hands-on insight can’t be achieved behind a desk!
How long have you worked at MULTIVAC?
I’ve been with MULTIVAC for just over six years. I initially joined as a graduate Project Engineer and later progressed to the role of Project Manager, a position I held for several years. This experience has granted me foundational knowledge of the wider industry and a deeper understanding of customer requirements for installations, as well as the intricacies of machinery, both upstream and downstream from TVI equipment. It’s essential to consider the full scope to ensure we’re providing customers with a solution tailored to their needs and one that integrates seamlessly with other equipment further down the packaging line. One of the benefits of being part of MULTIVAC as a group is our ability to offer a comprehensive range of equipment and deliver a technical solution that truly meets the customer‘s needs.
What’s your favourite part of your job?
Definitley, my favourite part of my job is working with our customers to refine or optimise a process and then witnessing the tangible improvements this brings them, whether financially or in other areas. It’s deeply satisfying to see one’s hard work materialise into benefits for the end customer, especially when it’s accompanied by the positive feedback we recieve. A 1% improvement in yield or giveaway might not seem significant at first, but the impact this makes over time is simply staggering.
What is a current problem our customers are facing that you are aiming to fix?
Sustainability and the current cost of living crisis are undoubtedly huge topics/concerns across the industry right now. When you consider that a beef fillet has CO2 emissions of 65kg per kilo, and a retail price of apporximately £35 per kilo, any savings in yield or giveaway can genuinley have a profound impact both on the environment and on our customers who are grappling with the ripple effects of high inflation. As the technological market leaders, TVI can offer significant savings in this area.
What are you generally working on at the moment?
Currently I’m collaborating with several smaller customers, including wholesalers and medium-sized butchers, to trial TVI’s GMS 400. This machine introduces the advantages of TVI’s volumetric portioning technology to an entry-level platform for the first time. In addition, I’m liasing with TVI on some excitng new developments set to launch in the UK next year – watch this space!
