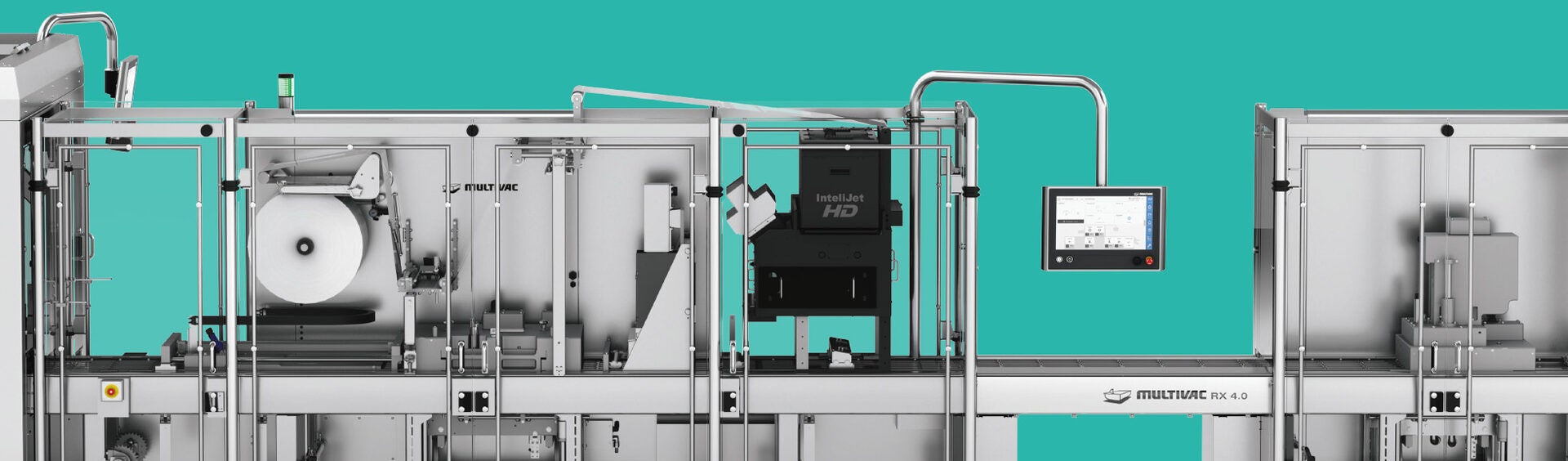
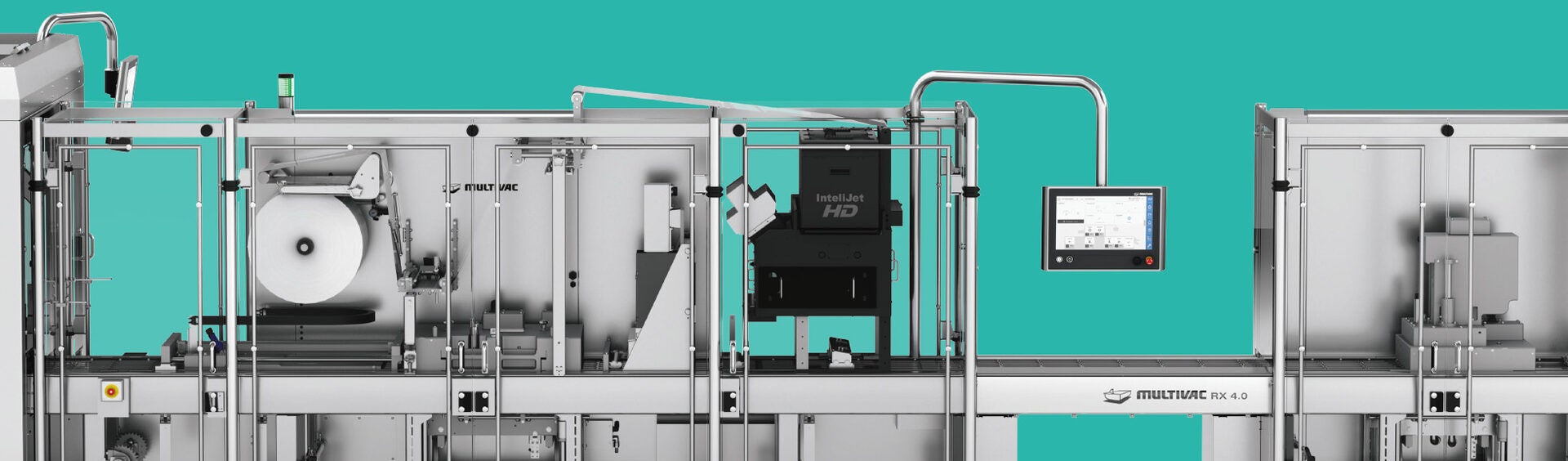
Since the legislators have not issued any regulations regarding the printing technology and systems to be used for marking the product and pack, the companies themselves within the medical industry have the choice. Among the common digital printing methods are currently thermal transfer, thermal inkjet and Piezo inkjet printers. These digital printing systems offer the benefit of being very flexible and also suitable for smaller batch sizes.
