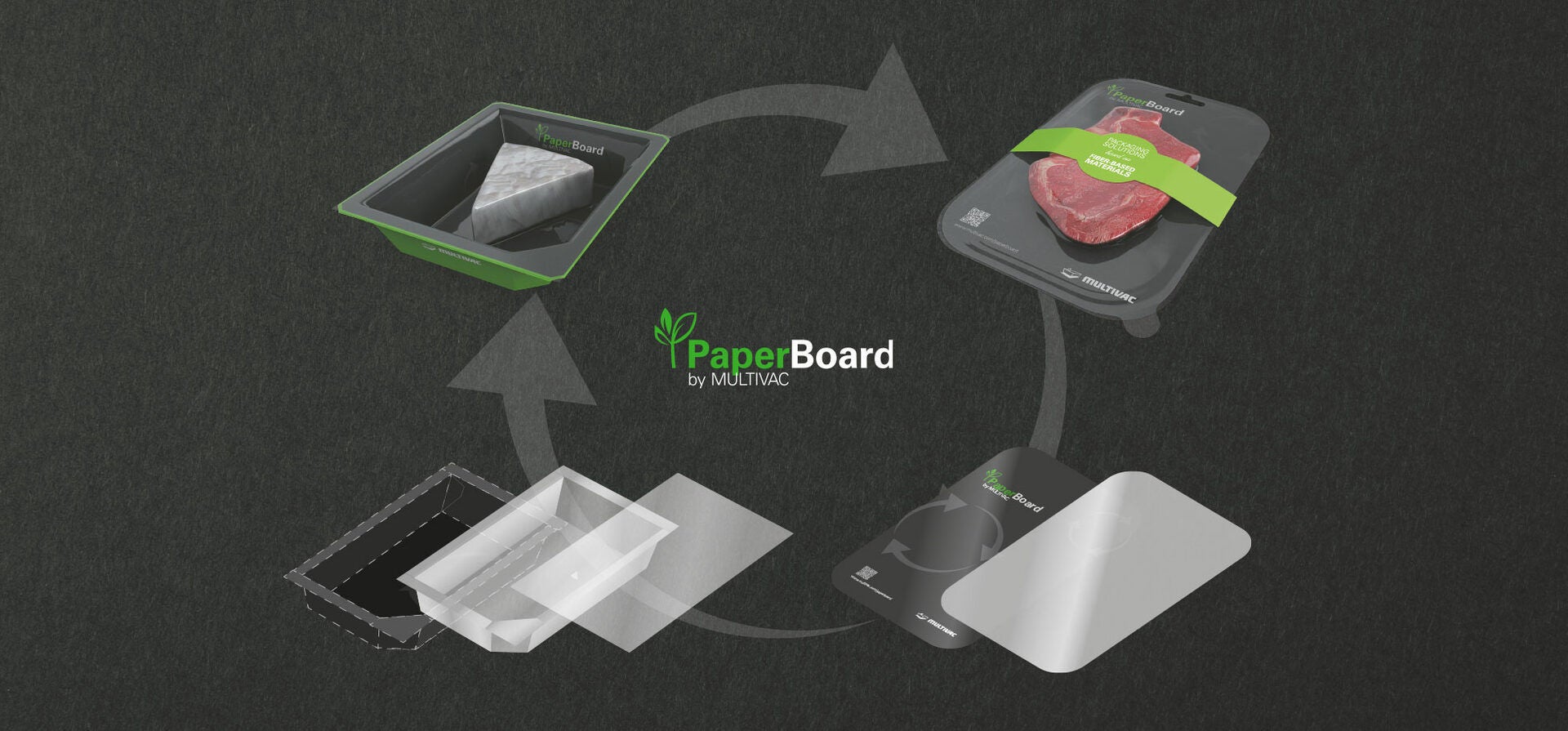
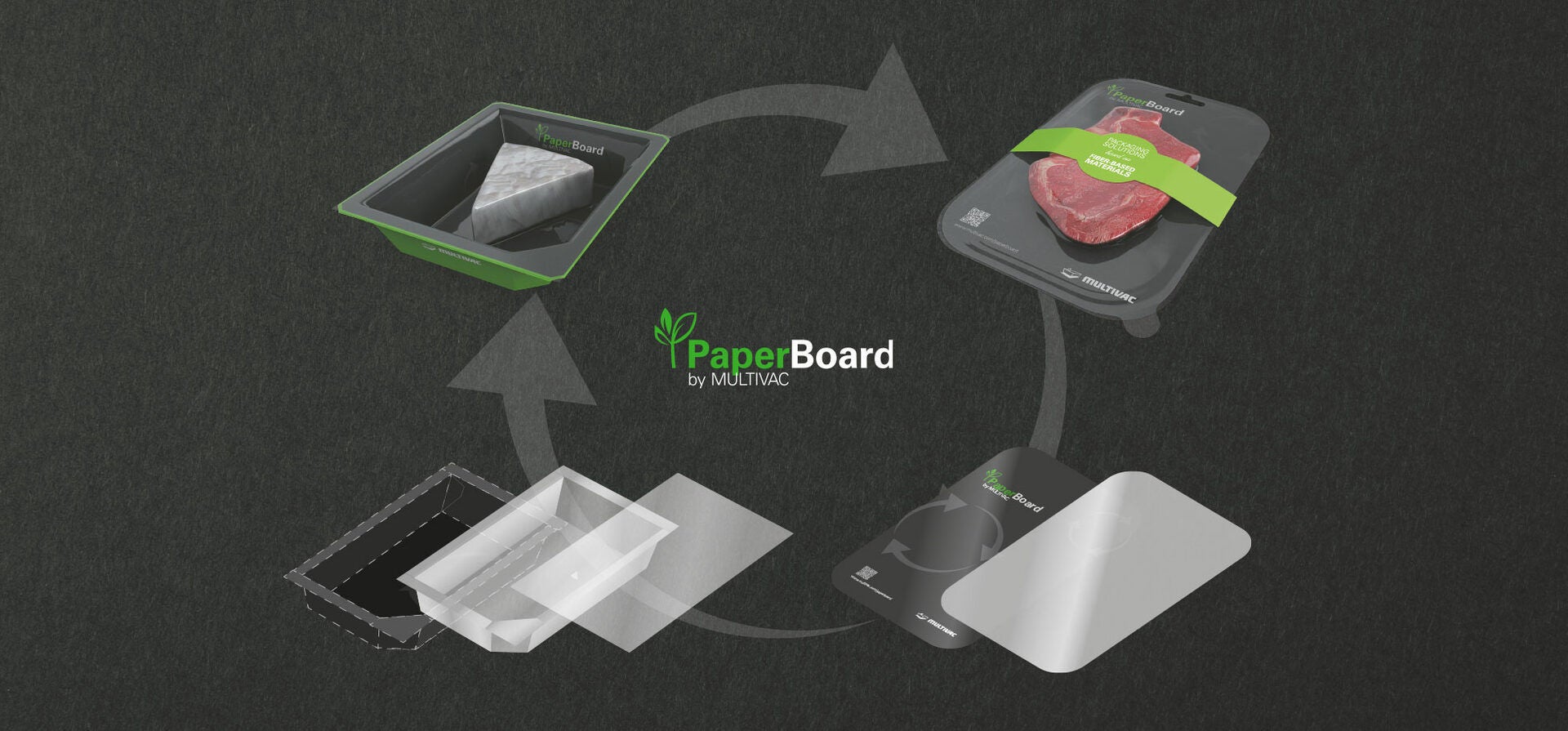
The new Packaging Legislation has been in force in Germany since the start of 2019. Among other things, it lays down challenging quotas for the recycling of materials and the reusability of packs. The introduction of a functioning closed-loop system for the packaging industry, as well as establishing that plastics are a reusable and therefore valuable resource, are important steps in the right direction. In parallel with this, the packaging industry is also driving forward the development of packs made from alternative materials. In addition to the introduction of a closed-loop system for plastics, the reduction in the consumption of plastics in the production of packs also represents another sensible approach to the sustainable development of the packaging industry.
