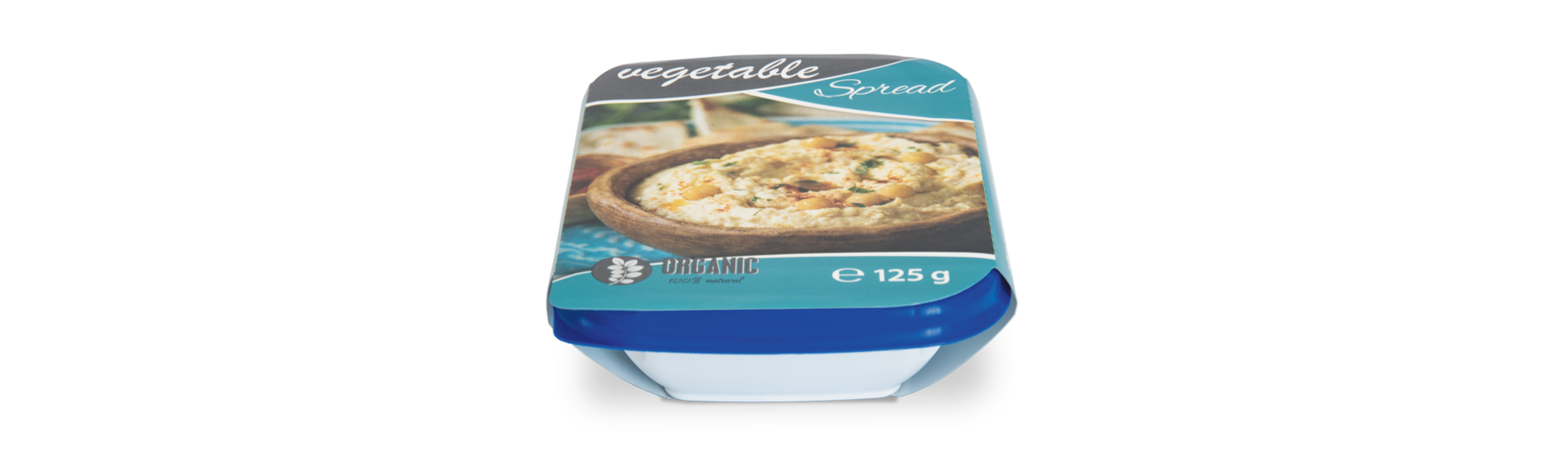
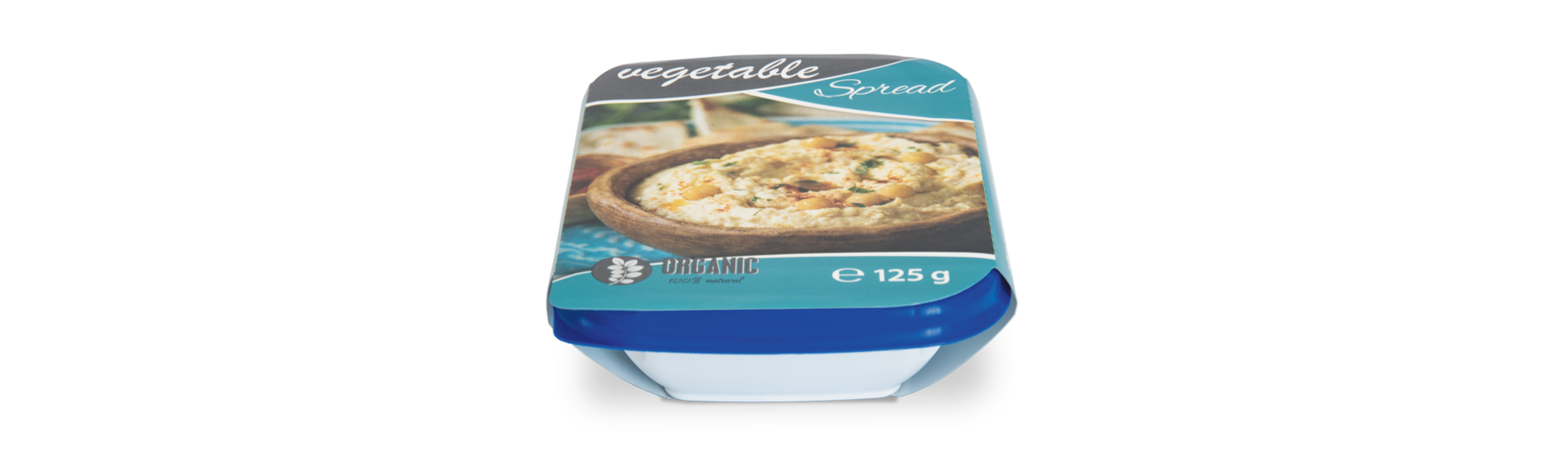
Whether it is Parmesan wedges or Emmental blocks in vacuum packs, Gouda and Tilsit slices in MAP packs, or fresh cheese spreads in lidded trays and even yogurts, soured milk or kefir in handy pots or glass jars - the diversity of products that can be produced from milk is as wide as the range of packaging concepts available.