Digital printers also enable changes of text and print image to be made very quickly and cost-effectively. This pays dividends, for example, in the case of manufacturers who producing and packing a product in different countries. Here the manufacturer must ensure the changeover takes place at exactly the same time in all the subsidiaries, and this is generally associated with a high level of cost and effort both in the preparation and the implementation. The digital printers can be linked directly to a central database, allowing for immediate changeover to the new layout to be made without any effort. Uploading the new print image takes just a few seconds. This saves time, effort and cost.
Thermal transfer printing is a widely used printing method. Here the print image is transferred to the flexible upper web by means of a thermal printhead, which uses an ink ribbon with a thin layer of temperature-sensitive ink. Due to the limited print area, these printers are used primarily for printing variable data, and only infrequently for creating large layouts. Since the variable data for medical products (e.g. best-before date, lot number, two-dimensional datamatrix code) must have good legibility, it is mostly only black thermal transfer ribbons that are used. There is, however, a relatively high material cost involved in these ribbons. Also only a fraction of the thermal transfer ribbon is used for printing, the rest is unused waste. The production equipment must also be stopped in order to change the thermal transfer ribbon - and the production capacity is therefore reduced accordingly. The thermal transfer printer scores over other systems in terms of the purchase price, but the costs for replacement of thermal printheads are however fairly high.
In the case of the thermal inkjet process, water-based inks are generally used for printing on paper or Tyvek®, while solvent-containing inks are used for printing on film. The ink is heated and expands. This causes the ink drops to shoot out of the nozzle. Although the size of the drops can be regulated, it is not however possible to graduate the application quantity within a print image. For example, if a higher resolution of 600 dpi is used, this results in a higher consumption of ink drops, whereas the consumption remains smaller with a lower resolution.
As with thermal transfer printers, only a limited print area is available with thermal inkjet printers. One print cartridge can cover a print image with a maximum height of 12.7 millimetres (0.5 inch). If a larger print area is required, several print cartridges are necessary, although their number is mostly restricted to a maximum of four to six cartridges due to limitations in their control. This printing technology is also therefore not normally used for allover printing, but mostly just for variable data.
Due to the water-based inks, this printing technology creates print images with a smaller ink coverage. The investment in the hardware is relatively small, however, the individual print cartridges are expensive. Thanks to the auto swap function, changing the print cartridges is very efficient - two printhead holders are used, each with a print cartridge, and the cartridges are automatically changed in the event of a fault. However, this does reduce the usable print area.
This solution can be used for all types of packs and all common materials, such as Tyvek®, paper, film and even aluminium multi-layer films. In the case of the medical products industry, the process is largely pre-determined, since the print has to withstand all the usual types of sterilisation, for example ethylene oxide gas, gamma irradiation and steam sterilisation.
The use of Piezo inkjet technology is particularly suitable for those companies, which have to print large production batches with variable information or print images with larger areas. Piezo inkjet printers are subject to fewer limitations in terms of the print layout, whereas other digital printing systems on the other hand offer a very limited print area.
