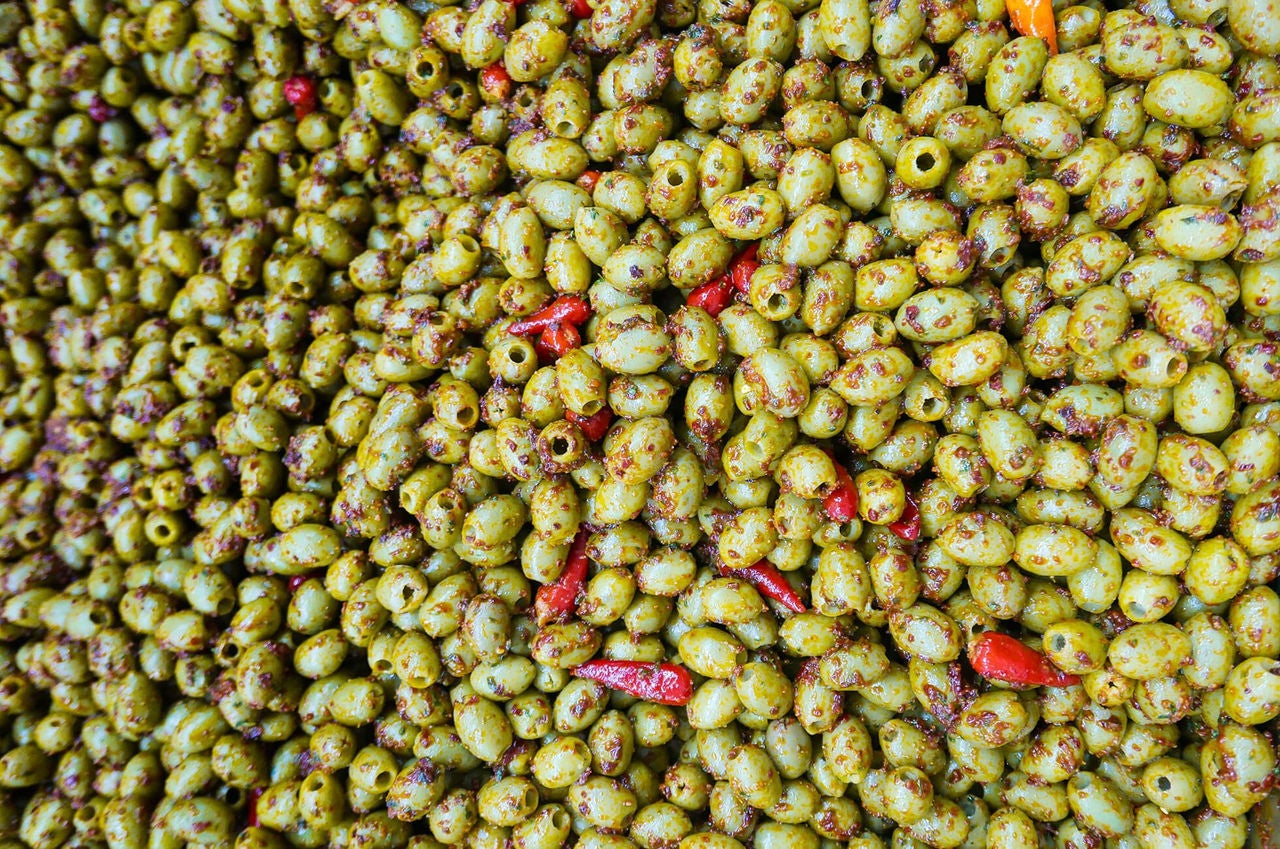
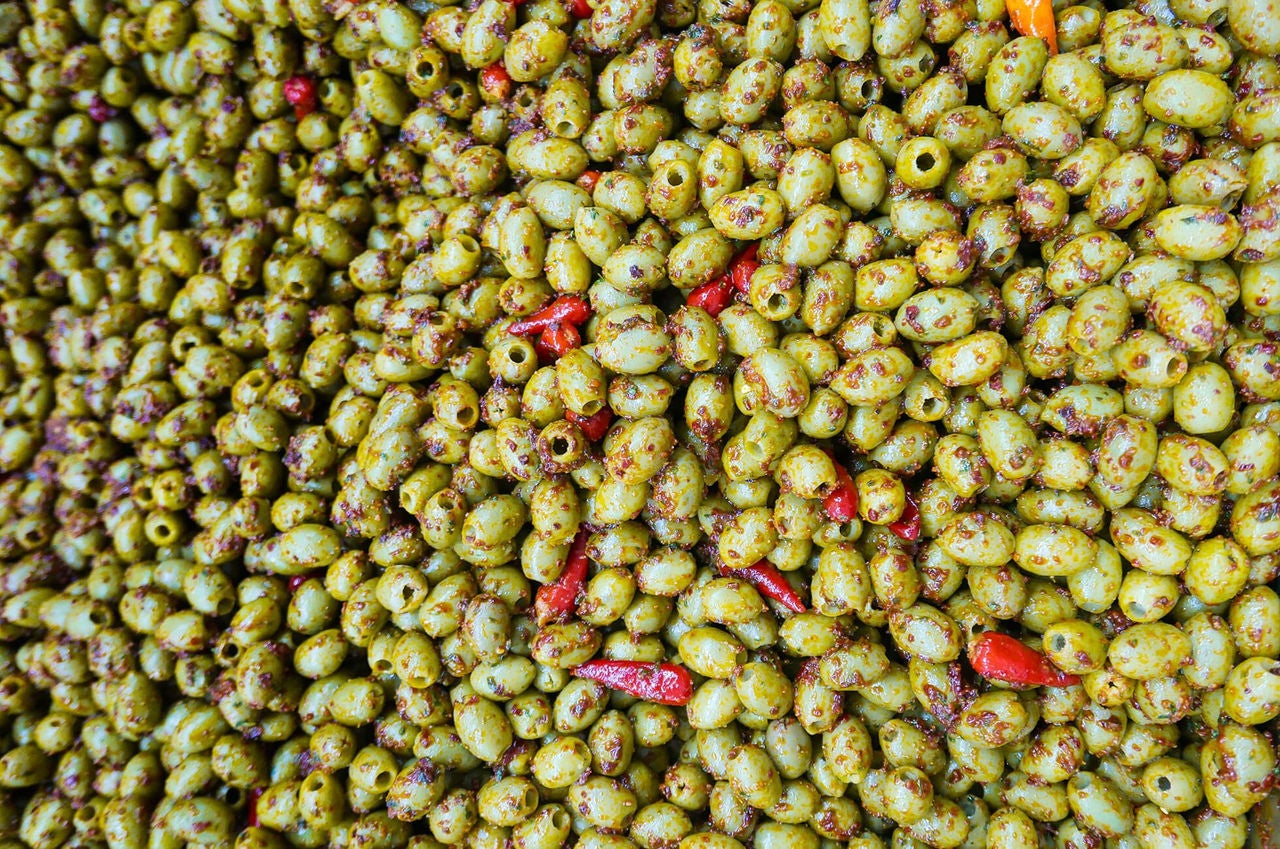
Ändra plats
Nuvarande plats
Master butcher Hanspeter Baer was seen as being exceedingly bold, when in 1999 he decided to sell fresh olives and antipasti rather than meat and home-smoked products, and when he then founded his own company. Despite all the prophecies of doom, Hanspeter Baer pursued his intentions with success: within a decade Ceposa AG with its headquarters in Kreuzlingen had developed into one of the largest manufacturers of fresh antipasti in Switzerland. A 24-hour delivery service with its own logistics and partners supplies around eight tons of hand-processed olives and antipasti per week to customers in Switzerland. Since the company was founded, 30 full-time jobs have been created. Depending on the season, Ceposa employs 35 to 50 staff.
In order to be able to rely on a consistently high quality of food products, Ceposa AG obtains these directly from selected Southern European producers, whom Hanspeter Baer for the most part knows personally. When processing its products at the production site in Kreuzlingen, the company dispenses with additives and uses only rapeseed oil, high-quality herbs and natural rock salt. The Mediterranean delicacies arrive fresh and appetizing at the retailers, packed with modified atmosphere in transparent, reclosable trays.