Today plastic packs contribute 60 percent of the typical end user's plastic waste. Worldwide around 325 million tons of plastic are processed annually, of which some 80 million tons are used for producing plastic packs - with Europe, Asia and the USA among the largest producers. And plastics production continues to rise. It is estimated that there will be a further doubling of worldwide plastics production in the coming two decades.
Plastic packs offer significant benefits however, particularly in the food industry. By combining different polymer layers, it is possible to produce plastic composites, which can be designed precisely for the barrier requirements of the particular product to be packed. Thermoplastic materials also offer great flexibility in the design and shape of packs. In addition to this, plastic packs offer the optimum product protection throughout the entire logistics chain, as well as ensuring maximum consumer safety. Thanks to their role to extending the shelf life of food, plastic packs also contribute to reducing food wastage.
In order to implement sustainable packaging concepts in the food industry, it is essential to view the entire added value chain holistically, from the manufacturing stage through the logistics chain and right up to use by the consumer. In addition to the introduction of closed recycling loops and the reuse of plastic packs, it is also productive to look at concepts for reducing the consumption of plastics in the production of packs, as well as the options for using alternative packaging materials.
In the case of glass, aluminium, and tinplate as well as PET bottles, there are already functioning closed-loop systems for recycling. In Germany, for example, around 99 percent of the PET drinks bottles with a returnable deposit are collected, while some 94 percent of these are recycled.
It is another story, however, with plastic packs: although Germany is the undisputed leader ahead of Austria, Belgium, and Slovenia in the recycling of plastics with a quota of 65 percent, this calculation is only based on the quantity of plastic waste delivered to the recycling centers, and not the quantity that is actually recycled. The overwhelming proportion of plastic waste is sorted before ending up in waste incineration plants - or alternatively sent abroad for disposal. One significant reason for this is that many materials can currently still not be separated cleanly. This is because packaging material used in the food industry consists primarily of multi-layer composites. They possess the great advantage that, despite having a relatively small material input, they offer barrier properties which can be individually tailored to the particular food product, as well as optimum protective functions. However, mechanical separation of composite materials is still not possible today on an industrial scale.
Intensive work is currently being carried out on the development of systems for chemical recycling of composite materials. The aim is to introduce a closed-loop system, in which the individual plastic materials can be recycled for further use. Chemical recycling involves splitting the plastic molecule chains into their individual constituent parts by means of chemical alterations such as hydrogenation, hydrolysis, or pyrolysis, and thereby recovering the basic materials for new packs. In contrast to the time-consuming and costly mechanical recycling of PET bottles for example, practically all plastics can be recycled by this process, particularly with hydrogenation and pyrolysis - and without having to be sorted in advance. The preliminary work for these solutions is still however in the pilot phase, and they do not yet represent an adequate or economic alternative.
One productive approach is therefore to develop pack concepts based on materials, for which closed recycling loops already exist. A good example of this are paper fibre-based packaging solutions, since the paper can be fed back into the existing paper recycling loop, after it has been used. Even if the material is disposed of in the normal packaging waste rather than in the paper recycling bin, it can be detected in today's modern recycling centers, where it is removed and fed into the paper recycling loop.
MULTIVAC's PaperBoard offers a range of solutions for producing packs made from paper fibre-based materials. The packaging materials, which were developed in conjunction with leading manufacturers, can be run on standard machines and meet the requirements of the food industry as regards barrier properties and protective functions.
The PaperBoard range includes solutions for producing MAP or skin packs on thermoforming packaging machines and traysealers. Both types of packaging machine can be individually designed to meet the particular output requirements of customers.