There is also a wide range of requirements to be met in terms of the most attractive presentation possible at the point of sale. Here the labelling of packs with a wide variety of labels plays a very important role. Labels also serve as carriers of information, and this has very great significance in view of legal requirements, particularly in the case of food products. By underlining the value and quality of a product or brand, labels make a major contribution to the improved presentation of products at the point of sale.
Generally there is a range of different factors, which influence the selection of a suitable labelling solution. In addition to the type of packaging machine used, the crucial aspects are in particular the pack shape and also special requirements as regards the positioning of the label.
A common packaging concept for dairy products is thermoforming packaging. This process enables products to be packed under vacuum or with modified atmosphere (MAP) - both make a major contribution to improving product protection along the added value chain, as well as extending the shelf life of the product.
When it comes to the inline labelling of thermoformed packs, cross web labellers are particularly suitable since they can be integrated into the packaging process itself thanks to their compact design and minimal footprint, and they can also be conveniently controlled via the HMI of the packaging machine. In order to meet the different printing requirements as regards production-related data, the labellers can be equipped with all the standard types of printing processes. The labels are precisely applied to the top and/or bottom of a pack, and a wide range of label formats and materials can be used.
With its latest generation of cross web labellers, MULTIVAC sets the benchmark in the market as the leading packaging specialist. The main features of the new models compared with the earlier machine generation are a previously unachievable cycle output and significant improvements in the machine control, drive system, and construction.
Thanks to the process-controlled functioning of the new machine control, the individual sequences are overlaid as far as possible, so the labelling process is optimised and significantly faster due to its harmonious motion profile. The virtually continuous operation of the longitudinal shift unit, as well as a robust machine construction and label dispensers, which are equipped with sophisticated servo motor technology, also make their own contribution to a significantly higher cycle output.
The use of servo drives means it is not necessary to perform reference runs before the labelling operation is begun - so set-up and conversion times are reduced, and the labellers are operational more rapidly at product changes. The simplified construction with its fewer number of deflection rollers also accelerates label roll change and makes it even easier.
Particular importance was attached to safety, especially in view of the high cycle speeds. The constant monitoring of travel speeds and torque ensures the highest level of process and operating safety is achieved, even at maximum output. In parallel with this, MULTIVAC has also optimised the menu guidance feature and equipped it with an integrated wizard function. The system only needs the required number of cycles to be entered by the operator - after that all the relevant speed and acceleration parameters are adjusted automatically and therefore reliably.
Dairy products such as cream cheese and quark are often packed in small lidded trays. The tray lids generally have a ridge running all around, and this provides the necessary rigidity as well as making the handling of the packs easier. This means the tray lid has a recess in the top. In order that the label can be applied seamlessly onto this uneven surface, the cross web labeller is equipped with so-called pin pusher plates. The pin pusher plates have up to 400 press-on pins, which adjust flexibly to the surface. This ensures the label material is pressed on securely but also gently, even where the surface is uneven.
Another labelling solution, which is frequently used in the milk-processing industry, is the so-called conveyor belt labeller. These modular systems are positioned downstream of the packaging machine, and their main feature is the high level of flexibility when labelling packs with different shapes. The spectrum ranges from pots and tubs through to folding cartons and right up to tubular pouches, thermoformed packs, and trays. Labels can be applied to the top or bottom surfaces of packs, to the sides and even over their edges. The application of sealing labels is also possible.
MULTIVAC's conveyor belt labellers offer many different options for achieving maximum efficiency and cost-effectiveness. One option is the zero-downtime facility, in which the labeller is equipped with two label dispensers for each label that is to be applied. Because the label dispensers operate alternately, the label material can be changed on the inactive label dispenser without interrupting production. In the case of lines, where packs are running in two tracks, it is possible to use conveyor belt labellers with two parallel transport belts, or alternatively two conveyor belt labellers arranged back-to-back, so that a high cycle rate is achieved with a small footprint.