What do you enjoy doing outside of work?
Outside of work, when I’m not at the gym or spending time with friends or family, I’ve found myself unexpectedly taking on a bit of an ameteur DIY role after stumbling into a house with a lot of ‘character‘. This has been a journey of learning new hands-on skills, and I find it quite relaxing in contrast to my typically hectic week!
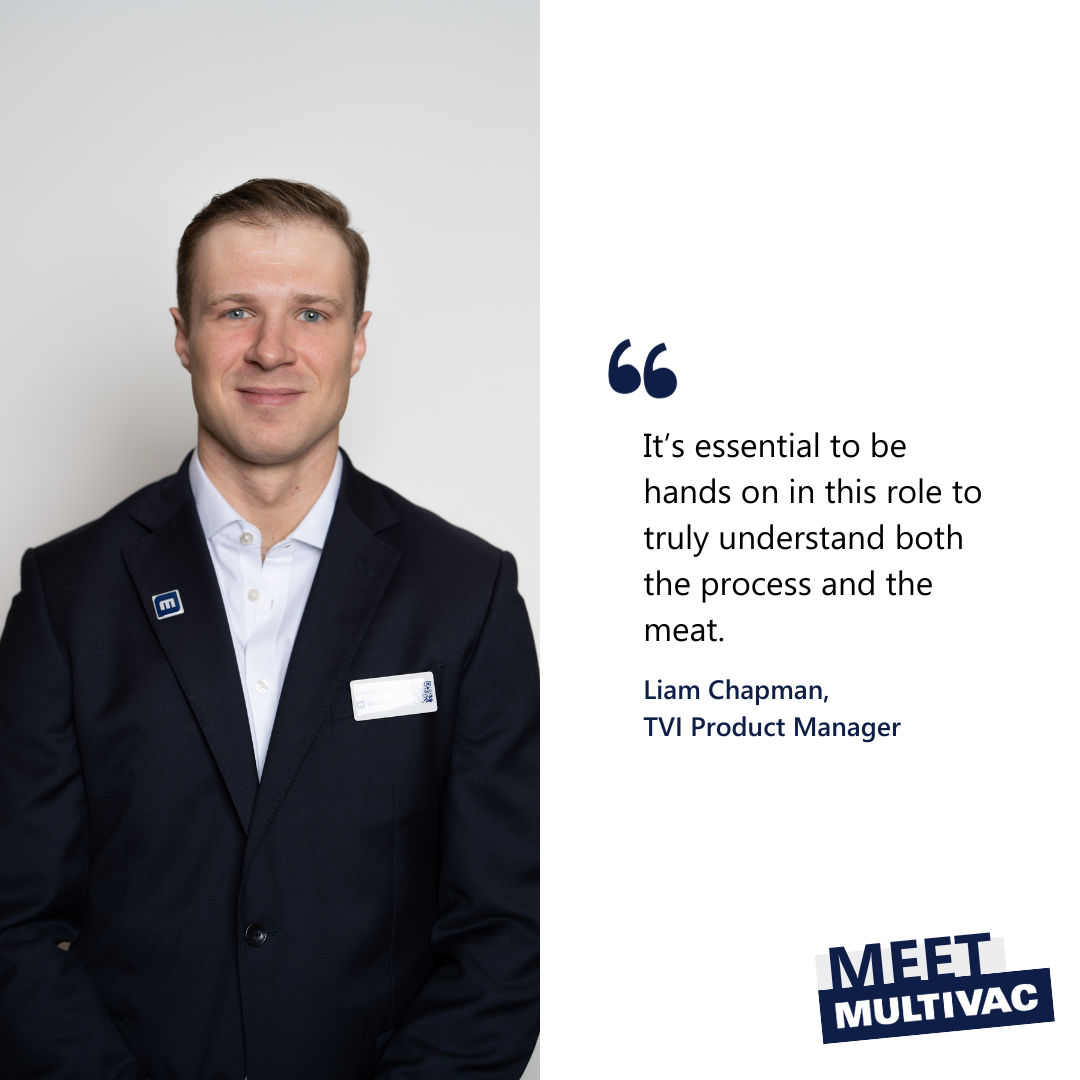
Meet Lewis Pascoe, Slicing Product Manager at MULTIVAC UK
Tell us more about your role at MULTIVAC!
I joined the processing team as Slicing Product Manager in March 2022. My role involves supporting sales, technical and product development.
What does your day to day look like?
Everyday is different! From visiting customer sites to present our slicers (and the many reasons why it is the best on the market), to visiting customers for catch-ups on how their current machine is performing. We are constantly working with customers to encourage them to make the right desicion when it comes to slicing. It is always good to speak to customers and find out exactly what their issues are, every site is different.
How long have you worked at MULTIVAC?
7 years and fast approaching 8 in January 2024. Before my current role as Slicing Product Manager, I worked in the service department as a Service Technician in the South East region.
What’s your favourite part of your job?
Installing a slicer into a new customer site! When the machine performs from day 1 and we can show the customer the exact reason why they should always choose MULTIVAC.
What is a current problem our customers are facing that you are aiming to fix?
Supply chain seems to be a promient issue currently. Improving processes for customers to make the MULTIVAC slicing line the most efficient in the industry, this allows our customers to have faith in our machine and maintain a healthy relationship with their customers.
What are you generally working on at the moment?
Replacing a customers existing slicing machine for a MULTIVAC one, so far we have replaced four, although we still have a long way to go!
What do you enjoy doing outside of work?
I’m a huge football fan so watching the local football teams on a Saturday with my friends, I’m also a Tottenham fan but I feel like I should keep that one quiet; Harry Kane has broken my heart!

Stay tuned for next month‘s instalment of MeetMULTIVAC!
For more information on any of our materials and packaging solutions, please do not hesitate to Contact Us.