When it comes to the traysealers, it is possible to run either trays or pre-cut sheets made of board or cardboard composites. MULTIVAC offers three different solutions for producing paper fibre-based packs on thermoforming packaging machines. Where vacuum skin packs are produced, formable paper composites can be used, which are available in various grammages and with different functional layers. Cardboard composites from the roll can also be used as carrier materials for vacuum skin packs. Both types of carrier material can be separated from the composite by the consumer after use.
In addition to this, MULTIVAC has also developed a machine concept for running cardboard trays, which are made from mono board, on thermoforming packaging machines. A suitable plastic sealing layer is applied in the forming die, which enables the appropriate skin film to be sealed. This concept also enables the end user to separate the packaging materials into their constituent parts.
Another approach is the development of packs which consist as far as possible of mono materials. These can then simply be fed back into the particular closed-loop system. From today's perspective, prime candidates are PP and APET materials.
Polypropylene (PP) film is a standard plastic material frequently used for packs. The material is characterised by its good barrier properties, heat resistance, and stability. PP also has the lowest density of all standard plastics. Packs made of PP therefore have a lower weight compared to those made of other materials - an important aspect in terms of sustainability and environmental protection. However, running this material on thermoforming packaging machines is more challenging than with other plastic materials.
The highly transparent APET (amorphous polyethylene terephthalate) material is also impressive in its very good water vapour and gas barrier properties. It is resistant to oils and fats and it can be used in a temperature range between -40 °C and +70 °C. Currently packs and trays made from APET and other mono materials are already being used instead of composite materials for packing fresh products. In order to achieve reliable packaging results, special upper webs with a thin sealing medium are used, such as sealing lacquers.
When using mono materials for packing food products, it is important to take into account the change in barrier properties compared with composite materials, which may have been used previously, as well as the effects of this on the packed product. It should also be noted that a reduction in the functional layers, such as the sealing layer, can also alter the parameter window of the materials, and this must be taken into account when setting the processing parameters.
When it comes to developing sustainable packaging materials, so-called biopolymers should also be considered as an alternative. The term “biopolymers” comprises two classes of materials: firstly those polymers which are manufactured from renewable raw materials, such as PLA or PHA. These polymers are biodegradable. The second class of materials includes those polymers which can be manufactured entirely or partially from renewable resources, but which are not biodegradable, examples being PET or PE. Based on current knowledge, thermoplastic PLA is the most practical alternative for producing thermoformed packs made of biopolymers from renewable resources. Due to its low barrier properties and impact resistance, the applications for thermoformed packs made of this material are comparatively limited however. It is often used in the fresh fruit and vegetable sectors.
If one is going to evaluate biopolymers overall, it is important to consider not just the economic aspects (price and availability), but also the recyclability of these materials at the end of the life cycle. In the absence of sufficient consumer education about these materials, as well as the lack of integrated disposal systems, it is not yet practical to completely separate the different types of biopolymer materials. This could lead to situations, where biodegradable polymers are fed into the recycling stream for conventional plastics instead of industrial composting facilities.
The new Packaging Legislation is aimed at increasing the recyclability of plastic packs and significantly raising the proportion of recyclate in packaging materials. These objectives will not, however, be achieved by merely establishing quotas. It is more a case of creating the appropriate incentives and framework conditions for the whole industry, so the necessary recycling streams can be put in place. An additional challenge is also ensuring that consistently high recyclate quality is achieved. It is only in this way that recyclates can be processed into high-quality materials. If the separation process is tainted, constituents such as colorants, plasticizers, or stabilisers in the original material can have a significant influence on the quality of the eventual recycled material.
And last but not least, stemming the amount of plastic waste through a reduction in packaging material volume is also a very productive approach. This can already be achieved today by implementing innovative packaging concepts, such as novel pack shapes or using new machine technology for producing the packs, and these measures can significantly reduce material consumption or increase material yield. You can find out about the possibilities available by reading the next edition of 'Fleischwirtschaft' (“Reduction in packaging material volume”).
16.04.2019