The modular L 320 conveyor belt labeller was developed for rapid and precise labelling of round or oval products. In addition to the label dispensers, which are based on servo technology, the units for the precise spacing, guiding, and aligning of the products ensure maximum labelling accuracy is always achieved even at high speeds. Thanks to a minimum of format parts, which can be changed very quickly, the L 320 can be converted to different products within a short period of time and without any additional tools. Since many parameter settings do not have to be changed during conversion, or can be very easily reproduced, the downtime is reduced to a minimum, even when a large number of different container shapes are being run. The rapid change of label rolls, together with the use of low-maintenance components, also contribute to the labeller's high level of availability.
The labelling requirements are particularly high for deli cheese products, since the expectations of consumers as regards product quality have to be underlined by the appearance of the packaging. Cream cheese spreads with exotic ingredients, as well as refined cheese nibbles in trays or pots are currently in vogue, and these containers can also be used as serving trays.
One solution for the attractive labelling of these packs is the so-called full wrap labeller, which not only reflects the hand-crafted character of the product but also meets the current requirements of sustainability and film reduction, when modern paper fibre-based materials are used.
With this type of labelling, which is also called D labelling, a label is wrapped around all four sides of a pack, similar to a banderole. Due to the size and shape of the label, there is a large surface available for the product and manufacturer information, which is required by legislation, as well as for the optimum presentation of the brand. In addition to this, recommendations such as recipes or cooking tips for the consumer can be included on the back of the label.
MULTIVAC has also developed high-performance solutions for this application as well, and they can be designed individually for the particular requirement. Full wrap labellers can apply labels up to 500 millimetres wide with maximum positioning accuracy - and also at a cycle output that can easily keep pace with high-performance packaging machines. Virtually all shapes can be considered for the self-adhesive labels that are used. It is even possible to have labels with curves or cut-outs, which can be perfectly matched to the shape of the particular product or pack. A 360° wrap-around can be achieved, as well as overlapping ends of labels.
Grated cheese in particular is generally sold in film pouches. Stand-up pouches, so-called Doypacks, are becoming increasingly popular. Tubular bag machines, generally known as form-fill-seal (FFS) machines, are used for packing these products. The IL 130 and IL 140 inline labellers, which dispense labels onto the packaging film in the running direction or across the film running direction, were specially designed for installation on vertical (VFFS) or horizontal (HFFS) tubular bag machines. Flexible mounting systems and compatible add-on parts enable the labellers to be laid out perfectly for the specific requirements of the customer. Interfaces to all the standard control environments ensure the labellers are integrated easily and seamlessly into the overall process.
Depending on the particular labelling task and required speed, different applicators are available for a precise and reliable application of the labels. These press, brush, roll, or blow the label onto the pack. The labels can be applied either intermittently or continuously. Various types of printers can be selected for printing production-related data onto the labels.
Inline labellers are also used for labelling round speciality cheeses such as Camembert or Munster, which are frequently wrapped in paper or film. These labellers are mounted directly on the wrapping machine and apply the label, which serves as a sealing label, to the underside of the pack. It is also possible to apply an additional label to the top of the pack.
MULTIVAC follows an integrated approach with all its solutions, so that the optimum efficiency, process reliability, and ease of operation are achieved in the packaging and labelling process. The declared aim is not only the right labeller but also complete solutions.
A wide range of equipment options and upgrading modules make it possible to design the systems perfectly to customer requirements. All the labelling procedures described above, i.e. cross web, transport conveyor, and inline labelling, can be equipped with all the standard printing technologies, such as thermal transfer, inkjet, and thermal inkjet.
The process reliability is further increased, if the labellers are combined with inspection systems for checking labels and print. This means that faults in the labelling or printing process can be detected reliably, even with a high degree of automation. MULTIVAC also offers a complete range of visual inspection solutions, which extend from label presence and position checking to product and print inspection through character recognition, code checking, and pattern recognition. Depending on the complexity of the inspection task, there is a wide range of sensors, barcode readers, and intelligent camera inspection systems available. The inspection solutions can be integrated directly into the packaging line or designed as stand-alone solutions.
The in-depth integration of all individual modules in the MULTIVAC machine control offers major benefits in terms of automation and reliability of operating processes, since they are all controlled centrally via one control terminal. This also means that any possible operating errors are minimised.
03.12.2019