At the beginning of 2015 the existing packaging machine had to be replaced. The rapeseed oil kept getting into the electrics when oil was being added to products. This caused a high level of repair and servicing work - to say nothing of the associated downtime. “One of our most important criteria in the purchase of a new machine was the electrics had to be very well protected in an enclosed area from all external influences,” explains Andres Kaspar, who manages Purchasing, Operations and Quality Management at Ceposa, and who obtained quotations from two packaging machine manufacturers. He also placed great importance on a quality product that was technically sophisticated, as well as on the manufacturer being represented locally. This is because Ceposa only manufactures fresh products with a short shelf life, and consequently any faults that may arise have to be rectified quickly and expertly.
Since the Production department was already working with a C 400 chamber machine and two small T 250 traysealers from MULTIVAC, Andres Kaspar favoured the T 600 traysealer. “We already had thoroughly good experience with the existing MULTIVAC machines, as well as the expert service and rapid availability of spare parts,” says Andres Kaspar explaining the reasons for the decision, and he states as a further benefit the close proximity of MULTIVAC Switzerland, whose service staff can be on site within the shortest possible time if required. “The quotation from MULTIVAC was also more attractive in the commercial aspects,” adds the Head of Purchasing and Operations.
Since the T 600 can pick up four trays at once, it fits perfectly with the anticipated expansion of production capacity, and it is an excellent investment for the future. The version of the T 600 selected by Ceposa is new and has a longer die than that available with previous T 600 die designs, meaning the output can be increased significantly. “In the future, we will be able to fully utilise the machine’s capacity of four packs per cycle and eight cycles per minute,” says Andres Kaspar explaining the company’s future plans. In the longer term Ceposa plans to further utilise the full capacity of the machine with a daily running time of eight hours, thereby producing approximately 15,300 packs per day.
“Our Head of Purchasing and Operations wanted the best and has got it,” says company owner, Hanspeter Baer, with a twinkle in his eyes. Andres Kaspar agrees with him: “We require an absolutely reliable packaging solution, allowing our sensitive products to remain fresh for a long time.” The versatility of the machine also immediately impressed the Head of Purchasing and Operations, since the T 600 can produce vacuum skin packs as well
The new traysealer has been in operation in Kreuzlingen since the middle of June 2015. The staff currently fill the trays by hand, and an automatic filler doses the rapeseed oil into the antipasti trays. The trays are then transferred onto the infeed conveyor of the traysealer, which seals 1,200 trays per hour. Mishaps such as oil flowing into the electrics are now things of the past. The electrics are housed in a control cabinet positioned on the side. Since the T 600 is certified to the IP65 protection class, it does not even have to be covered during cleaning. The ease of operation has also proven popular: “Operation via the large touchscreen is virtually self-explanatory,” emphasizes Andres Kaspar. This is particularly important for the company, since the users are not trained machine operators and are taught on the machine during running operation.
As the next stage of expansion, the T 600 will pack larger trays with several pack cavities for various antipasti, as well as the existing 150 gram packs for self-service deli counters in supermarkets. Running 1 kg trays for bulk buyers is also envisaged, but this is not yet possible at the current production site due to space reasons. As soon as the planned building extension has been completed, the T 600 is due to be integrated into an automated packaging line, complete with new metal detectors and a checkweigher, as well as a unit for adding oil to the products.
Andres Kaspar views the move with a relaxed attitude, since it can hardly be more difficult than the initial installation. When the machine was delivered, the T 600 had to be transported to the production level that was situated below. The challenge lay in the fact, that the length of the machine was significantly greater than the width of the lift shaft. Three service technicians from MULTIVAC, together with the lift company and an industrial logistics expert, were able to solve this problem. The machine was dismantled to its shortest dimension of 3.41 metres, and many add-on parts were removed where possible. A range of equipment aids such as load carriers, mobile trolleys and chain hoists were required to manoeuvre the components into the lift shaft and then to lower them upside down into the basement. “It was perfect teamwork, everyone worked hand in hand,” says Andres Kaspar with praise, and he is sure that he can rely on his new packaging machine as much as he did on the expert support of the MULTIVAC service technicians.
09.02.2016