Piezo printing technology is also superior to other inkjet processes in the fact that the intensity of the ink application in a print layout can be controlled very precisely, which means different colour coverage can be achieved within the print layout. In addition to this, the consumption of liquid ink can be restricted to the absolute minimum that is necessary. Printing with a resolution of up to 600 dpi can be achieved without problems.
Generally in the packaging process, films or other materials are used which have already been printed with the standard information by the supplier - or alternatively blank material, which is significantly cheaper than pre-printed material and more flexible in its use. The use of blank material also reduces the cost and effort of inspection, storage and logistics.
In contrast to thermal transfer or thermal inkjet printers, Piezo inkjet technology offers the benefit of being able to print not just variable data but also large print layouts onto blank material with a single printing system.
The InteliJet HD series of high-performance printers from the US manufacturer, BELL-MARK Sales Co, are drop-on-demand digital printers. MULTIVAC has been cooperating with BELL-MARK for many years, and since the end of 2019 MULTIVAC has been distributing these printing solutions exclusively on the European market. They can be supplied in different variants as either one-, two- or four-colour systems. One of the main features of the printers is their excellent print quality - even with a very large print area. They are easy to integrate into new packaging lines or retrofit to existing ones.
Thanks to its print resolution of up to 600 x 600 dpi and a printing speed of up to 150 metres per minute, the progressive technology enables texts, logos, variable data and various codes, as well as large-scale or multi-colour print images, to be printed precisely and cost-effectively on a wide range of blank or pre-printed materials. The high-quality UV inks dry very quickly with state-of-the-art UV LED lights, and the ink spread remains very small even with the coarse-fibred Tyvek® material, allowing even small icons and text to be reproduced perfectly. The modules can be fitted with up to twelve printing heads, so a complete blank material with a width of up to 649 millimetres can be printed.
These printers are of particular benefit for companies with a frequent change of print image. But they are also suitable for small, as well as large batch sizes, and the Piezo system really comes into its own where there are frequent changes of small batches at high production loading. The investment in this system also pays off for companies producing a single product in large volume over a long time period (mass production), and which can really exploit the benefits of buying blank material.
The particular strength of the InteliJet HD series lies in its print quality and flexibility in terms of colours, layouts, formats and materials. Special colours are also possible. The printing costs per print image are very small, due to the UV-based inks being more cost-effective when compared to thermal inkjet printers or thermal transfer ink ribbons. However, the last two printing systems mentioned are a lower-cost initial investment. The colour ink tanks of the Piezo system are exchanged "on the fly", so the packaging machine does not have to be stopped. Another plus point for Piezo inkjet technology: the ink hardens irreversibly straight after application thanks to the UV lamp, and this means it is permanent and legible for a long time - an aspect that is of immense importance, particularly due to the UDI regulations, since the pack marking and code have to be legible with a certain grade (C or better) over the entire shelf life of the medical product.
The main difference between the two currently available models, the InteliJet HD ServoWAS and InteliJet HD Traverse, lies in the arrangement of the printing heads. In the case of the ServoWAS model, the printing heads are stationary and arranged across the web path. The upper web is guided through the printer. In the case of the Traverse model, the printing heads are moved across the upper web by means of the integrated shifting unit.
The two printing systems also vary as regards the film width: whereas film widths up to a maximum of 649 millimetres are possible with the ServoWAS, the maximum film width for the InteliJet HD Traverse is 600 millimetres. Both printing systems can offer one-, two- or four-colour print images.
The printing is always performed after the film advance has taken place, so that very good print quality and accuracy is achieved. This means changes in settings on the machine, such as a change in advance speed, do not have any influence on the printing.
In the ServoWAS printer the film is transported during the process by means of an integrated film indexing device. This is driven by a servo motor, allowing the web advance to be set perfectly to the particular upper web being printed. With the Traverse printer, the speed at which the printing heads are moved across the web can similarly be set via the servo motor. This also contributes to achieving optimum print quality.
Seen overall, the Traverse version is lower-cost, but it can only have a maximum of two printing heads. Depending on the print image, this limits the layout size to a maximum of 220 or 300 millimetres. Larger layout areas are covered by the InteliJet HD ServoWAS.
The Windows-based machine control on both models can be equipped with different interfaces, so it can be linked to virtually all database systems.
10.03.2020